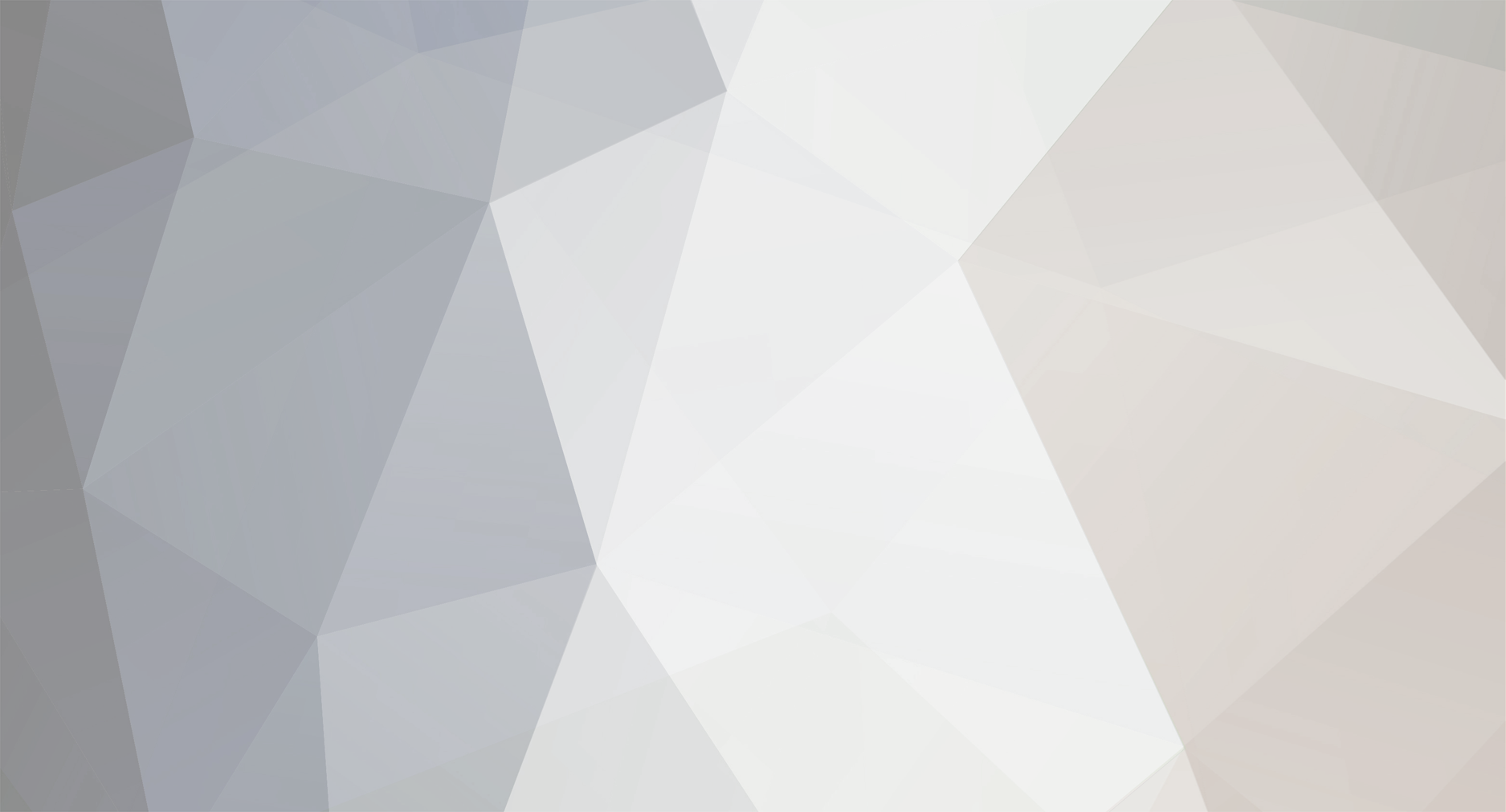
Lkuest
Members-
Posts
315 -
Joined
-
Last visited
-
Days Won
5
Content Type
Profiles
Forums
Store
Gallery
Downloads
Calendar
C-130 Hercules News
Everything posted by Lkuest
-
I could probably get in trouble for saying this, but you've got three other engines. That being said, I've been told by an engineer that when something goes wrong with the airplane, it's not just one thing that goes wrong, lots of things decide to break just then. It all comes down to what your stripes or collars are comfortable with. Just be careful though. Leaky props can possibly cause smoke and fumes in the flight deck, so if you decide to take it, close the bleed valve to that engine.
