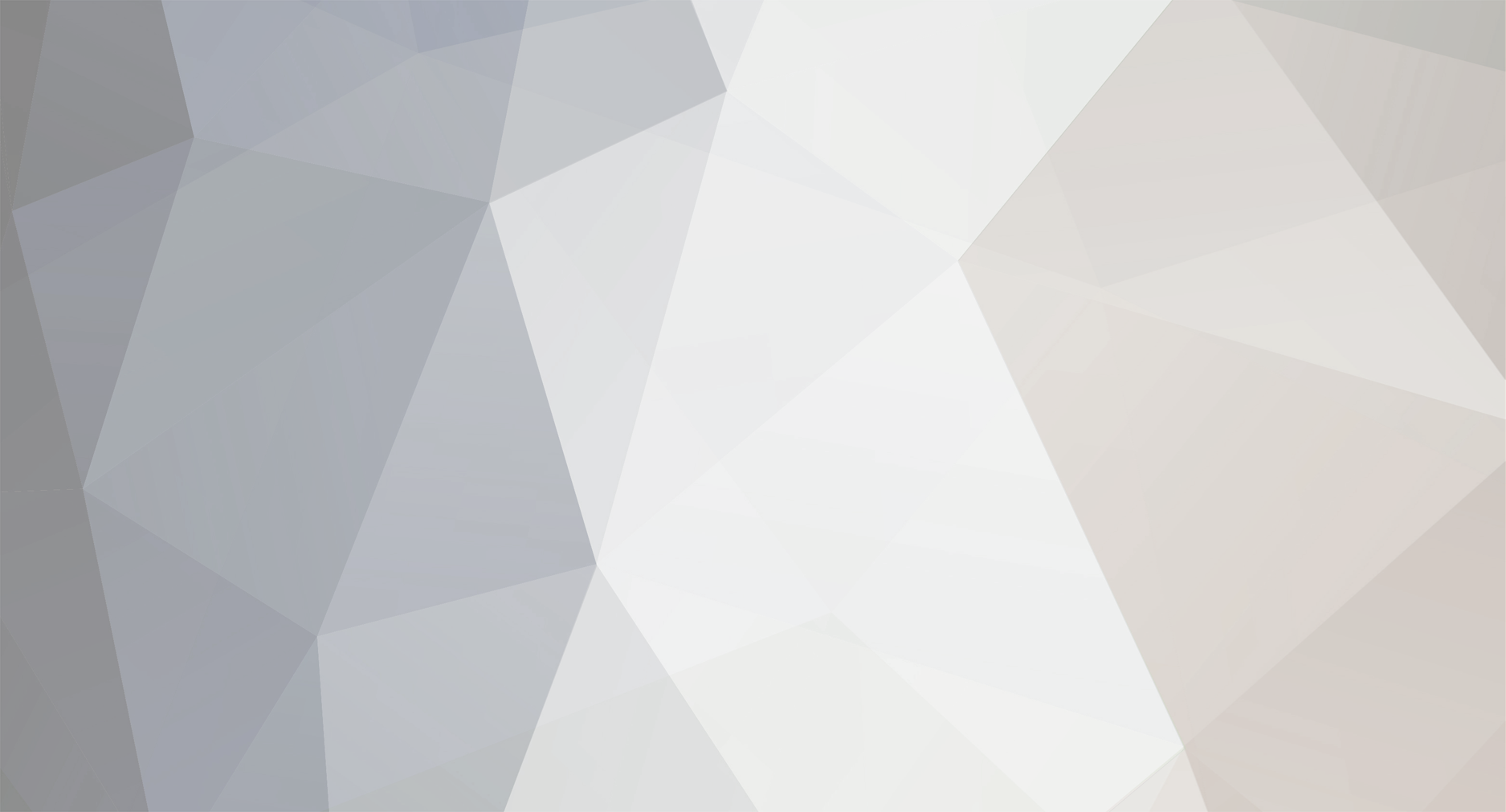
NATOPS1
Members-
Posts
785 -
Joined
-
Last visited
-
Days Won
7
Content Type
Profiles
Forums
Store
Gallery
Downloads
Calendar
C-130 Hercules News
Everything posted by NATOPS1
-
Tiny, Sounds like the "can do" is the VALI (varible altitude limit indicator) for selecting the minimum alt for flight/ approach...anything above this and you "can do" it....? With that said if it works below 300' then it sounds like the system is good just not enough "power" getting out. As sugested check all you RF connectors (look for connectors that "spin") If you have a similar aircraft and a TDR (time domain reflectometer) and a few "RF Adapters" hook into you good aircrafts RadAlt RF cables TX and RX and run a strip. You will see the length of the ant cable and the type of termination (ant) open or short. You can then compare your bad aircraft RF lines and see if they are different... if it is shorted you will get "less" power out and no Alt info above a certian height (300' maybe)
-
I dont have an issue with it other than training. Our mission (IFR/AR) requires two bodies in the back so you will have two fully qualified crewmasters vice one and an observer(working to become a crewmaster). It will be a much longer training track and unless it is a load to crewchief first or crewchief to load track with some ojt/experience in between the time to train will eliminate some students....
