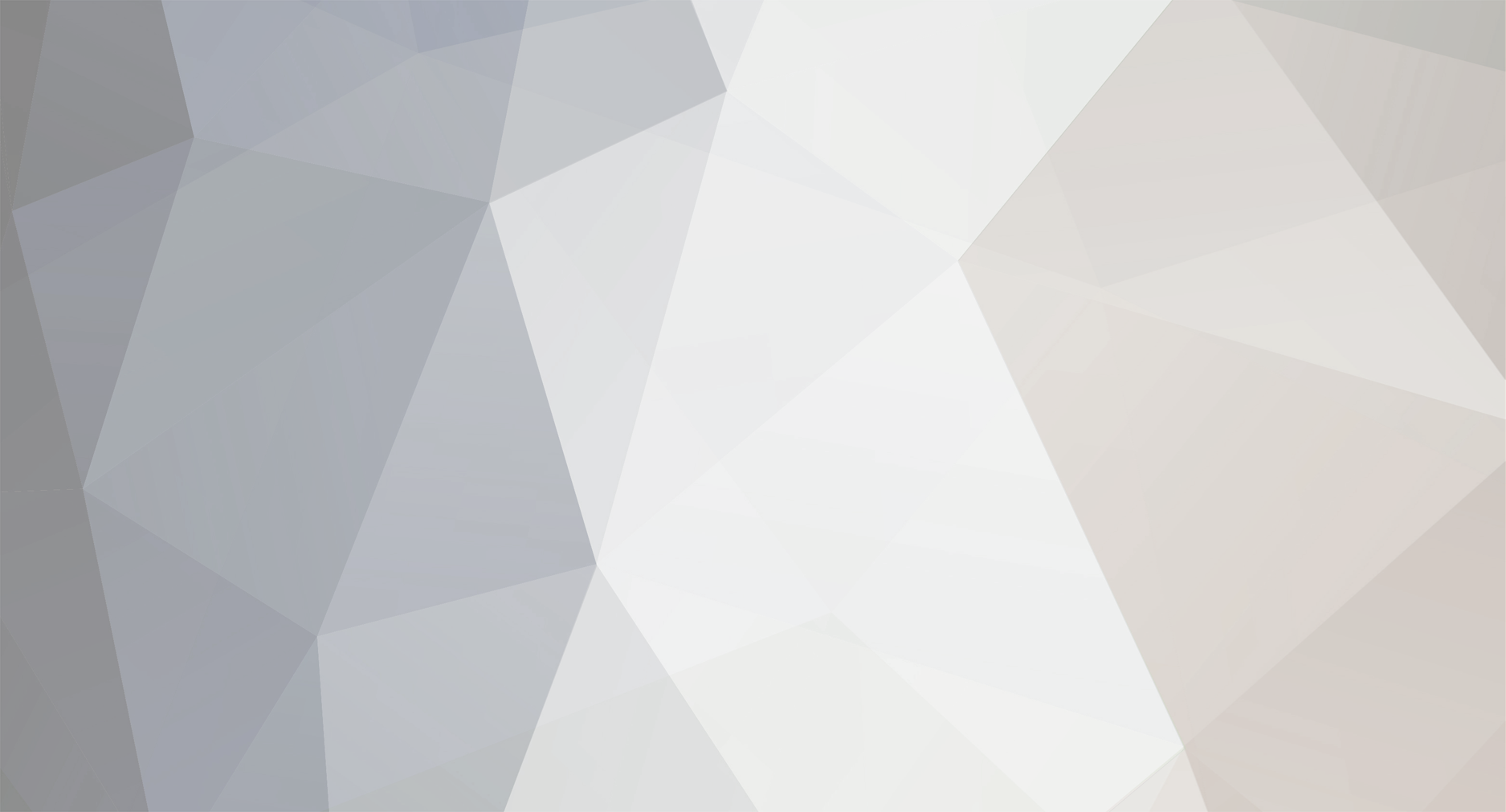
BDizzle
-
Posts
73 -
Joined
-
Last visited
Never
Content Type
Profiles
Forums
Store
Gallery
Downloads
Calendar
C-130 Hercules News
Posts posted by BDizzle
-
-
Different densities, so if you fill the tanks up to the same level they will weigh different amounts. Or, if you have the same weight the volume will be different. And the densities change with temperature too. The tank compensators are supposed to correct for that so if you take a stick (it doesn't even need markings at all) and the symmetrical tanks have the same level in them then you know the tank with the inop gauge has the same amount as the opposite tank.
