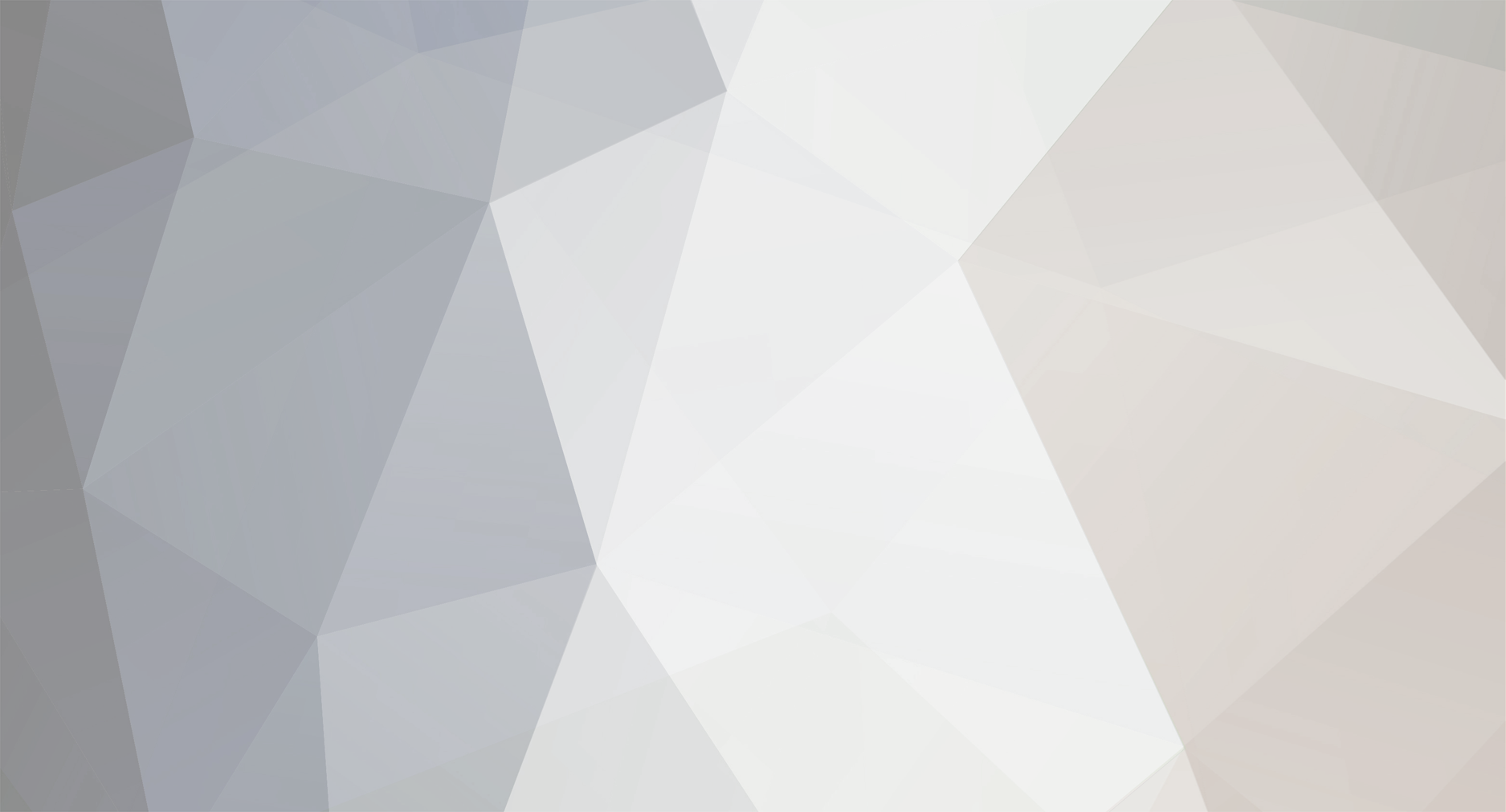
NATOPS1
Members-
Posts
785 -
Joined
-
Last visited
-
Days Won
7
Content Type
Profiles
Forums
Store
Gallery
Downloads
Calendar
C-130 Hercules News
Everything posted by NATOPS1
-
Loose cable break switch... The Emergency Flap brakes are not engaged or are engaged?
