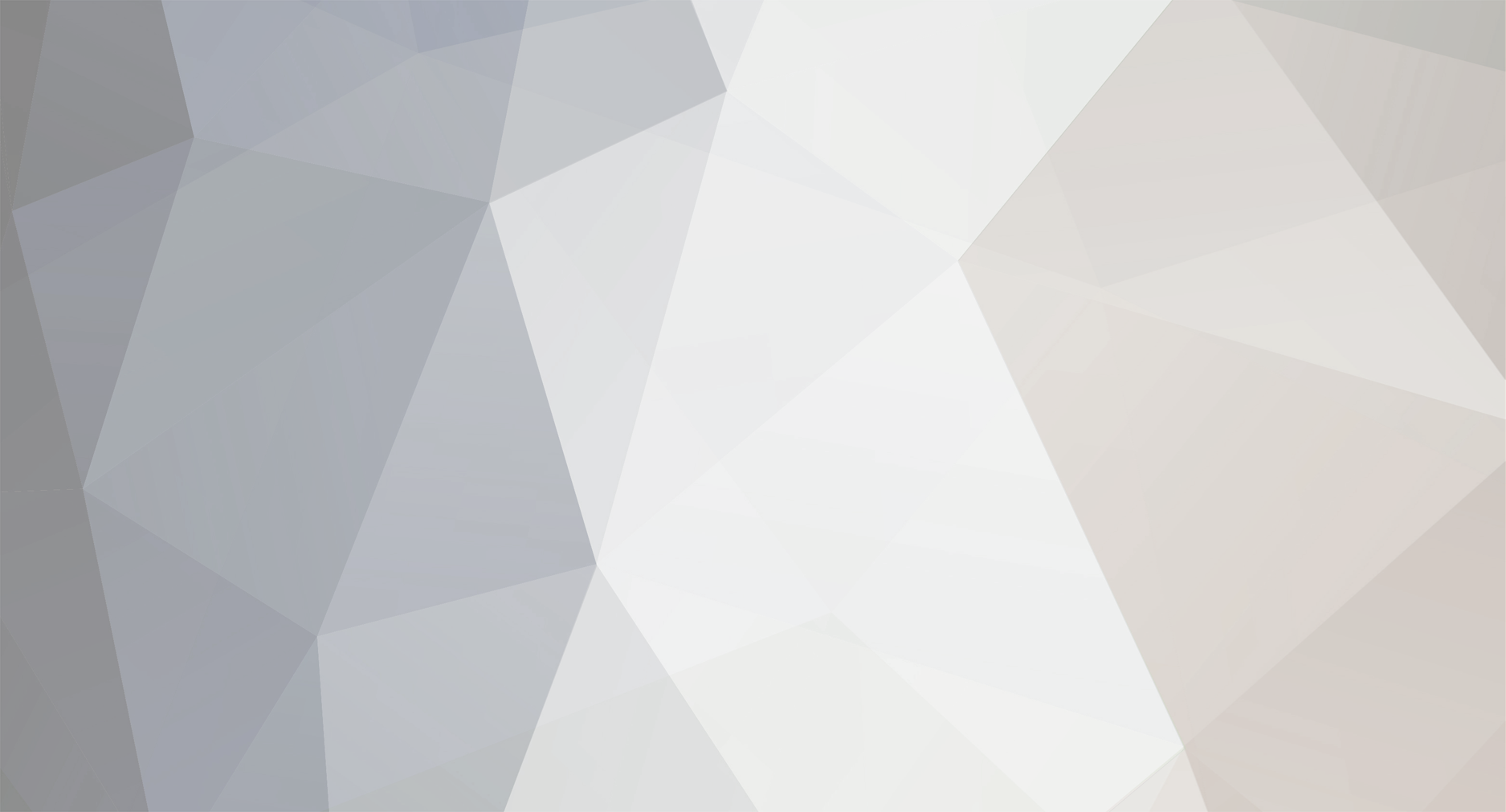
NATOPS1
Members-
Posts
785 -
Joined
-
Last visited
-
Days Won
7
Content Type
Profiles
Forums
Store
Gallery
Downloads
Calendar
C-130 Hercules News
Everything posted by NATOPS1
-
This is out of the Lockheed training manual not a TO...
