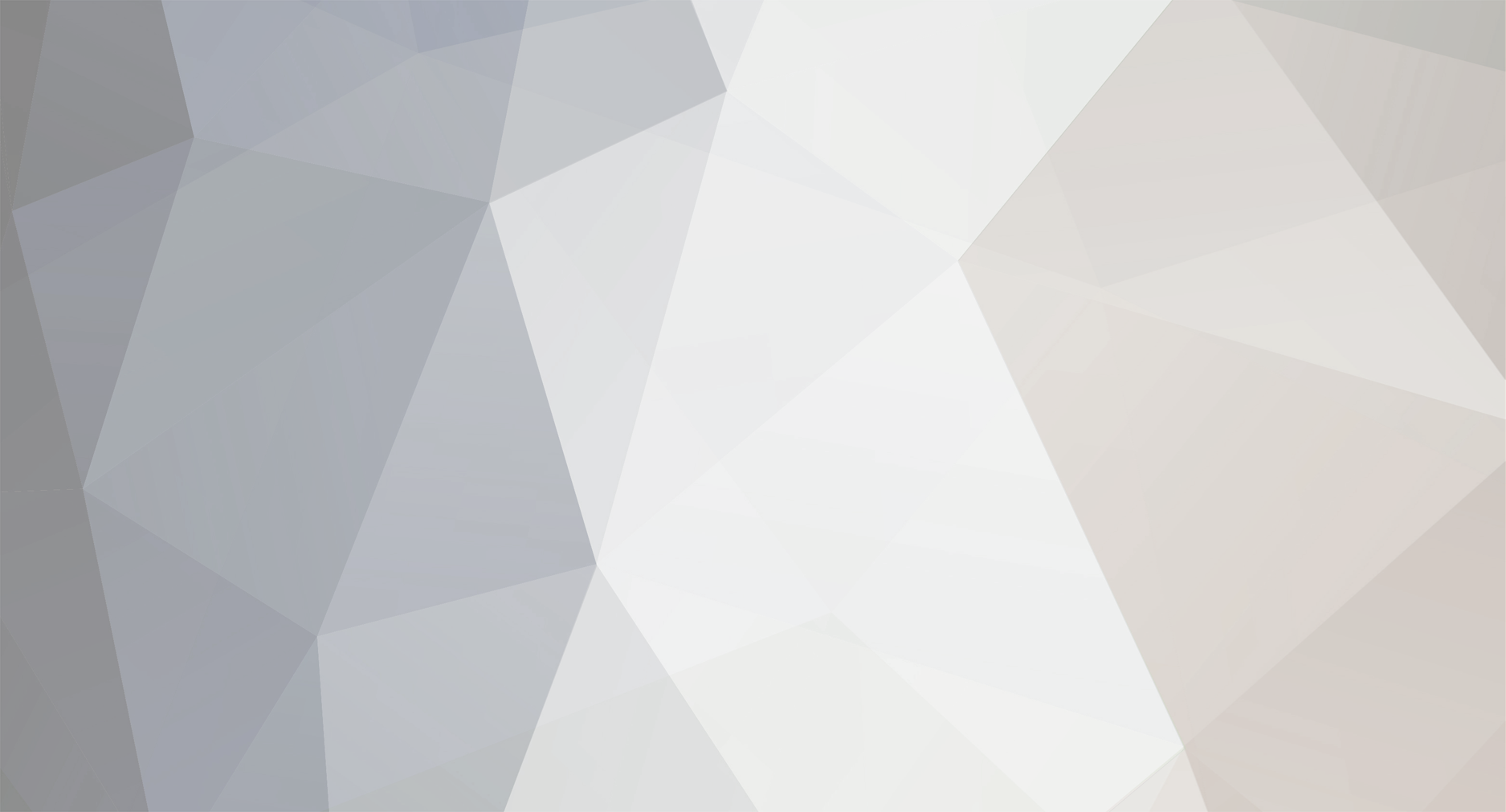
Steve1300
-
Posts
246 -
Joined
-
Last visited
-
Days Won
2
Content Type
Profiles
Forums
Store
Gallery
Downloads
Calendar
C-130 Hercules News
Posts posted by Steve1300
-
-
I'd bet that would be hard to find. I'm trying to picture the alpha shaft swinging enough weight under vibration to move the input lever one way or the other to make the throttle creep. Something are tough to wrap my head around.