-
Are the emergency flap brakes engaging? Why do you pull the CB?
-
We have left (almost) full fuel loads on aircraft for several days at a time. Every day we would taxi the aircraft to keep the tire round...
-
You can tow it at 175,000 so 175,000... If parked "for several days" the books talk about tire "stretching" (flat spots). Years past we would put a full load in fuse (think about cargo) you have "parked" an aircraft with a cargo load of 24,000 for 24 hrs or more yes? Partially fill the main tanks to avoid fuel venting but no weight issues. We did start the engines and move the aircraft each day if missions were cancelled to avoid the flat spots. The struts and tires will be fine any landing will far exceed the pressure generated by sitting...
-
Pull one CBer and see if the other stations clear up... If not reset 1st CB and pull the other to see if the issue clears. You may be able to isolate to one CB if not remove the cannon plugs (transmitter select and radio select panels) station by station and see if you can isolate it that way. More than one aircraft has this issue? If so look at the MOD and see where it ties into the ICS there may be wires on the wrong terminal (would not be the first time....)
-
I think I missed the point of your question or at least parts of it also so bad on me as well... Well given your options... Depending on fuel level I would land on crossfeed from the transfer pump 4K cutoff (maybe) the pump is more centered in the tank so the fuel would move towards it to some degree. At lower fuel levels the tank to engine would be better as the fuel pick up is in the surge box and would be more protected. I would "utilize crossfeed operations" but it would be from #1 boostpump but that’s just me. I think once you have an "abnormal" situation the "Normal" direction provided becomes secondary and your knowledge becomes primary. I would think the section that tells you to go tank to engine for landing is based on a boost pump being in an operable condition; it does not have a "boost pump inop" condition exception but that condition IN MY OPINION exempts you from the requirement to comply with a "normal procedure"...
-
It always matters; you can do an acceleration check time calculation for any takeoff; you are just giving yourself more runway to stop on by detecting a problem sooner (or at all) and at a lower airspeed. Not sure what you mean by this statement... I think you have a few ideas in one statement. If you had the same aircraft (weight) on the same runway under the same conditions the aircraft with the 100% engine would reach a speed (Vr) "faster" (sooner) than a 95% engine aircraft which would result in more runway remaining to stop on. Also the take off factor would be higher in the 95% engine resulting in a longer runway requirement, therefore you could induce a safe margin by calculating at 95% even if you had 100% engines. If you encountered "an abnormal acceleration" you would not end up in a position where you could not stop IF you computed the acceleration check time. You should detect this "abnormal acceleration" during the acceleration check time no matter which aircraft you were on 95 or 100% engines. 3 knots for acceleration check time not seconds (3 Knot tolerance for airspeed) So why do you not trust your numbers? It is a power vs weight/drag calculation. Tq of 19.6 vs a 150K Aircraft at 50% Flaps. X amount of power will accelerate X weight and X drag to X speed within X amount of seconds... So if you have a malfunction after takoff you may elect to stay on the runway? For??? load shift? Fuselage Fire? Please do tell....
-
Ok we need to separate a few items/ideas then we can sort this out. (CFL/Vcef vs Vr and acceleration) CFL is the minimum runway required to operate safely. Vcef is the speed at which we can continue to take off or stop on CFL. CFL and Vcef are a planning tools; they allow us to look at a situation and determine if we can operate safely from a particular runway with atmospheric conditions taken into account. Vr is the maximum speed we can go on the runway and stop on the remaining runway. In a NO wind calculation Vr and Vcef are equal if the runway required is equal to the runway available; in reality the wind value and the reliance of the wind to stop vice continue the take off ensures that your Vr is always higher than Vcef. Acceleration check time is a way to ensure the aircraft is performing to a standard to allow the crew adequate time to identify and react to a lack of performance prior to Vr (or stop point on the runway) Vr can be converted into a distance as previously discussed. We can calculate this time/speed any day, any takeoff however it has been deemed only necessary during short(er) field operations. If the Acceleration check time is not achieved we will be beyond our refusal point on the runway when we reach Vr; or below Vr at that point on the runway. We use speed due to the inability to physically mark the runway. Would you think wind impacts acceleration that much? Yes the charts are designed to account for the full stopping affect of the wind and a smaller portion of the wind for a continued take off. I would like to see your paper you can PM me on this site…
-
"In fact it is a distance not a speed." This is not exactly true... The calculated "Refusal Speed" can be converted to a "distance" and this is actually discussed in the 1.1 Acceleration check time section.