-
I have heard of one entire blade departing (falling off) it seperated at the hub. The aircraft was on the ground when this happened so not so bad but the blade landed about half a mile from the aircraft.... To shear the segment gears on only one blade is pretty rare I would think.
-
This should be all of the thread, #1 sharif101 engine downshifting fire on dash 7b engine #3 engine propeller brake locked then we try to unlock but failed.we gave apprx 10 us gal hot oil inside the RGB for prop brake release but failed to release.then RGB change & engine fitted.during Ground run found oil flashing from bleed valve ,drain mast also white smoke from tailpipe.we attempt 2nd start found no white smoke but during power reduce from takeoff to below x-over at that time flame out with poping sound after 2-3 second interval it happen several time at that time i shutdown engine manually.during flame out fuel flow increase suddenly.other parameters normal.TD sys calibrate & TD valve changed again ground run but problem remain _____________________________________________________________________________________ Lkuest When you retard the throttle, does the RPM drop with the throttle? If so, this situation possibly indicates a pitchlocked propeller and requires an investigation. Someone possibly forgot to install, or damaged the pitchlock regulator seals when the propeller got swapped over to the new RGB. Also consider Foreign Object damage to the compressor. Check 5th and 10th compressor blades. Borescope turbine for damage? NTS Gap too small when pulling the pump housing towards you? What is the engine efficiency? _____________________________________________________________________________________ pjvr99 I suspect the engine 'popping' noise is a result of flooding of the compressor during the initial attempt to release the prop brake. If the forward drain plug was not removed from the RGB, the oil would be forced down the T/M shaft into the power section. This would account for oil from the bleed valves and drain mast, and masses of smoke from the tail pipe. As the bleed valve system gets air from the diffuser, we may assume that some of the oil in the compressor got into the speed valve, and is sticking part-open or made sensitive to throttle-back movement, and bleed valves are popping open. _____________________________________________________________________________________ #1 sharif101 all throttle position FF,TIT,RPM,TRQ normal but only throttle back to just below Xover then flame out & sound produced 2-3 second interval but when TD null then no flame out.TD ams test check 2 times found good,cordinator check ok,thermocuple,harness,5th & 10th stage bleed valve,turbine check found good.now what can i do?pls anybody help _____________________________________________________________________________________ tenten Dash 7 or 101 make the task difficult to analyse, but as you mentioned on the last post with TD null the engine is behaving good, if so then your target is the TD system only. But if in NULL and below x-over some engine parameters are abnormal then the target is more than TD only; it can be acceleration bleed air valves issue as PJ already mentioned. Sticky valves resisting to be fully close at low power causing the engine to bug down especially with TD in operation. ("popping sound" is a clear indication of the cycling of the bleed acceleration valves.) -------------------------------------------------------------------------------- NATOPS1 You say it works in Null so maybe a rich lean check on your fuel control. (NO correction at crossover in NULL) Popping noise may be the engine trying to maint ignition but the air fuel ratio is not good. What is the "correction" to the TIT at crossover? A large increase as you enter temp controlling above crossover means a large decrease in TIT as you move below crossover. Check the filter between the 14th stage and the SSV. If oil is/was in the compressor it may have clogged the filter just enough to reduce the air flow to the SSV. -------------------------------------------------------------------------------- Lkuest When you checked the coordinator, did you check both the 65 and 66 degree switches for breaking contact above 65/66 as well as getting contact back above 65/66? I would also slave a Relay Box in and see what happens. I'm thinking it's possible that the TD system stays in Temp Controlling mode even below the useful range of the coordinator potentiometer, causing the amp to go to full take. The popping could then be caused by the engine dropping below 94%. Don't forget the "Flag" check. Upspeed