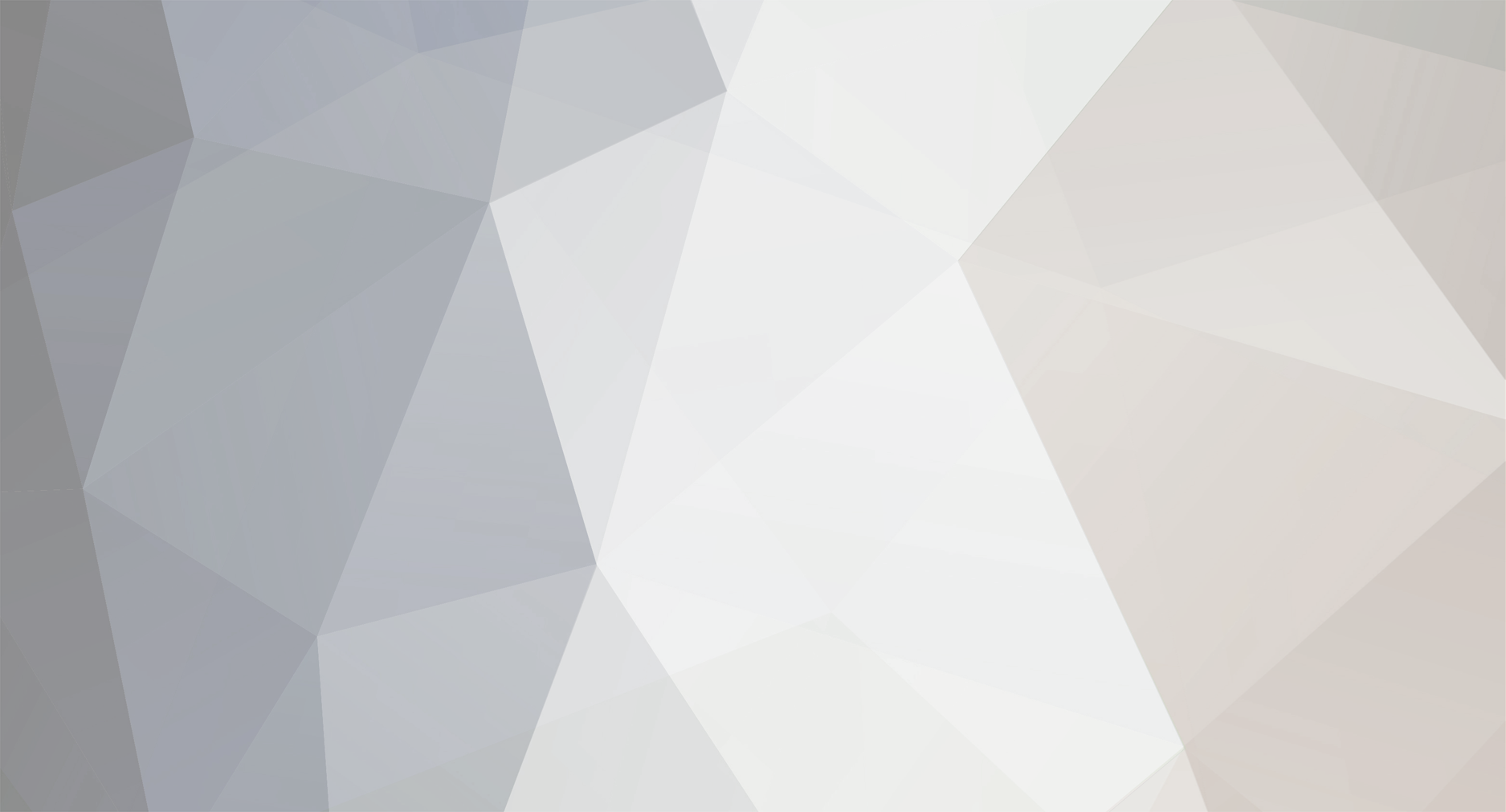
tenten
Members-
Posts
195 -
Joined
-
Last visited
-
Days Won
1
Content Type
Profiles
Forums
Store
Gallery
Downloads
Calendar
C-130 Hercules News
Everything posted by tenten
-
Right hand harness; ……..Heads I win, tails you lose.....
-
Munir; I appreciate if you inform us which wiring section is defective?
