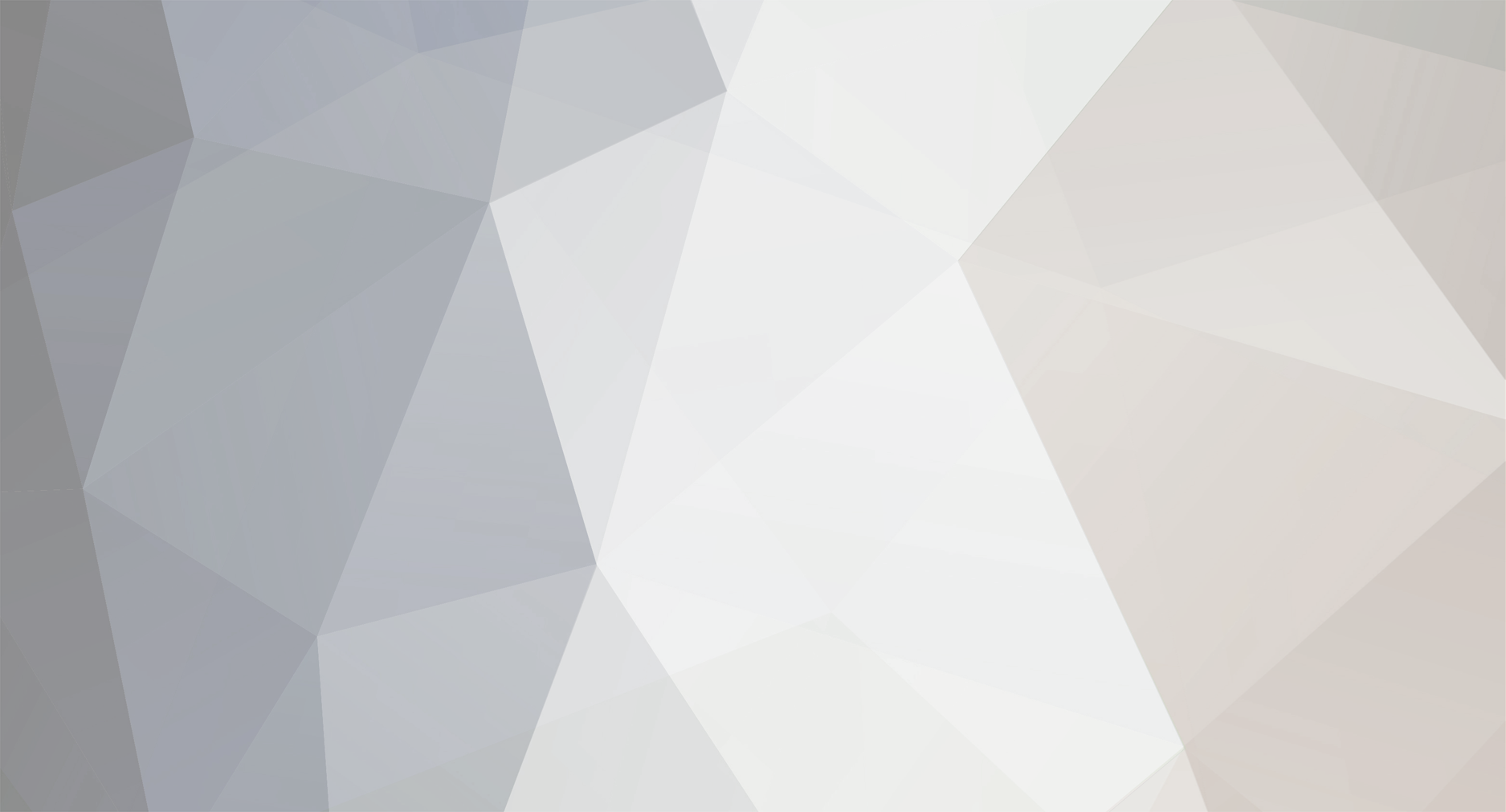
Lkuest
Members-
Posts
317 -
Joined
-
Last visited
-
Days Won
5
Lkuest last won the day on January 23 2023
Lkuest had the most liked content!
core_pfieldgroups_3
-
core_pfield_11
Went to LRAFB in November 2002 working as an engine specialist on the flightline at the 314 AMXS/Blue AMU. In May 2011, started working as an FTD instructor at Yokota AFB, Japan. Arrived back at 314 AMXS/Blue in 2014.
