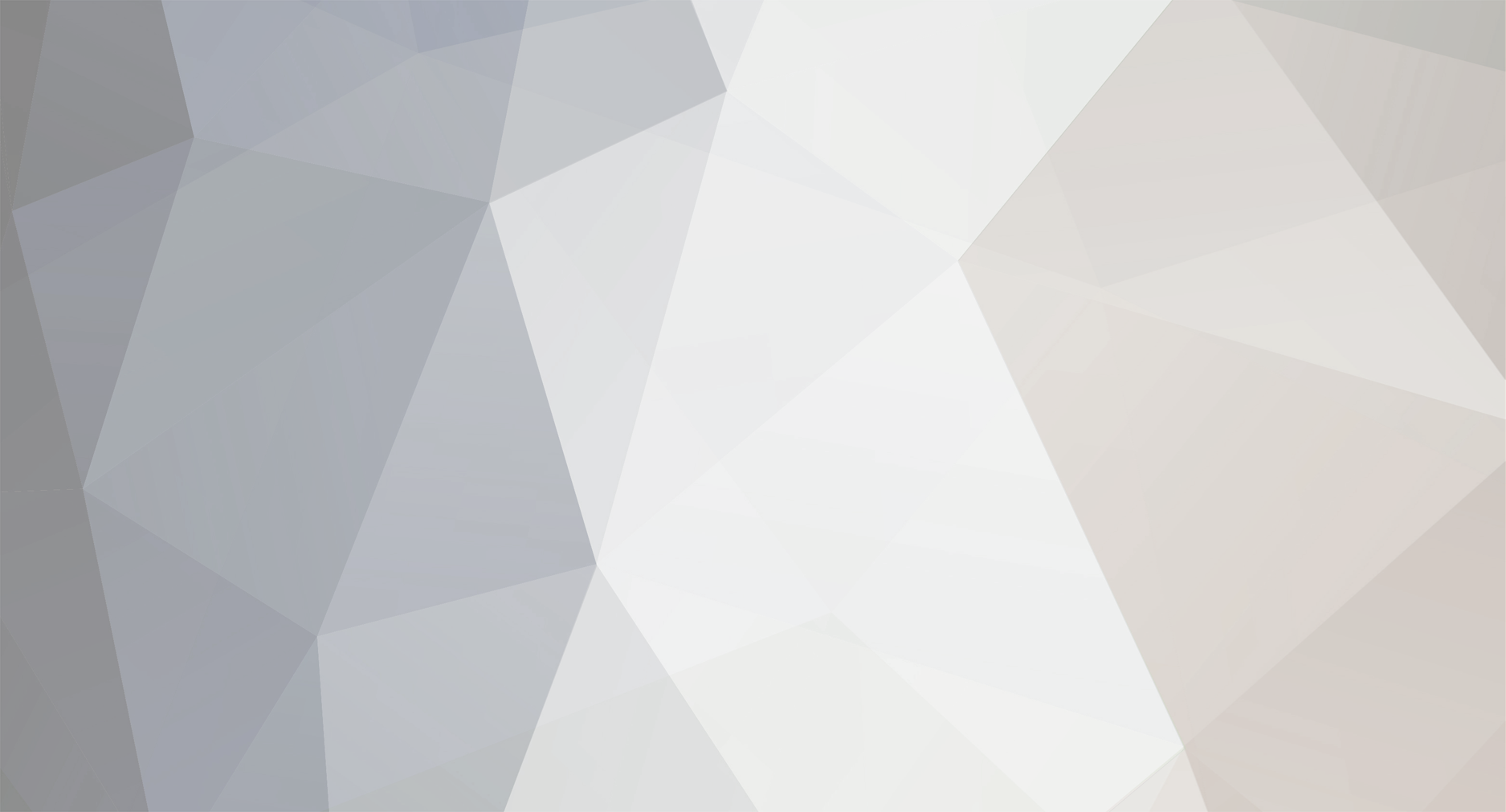
NATOPS1
Members-
Posts
785 -
Joined
-
Last visited
-
Days Won
7
Content Type
Profiles
Forums
Store
Gallery
Downloads
Calendar
C-130 Hercules News
Everything posted by NATOPS1
-
Easy answer... Throttle movement causes the valve housing to schedule speed (rpm) and Blade angle. Once the blade angle has moved the required amount, the valve housing tells the blades to stop moving. Hard answer... Throttle actuation moves the coordinator to change the fuel schedule and move the alpha shaft in the valve housing. On the Alpha shaft is the SPEED SET cam, (below flight idle) it rotates which increases the speeder spring tension disabling the flyweight’s effect on the governor. (Flyweights are used for constant speed operation.) Also on the ALPHA shaft is the BETA SET cam which moves the pilot valve to effect the blade angle change. During the blade angle change the BETA feedback causes the BETA shaft to turn which re-centers the pilot valve and stops blade movement at the selected (throttle) position.
