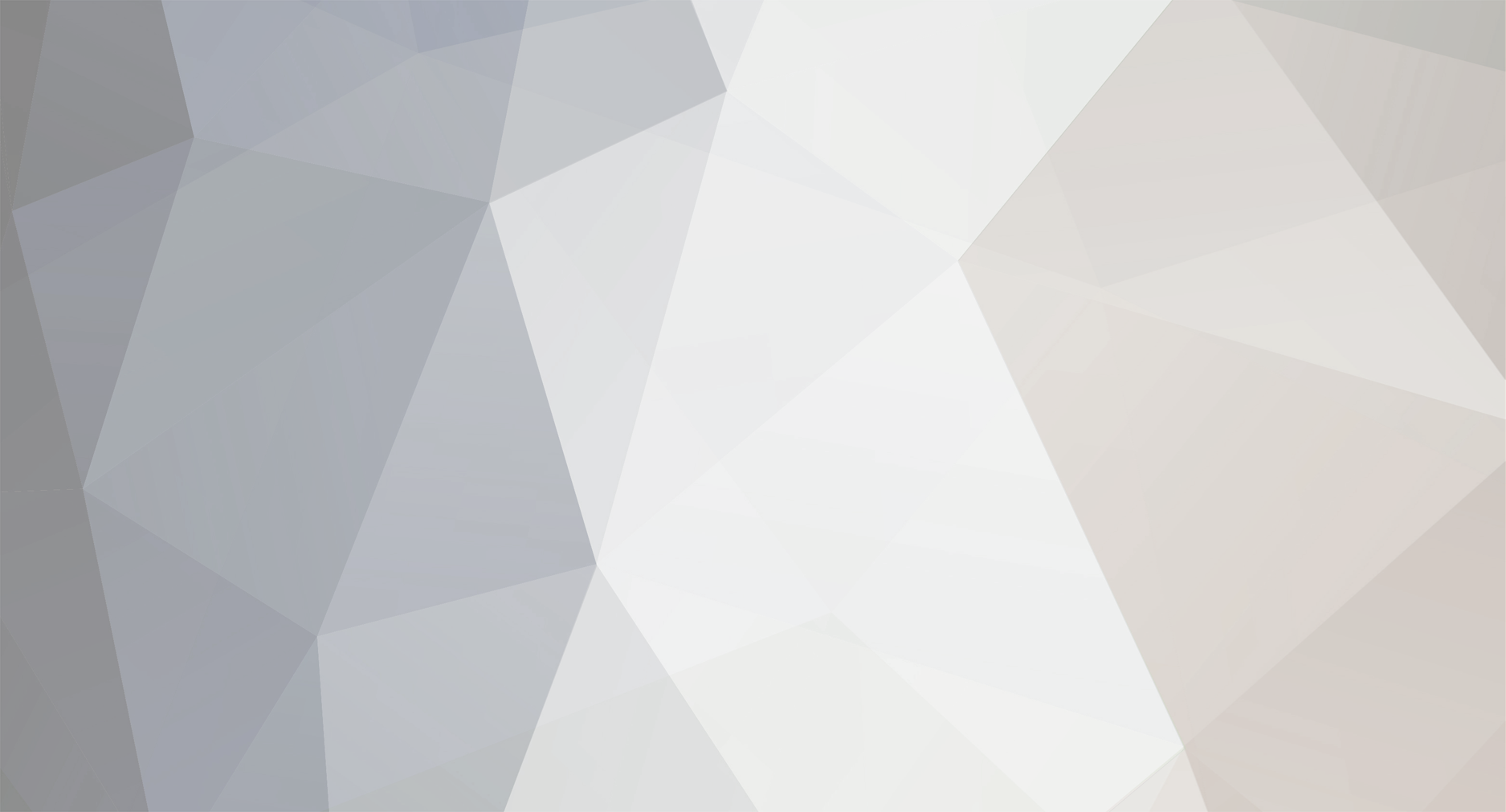
duffymp
-
Posts
4 -
Joined
-
Last visited
Never
Content Type
Profiles
Forums
Store
Gallery
Downloads
Calendar
C-130 Hercules News
Posts posted by duffymp
-
-
From Minne here.
