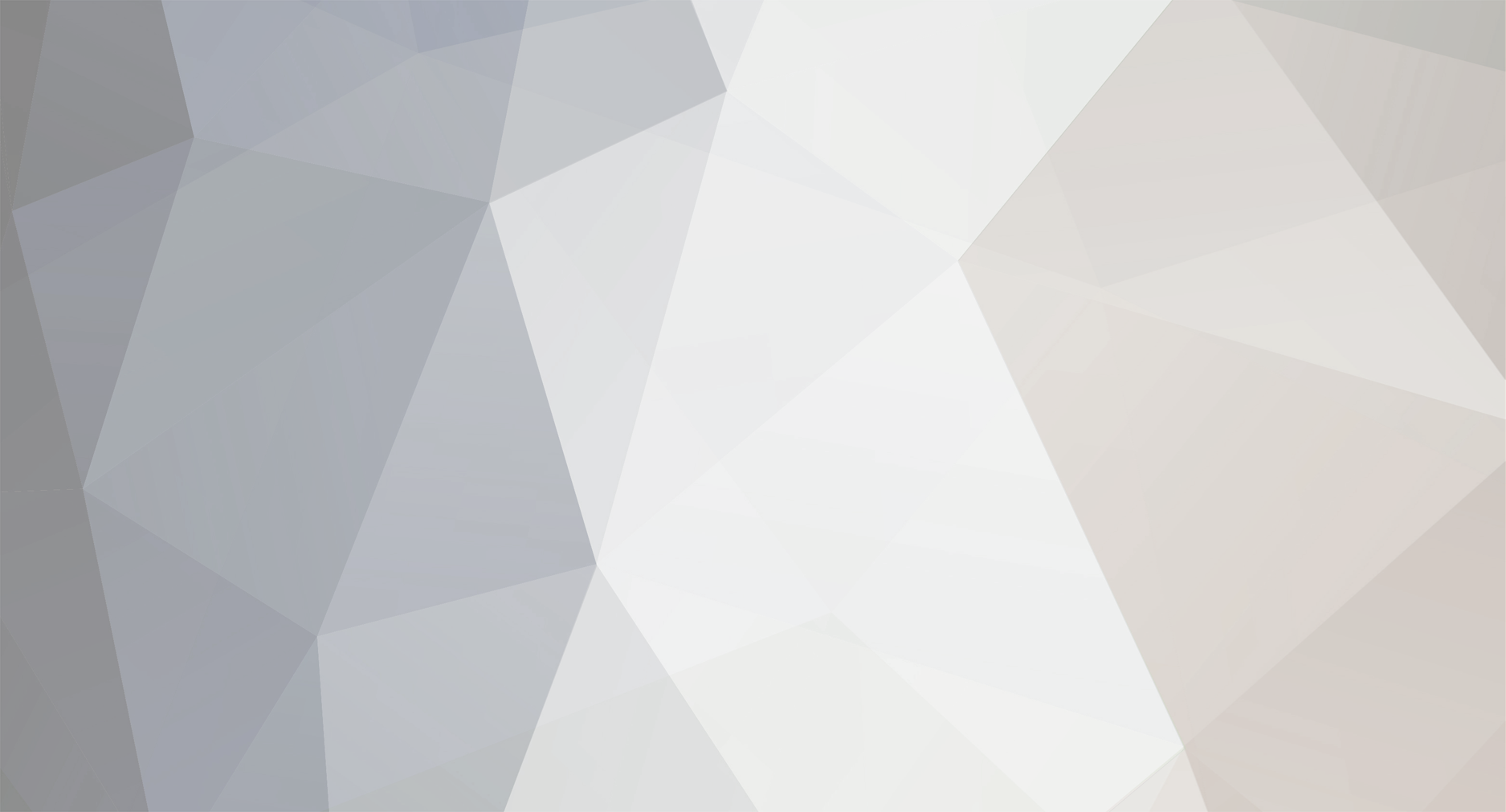
NATOPS1
Members-
Posts
785 -
Joined
-
Last visited
-
Days Won
7
Content Type
Profiles
Forums
Store
Gallery
Downloads
Calendar
C-130 Hercules News
Everything posted by NATOPS1
-
Very strange indeed… So the issue is when shifted to HSGI the torque increases to +-6000"lb, rpm decays to 94%, and TIT increases. You stated there is a blade angle increase and RPM decrease… The TIT increase is to what value? Do you suspect it is due to the speed sensitive valve opening the bleed valves (rag check them) or ? Just to set the stage... Once the engine is stable at HSGI the only way to change blade angle is NTS action or by moving the throttle. (Sounds like you have eliminated NTS as your issue.) To troubleshoot NTS, remove the NST bracket….or select valve and have some one watch the NTS light as you shift to HSGI. Or you could select NTS which will hold the light on and you will see if the linkage is moving. IMO, if the NTS is “sticking†it should drive the prop to feather and the engine would not continue to run. (Which is not your case) Run the engine (Check to see what the valve housing is reading prior to and after), shift to HSGI after the torque increase to 6000 go to ground stop and see what the blade angles do. See if they return to ground idle blade angle (prior to reading). I think they will… You are doing lots of unusual things to find the issue, cannon plus off ect… you may want to (watch the prop input) to see if it changes (moves) when you shift to HSGI. If the engine is “rotating†inside the nacelle due to torque it may be inducing a blade angle change (and fuel schedule) input to your rigging... (engine mounts, QEC disconnect bracket?) That’s why I think they (blade angles) return to normal (LSGI) there is less twisting in the nacelle and you have lost the increase blade