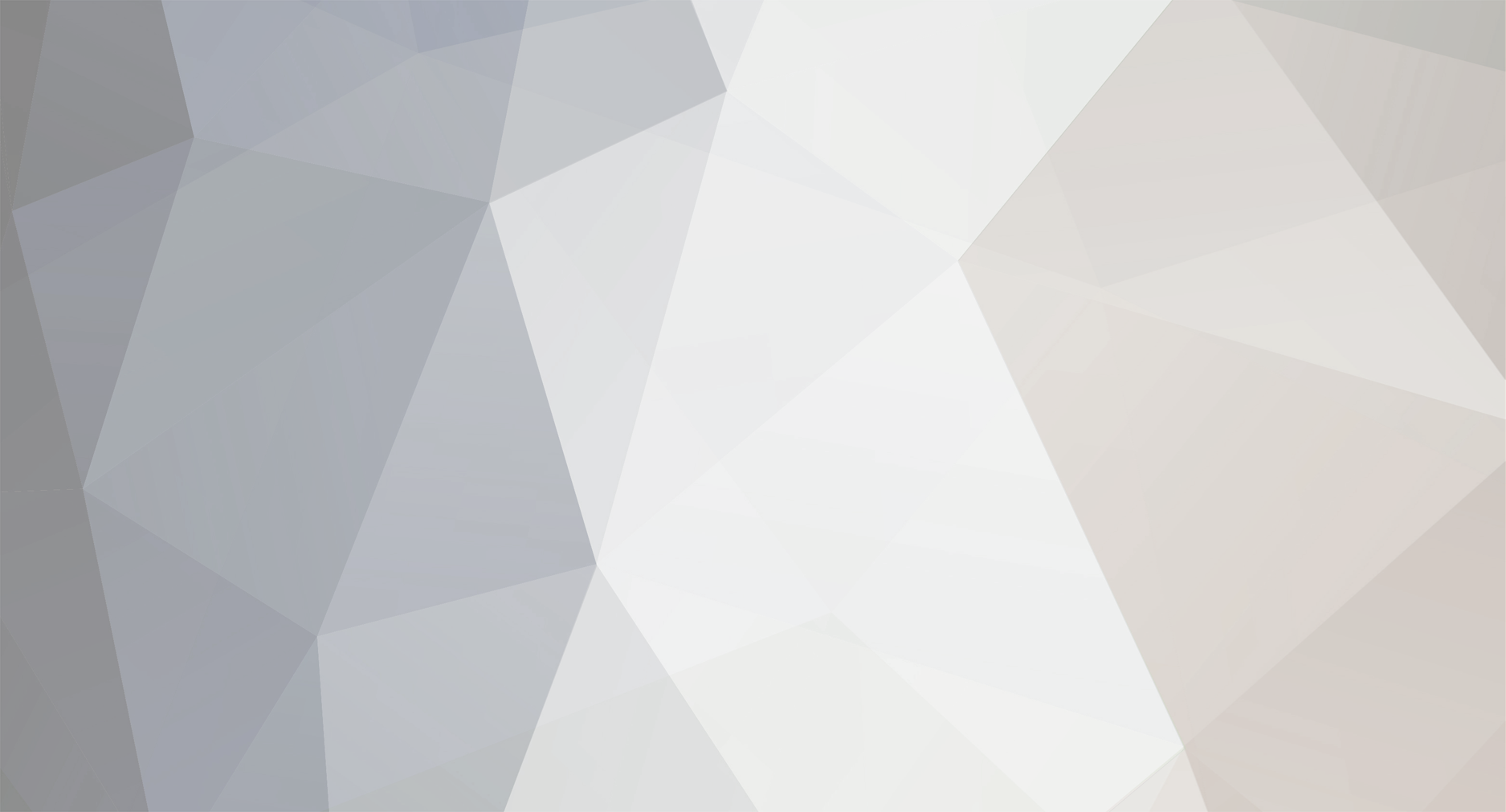
FredG
-
Posts
31 -
Joined
-
Last visited
Content Type
Profiles
Forums
Store
Gallery
Downloads
Calendar
C-130 Hercules News
Posts posted by FredG
-
-
Bob, I'll ask a friend down there if he can get the number for you. BTW, they have an 'A' graveyard there too and those A's are painted camo except for one that is their disco (all black)...they use that one for "events"
-
The N118Z number is sure close to the N118TG that International Air Response uses. I'm just say'n...