-
Any current or former Blue Angels on today? Wondering what version of the NATOPS you use.. Navy or Marine version .. I say MARINE KC-130T. Question is is it the same as the fleet or with specifics for your mission.... Thanks
-
Do you have regulating bleed air valves or OPEN closed valves? What is the bleed air check time? Maybe as simple as a bad bleed air pressure gauge...
-
Dont laugh too much but I guess you havent heard of the "Crewmaster" position.... Crewchief and Loadmaster.....wonder who is going to fuel the plane while the "Loadmaster" is loading and doing the Form F.
-
http://www.artsinheaven.com/search_items.asp
-
YEA RIGHT... Not so much the J has FADEC, so you push them to the stops and it adjusts for conditions to give max power. On approach you still have to set and monitor the power.... Auto-feather on the outboards for any "auto-feather" condition. The inboards will windwill at 100% if another engine is feathered. If all four flameout the inboards will windmill at 100%..........
-
The Gen Out light is Illuminated The ATM powers the Ess AC Bus The GCP has been swapped (with an engine and found to be good?) And the Gen Contactor has been changed. Pull the "ATM gen out light" CB and see what happens.
-
Victorp1.. those are close to the numbers I remember... 300 and 350... I remember them by association engine oil burn per hour .35 fuel burn 350 per hour...
-
HSI (course knob) Think of a bike tire with the spokes going out from the center to the wheel ("radial" straight line from hub to wheel...not crossed like your bike) 360 degrees in a circle and 360 "courses you can "dial" in. So if you placed the hub of the wheel on the center of the airport (navigational radio) and you dial in (select a course on the HSI) you would fly that spoke into the airport. So if the runway was say 360 if you dial in 360 and fly it straight in (course bar centered) you would fly right down the runway... then just set up a little descent (500-700 feet per minute) and touch down... HSI (heading set) is a compass reading only. Select say 360 and turn the airplane to 360 and the airplane will be going (heading) in that direction... With that said (360 heading) the course will be different if there is any wind from the left or right. You will have to fly a (heading) other than 360 to maintain the 360 course....This heading will compensate for the push from the wind.... What simulator program are you using?
-
128F thats just TOO HOT!!! You can keep ALL that.... We would also rotate the start from 3 to 4 to 2 to 1 to limit the exposure to the slower start times and higher temps (if and when it was an issue) Thats kinda why I mentioned the turbine... If it has been burned then its ability to produce power will be lowered and thus increase start times.. Dont think that is the problem though... I think when the Null is adjusted the start times will come down.