angle input so the blades go back to the (throttle commanded) blade angle (and fuel schedule) not the twist induced position. Last effort maybe “pin†the valve housing to see if your issue stops…. Then pin the rigging (work your way out) to find where it is malfunctioning. Just make sure you have the fire handle shutdown system enabled as the feather position will be rendered useless.
-
We never called it "Rudder" fin stall, just Fin stall. (15-20 degrees of yaw) The Evansville crash was the result of fin stall from what I remember. Practice engine out ball out, AC said step on the ball and the wrong rudder input was made. Loss of directional control, the wing is no longer in the relitive wind and stalls.
-
Sorry for the oil stuff, kinda funny though... The Brass screws are a good start. but this should show up at compass cal. Check and make sure the same test equipment is not used on all the affected aircraft. Also there is (used to be?) a "wet compass" fly heading card that is filled out. IE: fly 123 to track 120. A compass heading deviation greater than ±2 degrees of the INS reference heading or a standby compass heading deviation is greater than ±5 degrees of the INS reference heading, the compass needs to be calibrated. I would assume (but you know what they say about that) your deviations are greater than those limits.
-
NOTE to all.... This "oil" response started as a joke... MUST BE THE OIL IN THE GULF... However after a short google search (yes I do own stock)(not really) I found this... http://www.terrapub.co.jp/journals/EPS/pdf/2006/5810/58101401.pdf So maybe I'm right!! Or it might be the polar shift that is going to "change" the world in 2012. Didn't "we" "change" the world in 2008? What aircraft is that on your profile? (and dont say its the Bermuda Triangle!) Have you eliminated it as the cause?