the engine, then put a rag secured to a seat rod up in the left and right bleed collectors and see if the rag whips around, indicating an open bleed air valve. -------------------------------------------------------------------------------- pjvr99 As a side-note, I have a direct-reading gauge hooked up to the bleed valves during all runs on the cell. I had an engine surging intermittently, mostly during throttle back, but all throttle settings, and sometimes even at stabilized throttle setting. Eventually, during man-on-stand, I heard a puffing sound, and put my hand in front of the speed valve. Installing the gauge showed a momentary drop of up to 30psi, thereby opening the bleed valves. Since then I have found that a difference of more than 10 -15psi between CDP and speed valve pressure is enough to momentarily pop the 10the stage valves during some throttle movements Lquest has asked a good question on the rich/lean, and the cross-over correction -------------------------------------------------------------------------------- sharif101 yes, i checked coordinator both 65&66 degree switch.relay box replace new one.now problem shifted today given ground run 2 times.TD null 3times check but 1 time flame out.last time when TD auto and throtle back to flight idle TIT 720 degree then flame out with sound at that time FF increase 500pph,TIT above 900 degree & RPM 93%.i think bleed valve open since RPM below 93%.is it FCU problem?ssv filter check ok.pitch lock regulator replace new one.Xover TIT 775 degree. can i change acceleration bleed valve? -------------------------------------------------------------------------------- tenten I understand from the last last post that even in null the engine is flamed out; and that the RPM dropping to 93% just before the flame out. To me once the RPM dropped to 93% and bleed valves opened it is normal to see what you have seen. Based on that, I see no benefit of changing the acceleration bleed air valves. It seems to me that the main issue is RPM dropping once power retarded; then the puzzle need to be answered; Way at flight idle the RPM dropping below the threshold of keeping the acceleration bleed air valves closed (94%)? Is it a fuel Issue (FCU lean) (blocked fuel nozzles) or a valve housing issue, or the low pitch stop setting is high accompanied with less fuel? And I believe that the answer can be obtained from your engine instrument if you read and compare them with the symmetrical carefully. One thought: Use the credit of the null orifice and let more fuel to go and see what will happen while engine bleed air valve in closed position. -------------------------------------------------------------------------------- NATOPS1 Tenten has made a great recommendation. Adjust your TD valve null start temp UP to 810 (780-810 not a limit) maybe even 820? just make sure it is less than 830... Check your blade angle when it is on the LPS. --------------------------------------------------------------------------------
-
Tenten has made a great recomendation. Adjust your TD valve null start temp UP to 810 (780-810 not a limit) maybe even 820? just make sure it is less than 830... Check your blade angle when it is on the LPS.
-
You say it works in Null so maybe a rich lean check on your fuel control. (NO correction at crossover in NULL) Popping noise may be the engine trying to maint ignition but the air fuel ratio is not good. What is the "correction" to the TIT at crossover? A large increase as you enter temp controlling above crossover means a large decrease in TIT as you move below crossover. Check the filter between the 14th stage and the SSV. If oil is/was in the compressor it may have clogged the filter just enough to reduce the air flow to the SSV.
-
Anytime! Glad to try and help... FYI, The PMG tells the VR to send excitation voltage to the GEN which is routed through the GCR inside the GCP so there are a couple of connections that can cause this. You may have solved the problem as any loose contact from the PMG to the VR or from the VR to the GCP or the GCP to the Gen could be your problem.
-
Check the coax connections for your Antennas. I would start at the RT. If you have a TDR (Time Domain Reflectometer) that graphs "shoot" and graph the Coax cables to the antennas on a good aircraft and then shoot and compare your "bad" aircraft. You will be able to see the length of the cable as well as any "changes" in the resistance in the cable (think signal loss) along the cable. The antennas may be "open" or "shorted" on the graph (can't remember). I have not "shot" a cable in over 15 years but it works!
