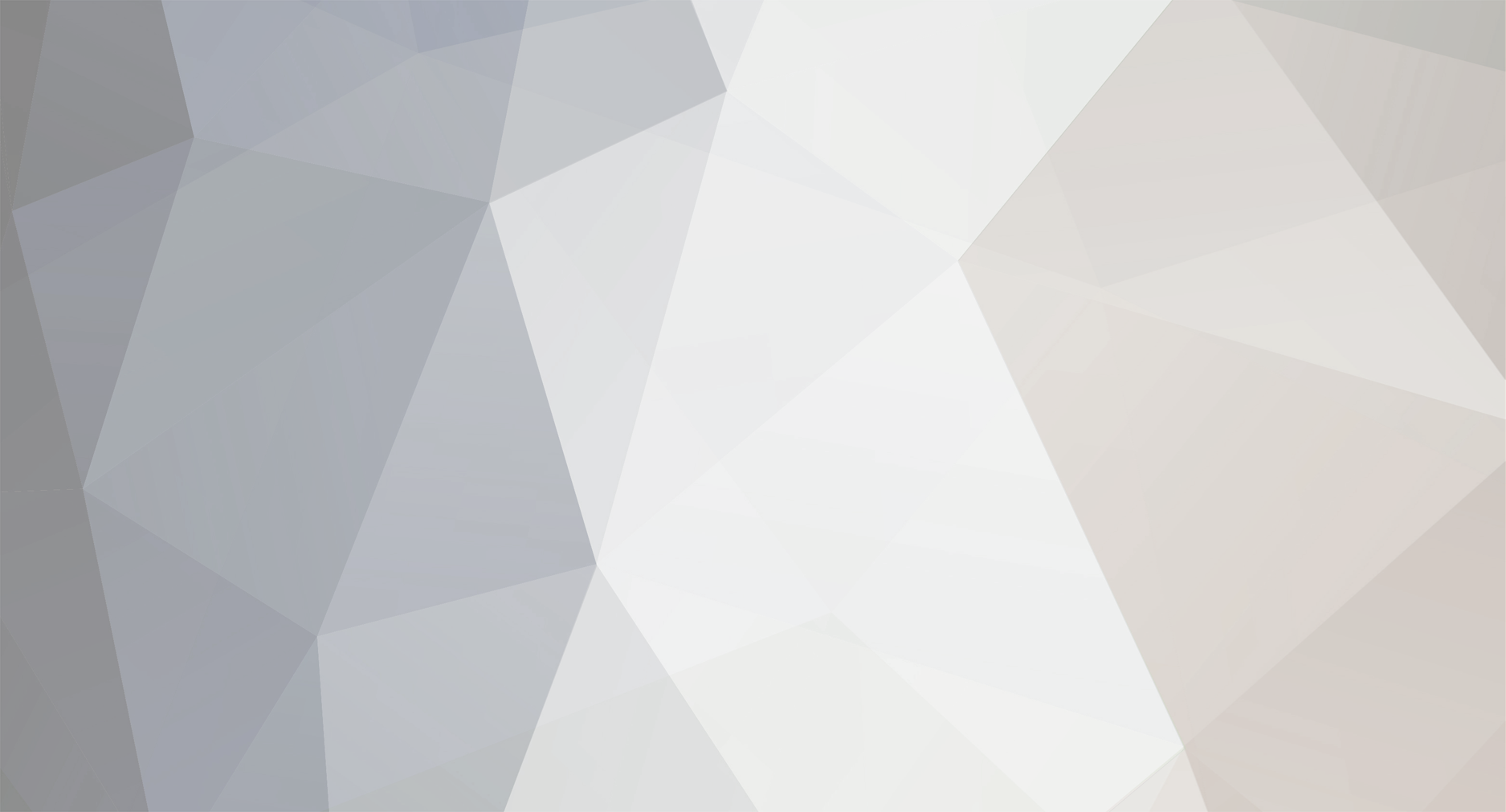
Steve1300
-
Posts
246 -
Joined
-
Last visited
-
Days Won
2
Content Type
Profiles
Forums
Store
Gallery
Downloads
Calendar
C-130 Hercules News
Posts posted by Steve1300
-
-
Thanks, guys, for making me feel younger. My first Herk TDY was from Forbes AFB, KS, to Pease AFB, N.H. in 1973. I was the crew chief if I had known then just how little I knew, I\'d have been scared.
:unsure:
-
I can only wish you luck in achieving your goal.
If you stick with it and perhaps even go into the civilian world as an F.E., I would suggest that you keep in mind that it is a \"different career path\" and not a \"higher career path.\" The mechanics you leave behind are not becoming beneath you, they are only on a different path.