-
Pulsing relay... For the NO ICE LIGHT on within 5 sec of testing #3. It controls the cycling of the 28 VDC that heats up the 90 Sec delay relay, which illuminates your no ice light. You can also check to make sure your interpreters are "cycling" and your diodes are good by checking the voltage on the coil X2 of the pulsing relay. (both systems use the same pulsing relay) Test #3 first and see if the No Ice light does the same thing "illuminates within 5 sec of testing the second detector"
-
The fault is that during taxi the system on light is coming on and will not go off by putting the master switch to reset. (This sounds like the auto reset relay but later on in your post it (auto reset relay) seems to be working) (try taxi with the LH or RH Ice det CBer pulled (or IGN Control CB) to see if you can isolate one of the detector circuits) (mechanical probes activate often for no reason) The light will go off by pushing the light out button. (Normal function, system is still "testing/ detecting ice" just no amber ice light) #2 system is testing ok, (meaning when you go to reset the ice light goes out... auto reset relay good) Try and test 3 first... my guess is it will also test good... but after testing #3 the no ice light comes on after about 5 secs. (This points to the pulsing relay [my guess] or the 90 sec delay relay) (Test 3 first and see if the no ice light comes on within 5 sec on #2) The light is going off at first reset and then staying on no matter how many times i go back to reset. (This is the puzzle)(light is the amber ice light yes?) or the no ice light? If i then try to test either system the on and no ice light come on immediately i put the switch to test. (The 90 sec thermal relay is HOT so the no ice light will illuminate, I think you have a pulsing relay issue stuck on always heating the 90 sec relay or the thermal setting on the 90 sec relay is bad.) Good luck...
-
Just got Cert'ed as an Instructor FE Today
NATOPS1 replied to F106A's topic in C-130 Community Announcements & Promotions
Hey Tiny You out there? F106A was one of the fuses for the APN-59 right? F106 was a B E A utiful airplne... B-58 kicks its arrrs though!! -
Try testing #3 first.... see if you have the same issue. Its a heated relay... 90 sec (right) cant remember the flow. will have to check out the wiring... Heats up to turn on the No Ice light. If its stuck it (no ice relay I think) will be hot and the no ice light will stay on. Wait it cools and you can start over.
-
She looks good Tony! Maybe you could provide the "number" change to BOB info. I know there was a SH**T fit when BOB was changed back to 808.....and then back to BOB... Maybe a picture or two of the names on the bulkheads... You enjoy the snow?
-
1. Friday afternoon 2. Pilots 3. Round of Golf (on Friday afternoon) Agreed to stop golf after 9 holes and 9 BEERS? Thats how WE play.... Airborne at about 1700 hours... On a Friday AFTER 9 BEERS I mean holes. Had me going there for a minute!!!! GOOD INFO NICE PICS
-
http://463rdairliftersassoc.org/names2.htm Might try this guy.... Name: Jim Caudill HomeAddTown: Fairborn State: OH Unit: 773 TAS Location: Dyess AFB Abilene, TX Year: 79 -81 Comments: I trained and flew with Mike Jones and Dean VanDam, both of whom died in C-130 crashes in Turkey (2 years apart) Jim Caudill http://www.google.com/imgres?imgurl=http://www.herkybirds.com/forums/image.php%3Fu%3D161%26dateline%3D1246903989&imgrefurl=http://www.herkybirds.com/forums/showthread.php%3Fp%3D8998&usg=__iYNHnPqD7l9TSRK11k4YVLQTfkM=&h=125&w=97&sz=8&hl=en&start=17&um=1&itbs=1&tbnid=9cEHBGpCPIqlDM:&tbnh=90&tbnw=70&prev=/images%3Fq%3DDean%2BVandam%2Bc-130%2Bcrash%26um%3D1%26hl%3Den%26tbs%3Disch:1 Junior Member Join Date: Nov 2008 Location: Fairborn, Ohio Posts: 2 I was a pilot with the 773 from 1979 to 1981. I knew crew members on both the 1980 crash and the 1982 crash. The 1980 crash occurred on March 14, 1980 and was due to a lightning strike that caused one of the internal fuel tanks in the wing to explode. This aircraft was carrying a number of civilians, incuding a teen "rock & roll" band that was to perform at another base. Our squadrom was on rotation and I had just returned to Mildenhall the week before, after flying a 17day stint in Turkey. Our crew was serving as the admin crew when we dispatched this crew to Turkey just 2 days prior to the crash. The regular nav on this crew (Brian Gomula) was not on board and was substituted by LtCol Benjamin Barnette that had just arrived to be the "on-site" commander for our operations in Turkey. I had flown with most of the crew members including the co-pilot Mike Jones (we were at Little Rock together and at Laughlin when I was going thru UPT) The other crash on April13, 1982 was with