-
Munir, If fluctuating comes only above X-over;.....Check your coordinator potentiometer.
-
Thanks NATOPS1 for the last added safety note ; Actually for that reason, we asked them earlier not to fly or even start the engine without resolving battery issue.
-
Thanks a lot for all responses… First of all, aircraft is on the air after replacement of both the Battery and the Bat. Relay. Flying crew upon receiving the two items elect to change both items ….. discounting our advice… for to replace the battery at first and then to check the operation of Relay). However I understand from “pjvr99” that a dead battery cannot be recharged regardless of the operation of the Relay .. Thanks “Munirabbasi” & “NATOPS1”, for clearing the main point that I was asking for (And I understand from you that: Relay cannot be energized through power coming from external, it requires a good charged battery to connect BAT Bus with Isolated Bus). “hehe” & “n1dp” our aircraft is equipped with only one battery (Lead Acid) and thanks for the ‘”get home tricks”… n1dp… the battery was newly charged …. and seems crew is like you … but they “Blame it on Rio” … that’s way both items been replaced…!!!
-
Thanks brother for your response; I agree with you about replacement of the battery, and I agree with you that most of the relays on the aircraft are required more than 14v to response; But my Inquiry which may solve the puzzle is:… Which power source energize the Battery Relay, is it the battery only? Or both battery and external power? To make it more clear; we are having an aircraft (out of home station with no maintenance facility) crew reporting that the battery voltage is very low 7v, and Bat.switch failed to connect Bat.with isolated dc bus (which is normal due to low Bat.voltage); and as reported when trying to regain the voltage by recharging the battery with external power the battery failed to build up any voltage during the charge …. So the question is; Is it a battery failure issue only ? or battery relay failure issue preventing the battery from been recharged and subsequently lead to battery failure ? If systematically the Bat Relay is response only to battery voltage; then the possibility of failure is Battery only; but if Bat Rely should response to external power voltage, then Bat Relay is also suspected.
-
Battery Relay With Battery voltage less than 7 volt; is it possible for the battery to be recharged with external ac power? Systematically… is the “Bat. Relay” can only be energized through a good charged battery..? Or it doesn’t matter; as this relay can also be energized through external power for feeding the “Bat.Bus” as well for recharging the battery. Any feedback will be appreciated as we are having an issue of one of the C-130H.
-
Hence fuel control units (FCU/TDV) are eliminated, is it possible the defect cause is related to one (or more) acceleration bleed air valve delay in closing (sticky)..? If so, certainly the TIT at the time will be higher than normal until valve/s are forced to close; as for other indication, I am not sure if the fuel will be higher or not (air to fuel ratio); the torque should show somehow less until defective valve/s are closed.
-
Locking the TD during fuel governing and pitch lock check
tenten replied to tenten's topic in C-130 Technical
Thanks "Lkuest" for your technical details which help me a lot to have a look at the TD electrical circuits; and by going over the "twisted circuits" it confirmed all the points that you stated in wards. Therefore-in short- can we say… 1- TD valve cannot be locked if TD switch is placed to "lock" below cross-over. 2- Advancing throttle to above cross over while TD switch being locked below cross-over will have no any effect on the TD valve brake.(brake will remain unlocked) 3- Correction light will remain illuminated on the entire throttle range if TD locked below cross-over. 4- The only advantages of locking the TD below cross-over are: a- To arm/energize the "normal limit circuit" on the entire range of throttle. (for TIT not to exceed 1077*). b- To deactivate the BIAS & SLOP corrections.(No fuel trimming at cross-over). Steve1300, I agree with you on the point that TD system is not an effective issue to have the pitch locked; it may only help "if in AUTO" on the case of rpm dropping to below 94% once throttle is retarded while the pitch is locked (over-temp. protection). As for your second point, I understand that you prefer to have the TD locked below cross-over to avoid any value of fuel trim in order to check "uncorrected fuel flow" against fuel governing chart/table. -
Locking the TD during fuel governing and pitch lock check
tenten replied to tenten's topic in C-130 Technical
Lukest, I have been having the same idea on how TD system works as you have it, until I came across the following which mix me up…. Quoting TM 382C-2-3 section 3-page 3: "The other switch "66 degrees coordinator microswitch" is actuated at a throttle lever setting of about 66 degrees and opens a circuit to prevent the temperature datum valve brake from being locked at a throttle lever setting below 66 degrees". Therefore according to the above; the TD brake should not go to lock below cross-over (open circuit) In which my questions arise… what if passing across the 66, while TD switch was already on locked position? Is it going to lock? And if it is supposed to lock; normally it should lock in a position having no any correction/trimming (Null position). As for the correction light, they supposed to remain illuminated hence the system is locked below cross-over. On the other hand, is there any holding circuit (relay) to maintain the lock position on the case of cycling the throttle below and above the 66 switch to prevent the cycling of the TD brake? As for how the system will act if locked? I agree with you and with "pjvr" regarding the existence of over temperature protection. -
In two similar cases we found the cause was related to a deteriorated fuel nozzle gasket..