-
From a maintenance standpoint, I'd say get rid of the current gauges as they are extremely unreliable. I can't tell you how many maintenance problems they cause on a daily basis. We changed three just today on two different aircraft, one had to be cann'd because we ran out on base. Late takeoff for both aircraft; nothing wrong with the engines. I can totally relate to your reluctance to lose your "scan" capability, but I firmly believe the current gauges are pure crap, and I wouldn't mourn their loss. I just won't believe we can't develop a better indication system than we have and still allow the engineer to asses engine operation at a glance. My 2 cents.
-
"So when was the last time you saw a C17 slow down in flight to 98 knots to refuel a helicopter" I hate to throw wood on the fire, but I just saw a C-17 maintain altitude at a Nellis airshow doing about 75 mph. I've seen it do some crazy things just showing off, and I think it's an amazing airplane despite the fact that I've worked 130's all my career and have read a lot of it's history here on this board. I think the point's been made earlier though, they both fill different niche's. The C-130 is a pain to work on, but it just so happens that the C-130 has literally done pretty much everything an airplane can do other than go to space. The C-17 just moves cargo more quickly and efficiently. It's not as glamorous, but it still gets it's job done, very well. I'm sure the C-17 is capable of performing a majority of missions a C-130 has been adapted for, but why ruin the airframes when we already have the purpose-built and more affordable platforms already in place? I just don't think the whole "when was the last time you saw a C-XXX do this" argument holds any water. The C-130 is just at the right place, at the right time, for the right price to pick up all these extraneous missions. Apples and oranges.
-
It's not the oil coolers themselves that have augmentation, all the oil coolers are interchangeable between engines with and without augmentation. It's the engine nacelles themselves that determine whether or not you have augmentation. You may already know this, but from your statement, I was a little confused. As for your question, tinyclark is 100% correct about the inspection reqirements. I just want to add that curled blades in the oil cooler intake are normal, but if you are having problems maintaining oil temperature, in flight or on the ground, and your propeller blade angles are set correctly, curled blades may be causing it. If you don't have oil temperature problems, don't worry about it. Also, oil cooler intakes are a common bird strike area.
-
I talked to an Air Force Tech Rep who seemed pretty convinced the plan was to upgrade all H-2's and above with NP2000 prop, and all H models period with the new Valve Housing. If everything I've heard came true, however, we'd be flying X-models right now (C-130E upgraded to H-model config) and Little Rock Guard would be training with AMP aircraft a year or two ago. I don't think anybody knows concretely what's going to happen because plans in the C-130 world tend to change quite a bit. I do know there is a Wyoming plane that is modded right now, which I had the fortune of seeing the other day, and an LC-130H is modded for trials as well, which you can find pictures of at airliners.net under a search for 83-0492.
