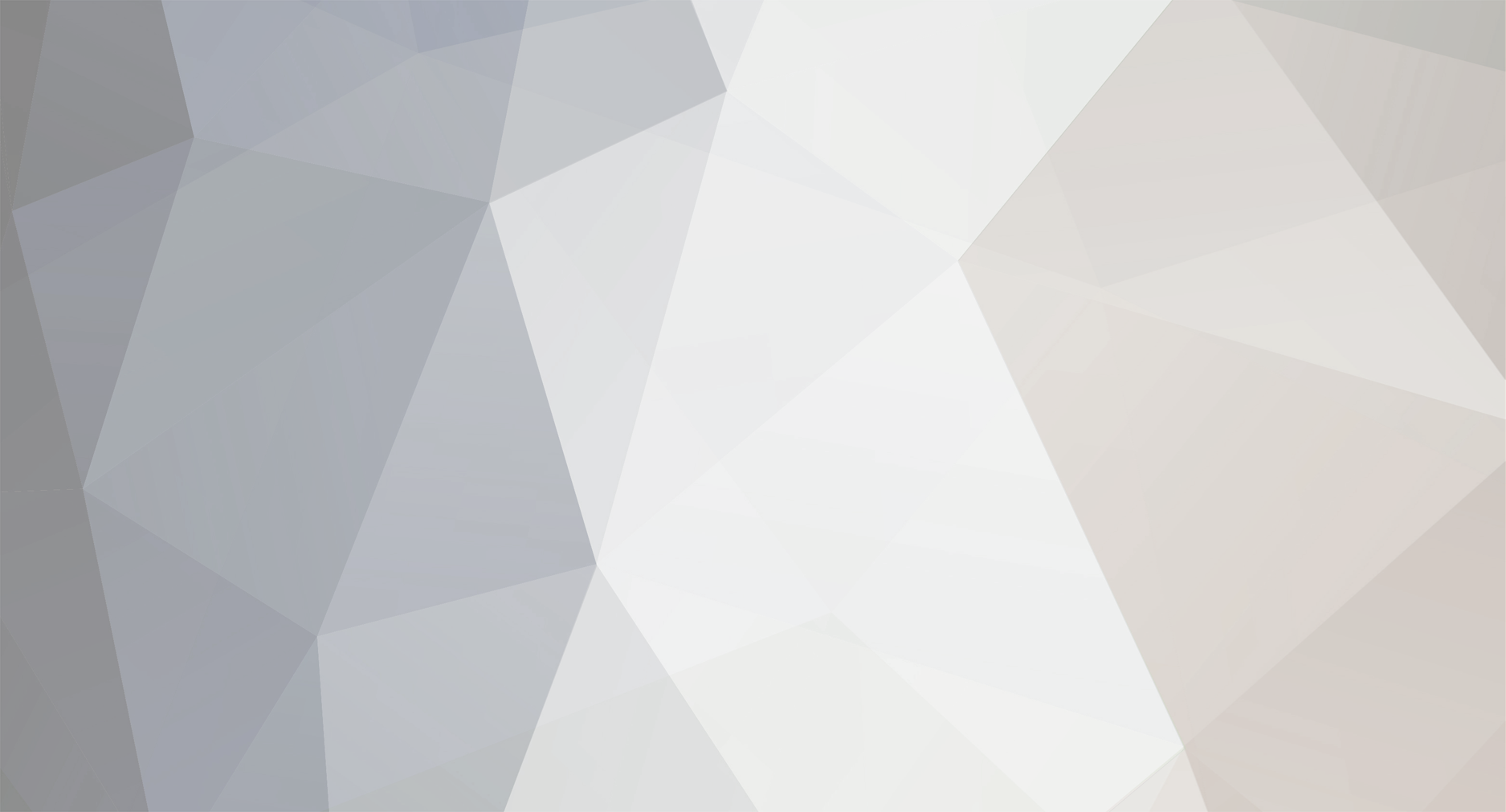
Steve1300
Members-
Posts
246 -
Joined
-
Last visited
-
Days Won
2
Content Type
Profiles
Forums
Store
Gallery
Downloads
Calendar
C-130 Hercules News
Everything posted by Steve1300
-
If an engine, in Low Speed Ground Idle, has the fire burning in the turbine area, how does that happen? It will start with low start TIT (750) and run in LSGI, but there is a fire in the turbine and the blades glow. The fuel nozzles were flow checked and they were good. If the engine is sped up to NGI, the fire goes out and when shifted down again, the fire stays out. I have never seen that before, and I don\'t really have an answer as to how it is happening. The only theory I can come up with is that, for some reason, the fire is not starting in one or more burner cans, so the fuel from that nozzle is making it back to the inlet guide vanes where it is igniting. Anyone have an idea or theory to share?