A good F.E. is worth his weight in gold in the civilian world, too.
-
Thanks! Nice to have the video to share with family.
-
The inverter is only a source of bus power when AC is not available or in case they lose AC on start.
Now, on the newer configurations, the switch positions are changing to put all switches in the fore/aft postition to standardize the switches. The -1 position is for AC and the horizontal position ( the dash position) is for inverter power. Of course, since we are losing the Co-pilot\'s inverter switch, there is only one to focus on.
How is that for keeping y\'all on your toes?
-
Wing struts? Do you mean panel risers? I remember the NDI of the wing dry bay risers and the subsequent repairs to them, but I really don\'t know what a C-130 wing strut is.
-
Actually, it was right after Eagle Claw that the flares were installed on the Kadena MC130\'s. They didn\'t have them in the late 70\'s at all.
-
FCCtoFE wrote:
Well I guess I have to chime in with my 2 cents, in my 16 years of maintenance experince and countless trips to a lot of unimproved landing surfaces, dirt, volcanic rock, rock and soft ground conditions. I have never had an FE or any other crew member for that matter come up to me and ask me to lower or raise the tire pressures. We would set them at 93 +/- 5 and call them good. I guess I just got lucky and never had to dig an acft out.You have been lucky. Lucky that you didn\'t land on an airfield that was too soft for your aircraft\'s footprint and weight.
I did get stuck on a gravel runway, but not in mud. I was stuck on the runway with both right side tires blown. It takes a bit of inginuity to jack an aircraft when both tires are flat. I was fortunate enough that a Canadian Herk was preparing to take off and loaned me a spare tire. Otherwise, my goose was cooked.
-
I had 23 years in the military before the last seventeen in civilian herks. I am somewhat familiar, but the \"modern day\" military is a bit unknown to me.
If I had to choose between under-inflated and over-inflated for the day\'s weight and conditions, I\'d go with over-inflated. It does much less damage to the tire sidewalls. I tend to cheat my pressures up rather than down.
I do understand folks not wanting to get stuck where the ground is soft. I\'ll bet most folks understand not wanting to have a blowout at that \"unimproved airfield,\" too. Did you know that a heavy Herk will push a jack into the ground long before the jack will lift the aircraft?
It smashes half-inch plywood pretty well, too.
Been there, done that. Peace, \'migo.
-
Perhaps some pilots don\'t pay any attention to where they land. In the civilian world, the pilots are responsible for all those decisions, and the discussion frequently takes place among the crew about those \"unimproved airfields\" before any decision to land.
Really none of that has anything to do with tire pressures. The requirements for pressures are given in the maintenance manuals. If you get stuck because a field was too soft, then you really should not have landed there.
And, yes, I have seen fields that were about as firm as bread dough that we were told was OK to land. Not every pilot is actually able to figure that out. A King Air or Twin Otter pilot looks at runways a little differently than Herk pilots.
If you have to run under-inflated, you will do damage to your tires. Someone will end up paying for it. The question is where and when would you like to have your blowout? I\'ve never been allowed to pick the time or place, but I did get to change the tires.
;)
-
Well, there is such a thing as a \"substandard field\" and then there is dirt that we shouldn\'t be landing on. If we have to drop tire pressures so low that we chance tire failure on a real runway, perhsps we should not be landing on the dirt that requires such a low pressure to keep from getting stuck.
We do have tire pressure limits for a reason. Personally, I don\'t care to have runway tire blow outs, so my pressure has to stay high enough to prevent that. If that causes the plane to get stuck in the dirt, shame on the pilot for landing there.
;)
-
Equipment and Supply, Inc. Monroe, NC 704-289-6565
Part # 340713 and 340714 for both main and nose.
-
A pressure indicator pointer \"jumping up and down\" is likely not indicating fluid pressure as much as it is air pressure. You may want to bleed the air out of the line at the transmitters. Have these lines been disconnected lately? Has there been a rudder pack change lately?
Then, it may be a transmitter or indicator problem, best checked out by swapping indicators or transmitters - just not between each other.
-
So the double-stretch J-model is 200\" longer from the wing forward?
Or did they move the reference point?
-
It is difficult to tell if you really have a problem or not based on your description. If I were trying to find out if there was a problem, I would first check to see if the accumulators are correctly serviced. By that, I mean that I would open the schrader valves and drain out any pressure and fluid trapped on the indicator side of the diaphram. Then, I service it again to the correct pressure. This will tell you if you are seeing the results of accumulator problems.
