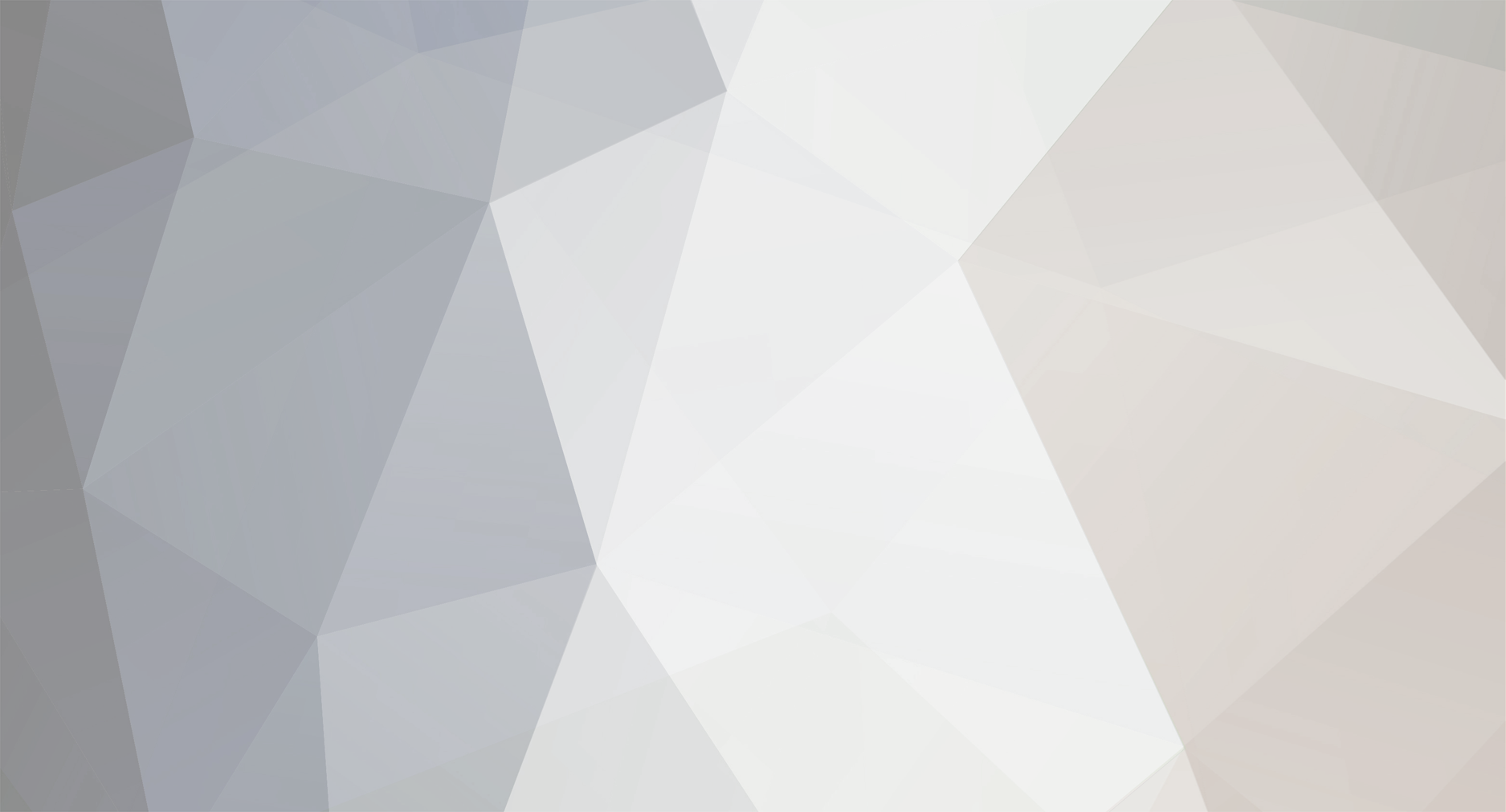
tenten
Members-
Posts
195 -
Joined
-
Last visited
-
Days Won
1
Content Type
Profiles
Forums
Store
Gallery
Downloads
Calendar
C-130 Hercules News
Everything posted by tenten
-
Thanks to all, it is indeed what I am looking for, appreciate the details brother Heimie.