-
core_pfield_12
LRAFB
-
Occupation
C-130H Propulsion
Recent Profile Visitors
The recent visitors block is disabled and is not being shown to other users.
Lkuest's Achievements
-
I don't understand what you mean by "during runnup, the prop brake no longer works." The starter disengages the propeller brake at initial RPM, then is held apart by oil pressure as the engine accelerates. If you mean "after engine operates and is shut down," then you may have a defective propeller brake. Of note, it is normal for the propeller brake to not work below certain cold ambient air temperatures due to excess oil viscosity (engine has not been run). As for why it works after brake flush and not after engine run, I don't know. It may have something to do with the manual separation of the prop brake that makes it seat better. You can confirm this by inserting the tool to unseat the prop brake, apply air, then immediately removing it without flushing the gearbox to see if the problem duplicates. Also, if the propeller brake pads are worn, flushing will only help a little. You'll still have worn brake pads.
- 3 replies
-
- propeller service
- propeller
-
(and 2 more)
Tagged with:
-
Nacelle Heat Shroud/shield twisting NP2000 equipped aircraft
Lkuest replied to dexeadie's topic in C-130 Technical
It doesn't surprise me that the NP2000 props would have more stress-related issues. I hear the RPM is much more stable, which means it does a better job of being an airbrake for the engine than the old props, which would magnify torque-related stress. I'd expect you to see more truss-related damages though. I'd recommend reaching out to the Lockheed tech reps and see if they can identify a modification requirement for the E/H wings and nacelles that is newly necessary with a more responsive propeller. They may even have resolved a C-130J issue that they could retrofit into the older models. The NP2000 engines might just be easier to overtorque, a problem the C-130J wouldn't have with digital controls. Lockheed might just recommend a torque data-capture modification to make sure all overtorques are captured. -
I don't have any answers for specific part numbers. Just a warning that C-130E aircraft had 2 different wing part numbers installed. There was a design change (in 1968 I think), and the USAF re-winged all their old C-130E's for the new design. It would be best to contact Lockheed for this information as they may have records for if your C-130E was already re-winged, and what new plumbing (if any) would be required to install whatever Part Number you can get ahold of.
-
The dome shell could have excessive roughness. You could also have a newbie on the flightline topping your propeller up with engine oil.
-
SEC Fuel pump press light goes out before start valve light
Lkuest replied to HerkyFE's topic in C-130 Technical
I'm quite a bit rusty and I'm sure everyone has their own callouts, but I've never called "valve" during my engine starts, it was always "button out". My best guess is the "valve" callout would only apply to aircraft equipped with the start valve light. If the valve was still open (light on) in LSGI, the starter is likely still engaged by a stuck valve, which would make it an important thing to call out. -
If you are at power, actuate the switches, and the RPM does not increase at all and fuel flow does not decrease at all, the problem is in the synchrophasing system. This includes the switches, wiring, and valve housing electrical components. Without the electrical components being good, neither the pitchlock regulator nor the fuel control can cause the issue because they're not given the opportunity to do anything. This also assumes the low pitch stop is adjusted correctly.
-
If RPM is staying at 100%, and the pitchlock check is the only check that is failing, the only thing that remains is a wiring issue or the switch is broken. I highly recommend you break out the wiring diagram and start checking for open circuits.