-
rpm doesnt estabilize at lsgi in starts whit hot wheather
Lkuest replied to coyote26's topic in C-130 Technical
To troubleshoot this type of problem, these are the recommended steps. 1. Inspect compressor for damage and dirt buildup 2. Borescope turbine for missing, damaged, or eroded blades. 3. Removed the Speed Sensitive Control cover plate and ensure the shaft rotates with the prop 4. Check engine rigging and control cables, ensure propeller blade angle reads no more than 6 degrees in ground idle (when measured by rotating blade angle from reverse to ground idle) 5. Ensure there is no excessive play between the prop control drive bracket and the retaining lug (holds the propeller control steady) 6. Check the NTS gap in both places as well as for cleanliness and freedom of movement 7. Disconnect the Compressor Inlet Pressure line and ensure the line is not clogged (do NOT blow air into the fuel control, only the compressor side) 8. Inspect Speed Sensitive Valve filter for contamination 9. Inspect engine for bleed air leaks 10. Ensure acceleration bleed air valves move freely by alternating between air pressure and vacuum and verifying they open and close. 11. Visually inspect magnetic drain plugs for contamination 12. Inspect Fuel Heater/Strainer filter for contamination (if this is clogged, usually you will see a low fuel pressure light for that engine at higher power settings) 13. Disconnect Fuel Heater/Strainer inlet line and inspect inlet for contamination 14. Inspect Low Pressure Fuel Filter for contamination 15. Inspect main fuel line for evidence of constricting flow 16. Ensure the fuel tank boost pump puts out enough pressure 17. Flow test at least two fuel nozzles for obstructions If you still have problems after all these checks, it is recommended you change the fuel pump. These steps are to troubleshoot a generic power loss, so you may perform the steps you feel are necessary given the circumstances, or only the easy ones followed by a quick runup to see if the problem is fixed. One thought though, if the RPM only stumbles at low speed ground idle, try to perform a Fuel Toppings check. If RPM stumbles there too, you probably have a bad fuel control. Also, don't have a bunch of things stealing air from the bleed air manifold during engine start unless you have at least one engine in HSGI. -
The static feather check is required in the 1C-130H-2-12JG-10-2 work package 12-16-03. Basically, you are required to perform the check every time you do a 15-day prop service check.
-
"I am told that in order to op ck the prop brake, local policy, no one can give me a tech data ref, but local policy is to cage the engine at 180FL. If the propeller rotates backwards it is immediately a write up requiring a flush." The 1C-130E(H)-1 states that the prop brake is designed to hold up to 200 knots, but you may have to slow down to 160 knots to get it to stop. If it stops, you can speed up until it starts rotating again, then slow down, but no faster than 200 knots. If it doesn't stop rotating at 160 knots, stay at 160 knots until landing. The FCF tech data may have an actual ops check for the prop brake, but I just want to point out that the H-1 isn't telling you how to ops check the prop brake, it's only telling you how to react to the circumstances of a propeller rotating backwards. I've only heard of our flight engineers at Little Rock complain about 160 knots rotation. The 1C-130H-2-70FI-00-1-2 states you must ops check the prop brake in flight using T.O. 1C-130B-6CF-1. I've never read it, but I hope it'll point you in the right direction.
-
We had one at Little Rock many years ago that had the tach gen mounted to the Speed Switch. It flew like that for a while until the commander made us change the motor---to clear up the K write-up. I can see one argument though; an engine decouple would be indicated differently, so the flight engineer might have a delayed response trying to figure out what was going on. There might also be a stigma against leaving a defective gearbox in service, even if everything else works.
-
Several sources state the power output of the -16 at around 4910 shp. The J-model engines are rated around 4591 shp to 4637 shp. I haven't read any technical manuals or anything, just pretty much relying on what I find using google. I have heard though that the J-model engine was de-tuned for the airframe and the actual power output may go as high as 6000 shp. I was just going by the rated output for the aircraft. That and the fact we're not allowed to install a -16 fuel control on a -15. Only a -14 fuel control is a suitable sub on H-models.
-
As far as I know, the Fuel Control and Turbine are upgraded from the -15. The -16 puts out nearly as much power as the J-model engine.
-
Interestingly enough, 2358 has some of the lowest flight hours of most of our E's, despite being the first one.