-
The TD Valve is not your issue. Our books have a "desired" (not a limitation) of 780-810 for a NULL start. You have a good NULL start so look at the TD amp settings. Quick check can be made by watching (listening) to the TD valve and place the switch to AUTO, you should hear the motor driving you TD valve to take fuel. If if does check your TD amp Start temp limit (830) the pot on the amp may have been "twisted" too far and gone all the way around. This can cause the TD amp to always think the temp is TOO hot and drive the valve to take fuel...
-
When you turn off the gen you remove the route to illuminate the GEN out light.... Engine not running gen out light would be on no matter the position of the switch. If you turn the switch ON with the engine shutdown you will get the GEN out light... The GCP contains the control componets so if there are loose contacts the desired operation is lost. We teach "reseat" the GCP as a trouble shooting step.
-
http://www.sandiego6.com/news/local/story/Part-of-An-Airshow-Plane-Lands-On-Carmel-Mountain/7h069zhIoEGxhcB1fgGNyA.cspx
-
No "specific" time frame "if the throttles are moved to the reverse range with a movement which is too rapid, it is possible to lose control of the aircraft before a propeller malfunction can be detected." "The movement from the flight range to the reverse range should be made at a reasonable rate which will permit detection of a malfunction, such as failure of the low pitch stop to retract." Also it should be noted that a “Slower†movement can cause the LPS to retract at various times causing uneven aerodynamic loads on the aircraft as each propeller enters the ground range. Remember reversing propellers at speeds of 115 KIAS or above could result in engine flame out.
-
Navy and Marine also have AIC-25 but we have AIC-18 info in the books as well. I think the change was with our "R" models (mid 70's) to 18 and then the "T" model (80's) has the 25. Same system (basic wiring) just different names? More capability (More radios, more wires, different boxes) on the later model so that might be it. Start the APU and use only the ESS AC bus to see if your issue is with the MAIN or LH/RH AC bus. If it is not the ESS (if you have the AC bus tie) tie the main AC bus and see if the issue is there or in the LH/RH AC bus...
-
When I said "too high" I mean above the threshold of the GEN OUT light (say 97 or 80 VAC) not the Overvoltage protection... There is NO under voltage protection (or indication) in the area between 115 V and 95 or 70VAC (depending on model), so if your voltage is between the level to illuminate the BUS (warning) and the level of the GEN OUT (protection) you will have an UNDERVOLTAGE condition on your bus... A) The reason you do not get a GEN OUT light is because when you turn off the gen switch you de-energize the contactor to remove the GEN output from the bus so there is no route for power to illuminate the GEN OUT light. The seamless switching actually takes some time (VERY VERY FAST though) because the contactor must de-energize, removing power then the contactor AUX contacts are made and the second GEN's power is routed to the BUS. If the timing last too long you could see a bus off light but not a GEN out light because you turned it off (The GEN is still working just not used) Start all engines and turn on all generators (not APU) then "downshift" your engines to low speed ground idle and you will be able to see the "switching" take place. (Blinking of lights etc) The Inverter when ON supplies power to the AC INST and Engine Fuel Control Bus which powers you TQ, TIT and FF gages. Low voltage could cause inaccurate readings... C) The ONLY way for the APU contactor to energize is if the APU gen is on speed (FSR) , developing good voltage (GCP), AND the GEN control switch placed in the ON position(route power to the contactor). D) The GCP not in the rack is on of the MAIN causes for GEN issues. One of the first things we teach to do is reset the GCP in the rack.... E) Not sure, will have to look at the schematic... but, the ISOL DC is used for resetting the GEN in the case of loss of volts or the failure of the PMG in the GEN. The internal workings of the GCP use 28VDC from its own internal TR unit so all the GCP relays are directly powered by the GEN output AC voltage, changed into DC and routed as needed. Basically the AC is changed to DC and as long as it is good (above 95 or 70 VAC) it keeps the GLC and PIR energized to keep the Gen "online" and the GEN out light OFF. So if all Engine GENs are ON they should remain ON if that CB is then pulled... Try it and lets us know what happens.....