Thanks, I'll be on the lookout for that.
-
Our SRM is fairly new and says the same thing. I don't think it is a mis-print. I do seem to remember that the aileron, when in the jig, tilts up while the others hang down.
-
It was tricky trying to replace the anti-collision light bulb on that ladder, but it was even worse using that ladder during a rudder removal. Should have recieved hazardous duty pay for that!
-
pjvr99,
I have recieved a lot of valuable info from you in the past. I am hoping now that you can do it again - would you be able to explain how a valve housing can cause throttle creep? I can't say that I have ever experienced that, but it is not at all unusual for me to find new and different problems.
Thanks in advance
-
Unless the hydraulic fluid is really old, it would be easy to tell a thrust nut leak from a prop leak. I have seen hydraulic fluid that looked like engine oil.
Remember that a warmed up prop should not leak except the maintenance manual limits of one drop every 45 seconds. That would not consitute a "visible fluid leak" in flight. That can give you evidence of a leak after landing.
The start of this was "visible fluid leak."
I'd bet that having a bad prop that will not feather in flight would cause folks to be kind of touchy about bad props.
-
Just to keep the chat on the even keel that we all want -
Pilots and engineer get intimidated into flying an acft that they don't want to fly.
Mechanics get intimidated into perfoming maintenance actions that they know aren't right.
It takes a real backbone to stand your ground, and sometimes we can't find someone with a backbone - and if we do, he or she stands to lose in the end.
Safe is safe, whether you are in Sandland or in the CONUS. If an unsafe act become safe just because you might have to sleep in the Herky Hilton, then you may want to question yourself about how "unsafe" it really was to start with.
-
In the USAF, our guidance is 4T-1-3, or it used to be. I've been out too long to be sure any more. For website guidance, look at:
http://www.goodyearaviation.com/resources/pdf/inspection.pdf
-
Oh, my gosh! The dreaded "three engine landing!" I don't know... sounds pretty risky.....
Can you get airborne? If you do, can you land on three?
Maintenance signs it off? How? Replaced lost fluid? Does anyone think that the maintenance guy would be afraid to fly with you? Somehow,I don't.
-
I am trying to do a bit of research on C-130 main landing gear malfunctions. It seems to me that operation in the Mideast has its own unique problem areas. Those of you who are involved in C-130 operations in sandland: are you experiencing any problems with gear that will not retract or extend? Is the problem exacerbated by cold temperatures?
Thanks for any information.
-
Around 1974 HS came out with a mod (service bulletin no. 39) to the pump housing which incorporate a dip stick for the atmospheric sump. The new dip stick was to aid in proper servicing. The dip stick had an OP LEVEL band and if the fluid level was in the OP LEVEL band while the aux feather pump running things should be good.
After many static fluid leaks from the rear lip seal in 1981 HS came out with a mod (service bulletin no. 101) to the atmospheric sump dip stick. The bulletin had you remove existing markings from the dip stick and remark one line just about where the old OP LEVEL lower mark was and this becomes the new FULL mark.
Now if there is any runback of fluid from the pressurized sump to the atmospheric sump while the prop is static the likelihood of a rear lip seal leaking due to overfilling is less.
Our HS rep told us that after initial prop servicing there is no need to open the pressurized sump cap to check levels. We safety wired the caps closed to remove the temptation of opening them. This procedure worked well.
Feb 1970 Service Information Release, Code SIR 54H-72 was issued which read:
“54H60 Propeller Servicing Procedure
Originally the various HS manuals specified that at the time of servicing 54H60 propellers, the No. 1 blade would be positioned in the 12 o'clock position. The theory that the beta feedback shaft would assist in purging entrained air has subsequently been proved invalid. There is no apparent difference in rate of air purging regardless of the location of the No. 1 blade.