-
Hi to all members and guests, Looking for an answer to the following... On "fuel governing and pitch lock check procedures" almost all manuals -on hand- are asking to lock the TD; some manuals required to have it "locked" at a governing speed (above cross-over), others asking to lock it once retarding the throttles to below cross-over. The main concept of locking the TD to my understanding is to avoid any sudden change of power when passing through cross-over point.. However which is not clear to me the idea behind locking the TD below cross-over; 1- Is the TD valve going to "Lock" below cross over? Hence the 66 coordinator switch is not actuated yet? 2- How the TD system is behaving once locked below cross-over? 3- How the TD system is behaving once throttles are advanced and passing through the 66 deg….. ? Any highlight on this will be appreciated.
-
Technical question regarding an engine malfunction
tenten replied to wildweasel_pt's topic in C-130 Technical
Let us create this scenario to (somehow) explain a defective paralleling valve: Due to valve internal malfunction; Paralleling valve at de-energized condition is not retarded to a full open position. 1- During initial rotation (valve supposed to be fully open) but due to not fully open, the fuel pressure before the 16% rpm will build up but not sufficient to trigger the secondary switch. 2- At 16% the valve will be energized to take a full closed position, this will cause farther increase of fuel pressure causing earlier than normal indication of secondary light. 3- At 65% the valve will be de-energized, thus valve will return to the previous position (not fully open) consequently the pressure will slightly drop causing the light to be off. (You may not see a clear indication of TIT cutback). 4- During flight as fuel temperature will decrease thus fuel pressure will increase and it may reach a point that trigger the secondary switch causing the light to be ON specially during cross feeding the engine from high pressure pumps. Is it a possible scenario ….? -
Our defect is solved by changing the NLG actuator, hoping to you the best to solve "the puzzle of the 3 seconds". NATOPS1 I did not catch your point when saying: "If the pin does not retract you will retain the ground and the down indication will remain" As for the LG warning light it was working normally and was not affected by the malfunction of the NLG position indicator. Yes; the point that hesitating us from flying back with the defect is exactly what you have said: "If you fly and retract the gear the next extension may not be "real" and the internal lock may not be engaged". Anyhow thanks to all for the feedback.
-
Thanks Ramrod for your help and clarification, as for the down lock switch it is LMCO part, and as for switch adjustment we have tried all setting of adjustment, but none of them worked. At present our intention as you state in your post is to replace the NLG actuator, but we are facing some difficulties on doing the task out of home base, we are trying to bring the aircraft under "Exceptional Release" and deal with it at home station.
-
Ramrod; let me highlight some points noticed during ground check with aircraft on jack, it may help in finding the defective component; 1- During ground with electrical power turned off ALL landing gears position indicators are showing "barber pole" which is a normal condition. 2- With power ON and gears down all indicators showing down. (Also normal) 3- When LG control handle is selected UP and all gears start the transition; mean gears only will show "barber pole" during the transition but the nose will remain showing down indication ALL the gears will retract normally to up the main gears will show up indications, while the nose will keep showing down indication. With this condition (NLG up, control handle up) when removing/sliding back the down switch the nose gear then will show UP indication. Therefore it seems that keeping the down switch under the depressing of the NLG actuator pin is the main cause of not seeing the barber pole" during transition nor seeing the UP indication when the NLG is at up and locked position. And it seems that the up electrical contact of LG control lever has nothing to do with the position indicators if the down position switch contact is not at first released by the pin retraction.
