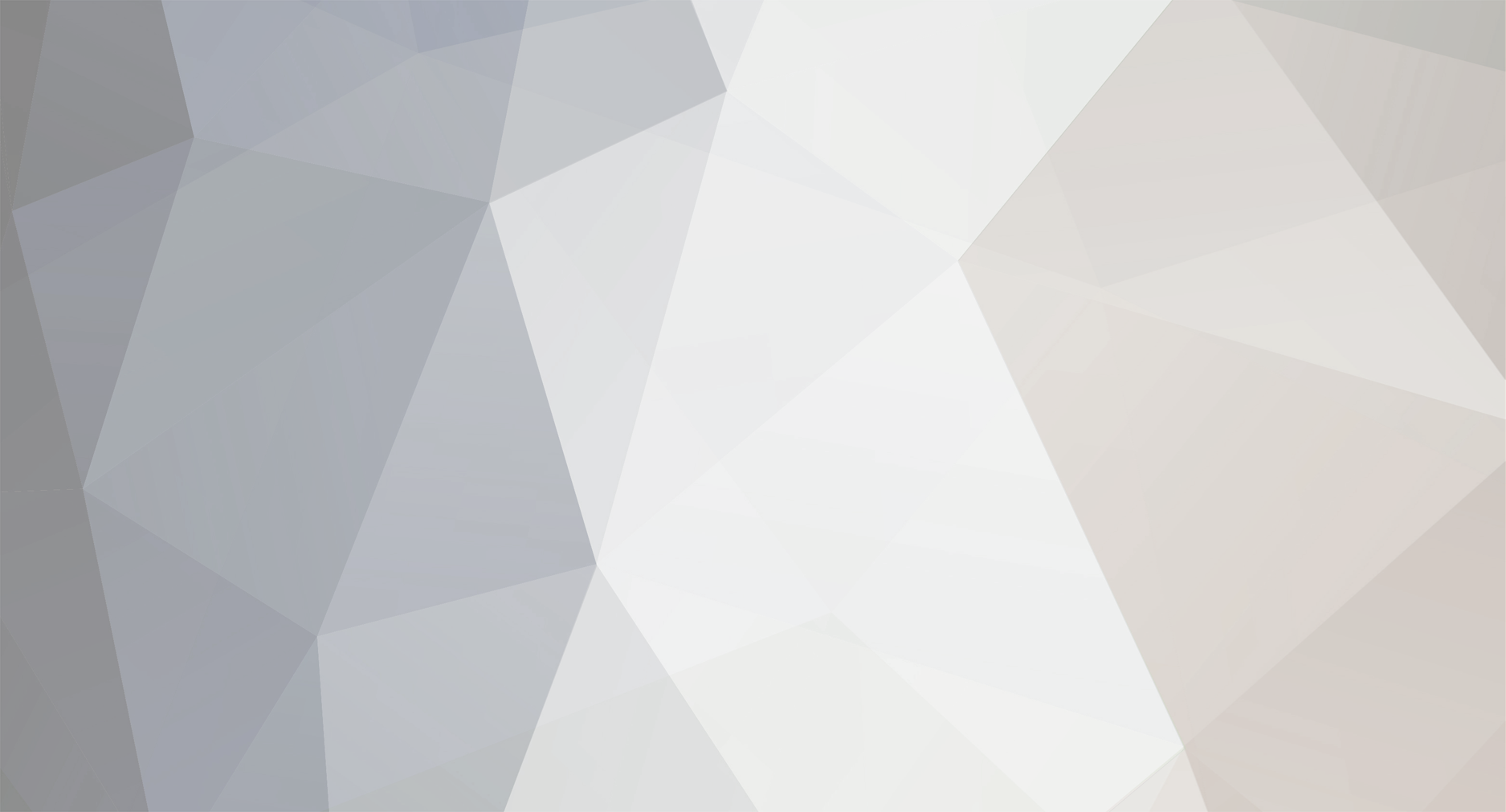
jakesnk
Members-
Posts
13 -
Joined
-
Last visited
Never
core_pfieldgroups_2
-
First Name
ANGELO
-
Last Name
GIAKOUMIS
core_pfieldgroups_3
-
core_pfield_11
HELLENIC(GREEK) AIR FORCE(HAF) C-130B/H FE
-
core_pfield_12
GREECE
jakesnk's Achievements
Newbie (1/14)
10
Reputation
-
Multiple engine power loss/stall/rollback(B models)
jakesnk replied to jakesnk's topic in C-130 Technical
The ice detection system operation depends(among others) on the ice detector. If the airplane is equipped with a mechanical probe the system starts functioning when the airspeed over the detector reaches 40knots. On engines with a solid state ice detector the system becomes armed as soon as power is supplied to the detector. In both cases condition lever has to be in the run position and in the first case the engine has to be running, in order to have flow around the probe(on the ground). When the test is performed during taxi, the whole circuit is tested(continuity, relays, lights, timer etc) and not the ice detector. So in order to test the ice detector you have to bench test it on the shop. Please correct me if I am missing sth here. Anyway my consideration is 4 engine power loss and I am thinking about requesting a similar scenario in the flight sim, next week.... -
Multiple engine power loss/stall/rollback(B models)
jakesnk replied to jakesnk's topic in C-130 Technical
Very interesting story DC10FE! I read recently a report from a similar incident from another military operator, which is still under investigation. In your case how did the FE specifically understood during taxi that #3 ice detector was inoperative? -
Multiple engine power loss/stall/rollback(B models)
jakesnk replied to jakesnk's topic in C-130 Technical
1685FCC, Is the TCTO 1C-130-1281, the one you mention? -
Multiple engine power loss/stall/rollback(B models)
jakesnk replied to jakesnk's topic in C-130 Technical
Our B models(ex USAF airplanes) don't have this TCTO installed. We had a lot of discussions with my colleagues here about this malfunction and lots of diferent opinions. So we think, the only option would be to decouple an engine by placing the throttle to ground idle. We choose an INBD engine, in order to have better chances to control the airplane. This will bring one generator back on line, powering the ESS AC and ESS DC bus. After that drop RPM below 65%, have the engines restarted and continue with 3-engines operation. It sounds quite risky and desperate but like US Herk wrote we will have the rest of our life to figure it out!. Thank you guys! -
Multiple engine power loss/stall/rollback(B models)
jakesnk replied to jakesnk's topic in C-130 Technical
Exactly my point! So, if a B model airplane experiences a 4 engine flame out, it is unlikely to restart the engines.... -
In case multiple engine flame out occurs, immediate corrective actions as described in LMA supplement No C-130-64 (TD null, PROP mechanical, bleed off, APU GEN ON etc), will bring the engines on speed. I ‘ve tried it a couple of times in the simulator and it really works fine! My concern is about old B models equipped with GTC/ATM GEN. As soon as the engines flame out and the bleed air pressure in the manifold begins to decrease, I am not sure if the remaining bleed air will be sufficient to operate the ATM Gen for enough time, (given the time the crew needs to identify the situation) in order to restart at least the first engine. I’ve tried it on the ground (only with GTC supplying air) and as long as GTC bleed air valve is closed the time for ATM gen out light to illuminate seems very short. Also there is no B model sim available in order to test this one. Any B model expert suggestions or tips on multiple engine power loss?