In view of the foregoing, the requirement for prepositioning the propeller for servicing has been deleted from all publications as they have come up for revision. Naturally there is no objection to positioning the No. 1 blade up-right prior to servicing any more than there is an objection to positioning it downward. This point is brought to the attention of all concerned in order to simplify to the maximum the already complex servicing requirements for this propeller model.â€
Vic
You might want to tell the folks at Hamilton Sundstrand about that. I attended their training course a couple years ago, and they disagree with this publication. They still instruct us to park the blades at 12 o'clock. If you have even pulled a pump housing off the prop, you would see just how fast the fluid leaks past the Beta feedback shaft.
The latest revisions to our maintenance manuals still require the #1 blades up as well.
Yup, you may have to inform the manufacturers........
-
I'd like to thank all of you guys for your responses. We have stopped many of our "NOSE BLEEDS" by spending more time figuring out where our fluid levels really are and by parking our #1 blades high at the end of the day. It is simply amazing what paying attention to tech data can do for you (and sometimes, how it can screw things up!), so maybe Hamilton Sundstrand might one day actually explain the relationship between the atmospheric and pressurized sump dipsticks. We know now that it takes two dipsticks to ensure proper fluid levels and not just one.
We still seem to get more pump housing front cover leaks, but it looks like those are coming from clogged valve-housing vents if not from corroded or warped covers.
I guess that is why maintainers have a job...... nothing works ALL the time.
-
He gets a "two-thumbs up" from me!
Hard to trust politicians now, but once in a while; ya gotta take a shot.
-
For those of you who sit left seat, but happen to be avid maintenance oriented types as well, sorry if I made it sound like you guys are too ignorant to talk about thermocouples. In every norm, there are exceptions.
If I wanted to discuss the faults/benfits of GCA/PAR or reliance on GPS approaches, I wouldn't look my for A&P for advice. But that's me.
There would also occasionally be an A&P who is into that kind of thing, but it is not where I'd go looking.
-
There are a bunch of folks who think that the Herk is obsolete. Those same folks never deal with the small airfields, small cargo areas at those airfields, or those dirt runways. The C-17 can haul the freight, but you had better provide the large area for it to work in. In the area that it takes a C-17 to taxi in, turn around, unload, and taxi back out, you can do three Herks.
They don't have the same capability. They don't require the same amount of fuel and handling.
We probably should not mix apples and oranges in the argument.
OH, before it sounds like I am a Lockheed cheerleader, I still think Lockheed made a big error in closing down the H-model line. They put all their eggs in the J-model basket, and THAT was a mistake.
-
I welcome you to the group. I would suggest,though, that if you have a question concerning the usefulness of thermocouples, that pilots aren't the folks you need to speak to. You might want to speak with those who install them, inspect them,and replace them.
In this forum, as far as I know, your questions can be posted here. There are some career engine folks who answer posts here to have been dealing with thermocouples longer than other members here have been alive.
-
We experience a shift in start temps also when moving around the country. If we move from a low altitude high temperature location to a high altitude low temperature location, we have a shift of start temps. Sometimes, it becomes a problem, so we make adjustments for it.
According to our friends at Rolls Royce (Allison), we adjust the TD amp potentiometer only to limit the start temps, not to "control" them. We control start temperatures with the "null orifice" adjustment on the TD valve:
Quote: After changing an engine or replacing a temperature datum valve, or if a previous
start exceeded 830°C (Refer to 72-0, Table IV), adjust the datum valve to give a maximum starting temperature of between 750 and 820°C.
Allison and Lockheed has stated in other locations that start temps below 750 can be acceptable as long as the start was smooth and within time limits.
When the start temperature has shifted and you find that a null orifice adjustment does not fix the problem, then Allison gives us a possible fix at the fuel control bellows.
Quote: B. Adjustment of Inlet Temperature Compensating Bellows
(1) Adjust retaining adjustment nut at compensating unit housing clockwise facing
rear of engine to decrease start temperature.
(2) One flat of the adjustment nut is equal to approximately 25 degrees TIT.