-
If the Generator is make voltage above 70 or 95 (depending on what system you have installed) you may not have any indication of a malfunction. Low voltage on the ESS AC bus will cause all kinds of issues as long as the freqs stay above 368 or 380 the line contactor will remain energized and supply the ESS AC bus with BAD power. The Voltage is too high for a Gen out light (and switching the load to a good generator) and not low enough to illuminate the bus off indicator. The Inverter being ran all the time is a WHOLE OTHER discussion!!! (bunch of crap! Good idea totaly wrong reason.) The Inverter being in the ON position will prevent some of the issues if it is an ESS AC bus issue. But you would have to have both inverters ON if you had engine instrument failures and ADI warning flags; this does point to an ESS AC bus issue as you stated. You say the gages "roll off" including the RPM? As LKUEST stated if the RPM is moving you have a real problem (LOW ESS AC voltage affecting the syncrophaser) and not just indicators "rolling off". The ESS AC has two sets of wires and CB's ESS AC (9 CB ) and upper main AC (9 CB ) check out your ESS AC Bus Isolation proceedure. With that said I think you need to look at your Gen Output (maybe low) the Gen to Contactor wires (which are monitored by the ground fault transformers) which should take the generator off line (no excitation) and deenergize the line contactor (did not happen but may take a little time to trip). The wires between the gen and the contactor are subjected to wing flex and I think this would be a good place to start. #2 Gen to the K2 relay.... Also the K2 relay may not release the contacts when deenergized ( too allow a good generator to assume the load).
-
All, It is ok to click and respond.. No identification info just simple answers... Rick is one of us....
-
"Lkuest... There is another possiblity, and that's the Coordinator. That component interprets throttle and condition lever inputs and translates them into a single throttle signal input into the valve housing. If something inside is messed up, the prop might think it's in the ground range, or maybe move it towards feather. It might explain everything, but it's a longshot." Not such a long shot in my opinion. If the only thing done was to verify the rigging and you get two OPPOSITE results the input has changed. Your coordinator tells your blade angle where to be (in the ground range) and 1000C prior to crossover sounds like a rich fuel control. Key to this is your "One more point… in both cases crossing the cross-over point had no any corrections..!!!" Did your correction light go out? I would think it would have or you would have added that information.... The overspeed condition i would not expect to see a correction (fuel topping) the first set of numbers 1000C prior to crossover i would expect to see a correction. If the coordinator is bad the system is never told where the throttle is so the fuel control prop and TD system alll have issues. Not so far fetched....
-
Not more weight.... not "bigger" just more expensive!!! 45 milloin to replace the FE... They could have given me half that and I would have stayed!!! Sorry it is a KOOL aircraft...
-
I think they took them off the civilian version.
-
Only spoilers are on the "southern version" NASCAR and all you know... No spoilers, same landing gear...
-
If your AC Inst Eng Fuel Control Inverter is "ON" Stby (DC position) you can "Take the ATM" (Gen off and ATM off) and do a No ext power self contained start. Once the starter is released turn the ATM on and gen to on. As Lkuest stated you are seeing "normal operation".