-
Currently, I am also having “one†reported pulling towards left during taxing; and during the landing roll when shifting throttle from F/I to G/I left wing sharply tends to go down. (Engine torque indicated equal in all positions). Left legs found weak re-serviced with hyd and nitrogen, the lifting of wing solved but the pulling to left during taxi remained reported by captains, Rigging and adjustment on the steering c/out, nose tires changed, all wheels re-torqued, steering control valve changed…etc; No improvement in stopping the write-up . The last action was the change of steering actuators accompanied with a cup of coffee to the pilot in charged to perform the taxi check during his waiting to prepare airplane for taxi check. This time I was with them during the taxi-check; there was no pulling tension when pilot hold the steering on the white mark but when leaving the steering free the airplane moving slowly toward left, this act repeated upwind and downwind, with inboard engines alone or outboard alone, with low or normal RPM, finally captain looked at me, asking me to comment; I told him I never been on left seat to evaluate, but is it recommended to leave the steering wheel free? I added, was the coffee offered to you not enough to keep hand in touch with the steering. Defect cleared by the captain. What solved the defect, Coffee or actuators?? No idea.
-
How the RPM can be increased/decreased in (G/I, Top of Beta) and on (F/I with low pitch stop engaged)? Which adjustment will do the task without much upsetting the torque? Is it blade angle adjustment? Is it null orifice adjustment, is it fuel control linkage adjustment, is it throttle rigging adjustment? And is there any adjustment in the FCU to correct the case? Is repositioning the low pitch stop will affect the RPM in F/I position? Some time I need only 1% RPM adjustment to be a way from minimum limit to avoid flying crew write-up. Need your help/experience on that.
-
Might be due to better stability of inboard engines to wing oscillation/vibration than outboard engines.
-
FM 382C-14E Section 7 page 12. Yes brother, AMPTestFE This function is equipped on C-130H airplane configuration codes (382C-14E) and (382C-45E) Lockheed Serial No. 4879, 4882, 4983 and 4985. (Foreign direct sales Lockheed).
-
Yes brother AMPTestFE, This function is equipped on C-130H airplane configuration codes (382C-14E) and (382C-45E) Lockheed Serial No. 4879, 4882, 4983 and 4985. (Foreign direct sales Lockheed).
-
The main idea behind putting the control switch on the SPR panel (on some models) is to provide the ability for the operators with the APU gen alone (40KVA) to use the dump pumps during the defueling process ( As you know all fuel dump pumps powered by main ac bus).
-
No idea about E models, our airplanes (H) having this function for ground operation only through fuel ground transfer switch on the SPR panel in which the APU gen. can also be connected to take the main Ac Bus through (K11). Other civil registered (L100) which I have flown having the control switch (AC BUS TIE) on the over head control panel but also limited for ground use only when all engine generators are off the line.
-
Tiny, You know that engine generators output to feed the buses is going through a chain of 8 contactors, and the route to feed the Ess Ac Bus from any engine driven is requiring to go through two contactors only (K6 and K7), those two must be energizes if one failed you lose a 50% of your credit, if the two failed a lot of things will wake you up a side of “ESS AC BUS OFF†red light. Have a look to this actual “scenario†in which I was lucky to lose only the 50% of my credit. (The culprit was K6 contactor, found burned). On a short mission, on the way back to home station; Indication at the time of malfunction started with momentarily flickering of some engine instruments and heading indicators, generator no 2 checked nothing found abnormal, no 2 generator switched off to isolate the defect, load transferred as normal to No.1 gen; but after some time the momentarily flickering hit again. No 2 gen returned to line and took over the load (I assumed not guilty and to avoid the high load on No 1 gen). The last hit was a combined with disengaging of auto pilot and with some flx of engine RPM; We started switching off some “subsystems†in preparing our self to go through “Lose of Ess Ac Bus Proceduresâ€. I was lucky during the last hit; I noticed that the load of Ess.AC was transferred from No 2 gen to No 3 gen and remained on No3 gen. Why not to No1 gen??! Is it a “contactors†issue?! At the moment the answer comes from the LM telling us that burning smell on the cargo comp…… APU started and APU gen was put on line, load of Ess Ac Bus was taken by APU. Within the last 40 minutes to landing, defect never repeated burning smell gradually disappeared. Two points on the issue; Bus contactors can malfunction, and using the APU generator will bypass the standard engine driven routing (K6 & K7) to a single route (K10).