a sister squadron, but the A/C was from my squadrom (773). His name was Dean VanDam (we called him Dino or Deano). I flew with, and trained in the sim, with Dino. He was trying to build up enough overseas TDY time to qualify as a remote tour - hence his volunteer status with the other squadron. He was also "best buddies" with Rick Wagner (the A/C of the prior 1980 crash). His crash came within about a month of being 2 years since we lost the other crew. The VanDam crash was due to missing and failed engine mount bolts. There had been an emergency T.O. inspection, requiring a check of the torque, on all engine mount bolts. Apparently some of these inspections had been falsified to get aircraft back in the air. Allegedly, some that knew this, and insisted that the aircraft being deployed on rotation go thru a "second" inspection. Maintenance personell, thinking that the aircraft had already been inspected just a few months prior, "pencil whipped" the second inspection. This aircraft was later determined to have been missing an engine bolt and had another one loose. The failure occurred when number four (starboard outer) engine mount failed, destroyed number three (starboard inner) engine, and the wing broke. Among the passengers of this flight was an entire IG team. FYI the 773rd experienced a couple of other crashes during this time period: In Sept. 1981 another crash occurred in the Nevada desert on a special night mission killing 7 Army soldiers. This was a controlled flight into terrain, during a blackout landing attempt. I know a fair amount of this one from hearsay, but won't share it on this forum. Also, in June 1983 another 773rd C-130 crashed at Nellis Air Force Base during a Red Flag exercise, near Las Vegas, Nev., killing six. -------------------------------------------------------------------------------- Last edited by Jim Caudill; 09-21-2009 at 03:33 PM.
-
From my orginal post 150 IAS is a different "force" at different altitudes. (this should have been "speed" not force) 150IAS at 1K = 152TAS 150IAS at 10K = 174TAS "One simple example of this is the fact that a given airplane at a given weight and configuration will stall (a function of the lift force produced) at the same IAS at 10,000 ft as it will at sea level." Agree, stall speed is a function of gross weight and not affected by altitude due to the fact you use IAS as the stall speed. "(but at very different TAS)" Indicated airspeed is the number of air molecules flowing over the wing... In order to have the same number MOLECULES at various altitudes you must increse the TAS to push enough molecules into the pitot tube at higher altitudes. The wing does not change its angle to expose itself to more air it is fixed and thus needs a certian ammout of airflow to maintain lift.... The prop changes angle, different angle for different altitude same TAS fixed decouple value.
-
"I want to understand why the prop at 10,000ft requires less force (i.e. lower IAS) to generate -6,000pds of torque in order to decouple vs. a higher force at 1,000ft." 150 IAS is a different "force" at different altitudes. 150IAS at 1K = 152TAS 150IAS at 10K = 174TAS "TAS is only "the speed of the aircraft relative to the airmass in which it is flying." " If the TAS is constant (150) the force sensed by the aircraft, prop and wing is constant and therefore a constant decouple setting. The force “PRESSURE†(amount of resistance or maybe drag) the prop “feels†is based on TAS not IAS therefore the prop feels the same amount of "force" at 150TAS but the BLADE ANGLE is higher at higher altitudes. "That doesn't make sense to me because there are less air molecules turning the prop towards -6,000pds the higher you go." Agree, so to maintain the same TAS we must increase the Blade angle to “chop†more molecules. For example 120,000 lb aircraft, standard day, at 30,000' 220TAS, 136IAS, 900TIT, 7300 TQ (high Blade angle) And the SAME 120,000 lb aircraft, standard day, at 10,000' 220TAS, 190IAS, 740TIT, 7200 TQ (lower Blade angle) TAS is the same, the aircraft feels the same pressure, the blade angle is the difference.
-
Understood, that is where we get our ranges. 1100-1400,1600 Max. @ flaps less than 15%. The question is what is the bypass capability of the rudder pressure relief valve? If @ the 1575 PSI full bypass can the valve relieve the increased 1000 PSI from the hyd pump? A dual failure would have to occur to get to this point... Hyd pump pressure regulator fail to limit output to 3000 and the system pressure relief valve failure to limit pressure to 3850....and the indicated pressure increased to 4000. At that point what would the rudder pressure be? Less than 1600 because the relief valve has the capacity to bypass enough or more than 1600?
