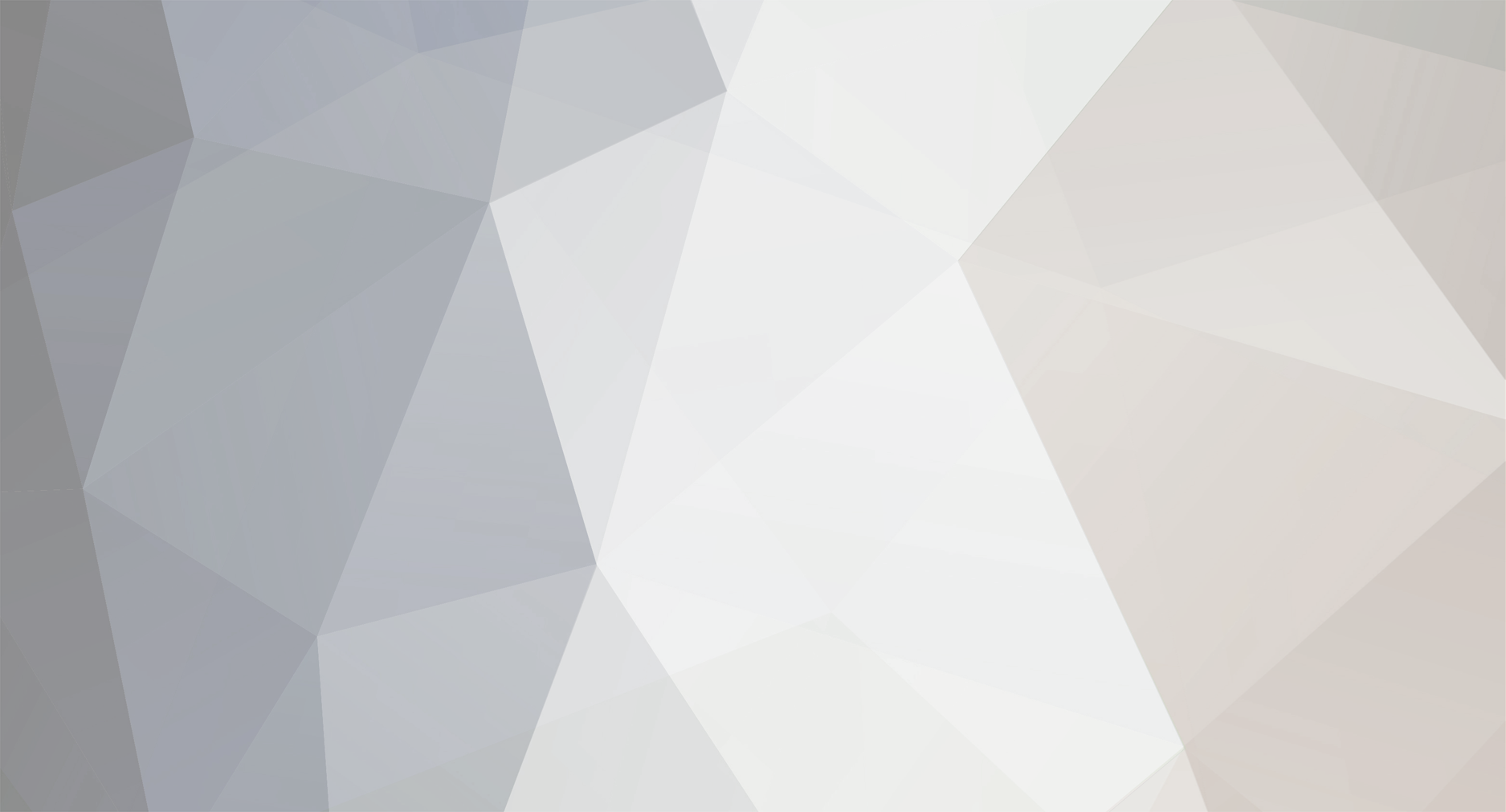
Steve1300
-
Posts
246 -
Joined
-
Last visited
-
Days Won
2
Content Type
Profiles
Forums
Store
Gallery
Downloads
Calendar
C-130 Hercules News
Posts posted by Steve1300
-
-
I'd bet that the guys at JAC could answer that. Mustafa and his guys surely will know.