-
"mechanic80 well the RGB oil pressure is 150 - 250 psi" Well, it depends on the oil pump installed. Some operators still use the 130 to 250 limit. Problem is 130 is good for the old pump but 20 PSI low for the new pump. Hence my question..... The new pump should be installed on most engines. A paper was published about the issue in 99 i think... Basically at 130 there is not enough of a "film" covering the RGB parts and failures result. This paper also addresses the oil pressure flux limit and range.
-
What are your oil pressure limitations? 130-250 or 150-250?
-
Just between you and me... and all the other Herkybird members... 3 bad valve housings... NO WAY!!! one bad sync box I belive..... Throttle anticipation will start the blades moving in the right direction "Prior" to the change in engine speed brought on by throttle movement. Reduction in throttle equals a reduction in blade angle "too slow of a reaction" low RPM and gen out lights. Three BAD valve housings with the SAME issue....?????
-
Place your AC Inst & Engine Fuel Control Inverter to STBY (DC) and see if you have the same issue.
-
"During an engine run the throttles were pulled back kind of fast (from 1077) cnd if throttles are at 1010. "kind of fast" would that be less than 1 sec? cnd (and)? 1077 "and" 1010...right? This intermittently causes the gen out lights (1, 2, and 4) to come on. It never happens to #3 gen, and rarely happens (to 1, 2 or 4) w/ temp datum in null or locked. Ok a few things peak my intrest... 1. Do an engine run and see what your TIT is "before lights out" at crossover... and then see what the correction is after fuel correction lights out.... I would think 1, 2 and 4 fuel controls are lean and you will see an increase in TIT @ cross over. Number three is equal or rich... If so when the throttles are retarded below crossover you "take" fuel away (lean fuel controls) and the engine slows down in addition to the higher blade angle (cant decrease fast enough). Once RPM is below (sensed rpm) 380 or 368 the freq sensitive relay opens and your contactors start to switch, hence the blinking and diming of your lights... Once RPM stabilizes rpm ABOVE 368-380 GEN OUT LIGHTS off and back to normal... As to the reason they (gen out lights) do not illuminate in locked or null is due to the fact you have eliminated the corrected fuel schedule (increase in fuel for a lean fuel control) so when the throttles are retarded below crossover there is no reduction in fuel and thus no reduction in RPM. As far as a T O that states the time frame for throttle movement, read the throttle quadrant for it is written on it "no less than one sec"... I would say this is a "NORMAL" occurance if once the throttles are at Flt Idle all indications return to normal. Normal due to a too rapid of a throttle movement coupled with a lean fuel control.. What I would do is check your fuel controls for a lean condition, set null start temps at 810 (most open "highest fuel flow setting" ) and retard the throttles IAW the placard see what happens.
-
After takeoff pull the IGN control cber for # 2 and leave it pulled (untill you land or need to pull the fire handle OR get the ice detection turns itself ON) See if the ice detection comes on in no ice condition. If it does reset #2 IGN control Cb and pull #3 and leave it pulled (untill you land or need to pull the fire handle) See if the ice detection comes on in no ice condition. You should be able to see which one (2 or 3) is tripping your system. do your engine inlets open when the ice detection turns itself on?
-
Lots of reasons as Bob said "that's the way it works best". A fixed pitch prop will only be truly effecient at ONLY one speed. A fixed pitch prop cannot reverse without changing the direction of rotation, which would be pretty hard to do...so for best performance (aircraft and fuel) a single speed and a varible pitch prop to "absorb" the excess power (as we increase the throttle) A fixed pitch prop cannot compensate for external changes the operator must constantly change the fuel schedule to maintain a selected power setting.
-
Is this the same aircraft as discussed on the above thread? Mechanical or solid state detectors?
-
I would have use the word "thingy" to make your point. Speaking of which I think that was my point. As far as fin stall, the process to get into the condition is immaterial, the effect is the discussion. Wrong input or lack of input will result in the yaw required to negate the vertical stabilizers ability to provide directional control.