-
Your generator (PMG) is most likly bad. the PMG (Permanent Magnet Generator) inside the generator, upon start should tell your VR to send start up excitation voltage to the "excitation generator" which starts to increase the "main generator" output. Resetting sends aircraft DC to “excite” the generator. I would swap the VR out with a know good one (you have four others on the aircraft) and see what happens. If it remains I would change the Generator when the aircraft goes into ISO or Phase or whatever you call your inspections or it fails…
-
hercmylove, I would fly without gages (don’t need no stinking gages...or is it gauges???) long before I would just reset the CB. Explosions are explosions no matter what the location of the aircraft! I would say to your people that "resetting a CB" is NOT maintenance and they run the risk of BLOWING the WING OFF!!! If they insist or continue this practice maybe it’s time to walk away before they rest it! You only get so many "that was stupid" passes in this life and to let fools use yours up is not cool! As far as flying with bad gages as long as you have a fuel flow meter for each engine you should be able to fly normal profiles (might increase you min fuel limit) we are only required to have 2 gages. (1 and 3) or (2 and 4) or (1 and 2) or (3 and 4) but even with less a fuel chart and operation proceedures should allow for near normal operations. Continuously scan your aileron trim and disconnect your autopilot on the top of each hour to check wing balance and you should have no problems. If you only have main tank fuel I would say you can safely fly 4-5 hours. and have approx 10,000 total fuel remaining. Aux would extend that time by 2-2.5 hours.
-
What is your torque doing? Seems like a large fuel flow drop for only 20 degrees...
-
Failure or malfunction of any fuel quantity indicator is indicative of a possible failure that would, with the proper sequence of events, allow the introduction of high voltage electrical power into that associated fuel tank. In the event that a fuel quantity indicator goes to OFF SCALE HIGH or OFF SCALE LOW pull the associated fuel quantity indicator circuit breaker. That's what you need?
-
My quistions... =when having such warning,is there any change on the engine indications(FF,TQ,TIT)? Maybe, maybe not. depends on malfunction. A fire warning is not a positive "FIRE" on the engine. The indication is the result of a rapid change (increase) in temperature around the sensor loop. If you shutdown the engine then isolate the wing you should have removed any additional bleed air source of heat and the warning should go out (no time limit to go out) so make a visual check befor using the second bottle. NO fire protection for the remainder of the flight will be FUN... If you have a true fire there will be smoke... Make sure your bleed air valves close when you isolate the wing. check for a torque increase on the engine when you close the valve.
-
There are lots of WARNINGS about introduction of high voltage into a fuel tank, as well as damage to the indicators if disconected/connected with power on the aircraft. In flight, failure or malfunction of any fuel quantity indicator is indicative of a possible failure that would, with the proper sequence of events, allow the introduction of high voltage electrical power into that associated fuel tank. In the event that a fuel quantity indicator goes to OFF SCALE HIGH or OFF SCALE LOW pull the associated fuel quantity indicator circuit breaker. Do a full visual check of wiring and then continuity checks prior to resetting the CB.
-
Flying with a bad prop low oil light float switch...
NATOPS1 replied to ShadoFE's topic in C-130 Technical
Removing the light bulb will not make the master go out. Remove the light bulb and remove the diode (from the bad prop) that isolates/seperates the master from the other individual lights. This will extinguish the master so if you get a prop low oil condition the master will illuminate and the "other" individual light. If you remove the cannon plug you will disable the 86 degree switch.... -
Sad day indeed. Thoughts and prayers to and for the loved ones.
-
I agree with the technical data solenoid (A) and ( and the "reason" but would you try low press air to see if the engine will rotate? I have had a start control valve that would not open with high pressure air so, I would...
