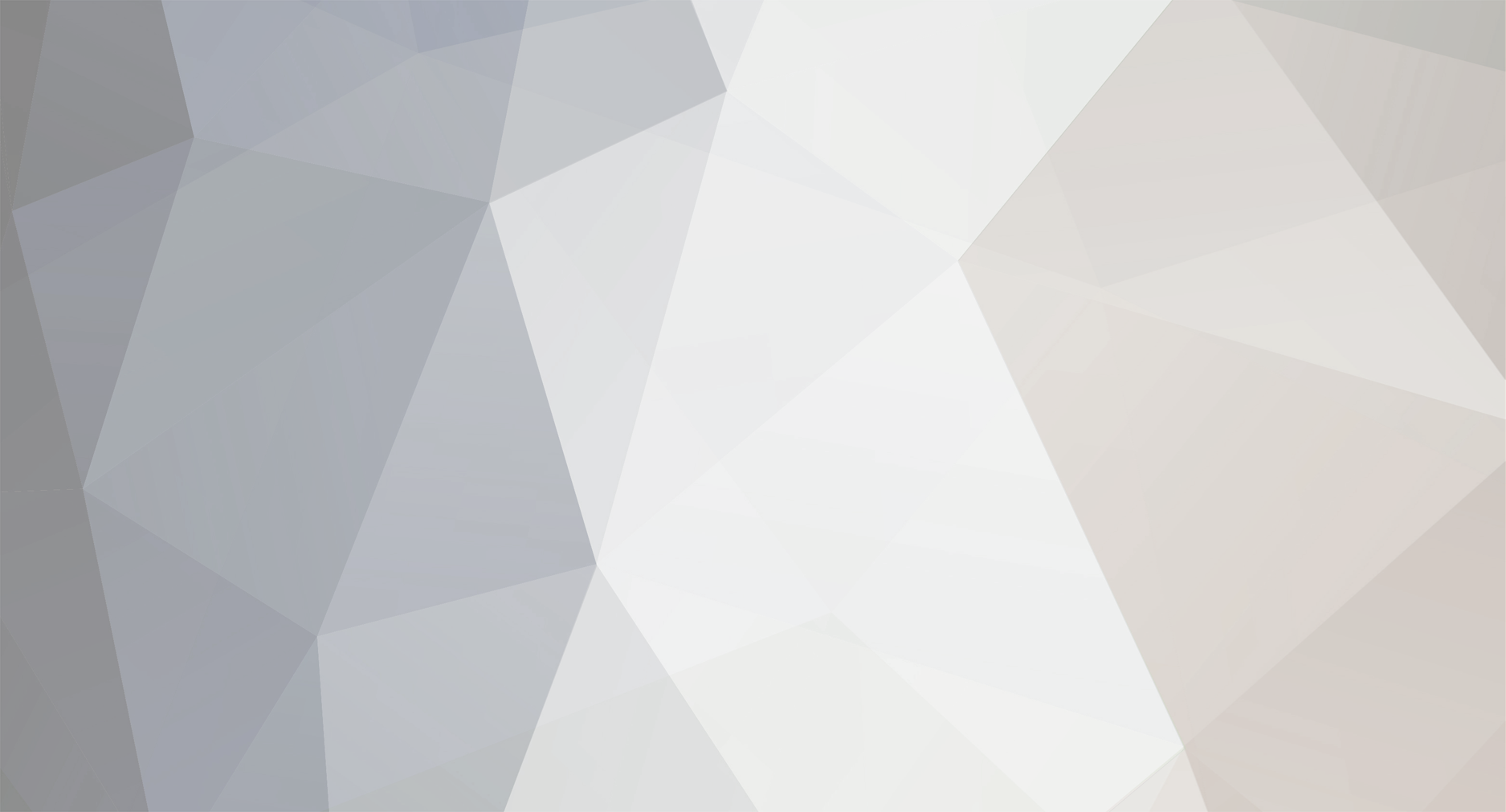
Lkuest
Members-
Posts
317 -
Joined
-
Last visited
-
Days Won
5
Content Type
Profiles
Forums
Store
Gallery
Downloads
Calendar
C-130 Hercules News
Everything posted by Lkuest
-
If I had a guess I\'d say the proposed -100 was most likely the Air Force version of the -427 as it was under development in the early 80\'s. Also, the AE2100 has shp figures closer to the -15 than they are to the -427. Just a guess.
