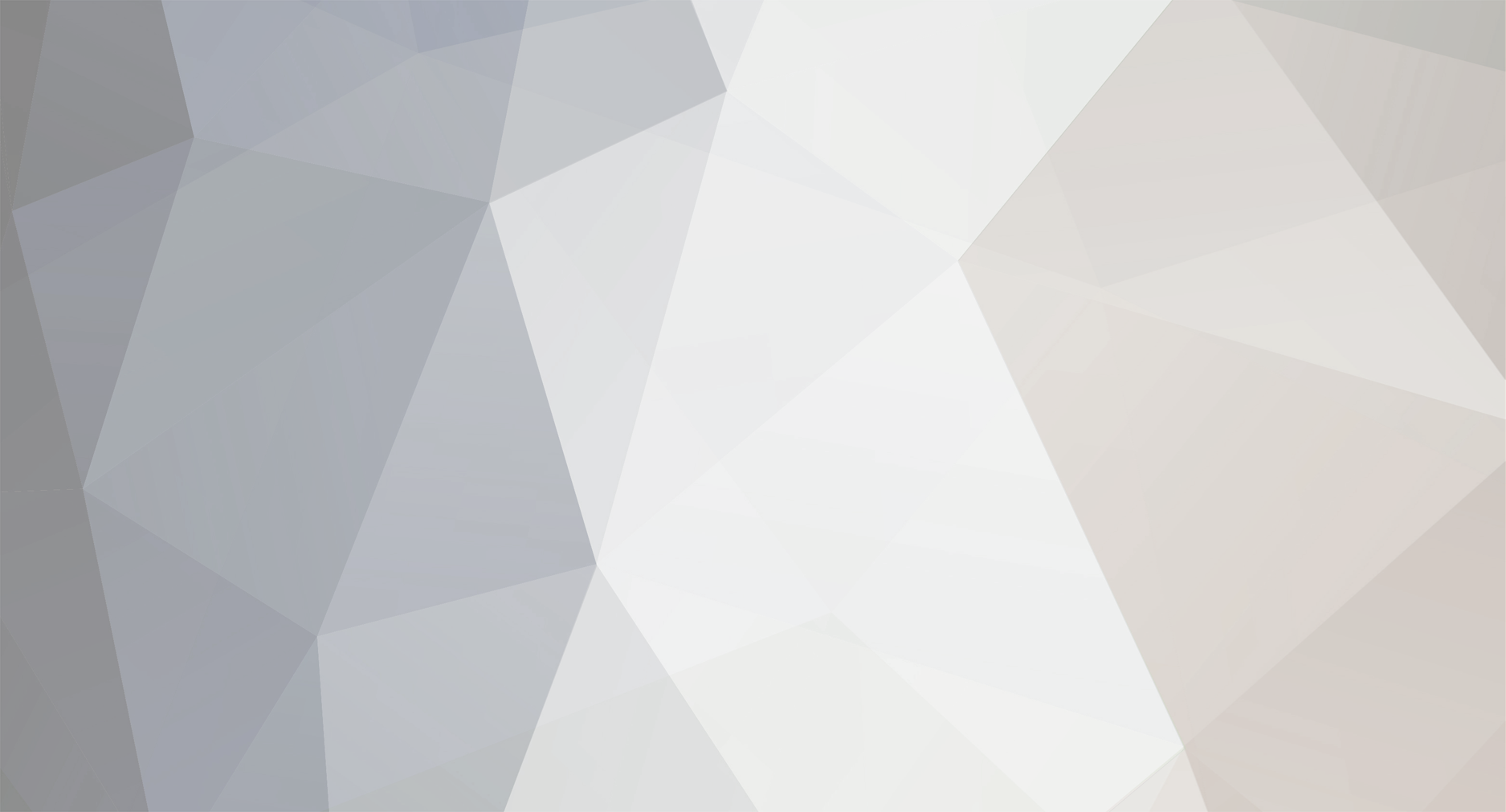
n1dp
Members-
Posts
138 -
Joined
-
Last visited
-
Days Won
7
Content Type
Profiles
Forums
Store
Gallery
Downloads
Calendar
C-130 Hercules News
Everything posted by n1dp
-
Might be left over from paratroop door scanner seats on the HC-130B and other export maritime patrol models. Photos?
-
Most military Herks had the mods. 1980s I recall. Belly strobe was tagged out on the ground because of brightness. Had to hit some override switch to test on preflight.
-
Had to do some reading. TCAS gets it's altitude input from the transponder (IFF) which in turn gets it from the pilot's encoding altimeter. At least on older models. Because it is happening at 10K, I'm going to assume it may be a bad altitude input (or lack of one) instead of the TCAS system. Disclaimer: It's been a few years!