-
Guess not.... I think I lost a few line of my orginal post... If you try to start an engine and get NO rotation (STOP START) "We" "check" and make sure we have power (Start valve open light will press to test) and we have air to the starter (we see a defelction in the air pressure gauge (gage) when the regulator valve is placed to override) But... we have a NOTE that tells us to reduce the bleed air manifold press to less than 45 PSI and attempt a restart... The question is...... Some say we reduce the manifold air pressure PSI to less than 45 to allow the engine bleed air regulator valve to "open" and some say it is so the starter control valve can open (against less pressure)... Does anyone have any thoughts on this subject? Does anyone have any references on the subject? I have had an engine /prop that would not rotate unless I used low press air and I'm sure it was due to the starter control valve not opening aginist "higher" air pressure (it was #1 eng)... Reduce the air press engine rotates and starts...
-
Vr would be the easy answer... Vcef is a planning tool (how much (minimum) runway do I need) BRAKE RELEASE-----------------CEFS(SPEED BASED ON CFL)-----------------------TO or STOP (ON CFL; NOT RA) Vr is a "Real world" Limit. (I have extra runway for my conditions so I can go faster and still stop) BRAKE RELEASE-----------------VR(SPEED BASED ON RA)-----------------------------STOP All the extra is a bunch of ________... IMHO
-
Some say we reduce the manifold air pressure PSI to less than 45 to allow the engine bleed air regulator valve to "open" (thinks the manifold air pressure is less than 50 PSI) And some say it is so the starter control valve can open (against less pressure)... I make no claim to either. I know our book says if you get NO propeller rotation to reduce the air pressure to less than 45 PSI and try to restart... I know the manifold pressure will be less than "50 PSI" but I also know the starter control valve is subjected to "less" air pressure.... Thoughts? References????
-
You have no idea which pump is bad. If you lower the gear or flaps the pressure may drop but it will return to the high pressure value once movement stops. You will also put the high pressure through all the "other" lines and fittings of the system you operate... You cruise engine shutdown so you can "stop" the pump. If you turn the pump "off" you isolate it (pump) from the pressure relief valve that may be keeping the pressure under control. Then ALL the pressure will be inside you engine/drybay land may rutpure a line. Before you CES your first engine inventory your engine conditions. Which one are you going to CES first? Can you start it back up? Have you any failures? SSC? Ign Control CB out?
-
Seems like AF only terms, we do not use them. We have rec (RA more than CFL) min rec RA equal to CFL and not rec (RA less than CFL). I think the terms are used as a decision making process to determine/define who (qualificaton level) can takeoff from any given field/op condition.
-
IT IS SOMETHING ABOUT THE SPEEDS THEY USE.???? Yes... Balanced is based on Vcef
-
Our version of these charts are a little different but... Question is how much longer 500' or 2000' or more? You only know if your true CFL is more than runway avalible if you compare BAL to UNBAL as the charted distance varies. Say takeoff factor is 1.0 Gross Weight 150,000 All chart correction inputs equal... Your avalible Runway is 4400' Balanced distance required 4000' Unbalanced distance required 4500' (0 degree temp dev chart input) After you compare you use the "Longest runway requirement" so your aircraft can perform to the Critical Field Length definition. Takeoff or stop in runway avalible. Critical field length is the... (minimum) runway distance required to accelerate on all engines, experience an engine failure, and then to either continue the take-off or stop. Balanced field length When the distance required to continue the take-off is equal to the distance required to stop. This is ok as you can takeoff or stop on the runway you have avalible. Unbalanced field length This would not be ok because you cannot stop.
-
100% best performance (for TOLD calculations) 98% not as good, a reduction in engine performance equals a reduction in overall aircraft performance. 95% Minimum allowed Check with your maintenance department. They should have the performance number for each engine in the logbooks. Then you can use the lowest of the engines to calculate you’re TOLD. Your (actual) aircraft performance will be better so you have a "margin of safety" if you calculate that way. You can check the performance of the engines when you set takeoff power. (calculate torque for the TIT you will use for takeoff power setting) not a true performance "number" but a valid check of the actual engine performance under your current conditions.