-
You can search Allison T56 in Wikipedia to clear any confusion as to the different T56 variants. I haven\'t heard of the -21 variant, but if there is one, it is probably for the Air Force. The Navy uses even-numbered designations with the exception of the T56-a-425 and -427 variants. The Air Force usually designates it\'s T56\'s with odd numbers.
-
Anyone else notice the RT horizontal stab looks like it was clipped?
-
Google Earth is showing eight C-130\'s. Don\'t know how old the pictures are or which are A models, but two are grey, the rest are either camo or whitish. Don\'t know how much that helps.
-
That might depend on how many pigs you see flying around.
-
WE HAVE A PROBLEM OUR SOME C-130 B / E AIRCRAFT
Lkuest replied to airman57's topic in C-130 Technical
On top of all the good suggestions, double check rigging. Usually before engine start, the propeller blade angle is anywhere between 6 and 10 degrees on the protractor. If it is excessive, move the blade angles to reverse, then move them back to ground idle. Assuming the linkage part of the rigging is correct, the blade angle for ground idle should be between 5 and 6 degrees if you move the blades youself. A 10% hang is usually a bleed air problem. If the manifold pressure drops down really low, say 5-10 psi, the engine is taking all the air that is provided, and the GTC isn\'t providing enough air. If the manifold pressure barely drops, the engine isn\'t taking the air that the GTC is giving it. If manifold pressure stays high, you can remove the starter sensing line from the starter control valve and cap the line and fitting off. This will force the starter control valve full open (only for troubleshooting purposes.) Another thing to do would be to start the affected motor up, then while it is running, check for leaks at all bleed air ducts. Also, ensure the anti-ice valves are closed by doing the LSGI anti-ice check. To test the speed valve, simply disconnect the speed valve and cap off the line and fitting. If it immediately starts easier, the speed valve is bad. -
That may be so, but we perfected it!:laugh: :laugh: :laugh:
-
Would be appreciated for some of you prop guys
Lkuest replied to Steve1300's topic in C-130 Technical
I\'ve had a Guard guy tell me he found an atmospheric dipstick mounting nut loose cause a leak from that area. Unfortunately, you have to take the front cover off to retorque it. Another thing to look out for is to make sure before installing a rear lip seal that the drain holes on the pump housing are at 6 o\'clock, otherwise there will only be one way for the vented fluid to go, and that\'s out of the rear lip seal. -
Would be appreciated for some of you prop guys
Lkuest replied to Steve1300's topic in C-130 Technical
I\'m sure the prop shaft seal leak has been mistaken for a rear lip seal leak many times. My rule of thumb is if the prop shaft leaks with aux pump pressure, it\'s the prop shaft seal. If it leaks as soon as you let off the aux pump, it may be a clogged breather preventing the venting of pressure out of the atmospheric sump or simply a worn rear lip seal. I\'m kind of ignorant though when it comes to clogged internal passages/filters/screens causing leaks. -
If there is only one plane being moded with 8 blades, than that one couldn\'t be it. The pics I saw were of 92-1536 from Wyoming.
-
did you ever find your problem?
-
7829 is not a ground trainer. It is still flying with the 62nd. 7764 is indeed a ground trainer. 1816 and 1296 didn\'t go to AMARC because of the lack of funding. Apparently it costs more money to put an aircraft into mothballs than it does to run it up every 30 days. At least we have two cann birds to choose from! I couldn\'t tell you about 1793.
-
That particular plane now flies for AETC, but you\'re right. It is pretty low time.