-
BDizzle
Could be but it was with two other pics that clearly showed 1505. Also look at the new flight instruments. 68-10935 never had new flight instruments.
By the way the URL you posted for 1505 subtitle was 1505 but the pic was of 1504.
Bob
The photo was 1504 but the news story says "On Wednesday, August 22, Minister of National Defence Tomasz Siemoniak participated in the ceremony organised on the occasion of receiving the transport aircraft C-130 Hercules No. 1505 as a part of equipment of the 33rd Transport Air Base in Powidz."
And according to this story they were all upgraded before we gave them to Poland so that would explain some better avionics.
-
I think it's just a case of the person who wrote the caption getting their tail numbers mixed up.
1505:
http://xairforces.net/newsd.asp?newsid=1762&newst=4#.UeMFM8u9KK0
1276:
http://jetphotos.net/viewphoto.php?id=7418511
Maybe just waiting for someone to paint 1505 on the tail.
-
Speaking of school, if you want to fly the AFSOC or ACC herks you have an additional 4-5 months of training compared to slicks, but there are only a few places you can go.
-
The screens are hit and miss, some engines have screens on both the upper cooling air outlets, some just one of the two, and some none at all. At least on the Es and Hs I've seen. I don't know if that's just how we get the motors from depot or what.
-
The units that have openings might be because of retainability problems... cost of living, bad leadership, etc. and flying as a reservist is much more difficult than being in maintenance. Not only do you have your normal drill periods, you also have additional AFTPs and currencies. It means for the first year or two until you get real good at FE-ing you'll need to commit to at least one flight a week to stay smooth and keep your currencies green.
-
For a normal takeoff it does say to start rotating 5 knots before takeoff speed in the USAF book.
But on a max effort (short field) takeoff it says to "accelerate on the runway to takeoff speed."
-
I never fully trusted the acceleration check times. I think they're padded far too heavily on the acceleration side and additionally, don't compensate for higher density altitudes very well. We were always taught to use the highest speed we could to get a more accurate time, but all that does is cut into your margin even more. Far too many times I looked up when the Nav called "time" and asked myself the question, "could I stop from here if I had to?" and more often than not, the answer was, "I don't think so"...this seemed to be far worse at high DA.
I have been told to use lower speeds because you can identify the problem (failure to accelerate) earlier and stop easier. We're usually going faster than charted because most engines do better than 95%. I wonder though, if you were torque limited in cold weather if the check time would be more accurate because you can't use more power than the chart assumes. Another variable is the 3 second delay built into the 1-1 refusal speed, and at 100 knots you'll burn up an extra 500' of runway in that time, but that's supposedly included in the calculation.
-
I pay closer attention now to what the pilots are doing and when my low pressure lights actually turn on or off because we had several airplanes where you'd start the first engine on a system and both warning lights went out due to a faulty check valve. I don't know how common it is for the total fleet but I had a long stretch where that seemed to happen every few weeks.
-
The very first check ride of my flying career was the worst. After flying with the same instructor and proving what I knew to him things were going pretty smooth, then when my check ride came for mission qual at Little Rock I got the wing stan/eval evaluator. He grilled me about limits and nomenclature about the weirdest things on that airplane. Then when we were flying he was asking me things about navigation and timing to test my SA. At the time I was brand new and could barely keep up with the airplane when we were flying straight and level, much less on multiple airdrops with an EF watching me. I thought for sure I'd failed that ride and didn't know anything. In the debrief he said that I was doing pretty good so he started asking me questions to show me what I'll have to start thinking about later in my career when I get better. That wasn't very nice! He scared me into thinking I had failed while he was really trying to help build my SA.
-
The "vol3" is the USAF book "Operations Procedures" and there's a slightly different version for each variant and command.
Absolutely you have to recalculate for bleeds closed, I didn't mean at all that you should just close the bleeds to make up for a lack of torque with them open. You also do have to reduce TIT for cold weather to avoid exceeding torque but minimum torque is still whatever you come out of the chart with. In the example for my particular variant the 970 "normal" number works for the vast majority of our operations but is not a blanket number.
-
If you do not get Cal TQ you "should" abort the takeoff... Not a SHALL but...
The vol3 says that if you can't make torque with the bleeds open then you should close them and recheck torque to determine if it's an engine problem or a bleed air system problem, but either way you will not fly the airplane.
As for minimum torque, 970 is the normal TIT for takeoff, and you have to make 95% efficiency, so the minimum torque for takeoff would be whatever the predicted torque is for 970 degrees at 95%.