-
Agree that an increase in TIT to 800-810 (5 minors@ 4C each) will decrease your time to start. (780 seems quite cool for the conditions) This will increase the energy available to drive the prop and engine. The starter only has so much power to drive the prop and engine. 60% starter limit. After that only the turbine can do the work to get the engine on speed, (“on speed†time limit of 60/70 sec) The Null adjustment will provide increase energy to both phases of start (starter engaged and disengaged) If you look at your starter release times it takes much longer to reach 60% RPM and then double the time to get on speed. The turbine is also suspect if burned it will not produce the required energy to complete the start within the time limit. Do an efficiency run and see if you engine performance is low. Also, check if you have (one or two) bleed valves stuck closed or not fully open...more work than the starter is capable of doing (within the time constraint) 108F crap thats hot!!!!
-
underfloor heating shutoff valave weird behavior
NATOPS1 replied to qasimzaheer's topic in C-130 Technical
SO with the electrical connector removed and you pressurize to 1.5 the valve opens? Also is it very rapid opening or slow? It (UFH valve) is a motor driven valve so it may just be bad (motor shaft) not holding position. Once there is an external force (1.5 in hg) of pressure the valve is "pushed" open.... You say "Heavy Bleed comes out" please explain. Do you have the floor plates removed so you can see under the floor? -
Remove "pressurization and Air conditioning" from the same sentence. The only common point would be the AC Press Master switch. Make sure the wires on the back are tight... Jump both of your temp control boxes. B to E and then C to F. This will remove all the voltage sources except the manual temperature control. Be carful as you do not have any duct protection. If the valves respond to your temperature switch then your basic system is operable. Then you can tshoot the control system.
-
underfloor heating shutoff valave weird behavior
NATOPS1 replied to qasimzaheer's topic in C-130 Technical
Take off the electrical connector (UFH valve) and see what happens.... if it still opens you have a structural issue. If not electrical... have you place the master in auto to see what happens? -
Watch your bleed air pressure when the start valve opens. Note how low it goes and then the check the pressure between 10-16%... Our books put the pressure 10-16% no less than 22 psi. Your pressure should drop off quite a lot (20 maybe) then recover to the 32psi, 22 minimum. Your start control valve regulates the air pressure to the starter so if it (they) are regulating low then the starter will have insufficient air and slower start times yet you will see "good" air pressure....... Also the GTC load control may be getting a "too hot" signal from the Pneumatic thermostat (THERE ARE TWO) you want to check the one for the load control RPM above 95%.
-
Duct anticipator (sensor) controls the more heat signal......
-
jump your temp control box I think B-E and C-F then drive your valve to hot (go slow as you have no duct sensor) if this works replace your duct sensor... if it is bad it will send a "less heat" signal all the time and drive full cold....
-
Gotta love installing bad parts... please let us know what the issue is when you find out... Strang to have this once much less several times.... bad valve housings that cause blade angle increase when at high speed. go figure..........
-
http://www.dynamicscalemodeling.com/c-130.htm Make sure you check out the videos!!! I wish I had that kind of time on my hands!!! Fishing and building models...
-
Tiny, May you find peace in your heart for the pain is no more...
-
So the easy answer is fuel flows through the tubes and oil flows around them.
-
So you changed the prop... Does that mean just the prop or the prop, valve housing and pump housing as an assembly? Understand the engine is what you are checking and it works fine. ONE DOWN!!! So the Prop is defined in this instance as just the propeller and dome? Same valve housing? Same pump housing? Still very strange!!!
-
Very cool video!!! Have you used a different pump housing? The increase in speed would directly affect the pressure output of the main and standby pump. The standby (twice as much voulme) may be suppling pressure when not needed...normally only provides "extra" pressure/volume to get faster response. If it thinks the system wants more due to a bad check valve it may be driving the blade angle without any input other than speed. In HSGI if you retard the throttle towards reverse does the RPM increase or overspeed or does the fuel flow and blade angle change? What happens if you leave the engine at HSGI for an extended time? TIT? RPM? Tq was/is 6000.
-
Good luck this is very strange indeed!!! Guys... The blade angles are changing when the engine is shifted to HSGI... Acc bleeds will cause the TIT to go up but the blade angle is "set" by the throttle (in the ground range). The bleed valves will only cause the TIT to increase (less cooling air) not the "power"...