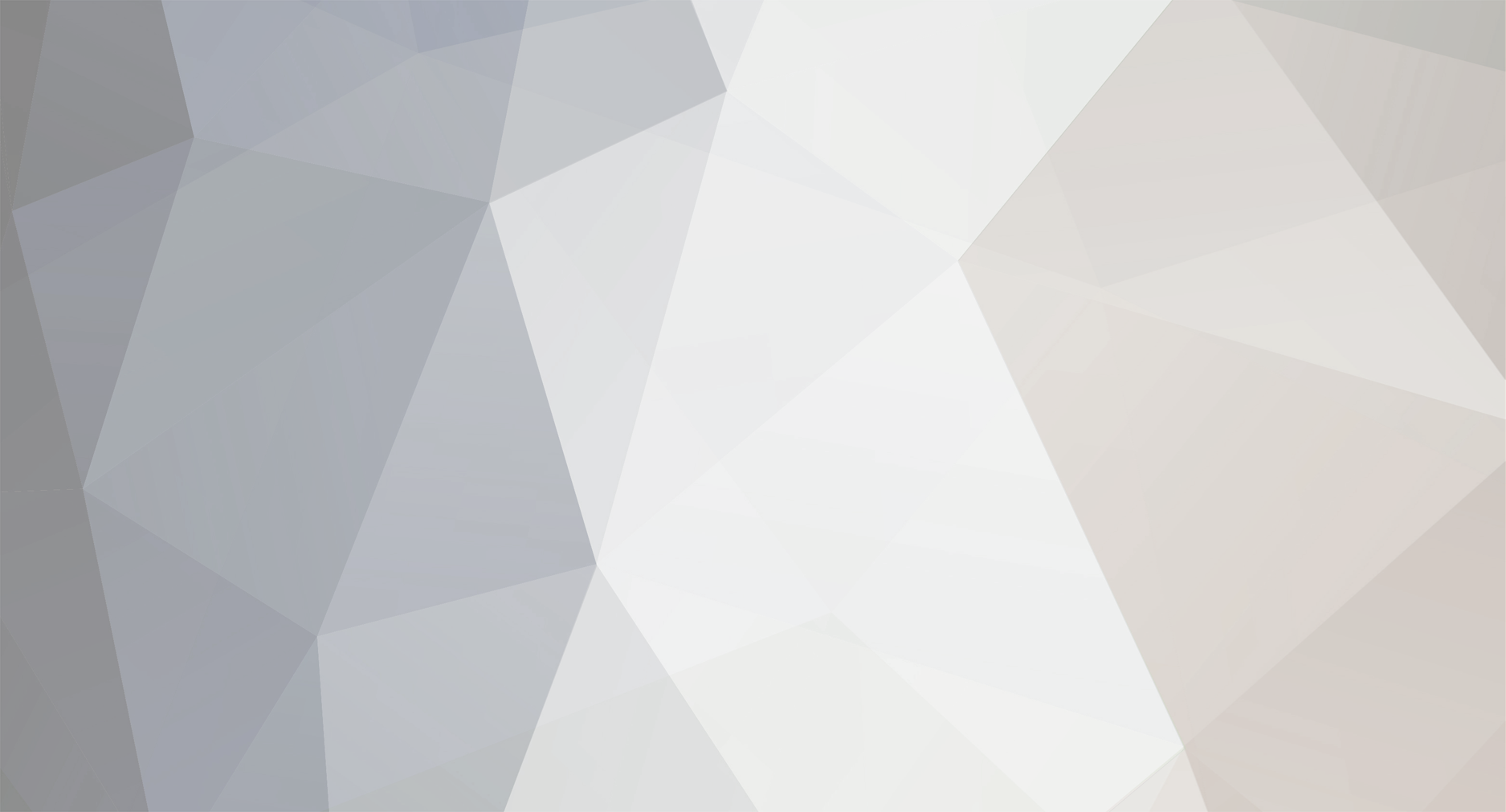
bischoffm
-
Posts
215 -
Joined
-
Last visited
Content Type
Profiles
Forums
Store
Gallery
Downloads
Calendar
C-130 Hercules News
Posts posted by bischoffm
-
-
Dang... I read it... I could have sworn that it didn't say anything about turning a screwdriver, but I stand corrected...
no worries!! I just wanted to correct that point the rest of you pump statement made sense, I've seen no one state that it was wrong, Finding TO's to help the troop is my job, that is why I had the answer to that, here to help.