You should have positive indication of pressure by the time the engine is started and full system pressure 30 seconds after that.
Steve
-
There is never a shortage of jerks in flight suits, nor a shortage of incompetents with toolboxes.
I would imagine that it is difficult to expect a production super in a pickup truck to solve problems when they are selected by rank and not by skill or knowledge. Isn't that the same way that other lead people are selected?
-
[ATTACH=CONFIG]3318[/ATTACH]
Depends on how much wind you can stand.
-
It's in the 1C-130H-2-61JG-10-1, S/S/SN 61-10-21, para 6 for Propeller leakage inspection. The pump housing as a whole is allowed to leak 1 drop/45 seconds either operating or statically. This does not include the propeller shaft seal, and nothing else on the prop is allowed to leak. If I get called out to an airplane for a lip seal leak, I'm going to use the maintenance book for the limit. If the aircrew refuses the plane for something that's within limits to me, it's their option, but it's also a late or an abort against OPS, not MX.
I can understand all that. Without having your books to go by, I had to do a refresher in my HS books. This is what I found:
Visually check valve housing cover to pump housing sealing area and drain plug area for hydraulic oil leakage. Install new seals if leakage is evident in these areas. Clean the valve housing cover breather with dry cleaning solvent (Item 2, Table III). Visually check the front and rear of the control for leakage. The front and rear rotating pump housing seals operate with a film of oil between the sealing surface and the rotating parts, therefore, a film of oil in the seal area is acceptable. However, oil seepage that causes oil to drip from the front or rear of the control in excess of one drop every 45 seconds (4 ounces per 24 hours) is cause for control removal and seal replacement.Seems to me that I can have 1 drop from the front and one drop from the rear at the same time! Where is my lawyer when I need him?
Going back in my memory banks - which is a risky proposition anyway - I remember a time when lip seals were not allowed to leak while running, but they could when static. I probably should quit tryint to remember stuff from that far back.
-
The #1 blade was parked at 12 oclock to "preclude" oil leakage from the beta feedback shaft. When it is cold this is the fix for that drippy nose prop sometimes. Bill
Yep, for some who don't understand how the beta feedback shaft lets fluid run through, they need to remove a pump housing one time and watch how much fluid comes out of the unsealed shaft. There is a lot of fluid in that barrel and dome looking for a place to go when the prop is not turning.
When the prop is turning, the scavenge pumps won't let the atmospheric sump fill up. When it is not turning, the levels can rise to the lip seals.
My books tell me that lip seals are not allowed to leak. I don't have a "lip seals can leak one drop every 45 seconds."
-
So our two grey "E Flight" aircraft were just a nickname. OK.
Our upgraded security clearances were just for practice, and the mission were actually haphazard.
I didn't realize all that.
Thanks.
-
I'll give you my view, and others can comment and add some light to this...
I think the SMP is for Civilian Hercs and TO's for military Hercs.
Here's an example of a difference, for the same leading edge section, a skin repair requires two rows of rivets under the TO, and four rows under the SMP. Why?
I will take a guess at that for you: different engineers provided the instructions.
A "typical" repair often calls for two rows of rivets using the closest rivets rows to the repair area as examples for size and pitch and spacing.
An engineered repair takes the metal bearing strength and calculated required rivet size and number based on matching the metal bearing strength with the shear strength of the rivets.
Using those two methods, it is possible to come up with a difference in repair instructions.
-
Personally, I would not bother with a TD system tester to fix a low power problem. If you are getting your TIT for the check, the amp is not causing your problem. As previously posted, if you are getting 100% rpm, your prop is not causing your problem.