-
Your T.I.T. indication is low and FUEL FLOW is HIGH. So, you have two sets of 9 thermocouples (18 total); one set for the TIT indicator and one set for the Temperature Datum system. In the flight range (above 65 degrees throttle travel) with the T.D. control switches in AUTO the T.D. system will give or take fuel to match THROTTLE position to a preset TIT temperature. The fuel flow data is not used by the T.D. sys! So, if there's damaged thermocouples your T.I.T. indication is wrong and you should ALWAYS assume the T.I.T. input to the T.D. sys is wrong too. With damaged thermocouples the FUEL FLOW is more correct for measuring engine power.
You want to play it safe especially while flying by taking the T.D. system's TEMP CONTROLLING feature out of the picture by switching to NULL because the T.D. sys only knows what the thermocouples are telling it. In NULL the T.D. sys is no longer trying to match the T.I.T. to the throttle position (above 65 degrees). If you have damaged thermocouples then your T.D. sys has wrong information! You don't know the real problem until you get on the ground. You have bad thermocouple(s) AND your engine could be damaged (F.O.D., damage from overheat, incorrect fuel nozzle spray pattern or fuel control problem) and you only want to cautiously troubleshoot this problem on the GROUND.
Your EP's state fly in NULL so that the T.D. is no longer trying to match T.I.T. data. Pushing your T.I.T. to 910 degree for a temp controlling check is not a good idea because the T.IT. is higher (maybe much higher) than the indicator shows. Don't troubleshoot this problem in flight because you will most likely further overheat and damage the turbine!
-
Amazing find CGRetired! Sure like to know the story of this bird and how it ended up there. BAE or L3 or maybe just an airplane lover with a place to put it.
-
Where's the damage?
-
United States Sends New Weapon System to Fight ISIS;
Air Force General Standing Behind the Weapon's Effectiveness Says, "Those terrorist som 'bitches asked for it"
-
-
How about it Dataman, inquiring minds want to know
-
MY GOD SCOTTY, IS THAT MY SHIP, ENTERPRISE?
Tell Spock we've got the modification, warp drive as soon as the photon torpedoes are loaded. We've got Kligons to kill!!
-
Paint it VN green camo. The gray doesn't represent the era and doesn't look as cool either.
With that said, I'm glad someone cares enough to restore it to keep it looking good.
-
58 minutes ago, Railrunner130 said:
I just can't believe that it's nearly a $1.5 million job to install wiring and whatever hardpoint modifications need to be done.
Railrunner, I believe the cost includes engineering (non-pylon tank airplanes), if you can believe that. In fact, I've heard of costs up to $10M and years of testing to be able to carry relatively light drones. A full 445 gal pylon tank will weigh more than 3,000 pounds (based on 6.8 lbs/gal). I wonder how much the LITENING pod weighs?
-
Assuming one aux pump may be overloading the ATM generator. Check your ATM gen load for each aux pump (energize one prop aux pump at a time) to find out if one of the aux pump is drawing more power than the others. This may indicate the pump or wiring is going/bad.
-
Too vague. Attach photo please
-
On January 20, 2016 at 9:00 PM, Casey said:
The US Department of Defense (DoD) has selected Rockwell Collins as the prime contractor for the C-130 Hercules fleet upgrade and supply of associated equipment to Pakistan.
Under the terms of the $30m contract, the company will design, manufacture, integrate, train and deliver 11 C-130E model kits and five C-130B integrated avionics suites and kits to Pakistani Air Force (PAF).
In 2014, Pakistan placed a request with the US for avionics upgrades, engine management and mechanical upgrades, cargo delivery system installation, and replacement of outer wing sets on six of its C-130B/E aircraft.
Powered by four Allison AE2100D3 turboprop engines, the C-130 aircraft is designed to conduct airborne assault, search-and-rescue, scientific research support, weather reconnaissance and aerial refueling, maritime patrol and aerial fire-fighting missions.
It sounds like Rockwell Collins is only doing the avionics upgrades. Does anyone know who's doing the engine upgrades, cargo system install, and outer wing replacement? Maybe Rockwell's ARINC arm?
BTW, when did they put C-130J engines on B/E's? ;-)
Fred
-
On November 29, 2015 at 4:09:40 PM, saikojer said:
INDICATION AT CROSSOVER.
Torque : 1400lbs
TIT: 678℃
Fuel Flow : 990
No.4 engine RPM overshoot to 103.3% RPM on power advance with pitch lock symptomps.
+ RPM fuel governed out of limit.
- pitch lock regulator - still persist.
New snag after a week :
No 4 engine nil low pitch stop.
No 4 eng RPM overspeed with TORQUE, TIT and FUEL FLOW, LOW at crossover with RPM overshoot to 104%.
* SATIS but torque anticipation very slow during advance throttle.
