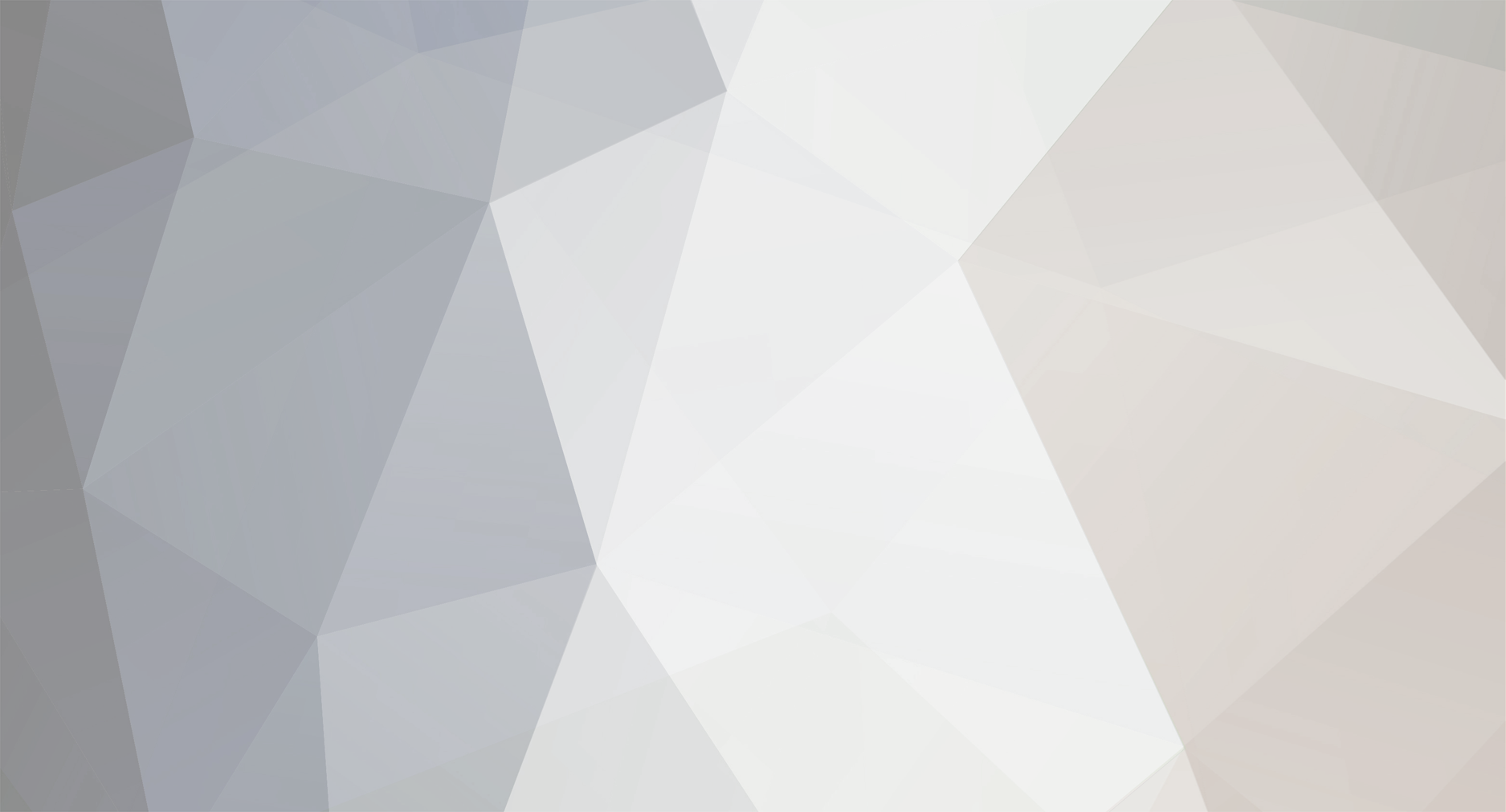
hehe
Members-
Posts
250 -
Joined
-
Last visited
-
Days Won
8
hehe last won the day on July 13 2021
hehe had the most liked content!
Personal Information
-
About Me
_
-
core_pfield_2
_
-
Website
_
-
core_pfield_4
_
-
core_pfield_8
_
-
core_pfield_9
_
-
core_pfield_10
_
core_pfieldgroups_2
-
First Name
_
-
Last Name
_
-
Gender
Not Telling
-
Location
_
core_pfieldgroups_3
-
core_pfield_11
C-130 Hydraulics
LITTLE ROCK AFB 2007-2012 C-130E/H/J
Moody AFB 2012-current HC-130P/J -
core_pfield_12
_
-
Occupation
_
Recent Profile Visitors
The recent visitors block is disabled and is not being shown to other users.