-
I am dealing with a lot of "low performance" problems with cargo compartment air conditions of old B models. And by "low performance" I mean insufficient airflow especially during colder settings(AUTO & Manual) and especially on the ground or low altitudes, causing discomfort to the crew and passengers during summertime(temperature regulation seems normal). The problem is the same both with engines and/or GTC supplying air. Things get a little better as the airplane climbs in a higher altitude. The air condition heat exchanger most of the times is found to be repaired or overhauled. Apart of the heat exchanger I think that the flow can also be affected by the shut off valve. Also no obvious leaks are noted in any case. Not sure about pressurization issues, since we usually fly the B airplanes from FL100 to FL140. We begun by replacing the water separator relief valve and bag, the shut off valve, turbine and after that the heat exchanger(repaired). No significant changes. Since the B model heat exchanger is quite hard to find in the market and quite expensive, any other ideas about what could affect the air flow and the performance of the cargo compartment air condition?
-
Thank you for the tips, Moon. While further investigating this one, we found pieces of the damaged pressure hose(the one I mentioned was found worn) inside an orifice check valve installed in the dry bay(don't remember the P/N). We replaced the valve, assuming that this would not allow the pump to have a proper output pressure. I will also try your tips and let you know.
-
Could you please let me know which manual states this ?
-
This was my first approach on this one. Everything OK! But after finding the damaged hose and since this is the only aircraft whose aux pump cannot support 4 engines, I thought about investigating a bit more......
-
The model is a C-130H. Its LH AUX Fuel Pump is rated 38psi(static-no demand). During flight and as long as crossfeed valves are opened this pressure drops. Finally with the AUX pump ON and four crossfeed valves open the output press is 20psi, causing the AUX tank empty light to illuminate. The three solenoids of the pump were measured and found ok. But, suspecting an internal mechanical failure of the pump, the pump was replaced. The discrepancy remained after the following flight. More careful inspection revealed a damaged pressure hose(the one connected on the pump). The damage was not so obvious, since it was in the internal part of the hose. Anyway, the hose was replaced and the airplane was dispatched for flight. Unfortunately same discrepancy, even with a finding. My guess is that an internal leakage of a line inside the aux tank, by-passes fuel and causes this press. drop. I am not really familiar of the AUX tank internal components and bladders internal arrangement. Any ideas what to look for?
-
Thnx for your reply. Looking forward for corrective action details.
-
Rudder Boost Pressure (with flaps up) should be normally 1100-1400psi. IAW the limitations section of the FM, 1400-1600psi is caution and 1600psi is the maximum allowable operating pressure. So, if the rudder press. is 1600psi(with flaps up) would you consider that a discrepancy? What could be the corrective action(i.e. transmitter?)