-
Hi Tiny, Losing the Ess Ac Bus during flight/ground can happened due to some malfunctions not necessarily due to generator failure. Malfunction such as: 1- High load on the Ess Ac Bus caused by malfunction of component or wiring. 2- Bus Contactors failure. May cause the Ess Ac Bus to be lost, in which no other generator can assume and takeover the Bus load. Another possibility of losing the Bus in-flight is when flying crew are forced to isolate the Ess Bus due to electrical fire on a component or wiring belongs to the Bus.
-
1- Losing the Essential AC Bus only will not put the battery under any load; Battery will remain charged by the main AC bus through the two main TR units. 2- Why to land as soon as possible? Well; check how many essential components using the effected bus then decide yourself if you want to continue or to land. I will give some of the lost: a- Heading indications (C12 compass, INS heading) b- No.2 fuel boost pump. c- Both hyd. Suction boost pumps. d- All trim tabs (the elevator trim will be shifted to emergency) e- Both secondary ac buses (two invertors will be used to recover the power) =heavy load on generator. f- Weather Radar, IFF/ATC, Auto-Pilot, INS, Radio Altimeter, Some of navigation/communication equipments. g- ………….I think… enough to land as soon as possible. 3- How long the Battery will sustain if it is the only source of power? Depends on the load; but I think it will not sustained more than approximately 20 minutes.
-
I don’t know what you mean by the last statement; Do you mean that you haven’t got the authority during flight to shift the prop to mechanical gov because you don’t have any other indications beside the torque flux? Or do you mean is it possible that the defect is related to a tachometer generator failure...? Look my brother; one of the “Golden Advice” that I have it from my IFE and it works many many times in isolating the defect is: When you “get puzzled” of abnormal -power related- indications (Torque, Fuel, TIT, or RPM) “Free Your Effected Engine from any assistant/supporter” (synchrophaser system, TD system, Bleed air regulating system). One by one and check the behaviour. Bearing in mind that; When removing assistant of any of the above you should be familiar of the normal reaction of each. Which one you start isolating first…?... Not a big issue, any… If not improving return it back. Concerning your defect; if what you have is only fluctuating of torque indicator without any abnormality of other indications. I advice to go first for torque meter indication system malfunction.
-
Since you did not mentioned any other indications beside the fluctuation of torque or any corrective actions taken; I have to ask. Is there any beating noise during the flux? Is there any flux on the frequency meter (more sensitive than RPM indicator)? I never had an “actual†torque fluctuating more than 600 in/lb without the above. If having any of the above; as brothers advised isolate the defect “first†(before you go farther) by: TD null, mechanical governing, and bleed off. If defect not a combined by the above, check your torque meter pick-up and indication system wiring, since you already swapped the indicator.
-
"Power off" stalling speed by definition is: The minimum speed at which the aircraft is controllable with deceleration not greater than one knot per second and with flight idle thrust at the stalling speed. This type of stall normally encounters during descending or approach to landing. While "Power on" stalling speed; Is the minimum speed at which the aircraft is controllable… while thrust power at maximum at the stalling speed. This type of stall normally encounters during take-off, climb, or go-around when higher than normal pitch-up is used. The “recovery procedures” to regain aircraft control slightly differ for each of the two types of stall.
-
Maybe you are looking for this.
-
It is 10 cubic inches of fluid. (ref. FM 382C-14E) Memory Refreshing: “The Fuse Control Head†divides the fluid flow into two flow bath, the main flow and the metered flow; the “two†flow create a balance pressure thus the main piston remained centred, once a line ruptures downstream of the fuse, the “flow†will increase (10 cu in) through the metered orifice(pressure will drop) causing the main piston to move and block the main flow. Once closed will remained closed until the inlet pressure is reduced to 5 psi, in which a spring will react and bring the main piston to its static position.
-
You are right Lkuest. "Geneva loc" is the name of the manufacturer. Simply, the Fuel control shutoff valve "actuated by electric motor" allows the fuel during start to be introduced to the engine burning section at a specified rpm, and due to the design it provides “cut-off†to the fuel electrically (and mechanically if required by condition lever feather position) when engine is to be shut-down.
