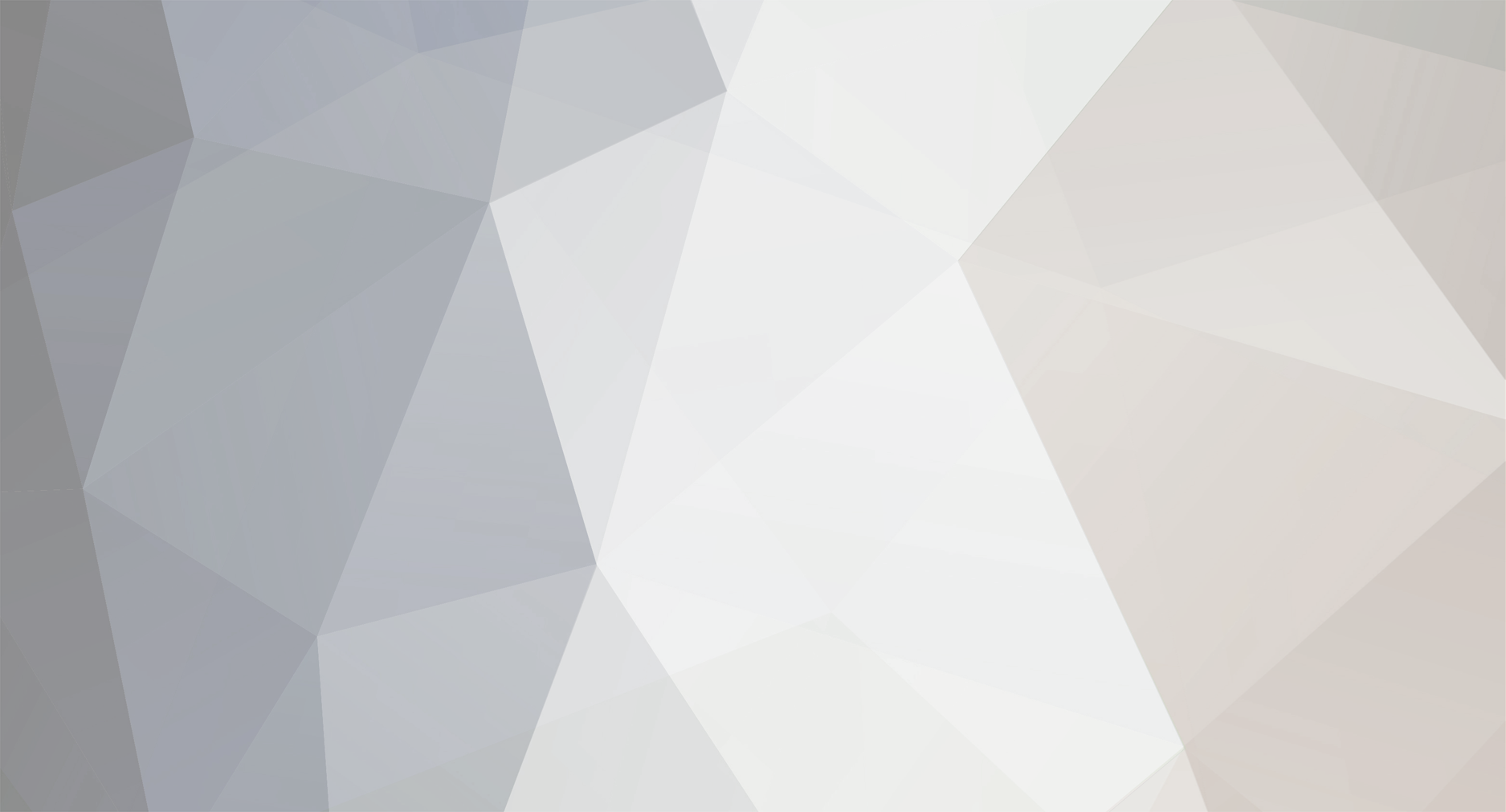
NATOPS1
Members-
Posts
785 -
Joined
-
Last visited
-
Days Won
7
Content Type
Profiles
Forums
Store
Gallery
Downloads
Calendar
C-130 Hercules News
Everything posted by NATOPS1
-
May sound silly but have you checked the friction lock on the throttles?
-
Change your "Oil Tank Pressurizing valve" located on the oil tank. This valve "closes" as the aircraft climbs to pressurize the oil tank at higher altitudes (10-18,000') which pushes the oil out of the tank to the pumps. If it fails to close the pressure is too low inside the tank and indicated pressures will drop as the aircraft increases altitude. The oil pressure will return as the aircraft descends so your crews can start the engine back up at a lower altitude and not land three engine.
-
Anyone with the units operating these Props? I have a few questions/ items of interest I would like to address...
-
Agree the correction does not have a specific limit but the FCU has a rich/lean limit as PJVR99 stated; 880 to 825 is good to go.
-
Manual override is used to manually operate (turn on or off) the unit in case of electrical control is lost. The flt station is in the pressurized hull, the cargo AC is external. The electrical control for the two units is a different set up as well.
-
After reading you post about the Flt station AC manual control I determined you have an early model aircraft and therefore gave you a partial answer to your question about the "jet pump". On the model aircraft you are inquiring about the jet pump we are discussing IS designed to increase airflow through the heat exchanger. The induced flow through the intake ensures a larger volume of air is drawn through the heat exchanger.
-
The "Manual feather valve" is mechanically actuated with the condition lever in feather. The valve ports fluid to drive the propeller "TOWARDS" feather but as the prop's rotation slows the pump output drops and the prop may not get all the way to feather. You can check operation on the ground by running the engine and pulling the Aux feather motor CBs and placing the condition lever to feather. Blade angle will increase towards feather and may get all the way to 92.5. 60 or 70 degrees while not fully feathered will reduce drag. Your maintenance books should have a description of this operation. ***EDIT*** In addition to pulling the Aux feather motor CBs you need to pull the Feather and Airstart CB to fully check the manual feather valve. Pulling the CBs listed is for maintenance check ONLY. You should NEVER do this in flight.