-
NATOPS essentially already answered this question above. The analog indicator is allowed to be 2% low and still be considered safe for flight. There is a different RPM limitation for a digital indicator. If the RPM actually dropped below 94%, the bigger problem would be high TIT, low torque, and likely flameout. If you are reading 92.5 but the temperature and torque nearly match the other engines, the RPM is above the Speed Sensitive Valve transition of 94%.
-
I seem to remember going over 100 deg C just resulted in pulling the mag plugs, and going over 150 is an oil change. Pulling the mag plugs is to check for damage, then put them back in. My guess is 100 deg C is the limit because that's the point when damage becomes much more likely. If I had to guess why this causes an engine shutdown event, I'd say only a malfunction could allow the oil temp to go above 100 while flying due to the robust amount of cooling air available. If the engine is shut down for oil temps, it is a good idea to get the engine restarted for landing for maximum controllability and go-around margin. As for a reference, my guess is whatever tech data the owner provides. For the US military, that would be the 1C-130H-2-70FI-00-1-2.
-
Gimme the BPO work cards and 1 hour, and I'll throw down three "red-x's" and 20 "/'s"
-
Travel of RPM and Frq with throttle movement.T56 Eng.
Lkuest replied to Badiul Alam's topic in C-130 Technical
Only thing I would add to pjvr99's response is consider resealing the low pitch stop too. I'd almost bet money the squeal check would fail. -
T56 -A-7B eng oil leakage from diff places.
Lkuest replied to Badiul Alam's topic in C-130 Technical
Here's the source website for service news bulletins. https://www.lockheedmartin.com/en-us/who-we-are/business-areas/aeronautics/sustainment/customer-support-center/service-news-magazine-archive.html -
If the orifice cups are clogged, you will never be able to accurately check servicing, as the pressurized sump may always show good, but at the expense of the atmospheric sump. The atmospheric sump is allegedly the most accurate location, so if it's inaccurate, it will always lie to you. You should check your tech data for how to clean the orifice cups. The only other option is to replace the pitchlock regulator, preferably with one that was recently overhauled to guarantee the cups are clean. One indication the orifice cups are clogged is that, when you check the pressurized sump after 2 minutes, the fluid fills up and overflows. This is due to the pitchlock regulator keeping the fluid pressurized in the system instead of draining the fluid into the barrel like it's supposed to. Be careful of those who tell you only the pressurized sump is required for an accurate fluid check. This comes from the idea that the pressurized sump dipstick actually gives you a quantity, and the atmospheric sump is only a go/no-go. The only thing the pressurized sump dipstick tells you is how much fluid is in the pressurized sump, who's job is to force-feed the pumps sending the fluid out to the valvehousing. The atmospheric sump dipstick tells you how much is in the barrel AND atmospheric sump. If there's nothing on the atmospheric dipstick, you have no idea how much is in the barrel, and that can be dangerous.
- 6 replies
-
- 2
-
-
-
- propeller oil
- propeller service
-
(and 2 more)
Tagged with:
-
It is likely your orifice cups are clogged, preventing proper filling of the barrel assembly, and therefore your atmospheric sump
- 6 replies
-
- 1
-
-
- propeller oil
- propeller service
-
(and 2 more)
Tagged with:
-
T56-15 engine torque increases when bleed consume
Lkuest replied to Ahmer's topic in C-130 Technical
This sounds strange. I'd almost suspect you had a bleed valve stuck open on one of the other engines, or there may be a wiring problem within the anti-ice system that is affecting indication. Does the engine pitch sound like it's roaring to life? Does the aircraft actually yaw a bit in the direction of the increased torque indication? I would also be interested to hear how all 4 engines behave together when all bleeds are open and the wing & empennage are actuated. Please, for clarity, when you say TIT remains the same, can you please specify whether the TIT momentarily moved up/down and corrected, or did the TIT simply not move? Can you verify the wing and empennage valves have proper function. Please clarify how much each indicator is moving when wing and empennage anti-icing is actuated Really, the only reason for torque to significantly increase with a steady TIT is the engine suddenly becomes more efficient by retaining more air within the engine, or the indication is lying.