-
NTS stands for Negative Torque Signal. NTS isn't so much a function of engine power as it is a reactionary system to prevent prop overspeed, not to correct engine underspeed. Negative torque means the prop is turning the engine due to excess airflow for the blade angle. There are helical splines in the gearbox that, when the engine is driving the prop, screw together and basically lock in position. When the prop turns the engine, the helical splines un-screw and start separating. This action has no function in the gearbox itself, but the unscrewing action pushes a rod forward that interfaces with the NTS bracket, enabling the actuation of the feather valve, increasing blade angle, preventing the propeller from either making the rpm run away or causing a decouple. The confusion here comes from the low pitch stop. This prevents the propeller from dropping below the pitchlock range in flight. The problem is that some pitchlock regulators are set at 25.5 degrees blade angle, some are set at 24.5 degrees, and the engine fuel control tuning differs from motor to motor. Flight idle, being the lowest power setting, as well as the prop hanging up on the low pitch stop causes the scenerio most likely to create an NTS condition on a single engine putting out the least amount of power, not because engine power is low, but that the airflow instead of the engine is driving the propeller. The power is lower, but the blade angle is low and airflow is going to make the RPM shoot up if it doesn't NTS. Now keep in mind the engine decouples at roughly negative 6000 in-lbs of torque. The reason all of this is important is people need to know A) what causes what they are seeing at flight idle, and an NTS condition can exist at all power settings due to either a maintenance problem, wind gusts, or a nose down attitude. The NTS system requires airflow to function correctly which is why you cannot duplicate in-flight NTS problems on the ground and there is an in-flight NTS check every time there is NTS system maintenance. If you would like to read up on the NTS system, you can check out the 1C-130h-2-70gs-00-1, section II paragraph 2-2.1. Your maintenance CTK should have a copy.
-
I just want to clear up this whole confusion on RPM limitations. Coming out of our maintenance manual, ground idle is 94% to 102%. Because of the low pitch stop and fuel scheduling at flight idle, it is 92.5% to 100.5%. Normal rpm in flight will be 98% to 102%. Of course, the upper and lower rpm limitations allow for an RPM gauge to have 2% RPM error in either direction, which is strange considering an RPM gauge is legally bad with 1% error. As measured with an Accurate Tachometer, ground idle is 96.3%-99.1%. Flight idle is 94.4%-98.3%. Normally in flight, RPM will be 99.8%-100.2% under no throttle movement. If you know your RPM indicator is dead on, RPM should never drop below 94% at any time because that is when the acceleration bleed valve are scheduled to open. As for the manifold pressure, between ground idle and takeoff, it is possible for bleed air pressure to change from 70psi to up to 110psi on ground runs with only a minor RPM increase. This is measured with all bleed air operated equipment turned off and one engine outputting air-- not exactly something you'd check in flight, but with jet engines, bleed air equals power and temperature. With all 4 engines at flight idle, some engines pull more torque than others. The engines that pull less torque will tend to NTS more often on decent. Because of the nature of the NTS system, the props will increase blade angle, then decrease back to the low pitch stop again when the NTS condition is gone. This can create an RPM and torque flux situation which probably won't make an engine go below 94%, but you'll wonder what's going on with it. As for why your squadron rules differ from the -1 guidance, who knows. These planes have been around for a long time and it makes sense to change the way we do business based on experience. It would just be nice if whoever thought it up would change the manuals if it's that important. Otherwise it's just an opinion.
-
"Just herd of one (recent).... happened during static power check prior to takeoff. Found a bolt on the coordinator worn that allowed the pulleys to rotate freely..... " I'm not one to play the blame game too hastily, but I would speculate that the extended time between HCS's and ISO's have something to do with this. I think it's about 260 or 280 days between each instead of the usual 180. I remember doing an ISO extension inspection to keep some planes flying until we could get around to flying'em to ISO. The most important part of that inspection was checking the integrity of the rigging, something that gets checked through thoroughly during an HSC or ISO. I think the purpose for this extended time between HSC's and ISO's was to lessen the load on manpower and "do more with less." It just seems to me we're doing less with less, which makes for a lower quality product while still refusing to acknowledge a large difficiency in manpower. Just my 2 cents.