-
The jet pump works in conjunction with the water separator to induce the flow of water (by air movement- IE the jet pump) from the separator to the heat exchanger. It ensures the removed water comes into contact the heat exchanger and increase thermal transfer. it is not just for increased "airflow".
-
Place TD to Null does it stop flux? Pitchlock the prop and see if it stops flux.
-
Final flights are always hard to hear of; had many informative and some humorous interactions with Bob over the years and like others here full of knowledge and willing to share. Fair winds and following seas my brother... Forever in the clouds; RIP
-
OK I think you may have two different issues. I would start with the mechanical side and verify all blade angles (low pitch stop, ground idle, reverse, feather, flight idle) and NTS gaps (anti rotation (drive) bracket, gearbox to NTS bracket and NTS bracket to valve housing) change or disassemble and lubricate the NTS bracket. Make sure to rotate the valve housing assembly to check the drive bracket gap. Question: the aircraft flew with out accurate torque indications and NTS was checked? I caution because there is a maximum negative tq limitation during the check which I'm sure you are aware of but just wanted to make sure...
-
When you say 27540 is from back shop are you stating the torquemeter stamped value? If so use it as the reference instead of 29850 and set your torque "range" around it.I am not aware of a minimum stamped value for the torquementer..
-
I take it the reservoir is filling up and over flowing then dripping out?
-
FYI, UNCLASSIFIED ROUTINE R 161447Z AUG 17 FM SECNAV WASHINGTON DC TO ALNAV INFO SECNAV WASHINGTON DC CNO WASHINGTON DC CMC WASHINGTON DC BT UNCLAS ALNAV 054/17 MSGID/GENADMIN/SECNAV WASHINGTON DC/-/AUG// SUBJ/DISPLAY OF THE NATIONAL FLAG AT HALF-STAFF// REF/A/DOC/DON/1990// REF/B/INST/DoD/1005.06/17JUL15// NARR/REF A IS THE UNITED STATES NAVY REGULATIONS. REF B IS THE DEPARTMENT OF DEFENSE INSTRUCTION FOR THE DISPLAY OF THE NATIONAL FLAG AT HALF STAFF.// RMKS/1. In accordance with references (a) and (b), the National Flag of the United States shall be flown at half-staff from sunrise on Sunday, 27 August 2017 through sunset on Thursday, 31 August 2017 on all ships and stations of the Department of the Navy in honor of the 16 Service Members who lost their lives on board the KC-130 aircraft on 10 July 2017. 2. Released by the Honorable Richard V. Spencer, Secretary of the Navy.// BT #0001 NNNN UNCLASSIFIED//
-
Can anyone provide a link to or copy of the accident report for 68-10951 that crashed on 10 Dec 78 Any other data (reports/ accounts) on Throttle Cable Failures would be greatly appreciated as well. Especially interested in any reports of Reverse blade angle encountered in flight and or blade separation. Thank You!!
-
As PJH said there are no "Engine" or RGB components that cause pitchlock. There are certain parts that are reinstalled when changing a prop assembly (regulator, prop rings, prop nut etc) and the reason for my post. Have you changed the Prop retaining nut? PJ called it the "brass barrel nut" if it is allowing pressure to bypass or leak you could get pitchlock. There have been many of theses dropped over the years.
-
Hearing loss and rigging in ears experience with VA
NATOPS1 replied to BRlang's topic in VA Benefits
Well youdid the right thing and was more concerned about your passengers/ crew. Did you have to see the Doc post incident? Maybe there is a record of the visit which could help substantiate your claim. There is an incident report for sure maybe get that as well and provide all the pieces for the review. Good luck!! -
Only other thing I can think of to help isolate your issue is to start only the left or right engines or use the hyd pump switches or boost shutoff switches to "turn offf" one of the hyd systems and measure the force "feel" required to move each flight control. You may find a difference in required force, maybe test a few other aircraft to get a benchmark but feel is not too scientific... maybe a fish scale etc to get specific readings...
-
With one-two hours of flight and the GEN fails on approach check the loadmeter and see how high it is with the Aux Hyd pump on. If your crew turns the Aux Hyd pump on before landing it may be running at a very high load run longer than during preflight/engine start as those only take a few min where approach will take an extended period of time.
-
Not sure I have ever heard of a problem like this where all flight control surfaces are affected and a "Feel" issue is noted as a discrepancy. There have been instances where a single viscus damper has caused a feel issue but to have all surfaces involved may be more the feel"er" than the feel itself. If there were extremely cold conditions present each of the dampers may have been affected increasing the viscosity of the fluid which could have increase a sense of more force required "feel". The fluid being mixed should not be an issue as they are fully compatible. will be interested to see what transpires with this one... Good luck.
-
Agree with 99... What is the crew calling a "Inflight TD check"?
-
Whole prop as in BOTH the Pitchlock regulator and PUMP housing were changed? Also please note pitchlock is not a result of the "hydraulic fluid loss" it is due to the loss of "PRESSURE" that holds the springs compressed on the pitch changing mechanism which is caused by a loss of fluid. The reason I say this is because if your pump is not making pressure then you will pitchlock without a loss of fluid.
-
Based on your post I would guess you have gone through the entire list of drag corrections for different aircraft configurations. The baseline model the testing was conducted on plus any mods (+20) seems low to me but I do not know your configuration. Check the paint type on the test aircraft, there have been lots of "changes" with not many updates to the performance manual so being off by 50 doesent seem too far fetched.