-
Your statment sure makes it believable that it is not a powerplant problem. If the speed affects it, then it has to do with the airframe and flight surfaces. If the rudder is, in fact, installed and rigged correctly static, then the airframe has a problem. I would wonder if there is a problem with the rudder mounting hardware/holes that allow it to move with an airload that does not show up in a static condition. If not in the belcrank at the bottom, perhaps the mounts running up the vertical need to be looked at. Personally, I\'d remove the rudder and look carefully at everything. I\'d also expect that an airframe asymmetry check is in order.
-
WE HAVE A PROBLEM OUR SOME C-130 B / E AIRCRAFT
Steve1300 replied to airman57's topic in C-130 Technical
I am still hoping that the solution to this problem gets posted here. Are there any results on the troubleshooting yet? -
This is great! Thanks a bunch.
-
WE HAVE A PROBLEM OUR SOME C-130 B / E AIRCRAFT
Steve1300 replied to airman57's topic in C-130 Technical
IT would be helpful to know things like outside air temperature, your altitude, and the TIT and RPM when the stagnation occurs. Also, are you trying the start in \"null\" as well as \"auto.\" Where is your null orifice on the TD valve set to? If it is an APU/GTC start, what is your bleed air pressure duing rotation? Have you tried it with another engine as the bleed air source? With everything you have changed, there isn\'t much left other than the fuel control itself. -
Would be appreciated for some of you prop guys
Steve1300 replied to Steve1300's topic in C-130 Technical
Thanks for your input on that. We are having to deal with front cover leaks which I can only attribute to a pressurized atmospheric sump. We never find bad o-rings,but the fluid is getting past them. I am thinking that most \"lip seal leaks\" are not lip seal leaks at all. That\'s why there are other actions that have to be taken instead of changing the lip seals. Anyone else willing to get into the discussion? -
We are currently working on some pump housing showing leaks. The plane has been in cold weather, so we also have some blade leaks, but nothing abnormal. The other herk forum has lost the old posts from back when this question was asked, so I am hoping that some of you ol\' prop guys will repost your answers. The pump housing actually looks simple when the covers are off, but they aren\'t simple when tracing the source of leaks when part of the propller assembly. I am interested the causes of \"lip seal leaks\" and those that just look like lip seal leaks. We have three props now that appear to be lip seal leaks and none of them were overserviced. Perhaps, when we get some of you to post some help for me here, I can save the whole thread so it doesn\'t get eaten up by the ether-net. Thanks in advance........:)
-
No, I was at Forbes just before it closed. C-130s then belonged to TAC instead of MAC. Being a herk crew chief back then was more like being a mechanic instead of an assistant loadmaster.
-
So, based on the last three posts, the prop cannot control RPM (since it is pitchlocked) and the fuel control can\'t operate as normal (since it is in governor mode). It would seem to me then that, if we want to check out the fuel control action as this point, once we bring the throttle back toward flight idles until RPM is back at 100% and release the Check Switch so that the fuel control is no longer in governor mode. At that point, if the flux continues, it is not the prop. If it fluxes at that point, it must be because of the engine fuel control(since the TD system swtich is in \"locked\" position). Am I correct here?
-
And I, for one, get a lot of valuable information when people share these problems and their solutions here. I\'d like to know how the tough ones get solved.
-
It is actually a circle of about 165.2 inches in diameter. We don\'t actually notice it, especially on a short Herk, because the center wing box and wheel well pods disrupt the appearance.Then, the nose from 245 forward and the tail at 737 change the shape. So, my answer would be that the \"aluminum tube\" we fly around in is, indeed, a circle. :)
-
I have the paid version of Google Earth, and I have not seen yet where they provide up-to-date imagery. While the notation at the bottom of the image claims a 2007 copyright, the images are seldom from 2007. Most of the ones that I look at are at least three years old. We are going to PC our way into oblivion.
-
It seems to me that the most inaccurate gage on the plane which is not calibrated is the generator frequency meter. Then, on top of that, 100% RPM is actually 398 cps. Hard to read that off the meters in our planes. I like the phototach personally.