-
So why would you cut a hose? I have landed with one in trail several times with very little damage to the hose and drouge.
In the MC-P book it is mandatory to chop the hose if more than a few feet are stuck out.
-
I've always used the HP48, but the part number for the program cartridge isn't loaded in the US Air Force supply system. You might contact a tech rep with Rolls Royce to see what they can do for you. I hear there is a newer calculation that is supposed to be more accurate and more generous, but I haven't seen it come my way yet, so it is just rumor as far as I know. Theoretically, the more humid the air is, the less power the engine should be expected to pull, so the efficiency numbers should be higher on a humid day than what we currently calculate.
I've never seen any of these calculators, but out of curiosity, how do they compare to the 1-1 charts?
-
Yeah, I have never agreed with that limitation, if I had gone out to an E mod or a MC-P and we didn't have significant pressure by 20 or 30 % we had a problem. Only times I didn't see almost system normal pressure by on speed usually it was a shelled pump; I think I would shut down and at least check filter buttons before pressing on with a pump that didn't read normal until 30 seconds after on speed.
Usually by the time I look from the oil pressure gauges to the hydraulic pressures it's passing though 1,000psi, typically at about 30% like you said. Sometimes the light goes out before we even have ignition.
-
The biggest problem I run into is when I show up to an airplane I haven't flown in weeks and there's a leak somewhere. The crew chief tells me, "Oh yeah, it's within limits." Who checked it? When was it checked? Where is it leaking from? How do I know it hasn't gotten worse? If I land off station I don't know how much fluid to expect coming out of it. I don't know if there's an easy answer but I'd rather call engine/hydro/whoever and have them re-explain it to me instead of taking chances on third person information. I think it's the same as an inop fuel gauge. The crew chief tells me it's already been dipped and verified but I'm going to do it again personally. Not because I think they're idiots but because I'm the one who will be in that airplane when it runs out of gas because someone assumed someone else checked it. And that is also why I might refuse to fly an airplane that has an "acceptable" leak.
-
Some of the crews now have never seen what a herk can really do, or don't have the systems knowledge and are scared of minor discrepencies. While it's our job to know when to ground the airplane it's also our job to know what we can safely fly with when there's a real mission to get done. I've seen more FEs who will explain to the crew why they should go fly than not.
Never thought of trying to spin the prop backwards myself though, maybe I'll do it just to see what my crew chief says next time...
-
Sharif,
I have never heard of any limit associated with fluxing voltage, I can't even begin to imagine the damage that would do to the equipment on that AC bus.
Ron
Do B models have a GCP?
-
I just went to "My Gallery" and checked out a couple pics of my old bird #877 that I have of the flight deck. I suffer greatly from CRS, but if I'm not mistaken, you will see the Engine Start Buttons located on the panel just above the pilot windshield. I noticed that the windshield wiper is stoped in the verticle position and if you look at the panel just above the wiper that should be the start buttons, nestled inside their protective shields. At least that's what I think I'm looking at!!!!! Keep in mind that that bird is a 1963 model "E" !!!!!!!!
Yep, those are the starter buttons. On the Es you have to hold them in until either the right RPM or the time limit.
-
ya know, now that you mention it, I think i can remember " three's turnin'" or something like that.. Is my memory correct about waitin' maybe five seconds or so for rotation to start.....I do remember callin' that a few times, and we would just start over........I reckon they had to rewind the rubber bands or somethin'
If the prop doesn't turn within five seconds the loadmaster says "negative rotation".
-
ACC herks still carry a chute for each crew member and our vol3 says you can wear either a chute or a harness with certain restrictions based on altitude.
-
I'm sure they're taking a good look at this for the future phases when the Engineer applications become available. But for right now, the rule is no Ipad usage below 10,000 feet.
We rarely get that high on a training sortie so you'd have to keep your pubs nearby anyway.
-
Our T.O. actually tells us to release the prop brake by slightly bumping it.
Is it possible for the prop brake to lock even if the prop never spins backwards? Since it's supposed to be held disengaged by starter torque anyway I just never understood the worry about bumping the prop by hand before starting engines.
-
I call out RPM, fuel flow, ignition, oil pressures, hydraulic pressure, parallel, starter, series, and peak TIT. Some people say more or less than that, it's all technique. You don't have to say anything at all either.
Herk nose gear pin?
in C-130 General
Posted
I have a note in my checklist too, and I reach over to touch the pin before I call it complete. Even after doing this sometimes I hold my breath when the gear lever goes up.