-
Good to hear. Was this found at the generator in the nacelle?
-
I guess I need to ask if these are the upgraded generator control panels where the "field trip" position on the generator switch is eliminated. If so, is it displaying a fault code?
-
Are you getting voltage at the generator terminals in the QEC?
-
Wiring in the form of a connector in the system. Rear fuel tank bulkhead connector for sure, but also the connector going into the pressure bulkhead. One of those gave us a problem many years ago for an external tank. Wiggle wire at the connectors too.
-
This sounds like a case of the ground tie valve either leaking or not rigged properly. This valve is used to allow aux. hydraulic system to power the utility on the ground. The valve is located above the left hand wheel well.
-
Not sure why the dark circles. Trying to find a good picture of the top of the wing for you. Those outboard fuel tank panels have no other penetrations.
-
https://www.usaf-sig.org/index.php/references/downloads/category/116-c-130-hercules-lockheed?download=419:t-o-1c-130b-1-flight-manual-c-130b-hc-130b-and-c-130e-13-11-1970 It looks like you have pages of the "B" manual from this vintage. Take a read through, many answers in that manual. Let us know if you have more questions.
-
On the formation light picture, you cane see the formation lights are installed over the flap well, not the main part of the wing where the fuel tanks and dry bays are. In early manuals, there was an over the wing refueling port for the Aux tanks, located between the inboard engines and the wing root. Pretty sure they were eliminated when the center wing boxes were replaced due to cracking. Also, those rectangular looking dry bay access doors were replaced by an oval hatch with a round cover in the middle. Disclaimer: It's been a while.
-
HC-130B had formation lights. (former USCG FE here) Same as all other "B" models. The double dark spots behind #4; inboard is the drybay access cover, about 6 inches in diameter, the outboard dark spot is most likely the #4 fuel tank Over the Wing (OTW) filler port cover. They were always red. Drybay covers were white. Also. when this photo was taken, we had not replaced the outer wings.
-
The blessed propeller synchrophaser.
-
The stainless steel can showed up with some of the H2s in the 80s. Atomic toilet in the back by the RH paratroop door and these in the front of the cargo compartment on the 245. Promptly removed. There was an old story "floating" around about the old urinals that were mouted up there with tubes to the back; 1960s. The story goes a crew member hurried back and used it forgetting that the Commandant and his wife were on a seat pallet in the back. Me thinks corrosion was the bigger factor in removal.
-
Yes, Co-Pilot would do it. More of a stretch, but the FE could reach it.
-
A fair amount of L100 operators here. Some I haven't heard in a while. Some from So. Africa, maybe one or two from Lynden.
-
Had to think about this for a while. I remember sitting in the Engineer's seat for many hours pondering the design of electrical systems. The simplicity of the three phase overhead fuel panel switch allows for control even if DC busses are lost. Something you would loose if you used DC power to control a power relay.
-
All the aircraft in B,E,H series had the electrical control provisions installed from the overhead panel to the nacelle, but few ever had the valves or diffusers installed in the nacelles to make this work. I suspect only the aircraft for arctic service had the complete kit installed. A note: many mods later on used the nacelle pre-heat wiring to run new items such as the chip detector TCTO on US Coast Guard Aircraft. I also think the wiring may have been repurposed for augmented oil cooling system for ground use. Disclaimer: It's been a while.
-
My gut feeling is the devices under load are considered more long lasting and stable and less likely to need a circuit breaker. Rare that a transformer fails, certainly at those loads. This is instrument power, 26 VAC single phase if I recall right. Never saw one fail in 26 years of fixing and flying.
-
It took a while for the old brain to kick in. I remember many a Functional Check Flight checking this: Low Cabin Air Pressure Warning Light 28V ESS DC CP Side CABIN LOW PRESSURE WARNING A low cabin air pressure warning light on the copilot’s instrument panel will illuminate if the cabin altitude exceeds 10,000 feet
-
Is this guy reminiscing about engine runs?
-
https://www.google.com/url?sa=i&rct=j&q=&esrc=s&source=images&cd=&cad=rja&uact=8&ved=2ahUKEwi23IKRjrrgAhWDNd8KHVvlAMEQjRx6BAgBEAQ&url=http%3A%2F%2Fwww.flight-mechanic.com%2Fremote-sensing-and-indication%2F&psig=AOvVaw3i8Doffa4eA2ef_NGe1i3I&ust=1550195346892974 It is a DC Selsyn System
-
After so many years and flight hours, the anti skid wiring from a terminal board above the wheel well to the transducers would wear. Intermittent anti skid tests was the usual symptom. Bad test in the air good test on the ground. After you have done all listed above and you still have problems with the system, change the wire.