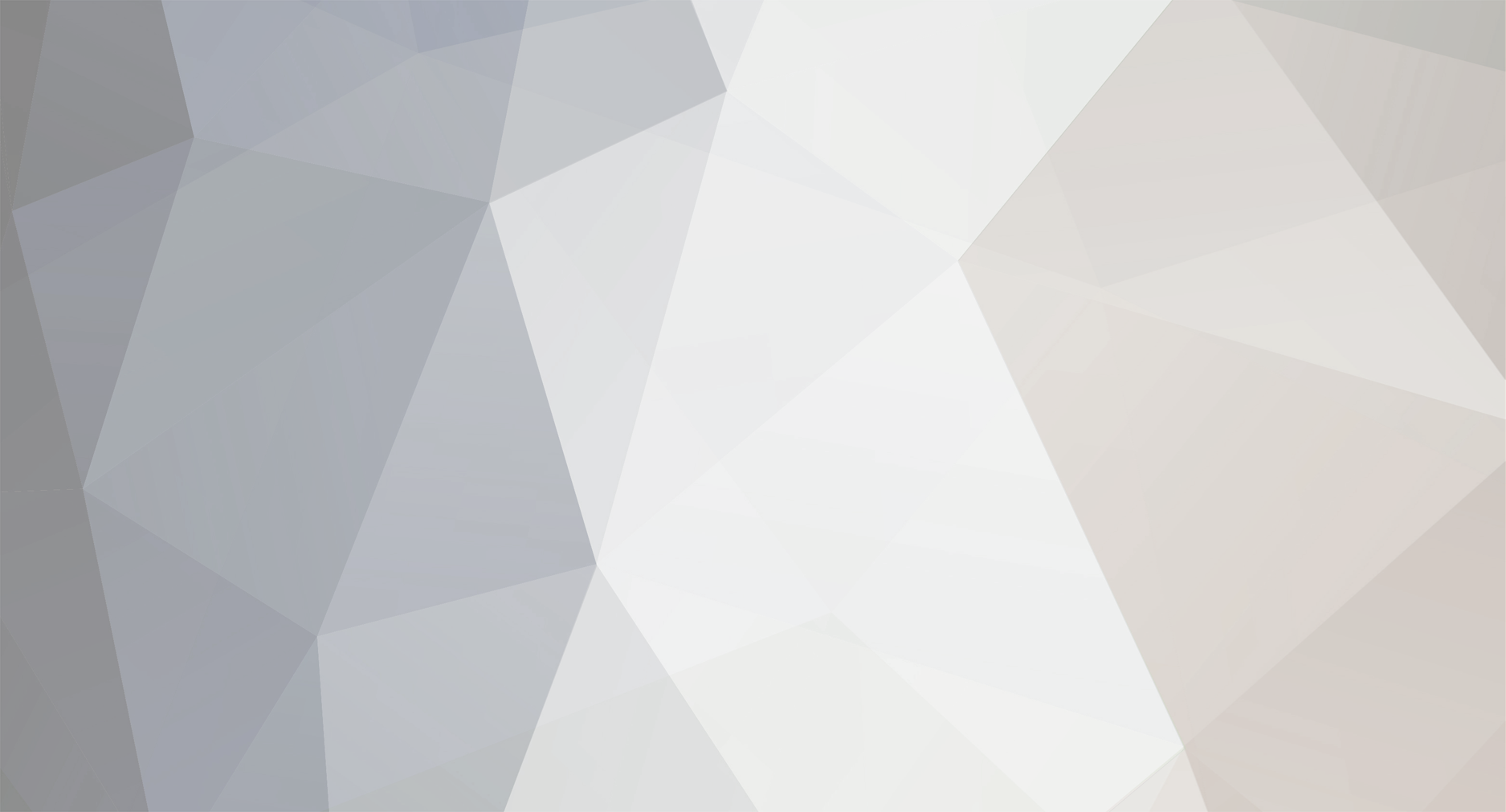
tinyclark
-
Posts
1,109 -
Joined
-
Last visited
-
Days Won
13
Content Type
Profiles
Forums
Store
Gallery
Downloads
Calendar
C-130 Hercules News
Posts posted by tinyclark
-
-
I have no damn idea, never worked on a J-model. I am assuming you'd have to switch to that display.