-
I've seen this problem before on a transient -130 from Dobbins several years ago. The plane came to Little Rock for a modification. Engine shop got dispatched to ops check an anti-ice valve and I noticed all 4 props looked like they were at flight idle. I moved all of the throttles to reverse, hit air start, moved the throttles to ground idle and hit air start again. One of the props stayed at reverse. I moved the throttle all over the place with the aux pump running, but it wouldn't move unless I feathered it. I left the throttle in flight idle and hit air start and the prop went straight to reverse. I checked all the rigging up to the valve housing and everything was fine. We changed the valve housing and everything was perfect. The valve housing was overhauled. What was found inside it was a retaining pin for I believe was the shuttle valve had become dislodged when I took the prop to reverse and made the shuttle valve hang up, causing fluid to be ported directly to the decrease pitch side of the dome, regardless of alpha or beta shaft inputs. Feathering operation bypasses that valve, so it all makes sense. As for the retaining pin, the valve is supposed to be safetywired now instead of using the failure-prone retaining pin to avoid just this situation. I'm not saying that's what your cause is. I guess my point is that anything is possible inside the valve housing, most things just highly improbable. I've also had a prop go full reverse on me during an engine run before. We changed the valve housing and everything was perfect again. Nothing notable was found on the valve housing rebuild that time though. It just got all new seals, thoroughly tested and kicked back out into the system.
-
"But in actuality they are saying is it’s allowed a TOTAL of 10psi, IN LIMITS of 50 to 60 PSI. " In TO 1C-130H-2-71jg-00-1 pg 1-11 note 1 clearly states: "Under clearly stabilized conditions, allowable fluxuation is +-10 psi (20 psi total travel) for power section and +-20 psi (40psi total travel) for reduction gear." I don't agree with it, but it's in black and white.
-
My interpretation is that the Gearbox oil pressure will not go outside the limitations for any reason as long as the engine is at operating temperature and at 100%. I don't care what the mean of the flux is, it should not drop below 150 at all. It does seem to be open to interpretation solely because the engine oil pressure flux is clearly allowed to be outside normal limitations. I wouldn't fly on it, and I'm a maintainer. Besides, I'm kind of lazy. I'd rather fix the flux than change an engine;)
-
"If there is anything specific in the MX books (Especially the 1C-130A-6 and work cards) that you feel needs to be fixed/tweaked, let me know." You might already be working this, but it never hurts to be redundant. Get rid of the Standby filter requirement in the HSC work cards. If we are going to be doing them every 90-days, it doesn't make sense to have them as part of multiple scheduled inspections.
-
Correct me if I\'m wrong, but I believe the prop starts fluxing at about three quarts low, hence the two quart limit.
-
Not working properly? It\'s allowed to be 100 deg rich. How rich was it?
-
Wow, apparently the \"front\" landing gear now has brakes installed. Interesting powerpoint.
-
I suppose you could use either the 4 or 8-bladed, but the navy has equipped the T56-a-427 with the NP2000 on their E-2C+ aircraft. Both propellers have been equipped on their C-2\'s with the T56-a-425.
-
If I had a guess I\'d say the proposed -100 was most likely the Air Force version of the -427 as it was under development in the early 80\'s. Also, the AE2100 has shp figures closer to the -15 than they are to the -427. Just a guess.
-
You can search Allison T56 in Wikipedia to clear any confusion as to the different T56 variants. I haven\'t heard of the -21 variant, but if there is one, it is probably for the Air Force. The Navy uses even-numbered designations with the exception of the T56-a-425 and -427 variants. The Air Force usually designates it\'s T56\'s with odd numbers.