-
Well, trev The answer you are looking for is not that simple without more information; such as: 1- The distance from brake release point to the obstacle (mountain). To get three/four engine climb-out flight bath. 2- The pressure altitude-at the time of the mission-not the field elevation. 3- The minimum specified/accepted rate of climb after take-off with three engines.(normally specified by the operators) this will give you the take-off gross weight limited by three engine climb performance 4- Drag index. 5- The ability to perform “spiral†climb is another factor to the whole subject. You should check your SMP777 to get the accurate answer of “AUWâ€. In my book it is in (figure 3-10) take-off gross weight limited by three engine climb performance. And (figure 3-17) climb-out flight bath three/four engine. But to give you an idea based on the information given by you: 1- Take-off factor 2.5 2- Temp deviation +25⁰C 3- Pressure altitude 7,230 ft. (estimated standard) 4- 500 ft (estimated minimum accepted rate of climb after take-off with three engines) Based on the above your take-off gross weight limited by three engine climb performance should not exceed 135,000 lb. (plan for the worse and hope for the best) The distance from brake release point to the “obstacle†is essential requirement to get the climb-out flight bath three/four engine, (if unable to do “spiral†climb or to turn to avoid the obstacles.)
-
“Low pressure†is a “warning†to the operators that the engine is under low pressure supply and need to be corrected-if engine is running- (the pressure switch is up stream of engine driven fuel pumps). And it can be due to: main tank pump failure, leakage/break on the engine fuel supply line, fuel tank contamination in addition to what brothers already mentioned. While the "tank empty" light (the pressure switch is on the lines leading to the cross-feed manifold) which mostly indicates that the tank (Aux or Ext) is empty, beside other possibilities of malfunctions, (but doesn’t indicate imminent hazard to the engines)
-
Maybe related to the ramp & door actuator cylinders (bigger volume capacity).
-
High flights.. How high have you flown in a Herk?
tenten replied to M_Wales's topic in C-130 General
Brother AMPTestFE; The shame & hiding is to leave the “front†to the inexperienced guys home only chewing and mummeries shallow information with nil experience. And guess who is at the top of the list? ….√ -
High flights.. How high have you flown in a Herk?
tenten replied to M_Wales's topic in C-130 General
Since, there are different procedures from book to book and time to time. Let me admit that my previous statements was not accurate, and need to be corrected by adding (in bold) the following to my previous statement. Therefore; the two pictures was definitely not related to each other; the top picture might show what altitude brother “M_Wales†was flying during his mission from xxx to xxx, but the lower picture showing an airplane flying on an altitude not above 21,000 feet, unless the crew were not following the normal operating procedures stated on the last updating books.†BEFORE TAKE-OFF. (Automatic Pressure Control) 1- …. 2- Set the cabin altitude knob to the desired cabin altitude, but never less than field pressure altitude. AFTER TAKE-OFF. NOTE: Monitor cabin altitude against airplane altitude to make sure that cabin altitude stays within the isobaric range. (See figure1-50.) BEFORE TAKE-OFF. (Manual Pressure Control) 1- Set cabin altitude selector to 10,000 feet and position air conditioning master switch to MAN RESS. REF. TO 1C-130H-1 (Original Issue) Section/Pages (1-153.154) -
High flights.. How high have you flown in a Herk?
tenten replied to M_Wales's topic in C-130 General
NATOPS1, You are correct, it can be in AUTO, but is it normal procedures to do so and to let the back-up system to correct your mistake of been not following procedures on setting the pressure controller? And what you achieve by doing so?! -
High flights.. How high have you flown in a Herk?
tenten replied to M_Wales's topic in C-130 General
I got your point, so you believe that crew might be operating in MANUAL mode. In this case the flight engineer seems to be not following the correct procedures during manual operation; in which the cabin altitude selector should be set to 10,000 feet according to procedures, but not to leave the cabin altitude selector close to 1,000 feet. Yes, I believe brother “M_Wales†that he hit the 31k because he said so, but I don’t believe that the second pic was taken of an airplane above 21K with AUTO mode of operation. -
High flights.. How high have you flown in a Herk?
tenten replied to M_Wales's topic in C-130 General
That is why we have asked the question what was the cabin altitude during the mission? Therefore; the two pictures was definitely not related to each other; the top picture might show what altitude brother “M_Wales†was flying during his mission from xxx to xxx, but the lower picture showing an airplane flying on an altitude not above 21,000 feet.