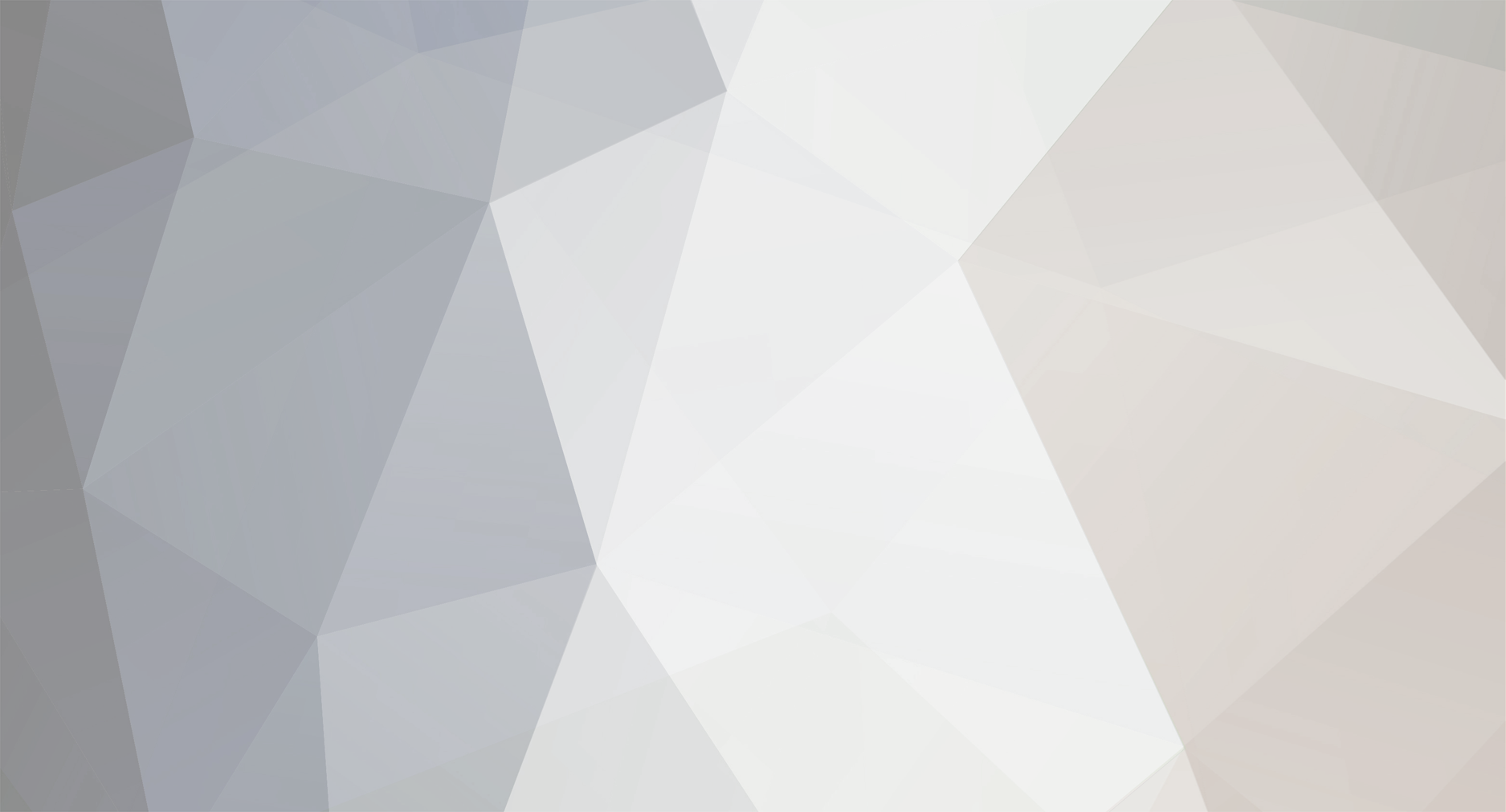
Lkuest
Members-
Posts
315 -
Joined
-
Last visited
-
Days Won
5
Content Type
Profiles
Forums
Store
Gallery
Downloads
Calendar
C-130 Hercules News
Everything posted by Lkuest
-
If this were a US Air Force plane, they'd have intake plugs in by now.