-
Has anyone experienced this defect; After the take-off when gear lever is shifted up the nose gear position indicator keeps displaying down and lock indication, though actually(visually) the nose gear traveled to up and locked position. NLG down and up switches electrical circuit been checked, no abnormality found. NLG Down switch replaced, and adjusted with no effect. When aircraft on jack we noticed that when gear is retracting the NLG actuator pin is not retarded back, which I believe it should go either fully "IN" or at least partially IN to release the down position switch. The questions: Mechanically: Is the malfunction of the internal locking mechanism within the actuator on the pin mechanism only or the down locking totally is at fault? (note: during ground the safety pin can be easily inserted) Electrically: Why when the gear lever is selected up and the gear is up and locked does not give the indication of up? Operationally: Is it safe to fly the aircraft to home station with this defect? If yes, is there any precaution during landing? Appreciate any input to the subject.
-
As a flight engineer with sufficient flying hours, I never experience any figure close to the 3 seconds. The shortest transition of all gears is normally around the 10 seconds. The 3 seconds is mentioned in our flight manual only on the following case which is totally out of NATOPS question. The quoting note is from section 3 (emergency procedures) on the case of take-off continued after engine failure. Quoting: If obstacle clearance is critical, landing gear retraction should be initiated within 3 seconds after take-off and propeller feathering within 6 seconds after take-off ….etc. So, the 3 seconds and the 6 seconds is an action required by flying crew to perform, and sure the 3 seconds is not the transition time for the gears.
-
Brother, check your Email.
-
We will miss you "DAN"………… "My sympathy to your family"
-
Identical case is experienced, the finding in our case was a messing signal from no.2 pulse generator to the synchrophaser unit, it was due to looseness/momentarily brake of one wire within the pump housing plug (P392B), (the plug carrying the signal of no. 2 pulse generator towards synchrophaser unit). Notes: 1- The most suspected area is the pulse generator wiring output within no.2 engine, therefore re-check it from P392B towards fire wall J241B bearing on mind that it may not be detected during static (no vibration/no twisting). If confirmed to be good then go toward the next check points routing towards syncrophaser unit. 2- Sometimes just cleaning and re-tightening plugs/terminals will cure the defect.
-
Lkuest, Once upon a time during FCF, whenever a full power is set for takeoff and as releasing the brake and aircraft start shaking and rolling, a sudden huge cut of power (Fuel, TIT, Torque) is taking place in one of the four engines, RPM was also seen dropping down of the 100%, takeoff was aborted. Nothing was detected during checking/testing of the TD system, the defect as well it never duplicated during static full power, however FCU, TD valve, TD Amplifier coordinator...Valve housing, etc ....been changed, but defect remained !! During the third/fourth... takeoff roll and while defect been acting TD was shifted to Null, power was restored to normal. TD system defect was caught in the act, and to pinpoint as well as to confirm it, the thermocouple leads at the “Terminal Block†was swapped. During the next rolling check with TD AUTO, TIT indicator alone suddenly hanged-up towards full scale!! By changing both thermocouple harnesses defect never duplicated. As for RPM drop-In my opinion, and as stated by Lkuest- if the TD system is at fault, in which leading to a big cut of fuel, it is normal for the RPM to dropdown out of the governing range.
-
ref. Lockheed Training Manual.
-
Propeller once feathered during flight and passes the 90 degrees blade angle, relative wind (ram air) will act and tends to rotate the propeller in the opposite direction; the propeller brake is shape designed to firmly engage against this opposite tendency rotation force thus stopping prop from rotation. In the case of prop brake malfunction, the propeller will keep turning slowly in reverse, the slow speed turning is related to the fact that the 2.5 degrees angle (above the 90) is not big enough to produce a high seed turning, in addition to the remaining acting force of the prop brake while trying to function, which will definitely generate a heat build-up as Dan mentioned. Once “Air Startâ€â€ is initiated (condition lever pressed) the prop blade angle will start decreasing from the 92.5 and once passed the less than 90°; reverse rotation will stop, prop blade angle then will be in a position to initiate the normal rotation. Unfortunately, both our FCF manual and our flight manual (and maybe yours) do not mention any precaution or action against this type of malfunction (I mean reverse rotation/prop brake malfunction). I have listened to some techniques on dealing with such defect during flight, but none approved by any manuals. So the only safe advice that can be given is: If the case is during FCF, don’t delay the air start of this engine, and if during emergency shutdown reduce the air speed (not below any safe speed), and ask for landing at the nearest suitable airport.