I have yet to actually work a low power engine that a turbine caused without having other indications of a problem. With an engine that appears normal except for performance numbers, it has been caused by compressor issues or leaks. Sometimes, it was something simple but we wasted a great deal of time finding it. Live and learn!
-
Lkuest, your guesses work as well as mine. I have often considered the gauge error to be the root cause of the temp limit for takeoff. In the civilian Herk world, our books call for us to set our slope at 1071 and not at 1077. I guess that to be to allow a TIT indicator error if 6 degrees. We should never see 1083 without a TD system malfunction.
As for TD system corrections, my failing memory reminds me that our corrections must be within 3 degrees. People with round steam gauges would have to guess if they fell within those kinds of limits.
-
I thought that the 73's went to LRF at first. They were there when I got to LRF in '75. If so how'd you make a 10-hour overwater to Hickam from LRF? Seems part of the story is missing. Anyway, sure liked flying missions with them, except for maybe the PPs with students in the winter! Ham-fisted students kept you on your toes knowing that any of the 100+ T&Gs might be an over-torque. Well it seemed like 100+ plus anyway.
I was at LRF in 74 when the '73 models arrived. Our overwater nav started with a trip to California. It seemed suspiciously like a benny run for someone other than me. That is the part that is missing, I guess.
-
The 73-models "H's" were merely the bionic "E-models." I received responsibility for 73-1586 when it arrived from Lockheed. It had 26 hours on it by that time and external tanks in crates in the cargo compartment. I was in awe of the engines as I had only experienced -7s and -9s before that. We quickly made an overwater-nav to Hickam with it and flew the whole trip below crossover in order to make it a 10-hour trip.
My jealousy started when Dyess started getting the 74 models the next year with the APUs and large air conditioning packs.
-
I am aware of the servo governor valve housing and the standard governor valve housing.
From what I can tell, the servo governor valve housing has slight different protractor readings during beta adjustments (ground idle 4-5.5 on standard; 5-6 on servo). However, because of a crew mishap report; they are not permitted to be installed on the outboard propellers. They are reported to be much more reliable than the standard governor types.
The part number of the standard governor valve housing start with a 5. The servo governor valve housings have a part number that starts with a 7. At one time, the servo governor valve housings had the filter assembly bodies painted white on the visible top.
I have yet to see a difference in actual operation.
-
Anyone have experience with this company's offering for compressor washes? We are looking for a less costly system for after-wash disposals and such, and I am needing to know is their system works as well as the gas path cleaner and rinse system.
It may also be known as R-MC Compressor Wash.
Thanks,
Steve
-
Would a yellow box check for the put and take reactions times show the problem? Since the brake failed and is locked (stuck) will the 14 second check demonstrate the need for a new valve?
-
Yep, had it happen at Subic Bay circa 1978. Vibrates really badly!
-
It's actually preferred to do it in flight. This allows for more stable conditions during the procedure. Refer to the 1C-130H-1, pg 1B-20. The only real consideration is during stable flight conditions.
One would think so, but when the solid state synchrophaser were installed, safety-wire holes appeared in the resynch switches so that we could prevent the crews from doing it in flight. We are still told to safety-wire them on civilian Herks. Does the military no longer do that?
-
If I get a chance today, I'll look and see.
-
Well, you don't say that there is any difference with the engine bleeds open or closed, but that needs to be checked. If the problem goes away with the bleeds closed, at least you know whether or not to concentrate on engine bleed air leaks and which one.
When you say that all ducts have been checked, are you saying that you have gone with your hands down each and every pressure duct by hand? All the way down the cargo compartment, with the bleed air ducts pressurized, you really need to get on a ladder and check the entire length. Also, make sure you check the external air connection to see that the check valve there isn't bleeding through.
It gets expensive changing parts without finding the leak source first.
-
Living and working on Okinawa, we spent a great deal of time close to the salty atmospere. The Navy had a "birdbath" built in their area where they could taxi through the fresh-water spray on the way to parking. We did not. I never was informed of what real benefit they experinced compared to our aircraft, but we changed a lot of engines. Since we sent our aircraft to PDM (IRAN - at that time), I didn't get to see the effect of the salt environment on aircraft structure in detail very often. Our POVs, however, suffered greatly.