-
I have found a phototachometer to be very handy for checking RPM gauges. Once a gauge is 1% off, I replace it. Same thing goes with TIT gauges. When I see a 6-degree error, it comes out. The problem there is that our TD system test sets are only as good as the calibration folks make it. The hard-sell for me is to get folks to calibrate torque indicators. I find that an inaccurate torque gauge will make for lots of wasted effort, but some people don\'t want to calibrate them correctly, if at all. While errors may be acceptable to the crew, it is a very bad thing for maintainers.
-
The actual RPM limits (using an accurate tachometer) is 94.4 to 98.3. The compressor bleed valves should never open. The allowable error in your indication system is plus or minus 1%. The writers of your flight manual allow you guys to see 92.5% as long as the compressor bleeds don\'t open.
-
We no longer use the turbines which called for lightweight general oil. All of ours now use engine oil. Much simpler for us.
-
I appreciate all the unput to my original question. I am left with the same thing I started with. The pressurized sump dipstick, when used on a just-shut-down hot prop tells you if you have \"enough\" oil. It will NOT tell you if you are overserviced. The oil backing up into the toilet bowl does NOT tell you that you are overserviced, but it does tell you that the pressure has not equalized to the atmospheric sump and/or pressure is trapped somewhere. The atmospheric dipstick is only there to tell you when you are overserviced. So many times I\'ve seen folks try to do the periodic servicing through the atmospheric dipstick and overserviced the prop. Other folks actually get frustrated and dump a quart in to make sure that they don\'t get a \"service me\" light. This is all just my experienced opinion, and you can tell since I originated this thread that I appreciate other views on the subject. Thanks again.
-
Thanks for all the input, folks. As many years as we have had these props (not counting the three-blades \"A\" model props), the only trusted method for me is to use the original way to do it. A leaning Herk gives false fluid level indications. The atmospheric sump dipstick will tell me only if I am overserviced and will not tell me if I have \"enough.\" The pressurized sump seems to be the only good work zone for fluid checking. Many times, I carried a screwdriver and no dipstick. Sometimes, I sure wish there was a sight glass on the pressure sump cover. Now, how to explain this to the new guys at work........?:S
-
Well, so far I can see that it looks like the answer is that there is no real answer? The Lockheed Service News article from the Canadian Air Force said that their success with prop servicing stemmed from having four people available to check props immediately after shutdown and placing #1 blade to 12:00. Yep, they referred to the atmospheric dipstick only. I started on Herks before there were any atmospheric dipsticks, so I never did trust them. My experience has shown me that, IF my pump housings had the same drain-back rates, I could pull in on one afternoon, and T my props with #1 up. The next morning, while by myself, I could cold check my props with no assistance or cycling required. If I got 2\" of fluid - approx - on the atmospheric stick and showed nearly one quart low with the pressure sump dipstick, my fluid was good. If either of those readings were not there, I had to cycle the prop to check it. I just find that it is difficult to explain that to the new guys we have at my company, as I always felt that my suggestion should be fool-proof, but its not. There will always be a pump housing out there that will prove me wrong. That\'s why I am bringing this question to you guys. Thanks for your responses.
-
After all these years, the subject of prop servicing is still discussed. I have experimented the last couple days with propeller oil levels, both static over-night cold level checks and cycled prop pressure sump and atmospheric dipstick checks. One aircraft leaned when I checked it and then I checked it again after I leveled it. What I found out was that the pump housing all act differently when the feather pump motor shuts off. Some drain back immediately and others don\'t drain back at all. A leaning aircraft throws the measurements off. I also found that if left for an additional 24 hours, the levels in both sumps increase. The amount draining back into the atmospheric sump is more than the amount that finds its way into the pressurized one. (#1 blade always at 12:00) I reckon, I need for one of the old propeller guys to offer some words of wisdom that I can pass on the the folks with whom I work. What is THE good way of checking fluids when we are out on the road by ourselves? Should we run them full or just the pressurized sump full? Is there a fool-proof way to get an accurate check (in your opinion)? Any information from you old pros is appreciated. Our biggest fear is over-servicing, but I get embarrased by a low oil level light. :blush:
-
Well, you can send me the tape and I will use my recorder to put it on DVD. Of course, you can also get your own recorder or set up your computer to do it. If you want me to do it, let me know. [email protected]