-
Where are you getting the numbers from? They should all be in the wiring diagram. What book are you using?
-
Don't know, unless it's bend to fit or per sample.
There are many tubes in this series and others that have bends and no dial settings.
-
I think they just used a switch from another application that happened to be moisture resistant. There is no reason to have anything like that in the overhead panel, and not have everything else set up the same way.
-
2-1.6 Gen 1-4 and APU ACAWS Indications. (Figure 2-4). When the GCU detects an out of tolerance condition, and a generator switch or EXT PWR/OFF/APU switch is in ON or APU, it will open the line contactor and send a system status indication to the bus interface unit BIU. The
BIU will then generate a data word to the mission computer that a failure has occurred in one of the engine generators or the APU generator. An advisory, caution, and warning system (ACAWS) text message (GEN 1,2,3, or 4 FAIL or APU GEN FAIL) will then be displayed for the first ten
seconds in reverse color (black letters on a night vision imaging system (NVIS) yellow background) followed by flashing master caution lights.
System Status Electrical Display. (Figure 2-2). The SYSTEM STATUS ELECTRICAL
display, on the head down displays (HDD), displays generator voltage and percentage of rated current load. Values for generator voltage and load are displayed in columns, labeled from left to right, representing generators 1, 2, 3, 4 and the APU generator. Three voltages are shown in the
column for each generator to indicate the voltage of each of the three phases of the generator: A phase, B phase, C phase. Percent of maximum rated load for all five generators (an average of the three phases) is displayed in the row below the C phase voltage. Information will be presented in
white when in the normal operating range, yellow for information out of the normal range but not out of limits, and red for out of limit values. If the system is not powered, OFF will be displayed in the appropriate data blocks. If the system is disconnected, three dashed lines will be displayed. The
display symbols are generated by the multifunction display units based on information received from the mission computer.
-
These are from the B-1.
-
What's this switch for?
-
We always built our own, but I have seen them. One of the items that will be hard to find are the HN style for the TACAN.
or...
http://compare.ebay.com/like/390414958437?_lwgsi=y<yp=AllFixedPriceItemTypes&var=sbar
http://store03.prostores.com/servlet/henryradio/the-691/High-Quality-30-Piece/Detail
http://www.elexp.com/con_rfad.htm
I thought I had saved a table of adapters, but I can't find it. Most were found in the King RF connector book I had.
-
The worst thing they did when they replaced the HF-102 system with the ARC-190 was to install dual systems. The complexity of the antenna interlock system overcomes the great reliability of the new HF, causing more problems and headaches to maintainers. The guys that have the newer rear stabilizer antenna don't have this headache, even though the radios share the same antenna.
-
Give me an email address in a private message.
-
Here's how the wheels on my brew work.
-
I have no idea what radios you have installed on your aircraft. Do you still have the 618T, the ARC-190, or something else installed? The interlock wiring system on these is ridiculous. Please let me know. I drew up a troubleshooting diagram for the ARC190. I can send it to you.
-
They are removed and checked during every ISO inspection IAW 2J-T56-56.
-
No management data is shown in WEBFLIS for any of the Services.
-
Bobby,
You could probably fix that with a patch, The actual name of the part is a pressure box, p/n 408323-01. A replacement would have to come from a retired aircraft in AMARG. They are a real bitch to get out, as i helped on one. The problem comes when you remove that tub, a complete DVS alignment would have to be redone.
I cannot get to drawings anymore to check the specs of the box, but I believe it is some type of resin construction. Maybe Mike Bishoff, if he's on one of these days, can tell you. If the crack is small, I would suggest stopdrilling it, then a small patch placed on top, but, I'm not an engineer.
-
I wish I could, but I don't have any connections at WRALC, as I am retired, and I never worked on J-models. I would contact the manufacturer of the LRU. You can try Lockheed, but I doubt they'll want to let you know. Have you switched it to partial to see if the display changes? I would have.
-
Not sure what you are referring to, on what model aircraft, or where this is selected. The is only one RADAR frequency.