-
Someone will get rich figuring out how to resurrect the dead (maybe it's a ZOMBIE horse!!)
-
It tells you how to make sure that it fits correctly and not to pry with it but I have not seen anything stating that you have to turn it to make it work other than the little note in there that says that you can use a wrench to turn it if needed. Nothing states that you have to twist the handle with your hands though.
Read paragraph 22.4.2.3 (Using a screwdriver) turn clockwise to screw in and counterclockwise to unscrew (that's rightie, tightie leftie loosy)
Sorry about hijacking this post!!!!:cool:
-
If your engine pump puts out 8.6gpm at 2525psi and you'r elevator bypasses at 3gpm when on the stops. That leaves you with 5.6gpm to play with. Guess what? You'r flaps have a 9.8gpm flow rate limit. That leaves you with -4.2gpm. Not every pump puts out 8.6gpm, the old stratopower pumps were only rated for 5.6gpm. Check SBSS when you get a chance or fedlog to get the characteristics for the different pumps, you will be surprised at how far off from the real limits they make pumps. I'm wanting to say that the Abex pump is rated for 9.2gpm but I am not at work to verify this. Look at the id tag on the pump if you want a quick reference.
Anyhow, a drop to 700psi with one engine on speed while running just the flaps through is nothing to worry about and is quite common.
Not everything is in a T.O. and sometimes it takes a little common sense and system know how to explain things. It's too bad that 99% of the people out there just go off of what a book says and never really looks into how something actually works and why it does what it does. I have yet to see a T.O. that tells you how to turn a screwdriver, yet people twist them instead of pushing on them. Using a little common sense goes a long way, although it may be hard to convince an engineer that the utility reservoir drops about 4" when the gear is retracted and it is perfectly normal. All that fluid fills up the nose landing gear actuator when the gear is retracted. There is no book that says that the fluid can drop. This is one of those cases where you have to be able to understand how stuff works.
I have put in countless TO changes just to have them denied then stolen and submitted by dickbags that want credit for everything.
Some quick and easy things that every hydro guy should know about the 130 as far as pressures
- with both engines downsped pressure can drop as low as 2,550psi
- If a suction boost pump fails you can continue to fly, hydraulic pressure can reach as low as 2500psi with a failed suction boost pump
- A clogged vent filter can cause all kinds of weird pressure problems
Not to be a smart ass, but the T.O. for the use of hand tools to to include screw drivers is AIR FORCE TO 32-1-101 section 22
You have got to remember the Air Force has practically everything!
-
Apples and oranges!!! The gauges are still bad you are just prolonging the inevitable.
Do you think this horse is dead yet!!!
-
This has been a hot topic of discussion for a long time. The J publications only states: "A more accurate fluid level indication can be obtained by allowing SUFFICIENT TIME for as much entrapped air as possible to escape prior to checking fluid level" which is very open to interpretation. I have heard accounts that when an aircraft required both struts serviced on one side, the servicing was performed by a fairly inexperienced crew and as they did not leave enough time for all the air bubbles to escape, when they charged the strut and dropped it off jacks it seemed fine however possibly due to a dry, sticking strut (didn't lubricate chrome part of strut during servicing,) on landing, both struts bottomed out due to excess of gas in the strut and damn near tipped a wing. This probably could have been avoided had the crew tapped the strut with a mallet after servicing.
Agreed, The answer to our younger troops should ALWAYS be follow what the tech order says period, not some old or new ways we found to do things unless it's in the book!!!
-
Applying a vacuum to the strut should remove any air pockets.
That pretty much what the Hydro Mite does!!
-
What about this statement "form a "fillet" of Sealing Compound" , this is no panel. I think it's French for "filling the gap":D
Interpreting Blueprints 230 defines it as this:
fillet- A rounded internal corner. A fillet adds strength to the corner and is often easier to machine.
personally I like the one about two sides of the fish!!:cool:
-
Just because the T.O. doesn't say not beat on the LOX bottle with a hammer doesn't make it the RIGHT way to do it!!
-
The amount of air that may be loosened by this mallet method is not worth the possibility of someone using something other than a dead blow mallet and is just is not worth the aggravation. (worked few other airframes and never heard the strut banging thing) The Hydro Mite is the strut servicing cart the Navy has been using forever and is currently used at USAF C-130 ISO's and is the ALTERNATE PREFERRED method for servicing all strut without even jacking the aircraft. Hopefully we will have one here at Kadena soon (working on that).