-
There was an Italian C-130J crash back in Nov 2009. I would like to know if anybody knows the back story on that. If it's crew error, than that's unfortunate, but not what I'm looking for. I just think that the first and only major C-130J crash might dig up some pertinent information concerning the safety of the aircraft design. It bothers me that I can't find anything on the internet about the cause even over 2 years later.
-
A question came up about the Stationary Ratcheting Ring, which is one of the rings installed over the Pitchlock Regulator. The job of the ratcheting ring is to prevent the propeller from decreasing pitch only during a pitchlock condition. The propeller can increase pitch, but not decrease pitch. The other job it has is to provide an alignment pin to help align the pitchlock control cam. The pitchlock control cam prevents pitchlock operation above 55 deg and below 25 deg. My question is this: Since the alignment pin on the stationary ratcheting ring is only there for a reference point to correctly "index" the pitchlock control cam to the correct blade angles, is it exactly necessary to have the alignment pin installed on the ratcheting ring, or can it be removed and still allow the propeller to remain operational? I know it is physically possible to still function correctly, as the barrel assembly prevents a correctly indexed pitchlock control cam from rotating in the absense of an alignment pin on the stationary ratcheting ring. I have been brought up through Tech School and T56 journeyman training to believe this alignment pin is optional. My problem is that I cannot find Tech Data which specifically states that it may be missing. I have already searched the 61JG-10-1, 3H1-18-2, and 3H1-18-3. Does anyone in the Herc community have any knowledge of the appropriate Air Force/Lockheed/Rolls Royce tech data that says I may use a stationary ratcheting ring with the alignment pin removed?
-
So theoretically, if the engine were to magically put out a torque of 29850, the exiter teeth would line up with the next set of teeth, and the torque indicator would read 0. I'm not adding anything to the arguement, just thinking aloud. With my keyboard.
-
As a fellow instructor, my answer would be "Who Cares". What's important is how the torquemeter measures torque, not how many teeth it uses to do it. If he wants an answer, you could probably get away with making something up that sounds good. Something that sounds like this: "The power source for the torque indicator operates at 400 hertz. At 13820 RPM, the signal at the pickup pulses at a frequency of 9213 Hertz, over 50 times that of the indicator. At that rate, the signal to the analog indicator would appear fluid, making torque indication smooth instead of jumpy. If the frequencies were matched (a single tooth), misalignment oscillations would cause an indicated fluctuation, much like how the props cause varying beating noises at the same RPM without the synchrophaser(assuming you are on an aircraft where your T56 wasn't upside down.)" The gap is standard for any electromagnetic pulse. Your pulse generator has one (assuming your prop has one on a P3), but there is a gap because if the tooth (magnet) touched the electro magnet, friction would wear them out. If they are a few feet apart, the signal strength would not be enough to generate a pulse. There is a specific gap so that the magnet and electro magnets do not touch, but they are still close enough together to send a meaningful signal. If they don't like those answers, just tell them it's magic and to quit sniffing paint after work.
-
From the rumblings I've been hearing, they still look to modernize the H-model fleet with new and affordable instrumentation, just not the AMP. Looks like AMP took so long to develop, it ballooned itself way beyond the scope of what it was originally intended to do. As long as we get rid of the crap analog engine indicators, I don't care what the flight deck ends up looking like. Not my problem. Upgrading the prop to NP2000, now that I can agree would be awesome.
-
It doesn't make any sense to retire the H2's. I was thinking they'd just swap'em into H1 spots. Either that or the H2's have less time left on them than the H1's that are getting new wing boxes. Maybe the wing life is the driver behind the retirement since they already paid to upgrade some of the oldest H's. When the WC-130H's came through Little Rock in the mid-2000's, they only had 7000-9000 hours on them, and they all had the beefed up wings, so it kind of makes sense to keep them in service from a wing life standpoint, but makes no sense in a parts-support standpoint unless you modernize them. Hopefully, the WC's have been modded with dual rails, otherwise they'll be useless to PRANG.
