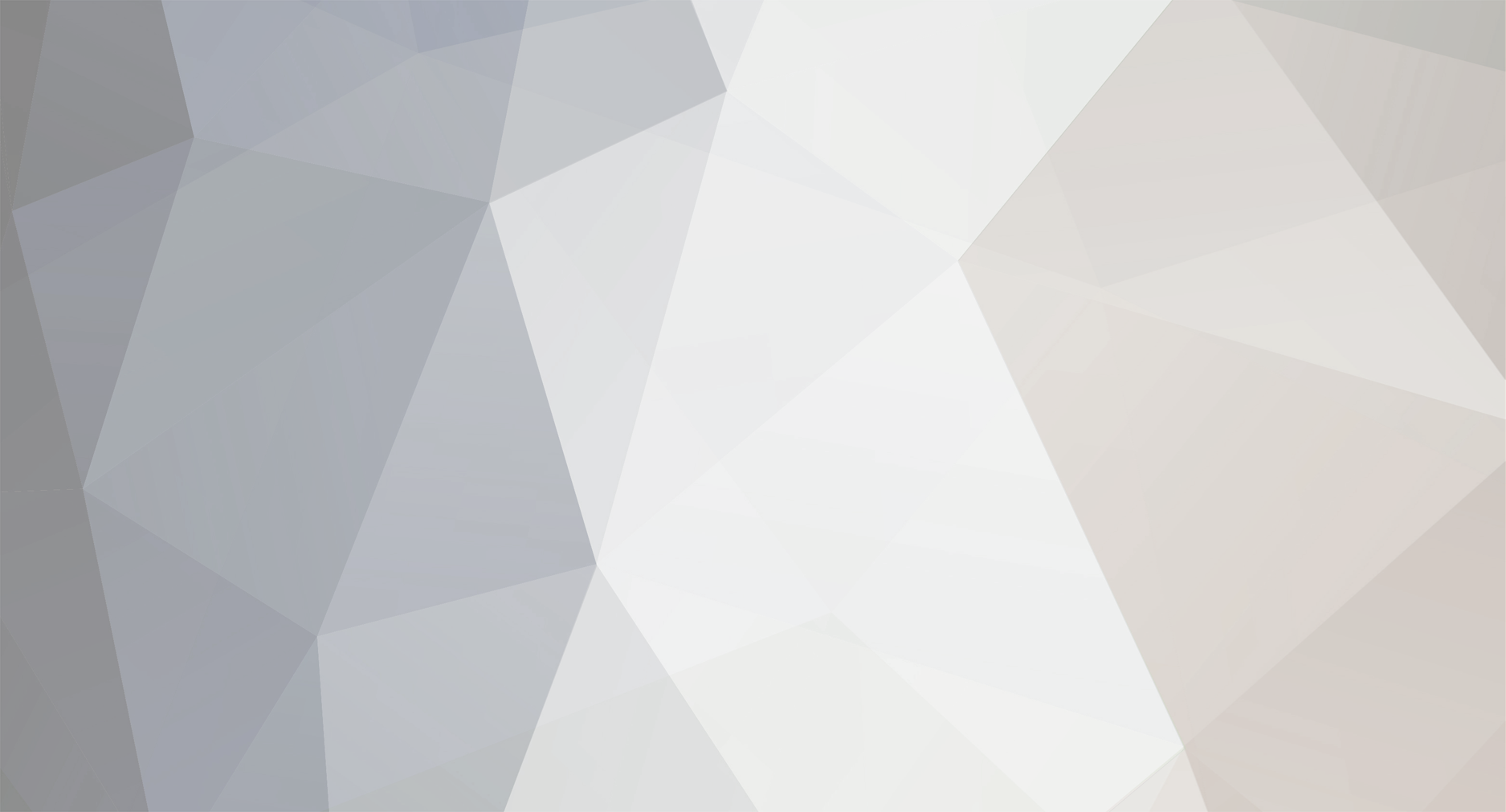
Lkuest
Members-
Posts
315 -
Joined
-
Last visited
-
Days Won
5
Content Type
Profiles
Forums
Store
Gallery
Downloads
Calendar
C-130 Hercules News
Everything posted by Lkuest
-
We have a low power checklist for just such an occasion. I'm not going to explain each step as I assume you'd know how to perform each check. If you don't, let us know. 1. Perform a thorough Intake and Exhaust inspection. 2. Inspect 5th and 10th stage compressor blades for curling and buildup, and valves for freedom of movement, valve lines for leaks 3. Check propeller and engine rigging 4. Visually inspect thermocouples, then test with high current or resistance tester 5. Check TD control system with a "Y" box 6. Perform visual and continuity check on thermocouple harness, "T" block, and Y-lead 7. Check or change speed valve filter 8. Inspect torquemeter pickup, verify correct number of shims. 9. Apply bleed air and inspect for leaks around anti-ice valves and ducts 10. Perform Man-on-the-stand run for air leaks and flag check. Operate engine 11. Perform torquemeter calibration 12. Perform LSGI anti-ice check 13. Perform 850 TIT anti-ice check 14. Check engine performance (generator off, engine hydro off, bleed air off, air temp with hand held thermometer, compare with other motors.) 15. Check Compressor Discharge Pressure. 16. If low power persists, perform comp wash and recheck (already done) If the LSGI anti-ice check passes, I usually get some power back by resealing the left and right inlet anti-ice valves anyway. The internal seals just don't last.