-
Where's Tiny Clark when you need him?
Don R.
Im Deutschland!!
-
Thanks bischoffm and others
That's probably the most comprehensive inspection I've seen. I have a similar task card here which outlines much the same inspection requirement for the airframe in the 19600 to 23000 inlb but for 23000+ it's just the same inspection with results forwarded to Lockheed Martin. I note your title reflects this is from the A6, which I'm unfamiliar with but assume it's attached to an older C130 airframe (A model maybe?). I'm looking at the H model, no idea what the airframe structural differences are (as you may have gathered I'm an engines man).
General gist of everything I've read here is that the engine is not going to fail from overtorque. I had wondered where in the drivetrain from turbine to prop it would break - somethings got to give eventually - but I guess that as long as the airframe is expected to start failing somewhere around 23000 inlb and the engine (or torquemeter at least) is good for at least 30,000 then there's no point pursuing it.
The A-6 is used for ALL C-130's except for some specialtiy and the J model they have there own. It covers and is used on the C-130H aircraft.
-
Here is the TCTO that added the lights
INSTALLATION OF ADDITIONAL TAXI LIGHTS,
C-130 AIRCRAFT
TO 1C-130-754
8 October 1974
I don't see where these light would interfer with the MAD they are wired with the postion lights unless someone screw up the routing. Because the TCTO is correct and made no chages addressing the issue that been have stated to have occured.
-
Maybe this will help!
04132 A. AFTER AN ENGINE OVER TORQUE EXCEEDING 19600 BUT NOT MORE THAN 21500
INCH POUNDS, ENTER OVER TORQUE IN QEC, ENGINE, AND AIRFRAME AFTO FORM
95 FOR HISTORICAL PURPOSES. 005
B. WITHIN 25 AIRFRAME HOURS AFTER AN ENGINE OVER TORQUE EXCEEDING 21500
BUT NOT MORE THAN 23000 IN-LBS., INSPECT THE FOLLOWING QEC, NACELLE AND
SUPPORT STRUCTURE FOR CONDITIONS NOTED(SEE TO 1C-130H-2-70FI-00-1-2 FOR
ADDITIONAL REQUIREMENTS.) AFTO FORM 95 ENTRY REQUIRED.
11540 (1) QEC UPPER AND LOWER LONGERONS AND FASTENERS ATTACHING UPPER
LONGERON TO FIREWALL FOR CRACKS (190) AND LOOSE OR MISSING (105)
FASTENERS. 020
11540 (2) PART NO. 362522 QEC BEAM FOR CRACKS (190). 015
11540 (3) QEC DIAGONAL BRACE FOR CRACKS (190). 010
11540 (4) DISCONNECT FITTINGS IN AFT END OF QEC FOR CRACKS (190), ALIGNMENT (127),
AND SECURITY (730). 010
11540 (5) TRUSS MOUNT LONGERONS, DIAGONALS AND SWAY BRACE AND ATTACHMENT TO
FRONT BEAM FOR CRACKS (190) AND LOOSE OR MISSING (105) FASTENERS. 030
0411B (6) PERFORM NDI OF THE UPPER TRUSS MOUNT VERTICAL LEGS (1154Z) AND TANGS
(1154Y) IAW TO 1C-130A-36, N-11. (APPLICABLE TO OVER TORQUES ON #1 AND #4
ENGINES ONLY). REMOVAL OF ENGINE IS NOT REQUIRED. 030
0411B (7) PERFORM NDI OF WING LOWER SURFACE PANELS (UNDER NACELLE FAIRING
ATTACH ANGLES) AND ENGINE DRAG FITTINGS (11540) IAW TO 1C-130A-36, CW-23 OR
OW-47 AS APPLICABLE. 015
11540 (8) VISUALLY INSPECT NACELLE FAIRING ATTACH ANGLES FOR LOOSE OR MISSING (105)
FASTENERS. REF TO 1C-130A-36, CW-23 OR OW-47. 005
11540 (9) NACELLE SKINS AND FAIRING FOR BUCKLES (780) AND LOOSE OR MISSING (105)
FASTENERS. 045
11550
11580(10) PERFORM A THOROUGH VISUAL INSPECTION OF THE IR HEAT SHIELD LOWER TUB
AND UPPER TRACK ASSEMBLIES FOR EVIDENCE OF BUCKLES (780) AND LOOSE OR
MISSING (105) FASTENERS. 045
C. ENGINE OVER TORQUE EXCEEDING 23000 IN-LBS. (FOR AIRCRAFT AT LOCATIONS
WHERE NDI CAPABILITY DOES NOT EXIST, THE NDI REQUIREMENTS WILL BE
ACCOMPLISHED AT THE FIRST FACILITY WITH NDI CAPABILITY, NOT TO EXCEED 25
AIRFRAME HOURS) SEE TO 1C-130H-2-70FI-00-1-2 FOR ADDITIONAL REQUIREMENTS.