-
Wow, 120psi is a lot. On a brand new engine, I wouldn\'t read too much into it. I did talk to a guy though, who said he\'s seen multiple engines on the same aircraft with at least 116% efficiency. He was convinced there was something wrong with them, but the engine troop that came with the plane insisted everything was legitimate. They ended up changing the engines out because of excessive compressor stalls. How they got up to 116%, I have no idea, but it may have involved some unapproved modifications (guard bird). pjvr99\'s answer sounds good. As long as you don\'t suffer from compressor stalls, you should be good to go. One question though. Is is a -7 or a -15? If you have a -15, everything is golden, until flightline has to do overtorque inspections once a week. If it is a -7 engine, the aircraft the engine is being installed on doesn\'t have bleed air regulator valves. A high efficiency engine can be a problem on E-models, and we\'ve changed an engine or two for being too powerful, and for some legitimate reasons. The problem is that if an engine\'s output air is not regulated, and it is a lot stronger than the other three, it becomes the only motor supplying air to the other systems. The flight crews check performance with the bleeds open and the A/C and ATM running. The strongest motor becomes the only engine losing air, and therefore power, and your 113% engine can turn into a 94% engine real quick, often hiding a legitimate low power engine that isn\'t putting out any air to the manifold. Maintainers check performance with the bleeds closed, so the problem likely wouldn\'t be found until the engineer checks power before takeoff. There is no maximum efficiency limit in the tech data, as long is there are no other problems associated with the engine being high power. You may have just found the four leaf clover. Congratulations.
-
This problem is obviously and indication problem. I\'ve never seen the inconel tubing cause this. That\'s not to say it can\'t, but I\'d start with the simple things and work my way out. The horrible thing about this system is engine fire and turbine overheat systems are indicated the same way, except the turbine overheat flashes the handle instead of making it come on steady for a fire. If you didn\'t notice if it was definately one and not the other, you may have to troubleshoot both systems. The fire control boxes do cause a lot of problems with the fire detection system. Water in the overheat stats cause a lot of problems in the overheat system, as do chafing wires and such. If you inspect the wiring and find nothing wrong, I\'d change the fire control box. If you don\'t have the resources to troubleshoot by changing parts, you could just swap the boxes around between two engines and see if the problems switches motors, but as with any safety-related system, I wouldn\'t recommend that unless you have no other choice. Don\'t waste your time inspecting the nacell overheat stats. They do not indicate in the T-handles. Don\'t forget, you also have a relay for each motor behind one of the left upper circuit breaker panel that could cause this problem as well. Of course, I\'m only and engine troop. An electrician may be able to give you better advice than this. I don\'t know how hard it is to just change the inconel tubing, because I\'ve never had to. Personally, I\'d start with the fire control box and go from there. They go bad all the time.
-
I think it\'s cool the Air Force is finally buying off a little on the 8-bladed prop, but wouldn\'t it have been cheaper to borrow Snow Aviaton\'s aircraft rather than modding an H-model slick for the sole purpose of using it for test flights? Maybe they wanted to mod an H-model since the current LC-130\'s are H\'s, but I\'m sure they could have put -15\'s on the E-model already moded and still came up with some accurate flight charictaristics.
-
The Brake Lock Relay will cause the exact same problem. If the speed switch causes the light to go out statically, it may also be a broken connection internally, not necessarily a stuck switch. Afterall, the switch is normally engauged until it exceeds 94%, at which time the switch breaks contact and telling the TD Amp via the brake lock relay to go from start to normal limiting. The 94% switch is completely independent of the 16% and 65% switches, so you won\'t even notice something is wrong unless you either get a hot start or you move the throttles up statically and observe the lights going out.