hehe's Achievements
-
All pre-ordered books have shipped. Copies are available here if any is interested. https://82innovations.com/c-130-tail-number-book Paypal check out is available on the website. 82 Innovations
-
Bringing back the Lars Olaussen C-130 Production Books. The "green book". Bringing the C-130 fleet book up to 2024 accuracy in honor of the decades of work Lars and others put into documenting the C-130 fleet. If you have information on your favorite aircraft, please reach out. I would love to have accurate data to make sure I'm getting this right. 30 books pre-ordered so far. Shipping in January of 2025. If you are interested, visit the site to pre-order yours or email. https://82innovations.com/c-130-production-book 82innovations@gmail.com
-
Looks like the Lars Olausson "green book" is coming back in January 2025. Final edits are with a print shop now to bring the book up to 2024 standard. If you would like a copy, check it out here: https://82innovations.com/c-130-production-book
-
Fuselage station. There were versions of the C-130 that went well past the nose radome. MC-130H had a longer nose radome, HC-130H and MC-130E had yokes that extended way forward of the nose, other models such as AC-130 had a massive pitot that extended well past the nose radome. If there is a pitot probe attached to the nose of a plane during design or initial testing, it defines where the fuselage station starts. They wouldnt use negative fuselage stations if they already know there will be a reference point that far forward. Most forward point defines 0 and it gives room for modification of extension of the nose.
-
It keeps the aux pump from cavitating at high altitude. Used to have issues with not being able to open the ramp and door at high altitude because the aux pump would cavitate. High altitude ramp and door mod was to fix that issue. It mostly did
-
I've always 100% disconnected scissors when towing as well. There is zero gain by towing with them connected. You might be hunting a self induced problem by towing with scissors connected. If you really want to go down the rabbit hole though, I would 100% ensure your strut is serviced properly (meets and exceeds minimum X dimensions) and you can pull the flow reducers out of the steering actuators to ensure they are in good shape. There are plugs on the aft side of the steering actuators, under that plug there is a flow reducer with a spring. That limits how fast the actuators can move fluid through them. The steering control valve doesn't do much when it's not being powered, the reduction in flow really resides in the actuator end caps. You could also check the bearings on the forward steering actuator trunnions, those bearings are finicky and bind up quite often if not properly maintained and lubricated often. Again, you are probably chasing a problem that is self induced though, no need to tow with scissors connected, it's all risk with no reward. Chris
-
Why would you ever tow with it connected? I've never heard of any manuals that state to tow with it connected
-
When you tow, you have to disconnect the NLG scissor. The top and bottom are not linked. Are you towing with the scissors connected? You should never have any reason to even talk bout the steering control valve because it's not in play when the upper scissor is disconnected from the lower scissor. Im very confident when I say you might be towing incorrectly,
-
I would suspect a MLG motor or utility relief valve to create that low of a pressure drop on both engines when isolated. Assuming you are isolating everything correctly, but do this: 1. Turn off all 3 boost packs (red guarded shutoffs). Is pressure the same? If it changes, isolate boost pack 1 at a time. 2. Run the system up and let it run for a good 15 minutes. Does the utility relief valve get hot? Can you hear it bypassing? Possible that it is dumping your pressure back to return 3. Remove the hydraulic lines and cap the outlet ports from the landing gear selector valve. Run the system up, does it still have the low pressure?
-
This is just a marking for the ring segment at fuselage station 165. The fuselage is essentially just a bunch of beefed up rings connected together.
-
It's not a bad idea to do it and hydromite is by far the best strut servicing tool available. As far as hydromite, If you aren't using hydromite or aware of how to use it, you are shorting yourself. If someone told me to go leak check a strut, service a strut, R2 a strut, deflate a strut, etc, etc. I'm asking for a hydromite. Hydromite is awesome for fixing strut leaks and servicing. Take the time to learn about it.
-
The struts are a time change item so you don't change the fluid out, the entire strut gets replaced. Short of moisture in the hydraulic fluid and it not meeting the water content limits, the fluid doesn't really break down in struts like it does in the system. Sometimes you can drain a reservoir and the fluid is visibly darker or dirty looking. Struts, in my experience, don't really have this same problem because there aren't moving parts in the strut short of o-rings. The fluid doesnt really come in contact with wear items like an engine pump or motor produces for example. This is just my opinion since I've drained a lot of struts and never really came across one with dirty fluid.
-
Elevator boost pack is what bleeds down pressure in both systems. If you pressurize booster and utility, and shut off the elevator boost pack shutoff valves, the systems will hold pressure after shutting down engines. Not forever but noticeably longer than without the elevator boost packs shutoff. If you also hold the elevators neutral, the pressure will not deplete. If the elevators are on the stops (yoke forward) the 3.8 GPM bypass will quickly deplete pressure Long story short, I would look at the elevator boost pack in relation to booster side. Bypass not bypassing when elevator is forward on the stops, elevator booster shutoff valve partially closed, booster return filters clogged
-
Not sure what you are doing to troubleshoot this but it's pretty easy to start. 1. Start diagnosing the tripped open ECB IAW 24FI for tripped ECB. 2. Swap/R2 APU relays and check all power connections. I would caution resetting the ECB multiple times until you figure out what is causing it to trip.
-
If the handle locks up at 40% it is almost always because someone pulled the UP lock lever while lowering flaps. The lock and flap lever interfere with each other in this state and lock the handle up. What model of C-130 was this?