-
The way I read the story, it sounds like the engine was windmilling after shutdown. Almost sounds like NTS wasn't set. I'm told the propeller will fly itself apart at 110% rpm. Then again, it should have been on it's way to feather by then and unable to windmill. A lot about that situation sounds bad.
-
I'd start with the NTS gap and the gap in the torque retainer lug on the back of the pump housing.
-
Does the problem happen only after you reduce power, or every time you advance the throtle above ground idle, but below crossover? In the first case, I'm thinking TD valve if the problem goes away in null, or Fuel Control if the problem stays in null. If it happens ever time you advance the throttle above ground idle, I'm thinking Valve Housing. These are just my opinion, but I'd need to know what all the other instruments are doing to have a better opinion.
-
Calibrate the torque indicator. It should be about 650-700in-lbs (roughly) in low speed ground idle with no load and the lowest power setting with the throttle. You should also check the torquemeter pickup for proper shimming and condition. It could be bleed air related. A Man-On-The-Stand run could help with that. It could be an anti-icing system malfunction. Operate engine at LSGI, close the bleed air valve to the engine, cycle inlet anti-ice a few times. If you get a 24 degree difference, everything is good. If you consistently get below 24 degrees, you could have a malfunctioning engine anti-icing system, and troubleshoot that. An alternate method is to advance power up to 850 degrees with bleed air valve closed and TD switch in auto, then actuate engine inlet anti-icing. You should see between 900 and 1400 in-lbs change. Any less, and your system could be malfunctioning. In either case, it wouldn't hurt to reseal the engine inlet anti-ice valves mounted on the Air Inlet Housing. The seals inside love to shrivel up. You may also have a TIT indication malfunction. The easiest way to tell is to perform all the TD system checks, such as start TIT, Crossover TIT (800-840TIT for -15 engines), Max TIT(Load the engine up with a bleed air load to ramp the TIT up), and TD Valve Brake Lock check (1084-1090 TIT). If all of these checks are skewed, then the TD amp is either mis-tuned or there is a difference between what the TIT indicator is seeing and what the TD Amp is seeing. In this case, look at the entire TIT indication system and TD system. You could have a combination of these, as there are many places for air to leak on the motor, and the TD system isn't extrememly reliable. The worst case scenerio is that you have a bad turbine or bad compressor. Borescope the turbine. Your engine could also be worn. The life of a typical turbine is about 5,000 hours (someone correct me if I'm wrong), and the compressor I believe is about 6,000 hours. Pull the 5th and 10th bleed valves and check the compressor blades for curling or build-up. Check speed valve filter for clogging. Check Compressor Discharge Pressure, and then check performance between motors with the bleed air valves closed. We've had a similar problem caused by a high-efficiency compressor pulling low power because it was running all the bleed air systems single-handedly. If you have bleed air regulator valves, you shouldn't have that problem. Please let us know what you find:)
-
I got a chance to work on that U.A.E. aircraft back in 2007. I looked really hard to see if I could see any signs that a prop blade went through, but I couldn't tell anything had ever happened to it. Whoever put it back together did an extremely good job.
-
Because of it's job and complexity, that's what I would change first, but if that doesn't fix it, it's plenty of other things that could cause this. It also depends. If you have a very pronounced flux in everything, about 4000 in/lbs torque, and the bleed air pressure coming off the motor is going all over the place, that's a speed valve issue, but that's so obvious, you wouldn't exactly have to pitchlock the prop to isolate that one. I suppose it's physically possible for some other fuel system component to cause this, but you are right, every time we've had a flux, slight or pronounced, after following all the steps and pitchlocking, it's been a fuel control issue.