-
I\'ve seen this problem twice, and both times it was the coordinator. I promise!!! Just to be absolutely sure, all you have to do is disconnect the speed switch cannon plug(no jumpers, just disconnect it and let it hang), connect a new coordinator to the two cannon plugs on the back of the coordinator, and put the TD switch to auto. Move the input shaft of the new coordinator up and down from takeoff to reverse repeatedly while someone is watching the fuel correction light. If it keeps popping on when you go below 65ish on the protractor, the old coordinator is bad. This method is quick and painless. Simply disconnecting the speed switch cannon plug fools the TD Amp into thinking the engine is running. This way you can fully ops check the light without even starting up the engines. The only other component that has direct control over that light is the TD Amp. The signal also goes through the speed switch and the brake lock relay, but your speed switch is obviously good, and I would think your brake lock relay is good since your temp limiting check passes. If the coordinator doesn\'t fix it, try the amp. I\'m 99% sure it\'s the coordinator though.
-
Don\'t the T2\'s get the SOF wings?
-
airliners.net has a pretty good picture showing the wingtip fuel tanks they installed. Just set aircraft type to Lockheed C-130/L-100 Hercules, and type in 3688 in the Keywords block and it will take you there.
-
I guess when people fix their problems they forget they are leaving the rest of us hanging.
-
Did you ever figure out your problem?
-
This sounds like a problem that one of those \'Old Heads\' that have been around for 40+ year might have seen before. I know I never have, but I\'d give it a shot. Does this flux only happen only during the pitchlock check when in locked at 99% rpm, or all the time below crossover? If only during the pitchlock check, you are basically pitchlocked at your first torque via your Low Pitch Stop, which takes the mechanical portion of the valvehousing out of the picture. When below crossover, you are basically in null since you have no electronic fuel correction unless you exceed 1077 TIT. Like Gmon said, go to mechanical and null and see if the problem goes away. If it does, then there is a problem in the TD system or Synchrophasing system that is making corrections when it isn\'t supposed to be. If the problem persists when in mechanical/null, you are looking at a fuel control issue. If this flux is happening at all times below crossover, see what happens when you go to null. If it fluxes in null at all throttle settings, look at the fuel control. If it becomes rock solid at all throttle settings in null, I\'d change the coordinator and see if the problem goes away. I\'d be willing to bet that the coordinator has an internal short that is intermittently triggering fuel correction below crossover. This would only be the case if the fuel flux is erratic, like wires arking with vibration. Depending on the model of coordinator, you may not even get an electronic fuel correction light if it is doing this below crossover. This is just a wild guess as like I said, I\'ve never seen this problem before. Definately though, eliminate as many systems as you can (TD, sync) to help troubleshoot the problem. Hell, it might even be something off the wall like a speed valve, so check CDP when this is going on. If CDP changes a lot during the flux, that\'s probably what it is.
-
With problems like this, I can imagine the synchrophaser test set would help for checking aircraft wiring and valvehousing components at the same time. When you hit the prop governing check switches, the motor won\'t move much at all, so I wouldn\'t worry about that. The mechanical rack has mechanical stops that prevent the motor from getting greedy and taking or putting too much RPM. If the motor does spin all the way, you\'ve got bigger problems. When I troubleshoot pitchlock problems, I have a process. 1. With engines running, advance throttles to maximum power. Once stabilized, hit mech/gov switches A. If you pitchlock, no defect noted. B. If it doesn\'t pitchlock, proceed to step 2. 2. With engines running in the flight range, without moving throttles, hit fuel gov. check switches. A. If RPM increases, check fuel control fuel toppings rpm and/or change pitchlock regulator. B. If RPM doesn\'t increase, do sync and droop check/throttle anticipation checks a. If all checks pass, check wiring for fuel gov check switch. b. If all checks fail, check both synchrophaser circuit breakers for being pushed in, the synchrophaser itself, aircraft wiring, reference winding, speed bias motor Basically, since you changed the valvehousing, as long as the rpm of the prop doesn\'t increase, it\'s either aircraft wiring or the synchrophaser. If rpm does increase when you hit the switches, it\'s either the pitchlock regulator or the fuel control settings. I hope this helps.