-
OK here we go. I worked on this issue many times and it is very subjective. Here is my take on things:
The old way---- Guys used to cycle the prop from reverse to feather (3 times) then wait two minutes (if you were a newbie it was right away for a good laugh) pop the the tiolet seat and check using a 6 inch screw driver (or the dipstick if you had one). The lines on the stick were always different so everyone (this is at Pope in the 80\'s) just learned that it should be this \"high\" on the stick and this \"high on the old screw driver.
Things learned: At Pope Ham Standard came out to investigate all of the prop leaks that we had. I would have to say that pretty much every airplane had 2 or 3 prop leaks.
What they found was that 80 to 90 percent were all overserviced.
From that study came the Atmospheric check. Cycle the blades from reverse to feather three times, hold the condition lever in air start at GI and check the atmospheric dipstick while the aux motor was still running. They stated that while everything is running there should be 11 to 16 ounces remaining in the atmospheric side. They recommend that the atmospheric dipsticks be remarked to have a scribed line a half an inch from the tip of the stick. Finally a definative line to work with. Problem was if it was a quarter of inch showing on the stick how much to you add??? They then recommended that only 4 to 5 ounces be added at a time and then rechecked. What we found was, we were moving, servicing and rechecking a number of times that it was just a pain in the ass. So when you saw that there was no fluid on the stick or maybe just a quarter of an inch up, everyone started by putting a half a quart to a quart at a time and then rechecking. If it was a little over it was thought to be ok. Problem with that was not really knowing where all of the fluid was.....
I moved from the active duty to the reserves where we had a little more time to look at this problem (in between taking union breaks).
When the system is running it pulls from the atmospheric side, through the pressurized side (obviously) then through the VH to the PLR and dome then back and it dropped back into the atmospheric side and the cycle starts all over.
When the pumps are shut off the pressure from the pressurized sump is relieved into the atmospheric sump and the air is then vented through the valve housing breather.
Really old head prop folks actually used both sticks to KNOW where the fluid is. The fluid that in the pressurized sump flows back over to the atmospheric sump (when the pumps are shut off) the problem lies in how fast does that happen. If you had a prefectly clean pump housing and clean fluid (which is NEVER the case) fluid would flow back quickly and at that point checking servicing using the pressuried dipstick would be very accurate. That never happens. Some flow back quickly, some may take 15 minutes to an hour. This is really what you need to remember. There were times when checking that you would wait your 2 minutes pop that toilet seat up and fluid would flow out of there. You would close the cap and wait a few more minutes and recheck it or one would assume that the prop was over serviced.
After understanding that some flow back slower than others you can acurately do a good service check by using both dipsticks. If the flow back is slow you wil see that using the pressuried dipstick the fluid level is high and lower on the atmospheric dipstick. Pay attention to the difference. When the propeller is left to slowly relieve that pressure and the servicing is good, the amount and both sticks should be exactly the same. Hold the two of them side by side, if everything is working like it should they should match.
Now if servicing is low it will be low on both sticks. There used to be a full line (about 4\" up) on the pressurized dipstick. Both sticks should match that line in a proper serviced propeller. This was makes it easy as you actually know where your fluid is. If the prop is over serviced you will know it immediately by seeing fluid high on both sticks.
We used this procedure on all of our 8 airplanes at the unit and with in 8 to nine months we had solved about 90 percent of our prop leaks. It works.
-
This has been a LONG time problem and there really is no exact fix to the problem. It may any one of many problems associated with that cover. The lip seal not being pressed in properly, dip stick seal or nut not torqued, cover plate seal, valve housing cover breather being clogged. A long time ago Hamilton Standard did a big study at Pope AFB in trying to determine exactly what the cause was. Out side of the normal stuff discussed earlier they found that almost 80 percent of prop leaks are caused by an over serviced propeller. During the study at Pope we found that some of the propellers had almost an extra gallon of fluid in them.... This is why it is so important to not just throw 2 quarts in everytime the low oil light comes on with out checking the servicing first. The book has the established way of checking servicing but you will find that a lot of the old heads do it differently. Remeber that a little fluid goes a long way.
FOD Incident
in C-130 Technical
Posted
----- Hey Steve, I was stationed at Pope AFB when the guys did that! They had pulled the prop, re-sealed the thrustnut and started the thing up to leak check the thrust nut. They did leave one set (2) from one side of the after body laying in the drip pan. Actually I think that they were on that little shelf up from the drip pan. Engine started and sucked them in. I know the name of the guy who did that do you?