-
Thanks I have the rated output and the pressure relief valve numbers but Im looking for info on if there were a dual failure of the pump pressure regulator and the system pressure relief valve how much could your rudder by-pass to keep pressure down (at the rudder) The reducer part number is 3A004 Manufacture (98391) I do not have access to milspecs or the like I do have a few pubs numbers that if someone has access and time would like to look up the info..... 03-30ARA-4 and a TO 9H8-15-35-3.. If we could find out what the bypass gpm maybe we can figure out what the pressure increase would be.... I still think it would be minimal and stay within the 14-1600 caution range....
-
Anyone seen an overpressure in the 3850-4000+ range? If so did your rudder boost (if flaps were up) increase but not to the overpressure valve (due to the de-boost)? I do not know the bypass capability of the pressure relief valve for the rudder but if it can bypass enough to limit the 3000 input to 1100 to 1400 output then a increase to the input of 1000 should not make a huge difference. Maybe the increase would be in the 1400 to 1600 caution range…. Any ideas?
-
About the temperature compensating unit in FCU ?
NATOPS1 replied to caps36's topic in C-130 Technical
Temp probe and bellows are filled with alcohol. As the temperature changes the volume changes which changes the length of the bellows and causes movement thus a change in the fuel schedule. The spring ensures the bellow movement is transfered to the output lever -
Do not exceed tow bar limits. The maximum gross weight at which the airplane can be towed is 175,000 pounds. However, at gross weights above 110,000 pounds, exercise extreme caution with respect to surface conditions and rate of acceleration while towing from the nose gear to avoid failing the tow bar shearing mechanism.
-
Not good... Not so much a time limit to quote but the valve is spring loaded closed so as soon as the "pressures" are equal the springs win and closes the valve... After the high pressure bleed air is removed the valve should close rather fast. If it slowly closes you may have a clogged air filter on the actuator side. When clogged it will act as a check valve and resist the spring (not let air in) and cause it to be slow.... the fact that it does close tells me the springs are good and air is slowly refilling the actuator side of the valve its slow due to the clogged vent filter.....clean it and see what happens.
-
I understand what you are saying but at 16% the fuel pumps are turning at the same RPM no matter the time frame to get there. As for the fuel pressure, input pressure say 40PSI will be far less than the fuel pump output pressure and the fuel manifold pressure will be zero until 16%. The system is just waiting on 16% to allow fuel flow. The 50 PSI will be obtained at fairly the same time/rate.... I too hope it is simple and we get the outcome posted...SOON
-
"Another thought: if the starts are being done on the ground, is this engine being started using APU/GTC bleed air, or engine bleed air?" May need to clairify this as I can not make a connection between air source and enrichment other than a slower or faster rise to 16%. In flight there is no air source other than the propeller rotating in the airstream. "And are the tank boost pumps being used, more specifically aux and/or external tanks?" Again the source of fuel should not change the enrichment as the pressure used is downstream of the fuel pump assy. There is a connection with fuel source and the secondary fuel pump pressure light illuminating.
-
OK we need to hear from you... If you start with enrichment, STAY on the ground, shutdown the engine and restart with enrichment does it work? You have stated it is consistant with heated engines... so take out the flight varible and try it staying on the ground.... Another thought would/could/should be wing flex, engine torque flex anything that could "move" a wire just enough to open it and cause your enrichment to be inoperative.....
-
I was a 3rd MAW team member at the Marine Corps Matches (Marksmanship Meet) in 1984 and at the 600 yd line sending rounds down range noticed a Herc slow and "DROP" a Humvee from oh I'd say 2000' NICE streamers instead of chutes and watched it disapear into a HUGE dust BOMB!!! Range was kinda quite for just a second then back to popin some caps!
-
This is what I would look like..... I would still have that SMILE on my face!!!