-
With all the re-wiring that needs to be done, I would think it would take a few months to do the AMP, even with a parts kit. When the E models were getting modded with the sync rewire, it took about a month just for that, and that's not taking into account when the civilians would sign off on the wiring ops checks and we'd find problems on the first engine run due to some crossed pins. It might make more sense to do it at depot, but even the depot cycle is in a state of possible changes. They're talking about eliminating ISO and just going to depot every 18 months for a different area of the aircraft each time. With the way they're retiring H's, I'm wondering if AMP is even worth it at all. It might be better to go all the way-J to have a smaller supply footprint and just sell the H's. Other countries already have glass-cockpit solutions they could mod with themselves, and we wouldn't have to worry about our H's not being able to fly through euro airspace. I just wish the U.S. C-130 world wasn't so complicated and uncertain. If we kept up on modernizing E's and H's like we intended to in the 80's and 90's, it might have been of questionable merit to convert to J's in the first place, and probably much cheaper to operate the fleet than with the mess of constant changes and uncertainty we've been putting up with over the past decade.
-
You could develop your own checklist derived from the TO. The 2J-T56-101CL-1 is an official TO, so you have to go through the official channels to make sure it's ok for export. You pretty much have to get the Department of the Air Force's permission to do so. I'm guessing a diplomatic ambassador might be able to swing something? Otherwise, nobody can legally help you.
-
That's ok. We don't need more reliable and capable aircraft. Being able to fly through European airspace is overrated anyway. High-tech flight decks and reliable technology on an airplane are for wussy's.
-
I was thinking along the same line, but they get power from two different sources. The A/C Instrument and Engine Fuel Control inverter recieves power from the Essential D/C bus in flight, unless they have it switched to the Essential A/C power position, while the prop anti-icing receives power from the RH A/C bus. Unless there is a grounding issue, the only thing the two systems could possibly have in common are cannon plugs. Is the problem there in Null? Switch the invertor to the other position and see if it duplicates. You said you "Were having an issue". Does that mean it was already fixed, or just not duplicating anymore?
-
He's asking his invisible friend for a hydraulic leak so he doesn't have to fly.
-
5 years is the magic number for following the Depot cycle, unless they started converting to the new high-tempo cycle they've been talking about. It might also have the beefed-up wing boxes that would last the rest of the flight-hours necessary to allow the H fleet to make the C-130J conversion. If they project the H-fleet will not last until J's come on-line, it would make sense to add another one or two to the fleet to reduce fleet attrition. The J line keeps getting backed up too. I can find a few reasons to use it.
-
The only thing you could do is change the oil cooler thermostat, but tinyclark is correct. Technically, as long as the oil temp remains within limits, there is no reason to assume there is anything "wrong" with the motor. I've run into this situation a few times, and signed them off every time.
-
I know both aircraft retired out of the 62nd at Little Rock. 7860 had an early retirement. It sat for several years with wing cracks so large you could see them from the ground looking up. There was a long debate as to if it was worth repairing wing cracks so severe. I dropped the inboard engines as an A1C so the cracks could be evaluated and repaired. Later, the center wing box retirement hours became more stringent, so we decided to leave the wings alone and just fly it out to the boneyard. I installed the engines as a SSgt, and it retired within a month after that. I know 7860 had a special mod that put two extra HF wires on top of the plane, totalling four. I never saw the extra two installed, just the attachment points on top of the wings. I was told it was for a special Vietnam communication mission. I don't remember much about 7799, just that I worked it sproadically, so it must have been a decent flier. We went through so many aircraft on their way to retirement that it's hard to keep all the tails straight. Especially when we had 7799, 7879, 7899, 7767, 7877, etc.. 7860 was memorable though. It sat on the ramp for years with only 2 engines, and once had to cannibalize oil filters off of it to fix another airplane. After we put it back together, it took a solid week to get all the engines started. On the first successful engine run, we got a fire light indication. Apparently, it took a while for the plane to wake up.
-
An easy thing to do would be to shove a borescope into the left and right hand bleed collectors and inspect all of the 5th and 10th bleed valves all the way around. If you have one stuck in the closed position, that could easily cause your problem. So could indication problems between the thermocouples and the flight deck indicator. The engine is obviously getting enough air since the engine winds up in 45 seconds. Unless fuel is being bypassed through the fuel enrichment valve, all other fuel causes should have been eliminated by now through changing all the components, including the TD system with starting in Null and changing the TD Valve. At this point, you might as well flow test the fuel nozzles and check that the thermocouples haven't been burned up. Do all 4 engines read the same TIT after the aircraft has been shut down for 12 hours or more?
-
;)
-
Try P/N P5010 Accutach Model 9660, P/N 3402875-1 Lockheed Martin Tachometer, or P/N H391T-56-1 Howell Tachometer.