AFTO FORM 95 ENTRY REQUIRED.
(1) ACCOMPLISH ALL ITEMS LISTED UNDER PARAGRAPH 4.B. ABOVE.
(2) NDI THE FOLLOWING STRUCTURE FOR THE CONDITIONS NOTED. THE POWER PLANT
MAY REMAIN INSTALLED.
0411B (a) PERFORM NDI OF ENGINE TRUSS MOUNT SWAY BRACE ATTACH LUGS (1154Y) IAW TO
1C-130A-36, N-9. 015
0411B (
PERFORM NDI OF FORWARD OR FORWARD UPPER (AS APPLICABLE) BOLT HOLES OF
ENGINE TRUSS MOUNT UPPER TANGS (1154Y) IAW TO 1C-130A-36, N-10, SCANS 13 OR
15 AND 8 OR 18 AS APPLICABLE. NDI BOLTS BY MAGNETIC PARTICLE TEST BEFORE
REINSTALLATION. 015
(3) WITH THE ENGINE IN A NO-LOAD CONDITION, CHECK THE FOLLOWING BOLTS FOR
MINIMUM TORQUE IN THE TIGHTENING DIRECTION. IF BELOW MINIMUM TORQUE,
REMOVE AND REPLACE WITH NEW BOLTS OR REMOVE, NDI AND REPLACE THE
FOLLOWING BOLTS:
1154P (a) UPPER QEC AFT ATTACHING BOLTS, 3700 IN-LBS (FOR AIRCRAFT WITH TCTO 1C-130-
1340 COMPLIED WITH MINIMUM TORQUE FOR #2 & #3 UPPER ATTACH BOLTS IS 4800
IN-LBS). 005
1154Q (
LOWER QEC AFT ATTACHING BOLTS, 2300 IN-LBS. 005
1154M (4) WITH THE ENGINE IN A NO-LOAD CONDITION (REF TO 1C-130H-2-71JG-00-2, 71-20-10),
CHECK MINIMUM TORQUE ON THE FRONT ENGINE MOUNTS (LORD MOUNT)
ATTACHING BOLTS. IF THE TORQUE IS LESS THAN 400 IN-LBS IN THE TIGHTENING
DIRECTION, REMOVE AND REPLACE FRONT ENGINE MOUNTS (LORD MOUNTS). TAG
FOR OVERHAUL IAW TO 2RA3-2-3: 060
1154M (5) IF THE RUBBER OF THE FRONT ENGINE MOUNT HAS FLEX CRACKS WHICH HAVE
PROGRESSED INWARDLY TO A DEPTH OF ¼ INCH. REMOVE AND REPLACE FRONT
ENGINE MOUNTS (LORD MOUNTS). TAG FOR OVERHAUL IAW TO 2RA3-2-3:
-
USAF uses the 1C-130A-6 for it's inspection criteria (for the -15 engines)
-
Do you mean nacelle interface unit??
-
Did not C-130A 5500022 (Lone Wolf) retire with a still active formard cargo door?
-
Because someone was messing around with the forms (some crew chief humor!!)
-
These tanks were mixed alot we got rid of the Lockheed tanks (solid) 388236-1 and sent them to the bone yard for ease of maintenance and installed100001-300. As you can see the tank T.O. 6J14-2-12-93 does say not to mix them; however, the 1C-130H-4-28-1 makes no distinction. This could be a good AFTO 22 for someone!!
-
They are the same part number tanks!
-
if you follow the 16W14-12-3, it means you don't have to have any on the lower edge to call the panel secure. I think that protection from the wind on the ground not air flow!! There is still NO book telling it's OK or NOT OK to fly with any fasteners missing! Like it has been said common sense rules for those who have any!
-
You have changed the ATM right??
-
Lots of times that is the best place for some ocifers!!:cool:
-
They are doing or a TCTO so maintenance can add a digital pressure gauge to adjust the regulator within those T.O. limits. Some AC may not be done yet!
pump issue: abex vs. parker
in C-130 Technical
Posted