*Throttle already at FLIGHT IDLE, TQ remain : 1.40 lbs.
-After about 10 sec TQ increase to 3.4lbs.
*Advance throttle, RPM+FUEL FLOW + TIT increase with low TQ until RPM overshoot until 104.4%.
- Retard throttle, RPM drop and TQ can SLOWLY can achieved 7.5lbs.Saikojer,
It sounds like the fuel scheduling is good. The RPM increases all the way up to 104.4% because of a lower blade angle. Then, eventually the torque increases to NORMAL (matches symmetrical engine).
- Does the RPM decrease (matching symmetrical engine) as the torque increases?
Your low pitch stop problem:
You may not have a low pitch stop problem. Push the throttle to crossover and give the propeller angle more time to increase past 25 degrees (match torque with the symmetrical engine) before retarding the throttle back toward FI. The blades may need more time to increase the pitch.
- What is the torque at crossover? You mention above that it's 1,400 in lbs but, doesn't it eventually increase?
-
Saikojer, did you replace the the pump housing? How long does it take to go from REV to feather using the aux pump? Wondering if you're pump housing is bypassing pressure between the two sumps (pressurized and atmospheric). This might keep you from changing (increasing) blade angles.
-
Ya Mark, I saw at least one at Pt Mugu with VR-55...
-
Casey, thanks for the information. I read that Coulson sold the RADS XL (gravity) air tanker systems for these 7 Herks. More agile system than MAFFS II and performing well in Australia right now on tanker 131.
Maybe I missed it but, I thought the Herks were getting new CW's and/or OWs (?) compliments of the AF....
-FredG -
Lucky crews! On one hand, I think automation is the biggest challenge facing pilots today and in the future. How many crews turn on the AP on climb out and then leave it there until their approach...or longer! I think many of these commercial flights like Air France over the Atlantic and the one that just happened, AirAsia flying to Singapore, hit bad vertical winds and the pilots tried unsuccessfully to fly those planes by hand. In my mind they mis-interpreped the airplane's cues and lost control. More pilots should go through upset recovery training so they can experience those unusual attitudes and get themselves out of that situation.
On the other hand, what happened with TCAS on these airplanes? Why didn't TCAS see the other airplane? It was because the crews were too reliant on TCAS they didn't do normal scanning.
There's nothing wrong with automation if its used as a tool and not as a crutch! These guys will never put so much faith into TCAS again.
Pass on lessons learned!
- FredG (Armchair Crewman) -
GVS - yeah I remember those blankets. They were used for keeping the struts warm(er) while flying. But sometimes they would arc against the strut causing strut replacement if it was bad enough.
-
The main problem with really cold temps is strut leaks and you can say the same thing for sand. I think there's an actual number but i've forgotten what it is but when the temp gets below freezing you might want to stuff a preheater hose in the WW before TO. In sandy conditions when the struts aren't wiped down the grains of sand can scratch the chrome/damage seals, again, to cause strut leaks. As far as the raising or lowering of the gear...just make sure the tracks and ballscrews are cleaned regularly.
-
DC10FE, I think your right. I'm sure it had terminal cancer after all those years of sitting around in the tropics. Too bad.
-
Okay, good.
-
Capt. Howdy (great name),
If the mission were a tactical one (going over enemy lines, etc.) then the crewmembers would wear a survival vest, which has an emergency radio in it. Being in the Navy IF we flew those types of missions we would wear the SV-2 vest (pictured below without the inflatable bladder) but typical of overland C-130 tactical missions. I’m not sure what the Air Force wears. But, the point is that if the mission is tactical they will wear some kind of survival vest that have a couple of things in it to grab someone’s attention. 1) Radio (PRC-90 or PRC-112), 2) a signal mirror (good for getting a tailing fighter pilot’s attention) and 3) a rescue strobe light with IR lens attachment to be seen by people wearing night vision goggles.
[ATTACH=CONFIG]3990[/ATTACH]
Which radio you use depends on the era your filming.
[ATTACH=CONFIG]3991[/ATTACH]
PRC-90-1 & 2 (this radio goes back to the Vietnam era and up through late nineties (maybe):
• Frequencies –
o Voice 121.5 and 282.8 and the
o Emergency beacon 121.5 also
o Button for Morse code
PRC-112 - is the most current
• Frequencies used were combined UHF/VHF
• Later models had GPS that could transmit encrypted information about the position
• Two-way communication through satellites
Anyway, if I were in a bad situation like that, that's what I would do. FredG
C-130 News: Officials confirm C-130 Hercules military plane went down near Savannah
in 2018
Posted
Airplane looks slow on takeoff and slow in flight.