-
My only reason I believe in treating this as an RPM flux is that the problem moves around to all 4 engines, and often times the RPM indicators can be too stiff to follow a 1000 in-lb torque flux. The only real way to isolate whether RPM is truly fluxing with Torque or not is either with an Accutach or checking Freq's coming off the generators. Of course, if the RPM is indeed Rock Solid on the Freq Meter and/or Accutach (I understand it cannot be duplicated on the ground), it would most likely be a power issue somewhere that connects all 4 indicators together. If the Generator frequency is fluctuating with Torque afterall, it could be anything in the Synchrophaser system, including power source and Constant Voltage Transformer. In case it helps someone, the CVT was added via TCTO 1C-130-1309. It would also be pulse generator wiring on a selected master prop, or a Tach Generator sending errant signals. It could be lots of things. Just another idea, you might trigger the radios during your ground run, as well as activate all the avionics used in flight and operate the engines at power for as long as the aircrew does when they get this problem. I've seen a lot of other outstanding ideas come out here, lots of great experience is on the table. ec130, please let us know what you find. It could help someone else down the line.
-
Treat it as an RPM flux and think Synchrophaser system since it is more than one engine involved. Also, make sure all 4 engine mechanical RPM's are within .20% of 100%. If you're on an EC-130, you might have electrical shielding problems around your Sync, but I'm just grabbing at straws. If you're US Air Force, you probably don't have problems with clogged filters or dirty fluid.
-
The coordinator potentiometer starts kicking out resistance values at 60 degrees. They just don't come into play until crossover.
-
Sorry Steve. I realize I posted a lot of the same information you posted, but I didn't mean to. I started my reply before yours, but I didn't submit until after you did. I agree with you 100% and had a couple of other thoughts.
-
There isn't much information here that we can use as many things can cause this problem. The temperature indication system is not very reliable. Is Fuel Flow and Torque the same as the others at the lower TIT, or is Fuel Flow and Torque higher than the other three at the same TIT? After you let the aircraft set for 12 hours or more, does your bad engine TIT indicator read lower than the other three engines? Is the crossover TIT low? Do you get a cold start in Auto only? All of these things can point to a bad Temp Indicator. Swap indicator with another that you know is good to verify. When you installed a new TD Amp, did you use a TD Amp Test Set to check calibration? If not, you may have a bad co-ordinator causing the TD amp to read a low "desired" TIT. There is a way to check the co-ordinator with a multimeter. What TIT does your TD Valve break lock check break? If it breaks at the lower TIT, your indicator and TD Amp are not reading the same thing, and your problem is in the indication system somewhere, such as thermocouples, thermocouple harnesses, T-block, Y-lead, or most likely the Temperature Indicator. Does your temp controlling check function properly? If not, you could have a stuck TD Valve or a bad J3 lead (going from the amp to the valve). The TD Amp test set can also be connected to the firewall thermocouple c/p with an adapter cable to test all the wing wiring and indicator. You just dial in a temperature, say 971, and the indicator has to read within 6 degrees of that temperature. If your maximum TIT is about 830 to 850, you could have a bad 94% switch in the Speed Sensitive Control. Some things that can aid us in helping you further troubleshoot this problem: Did you swap with a known good indicator? Did you perform a TD Amp Test Set? How low is the TIT at the wall? How is your rich/lean check? Cold start in auto only? What are the other three engine Torques and Fuel Flows at Takeoff?
-
Steve is 100% correct. Out of the three times I've seen this problem, all of them were caused by a failed engine relay box. You may also have a failed 94% switch in the speed sensitive control. You don't even need to perform an engine run to ops check this function of the new relay box. Just slave a new relay box in, and advance the throttle with the engine not running. If it still has the problem, short out pins F and D on the speed sensitive control and try again. If shorting out pins F and D on the speed sensitive control fixes the problem, the speed sensitive control is bad. Something for everybody to keep in mind for troubleshooting strange temp controlling light issues without running engines, you can fool the engine into going to temp controlling mode by simply disconnecting the speed sensitive control cannon plug, and the light should go out and come on with throttle movement. It is a very useful tool for strange temp controlling problems, or the fuel correction light just not coming on or not going out when it's supposed to (light receptical issues).
-
I believe YJ refers to the tailflash. He's talking about the H1's that are stationed there.