-
That's entirely up to you, but that perfect storm scenerio can happen. Every base has a different setup. At Little Rock, our supply lines are set up to recieve only one type of generator, so we've never had the situation where we've had to change the voltage regulator. On a recent engine change, our E&E actually found our new engine had a different branded generator. They said if we ran the engine, the generator would have burned up. They searched high and low for the voltage regulator and came to the conclusion that we couldn't get it at our base quickly because we just don't stock it. They changed the generator on the brand new motor just to speed up serviceability of the aircraft. Our aircraft did not have GCU's, and checking the generator is in our engine change tech data, so if we didn't check compatibility, we'd be standing tall the next day. Hope this helps someone.
-
I've been taught only one way to troubleshoot this problem with engines running, and it usually isolates 90% of all fluxes to a specific system. It helps if, before you start, double check propeller servicing in case the low oil level transmitter (float switch) is failed and not showing a low oil condition. 1. Verify Freq's 2. Swap Indicators 3. Temp Datum Switches to null (If flux goes away, investigate TD system) 4. Mech/Gov switches to Mechanical (if flux goes away, check Synchrophasing system, including valve housing speed bias assy and throttle potentiometer) 5. Condition lever air start (if flux goes away, suspect dome seals, clogged standby filter, leaky low pitch stop/pitchlock regulator, or other internal propeller leakage) 6. Perform pitchlock check (if flux goes away, propeller is at fault, if flux stays, the fuel control or other wet fuel system component is most likely at fault). If anybody else has ideas, let's here them. Please let us know what you find so we can add it to the pool of knowledge and pass it around.
-
Same reason someone chalked the tires on an A-10 that performed a wheels-up landing. If there's a regulation, and you have no explicit reason not to follow it, why not? If you can find a picture of that, it's pretty funny though. The story I heard about this aircraft was that, the day before, the propeller was changed on #3. On it's first flight, the RGB separated. On it's way down, the #3 prop impacted #4 in-flight, causing the #4 prop blade to bury itself into the leading edge. The personnel changing the propeller the day before were under investigation for the mishap, but were cleared when it was found out that the RGB was defective. I don't know if the story is 100% true. When you start getting into second and third-hand stories, you never know what's true, but this is what I was told. If I changed the prop the day before, I'd be sweating bullets during all this, for sure.
-
I've seen at least three cases where the Blade De-Ice checks good statically and at LSGI, but as soon as we upspeed the motor, the blade de-ice lost some amperage. Every case ended up causing us to change the propeller. I've also seen a dome leak make the spinner contacts too dirty to pass voltage, so without you telling us which De-Ice is low, and how many engines, it's hard to say. If it is both spinner and blade de-ice on all props, think bus problems, or De-Icer Timer.
-
I'm with Herk 308 on this one. I'm thinking Speed Sensitive Valve. 4,000 to 5,000 inlbs is the magic numbers for speed valve failure.
-
From what I hear, AMC is going 100% J-model eventually, leaving the H's to Guard and Reserve, so that might give you a bit more hope for the NP2000
-
I'm no hydro troop, but I also want to say that's normal.
-
I would recommend installing the TD Amp Test Set on to the Firewall TIT harness and checking the indication that way. The indicator should read within 6 degrees of what the TD Amp Test Set is set to, but to be safe, I'd change a low-reading gauge until you get one that reads right on, or slightly high, but within limits. Also, Ohm out the T-block and check the Y-lead. Then, do a good Torque Calibration. If you don't have specialized equipment, or can't afford to start swapping parts out, you can just swap TIT indicators and fuel flow indicators between motors, as well as swap the Y-Lead leads between the AMP side and IND side of the T-block for troubleshooting only. Technically though, there is no limitation on Fuel Flow alignment, just a blurp in the -1 that says it could indicate a malfunction. That is why I would recommend calibrating the torque indicators. You should also check how old the engine is. If the engine is newer than the other three, it will by nature pull more torque. Every situation is different, but I believe it is an indication problem in the TIT indication system somewhere.