CAUTION: DO NOT ADJUST MORE THAN TWO FLATS. THIS ADJUSTMENT
SHOULD BE MADE ONLY AFTER ALL OTHER POSSIBLE CAUSES
HAVE BEEN THOROUGHLY INVESTIGATED. GET ENGINE HISTORICAL
RECORDS TO REFLECT NUMBER OF FLATS ADJUSTED
MAXIMUM POWER RUN REQUIRED AFTER ADJUSTMENT.
-
I think it is always a good thing to have new blood on the board. Welcome!
-
Yes, the RDL on the stubby is 30" fwd of the nose and on the stretch is 130".
And when referring to Mean Aerodynamic chord, the actual 15-30 % envelope is very small in relation to the overall size of the wing.
There is a difference in stretch versions then. Our civilian reference datum is right at the reference screw just forward of the forward nose gear door, about 70 inches forward of the nose landing gear strut. While I have a reference put out by Lockheed that states that to be true, I can then provide evidence that it is not since FS 245 is at the same location on our aircraft as it is on stubby C-130s. There are many disagreements between our books and the Type Certificate Data Sheet. I guess it has never been important enough to correct.
I certainly agree about MAC being the same since the wings are the same. Procedurally it is different in the computation, but the end result does not change.
-
Had to stop using the stuff it was too corrosive especially for the landing gear struts!!
Really? Yours must be different than ours then. We still use 5606 in our aircraft, and we have found that 5606 is as good as CPC under the floor panels.
The USAF changed from 5606 to the currently used hydraulic fluid purely because of flash point. A prop leak that ends up in the brush block using 5606 sometimes catches fire. I guess the new hydraulic fluid won't do that?
-
If we read both the Commerical Service Letter and the service bulletin put out by Allison (Rolls Royce), we can see that the information about the advantages of using low speed ground idle was submitted both military and civilian aircraft using the T56 and 501D engines. It was rare if not impossible for civilian engine users to get JP8 at that time that those letters came out. Allison did say in their information about the need to clean and flow check the fuel nozzles that, while they recommend it be done every twelve hundred hours, that those who use JP8 have changed the intervals to 600 hours.
-
Steve1300,
Coast Guard FEs are fixers and fliers. All aviation maintenance personnel are also aircrew qualified. Most CG personnel going to FE school have at least a year of maintenance experience. It took a while, but each C-130 airframe now has a tool box bolted to the airframe just aft of the "atomic toilet." (RH side flush model) Not a big division of labor due to our size so everyone gets plenty of experience fueling, towing, wrench turning etc.
I understand that. The retired CG guys I have met who were F.E.s were pretty sharp on the Herk. Some branches do it better than others.
-
The bulletin from Allison has been around for quite a while. It does not blame the procedure on any specific type of jet fuel. It does specifically state that the temps need to be reduced to prevent coking, so we need the two minutes at LSGI prior to shutdown.
When we get clogged fuel nozzles, we can get "burner can" damage as well as burned turbine vanes and blades. It is a bad deal all around.
-
Back in the early 80's you had to come from a mechanical background to cross train into the FE career field.
Yeah, what goes around comes around.
It has been a few years now, but there was a report that the AF was taking folks out of tech school into FE training. I don't know how that stands now, but I was a bit shocked when I heard it back then.
I guess it all depends on how short-handed the AF gets in that career field.
The RGB cover plates were part of the aircraft equipment. I remember when we had overhead racks on the trash-haulers, we bolted those plates onto the bottom of the overhead racks for storage. They got lost way too easily if left loose.
-
I have known F.E.s that were good enough at switchology AND maintenance to be called flight mechanics. Many of them were VN vets and early crew chiefs - back before MAC decided that crew chiefs were loadmaster assistants. In that early to mid-70s in the USAF, that all changed.
The people taken in the F.E. training program were taught classroom systems classes and theory, but never actual maintenance. They were cross trained out of career fields like cooks, cops, and admin. They became systems operators rather than mechanics. I don't know what the Navy or Coast Guard did about F.E.s then.
I think all this was called "progress."
Throttle Creep
in C-130 Technical
Posted · Edited by Steve1300
Thanks again.
Wear and loose things add up.