Can you be a bit more specific?
-
Is this doppler the APN-218 system? Repairs to he radome skin are very limited. This if from the shop manual.
6-10.1 Radome Repair. Major radome damage requires antenna boresight correction constants be verified
once repair has been accomplished. Antenna boresighting is a depot repair function. Scratches, etc. to the
radome not exceeding 0.004 inches in depth and 3 inches in length need not be repaired. Intermediate level
maintenance is limited to repair of minor abrasions and scratches in accordance with paragraph 6-10.2 and
removal of oil and similar contaminants in accordance with paragraph 6-5. l.b. Minor radome abrasions and I
scratches are defined as follows:
a. Damaging agent has not deformed the radome surface.
b. Damaged area is free of all fragments of any type metal.
c. Abrasions or scratches do not exceeds a depth of 0.010 inches and an area of 0.06 square inches for the
APN-230 or do not exceed the dimensions shown in figure 6-1.
NOTE
Limit repair to only the damaged area of the radome and only a one time
repair of that specific area.
6-10.2 Repair of Minor Pits. Abrasions and Scratches. Make minor radome surface repairs as follows:
a. Clean radome in accordance with paragraph 6-5.
b. Wipe area to be repaired with a clean lint-free cloth dampened with Axerel 2200 or equivalent. I
c. While area is still wet, rub briskly with a dry, clean lint-free cloth, turning cloth frequently.
d. Wipe with a clean, lint-free cloth liberally dampened with P-D-680, Type III or equivalent. I
e. Rub dry with a dry, clean, lint-free cloth, turning cloth frequently.
f. Lightly abrade area with a fiberglass brush or 320 to 400 grit sandpaper and dust abraded area with
a clean, dry bristle brush.
g. Fill nicks, scratches or abrasions as required using polyester resin with 1/2 to 1% MEK peroxide as
the curing agent.
h. Using 320 to 400 grit sandpaper, sand the cured polyester resin to restore the original contour.
Repeat step d to remove sanding residues, and allow the surface to air dry for at least 30 minutes
before applying primer.
i. Apply primer coat (SCDPE0028-1); limiting thickness to existing primer coat and cure at room
temperature for one and one-half hours minimum. I j. Apply finish or urethane coating (MIL-C-83286) Color No. 26081 or 36081 (APN-218) or Color
Number 16081, 16118 or 36081 (APN-230), limiting thickness to existing outer coat and cure at room
temperature a minimum of 24 hours
-
The ETCAS, GCAS/GPWS & Digital Autopilot are fed by the Analog altitude signal. The indicators get the Aux Analog and Digital Altitude signals. If there are no GCAS or ETCAS problems, I would check the Aux and Digital lines to ground. Maybe one of the lines is shorting to the shield. These wires are also spliced. Whether it will cause an R/T fail indication on the indicator, I have no idea.
-
It would be easy enough to put an ammeter across the battery and see if there is any current flowing. Easiest way would be to pull the ground off and hook the ammeter up there.
-
Hope this is good enough
-
Sorry, it's 53-199-00. I can't figure out how I did that except for old age...
-
Fitting part # 371603-1
C-130A-3
1. General.
Depot Level Repairs are those repairs that may require a higher degree of skill and/or specialized
equipment or facilities which are not normally available at the organizational level of maintenance. Prior
to performing any of these repairs at the organizational level, authorization and possible assistance is
required from WR-ALC Engineering. Refer to Table 1 for a listing of Structural Repair Kits.
1C-130A-3, 59-199-00, page 6, D.1.
Replacement of Part No. 371603-1L and -1R Floor Bulkhead End Fitting at Fuselage Station 597
and Installation of Vertical Beam Splice Part No. 7843161 at Fuselage Station 597. Applicable to
73 models and prior. Part No. 7843161-01 for left side. Part No. 7843161-02 for right side.
-
Sorry, I am not familiar with the FMS system at all. Have you tried to do multiple alignments to reduce the error? Can you swap out INUs, #1 with #2, or with another aircraft?
FBW
in C-130 Technical
Posted
The autopilot is fly by wire.