-
My apologies Natops, I guess I can be kind of unclear and rush through my explanations. My intention was to show an easy way to check if the synchrophaser system is causing the problem. If you do the check correctly, you advance the symmetrical throttles above crossover, select locked, then retart the throttles until RPM drops 1% RPM from normal governing (AF), normally 99%. You note torque, then select the fuel governing check switches and advance the throttles to takeoff setting, then note RPM and Fuel Flow. While still holding the fuel governing check switches, retard the throttles until the RPM drops off to just where you hit the switches, normally 99%, then note torque again to verify pitchlock. You must have 500 in-lbs higher torque the second time (AF Prop and Engine Book). What I was getting at was, if you hit the fuel governing check switches and advance the throttles, there is a problem with the synchrophaser system if the RPM returns back to 100% with the fuel governing check switches still selected, but we've had people, through lack of experience, think this malfunction is caused by a pitchlock regulator or fuel control, when in reality, they haven't even been able to do their jobs yet because the synchrophaser hasn't done it's job, due to wiring, power supply issues, or speed bias assy malfunction. How I do the check? I personally like to bypass the first step and assume it's 5000 in-lbs (-7), go to 970 TIT (-7), then hit the fuel governing check switches to check for the RPM increase (if the sync system is malfunctioning, the RPM will remain at 100%), then decrease throttle setting until I hit 99%. I'm usually around 7,000+ in-lbs (-7). Doing it this way makes the check go by a little faster, and I'm usually not even close to 5k in-lbs, so I don't have to spend time staring at the torque gauge for accuracy. The less time spent in Pitchlock puts less stress on the first stage compressor vanes. I also have better luck successfully pitchlocking this way. I'm not really going against the book. This is the way our book tells us to do it if the first two attempts fail. We've had ISO kick aircraft back to us for multiple props not pitchlocking the first time and expecting us to change pitchlock regulators for them. I'd do the check my way, sign the write-up off and kick it back to them.
-
As long as RPM didn't correct back to 100% on it's own, you're 100% right, but all he said was that RPM topped out at 104-105, he didn't say if it stayed there or not. 104 to 105% RPM can happen with Synchrophaser system failure if you perform the Pitchlock check correctly, with a throttle burst. That's why I prefer to perform the check while already at power. HispanicMechanic, please don't leave us hanging like most people do with problems like this. Tell us what you find. Might help other people out down the line.
-
Seen this problem many times, with many causes. A lot of it has to do with how you are trying to pitchlock. I always have more luck moving my throttles to takeoff and then hit the switches after the RPM has stabilized. If RPM stays at 100% RPM with the switches engaged, think synchrophaser system failure, such as Synchrophaser, Valve Housing, or associated wiring (we had a plane come back from Depot with two wires crossed in the wing.) Also, check the C/B's. If the sync isn't getting power, it can't tell the speed bias motor to go to 106% If RPM does increase when you hit the switches at takeoff, you may have the Fuel Governer set too low on the fuel control. You should do this check with an accutach if you are having problems. The limitations for the RPM setting are in the 1c-130h-2-61jg-10-1 s/s/sn 61-00-02 pg 1-84 through 1-86. You may also have a bad Pitchlock regulator from supply, seen that one before. I suppose it is possible the TD Amp could cause this problem, so try the check in Null and see what happens. I've never seen an improperly manufactured propeller cause this problem, but that doesn't mean it's not possible. Before you start tearing the prop apart looking for a smoking gun though, I'd look at the easy things. Definately actuate the fuel governor switches while already stabilized at power first and see if the electrical portion of the system is fully functional. If nothing happens, there's most likely nothing mechanically wrong with your prop.
-
Might have something to do with gutting a $66 mil airplane instead of a $34 mil airplane. You can basically have 2 H-model airframes available for gunship mod to the J-model's 1. The U Gunship modification itself probably costs over $150 mil, so the extra for a J may seem like a drop in the bucket anyway. I dunno. Food for thought.
-
You should try to check the clearances on the torque retainer lug assembly. You should also make sure the parts of the assembly are bolted on tight and safetied. If the clearances are correct, you may have some binding linkage underneath the valve housing cover itself. If you can get the problem to duplicate without actually operating the engine, it would definately indicate rigging problems. If it cannot duplicate without running engines, it would seem more like a linkage/torque retainer lug problem.
-
From what I heard, Brush Block fires were a hazard until they switched to the new spec. I have yet to see one catch fire, although I've seen them shoot sparks and electric bolts.
-
I hope 7849 doesn't get tossed away as scrap. I took that plane to McChord in 2003 as part of the 29th, and it was solid flier then. I believe it retired not too long after that trip. The plane itself came from the 53rd before it went to Sheppard.
-
Just got an Alaska bird too. Still no Reserve people though.