If you have the engines running, with one pump shut off on each system, see if you can move the controls and maintain at least 2000 psi in the system. If you can, you don\'t have a problem. If the pressure drops below that with NORMAL operation of the flight controls, then you may have a problem to chase. If you have to make large quick movements to get pressure that low, then you still don\'t have a problem.
That\'ll be 2-cents, please. ;)
-
The double streched models, civilian world anyway, have charts that look similar to the short military models. There doesn\'t seem to be a lot of variation as far as limits for flight. I have not seens the single-stretch MAC limit chart for flight.
Wt and Bal is calculated based on \"trim station\" versus fuselage station and we end up dealing with positive and negative numbers in the calculations, though both methods are just different ways to reference the datum line.
Essentially, there isn\'t a lot of difference. We still have forward and aft limits that are similar, but of course, we do have conflicting documents.
-
Our start times were still around 45 seconds. The second stage vanes were burned out in only one section as well, so that would be where the fuel fire was starting. A turbine like that will not necessarily give enough torque difference that folks would notice it right away. We also do not know how long those turbine fires were going on, but as I orignally said, it happened only in LSGI.
-
The engine overhaul facility has not reported finding any problem with the cans, but the second stage vanes were destroyed. I\'m afraid that we will never know what happened. Since our nozzle tester showed a good pattern, we are out of ideas. Hopefully, it will do well on their test cell and we\'ll get it back soon.
I really would have liked to have something to blame this problem on..... Drat!
-
Thinking back on it, the problem as explained - does the pressurization never stop increasing? You say that it stays between 700 and 1000 feet the whole time?
It really sounds like the underfloor heat is working OK, but they can go back and feel the floor if they think the overheat switch is cycling. It will surely be hot to the touch.
-
Nearly every time I have that problem, I end up replacing worn bushings in the gimble itself. There is a knee joint for the gimble that has bushings that will wear, but gets little attention as it is difficult to see. If those are worn, they will cause the throttle lever to creep.
-
Jake wrote:
There are two thermostats that operate the underfloor heat valve. One (the overheat, set to 180 degrees if memory serves) will close the valve and subsequently open it when the temp has reduced (do not remember what temp). This will cause the cabin pressure to cycle. I suspect you have changed this as your post says you have changed most of the components.If the cycling is from the overheat stat, the control thermostat would have to be bad as well, wouldn\'t it? Sounds like two bad parts to me.
-
I still use many of the terms we had for years:
Grasshoppers - ads support arms on the ramp
Dog Bones - gimble links
Hog Trough - overhead center equipment rack down the middle of the cargo comparment
Elephant ears - raised skin of the ramp that covers the actuator attachement
Dog Legs - aft nose gear door swing arms
Chicken Legs - connector rod between flap jackscrew and flap
Pork Chops - ends of the structure that connects one wheel well to the other across the fuselage belly
Butterfly fittings - the lower part of the vertical support rods aft of the ramp hings that attach to the sloping longerons
Bath Tubs - the sloping longeron end attach fittings at F.S. 737
Spiders - on the old C-130s before the \"new\" AC packs - the ejectors below the heat axchangers
Bread pans, bread backets, etc... are all new to me.
-
WE have a fuel nozzle tester which checks the patterns versus the spray pressures. All of them were good. The repair station where we sent the engine said that our actual flow quantities were slightly high on a couple of them, but the amount was only about 2%. I don\'t think that would cause the degree of troublw we were having.
I am trying to imagine what would give us unburnt fuel all the way back to the turbine and burn up the second stage. I\'m pretty sure that the fire is not taking place in the can, since the fuel is making it back into the turbine blades before burning.
When I do get some information as to the cause, I will remember to post it here for everyone. That is - if they ever actually give me the cause to report.
Thanks for the input, guys.
:)
-
My initial assessment was that I have a can not burning. The fuel is hitting the thermocouples and cooling them off - giving me the cooler start temp.
We shipped the engine out to Miami Lakes to get checked. I hope they come up with something to go on. We don\'t pull our own hot sections here, so I have to depend on others to evaluate the problem. It should be on the test cell for run today.
-
All of the information I have about the situations encountered with only one ignitor firing tell me to expect slower starts. I have nothing to indicate - if the flame propogates as designed - I should have downstream burning in the turbine.
By the way, both ignitors are firing.
A cracked can? If I have a cracked can, is it possible that the split is large enough to allow air to prevent the fuel stream from being ignited within the can?
Help with part numbers?
in C-130 Technical
Posted
http://www.alliedelec.com/Search/SearchResults.aspx?N=0&Ntk=Primary&Ntt=sleeving&sid=11C5A3B06525