I do know that salt is harmful to metals. It takes salt, moisture, and time in order to wreck your aircraft. Get rid of either the salt, the moisture, or the time; and you will be doing a good thing.
-
In one copy of Lockheed's Corrosion Manual, it states: Rinsing to Neutralize Salt. Some operators with bases adjacent to coastal or brackish water find contamination from salt fall-out to be sufficiently destructive to warrant fresh water rinses between wash cycles to control salt build-up. Where practical the rinses are performed daily, usually after the last flight of the day. A few operators have automatic rinse equipment and a rinse solution that contains inhibitors. If airplanes are parked within two miles of the sea or operate under 3,000 feet above the sea, a regular rinse to neutralize salt contamination is recommended.
Any Navy personnel could probably offer suggestions based on personal experience.
-
It is spring loaded closed, so with the aircraft parked and no bleed air pressure on the manifold, it will be closed. However, on military Herks, if you should have bleed air pressure and place the switch in Aux Vent, it will open. You do not have to try to pressurize the aircraft, just the bleed air manifold.
-
There is one very similar; a digital edition, put out by
362d TRS, Airlift Training
Heavy Training Flight
Air Education and Training Command
I long ago lost my yellow one, but I still have this one.
-
One of the things I learned, and it took me a long time to do it, is that I don't know everything. I found out - and it was painful to a degree - is that other people have good ideas and may actually be able to teach me something. Don't throw away good advice out of a false pride or ego. The military has better manuals that civilian companies, but they still don't answer every problem.
-
Lots of very experienced current and past maintainers advocating subject procedure, citing different methods. However, in all the posts did not see a single TO, page and paragraph detailing hammering a deflated strut to ensure removal of air/nitrogen. Seems to me if this was, in fact, a valid procedure, it would be in the TO. As a flight line troop most of my career starting as a third wiper and concluding as sqd. superintendent including a tour as QA super. was adament about following tech data. In those instances where tech data was deficient or just plane dumb - and there were many - we made every effort to change it. If an AFTO 22 failed we made it a PMR/MMR adjenda item. The point am trying to make is if the procedure is valid it needs to be in the tech data!
You do have the perfect QA inspector position on the procedure - and sometimes we must send the QA guy on an errand so we can get the job done.
As for Tech Data, after several years at WR-ALC, I've seen how some T.O. changes take place. I can assure you that our technical orders are not corrected by experts and the suggestions that make it into tech data and those refused are sometimes done in error. There is such a thing as general practice that have proved themselves over time, and those techniques don't get included into tech data because they are not suggested or they are evaluated by the guy on the floor that is asked for his opinion - who might not use it himself - so it is then declared "dumb."
I've submitted AFTO 22's when I was AD that were turned down but then showed up in Tech Data several years later - only because of which guy on the floor the people from the T.O. office took the suggestion to.
Not all ideas that are not in the T.O. are dumb - they are just not in the T.O. If we want to see if a job violate the Technical Data, then we need to actually check for violations - not just "helpful procedures that are not there." Common sense is not illegal.
nose wheel wobbling
in C-130 Technical
Posted
I have seen many people change nose tires and think that they fixed the problem because the next crew didn't think it was serious enough to write it up. If you have different crews flying the plane, they all seem to be concerned about different problems and not all of them get documented. It is only after a nose wheel shimmy gets bad that everyone complains.
There is also the fact that a shimmy does not necessarily show up on every landing. Runway surface and condition can initiate a shimmy. A different runway with different conditions may not initiate it, so we call the problem "fixed" when it actually is not. Also, the pressure on the nose wheels can contribute to whether or not the shimmy happens.
We are fooled into thinking we fixed it with new nose tires when it does not happen on the next flight.
I've seen a lot of wasted nose tires when the problem was air in the steering actuators and worn scissors bushings or rod ends. Of course, the tires are easy to change, so ...........