-
Dan as a very long time member of this fourm I know you only here but based on what I have read in your post we share alot of the same values. Fair winds and following seas is what we wish for our Brothers and thus they are exactly what I wish for you...
-
The reason I ask is because these numbers make no sense to me... Engine 1 2 3 4 Lbs 500 500 1700 1700
-
Start engines, record NULL start temps, record minimum TQ readings, go to reverse get TQ and FF readings, go to Flight Idle get TQ and FF readings, advance throttles to crossover record TQ and FF and also watch the TIT change (Rich/Lean) and record TIT increase or decrease. Retard Throttles to Flight Idle record TQ and FF, Ground Idle record time for LPS retract as well as TQ and FF numbers...
-
C-130 two left engine out, and blowing a tire landing on the news.
NATOPS1 replied to mark18mwm's topic in C-130 General
Yea I still think they (flaps) are at 50% I say this due to the "downward movement" they have made. Look at the ailerons as it "flies" by and you can see the flaps are half way; if at 20% not that much downward movement. Think increased lift without the drag penalty of 50% but no 20% landing speeds so using 0% speeds means your fast... -
Is the Low pitch stop retracting? Sounds like it is NOT... This is why your aircraft is moving right (Forward thrust) TQ on the left; ground idle blade angle on the right (DRAG) so you "wink" right. Check for the LPS to retract...
-
C-130 two left engine out, and blowing a tire landing on the news.
NATOPS1 replied to mark18mwm's topic in C-130 General
Quibble away; I get the airspeed relationship. If you look at the blade angle it is pretty close to feather (at least 86 degrees) so that is why I said no drag... The VMCA is based on a prop that did not feather IE: FLAT MAX drag; not feathered rotating backwards... If you look the prop in this case it is feathered, to the point it is rotating backwards... FYI, You could have no failures in the RGB and have a "coupled windmilling prop". Just for clarity the prop brake is internal (RGB) the Safety coupling is external and not "part of the RGB". -
C-130 two left engine out, and blowing a tire landing on the news.
NATOPS1 replied to mark18mwm's topic in C-130 General
I do not think it was decoupled it was spinning too slow...it was feathered so no drag. Also the prop would have to "drive" the engine with a lot of force in order to decouple; not something I could see happening in the case it looks normal only with a weak prop brake. So Flaps 50%? Is that standard? I would guess they would have been cranked or positioned prior to the second engine shutdown. Also seemed FAST to me but it may be a camera angle thing... The Flaps being at 50% is a surprise to me... -
Some call it the Syncrophase check now...
-
A few points. 1. Crossfeed is using fuel from any tank to any engine. 2. I would further say that "Crossfeed" is generally defined and accepted as the practice of utilizing the crossfeed manifold and Main Tank Boost Pumps and or the Aux/Ext pumps; NOT the transfer pump, transfer manifold and the Crossfeed manifold. 3. I see your Transfer pump use and would ask why would you use the transfer pump and not the No1 main tank Boost Pump "on crossfeed for landing? (or AUX/EXT) 4. Does your book have a Caution about unbalanced fuel due to the use of transfer pumps and crossfeed? 5. Also if you can do touch and Go "Landings" on crossfeed from the Aux/Ext you can "land" on crossfeed and I would think you could "ABORT" the GO part of a "Touch and GO" Landing yes? SO to answer your question; I would NOT land on “crossfeed†from the transfer pump. I would utilize the main tank Boost pump on that wing; in your example I would use the TK1 Main Tank Boost pump and crossfeed to Engine 2. Also the Ext tank pumps are located inside a "surge box" so no sloshing...
-
Land with the engine on crossfeed... This will prevent the flame out not induce it. There is NO fuel "slushing" (sloshing) because the fuel pump is inside a surge box. The box is full of fuel at all times and remains full due to inward flow as well as fuel pump discharge (water removal system) also the box will not allow the fuel to "leave" the box unless there is too much fuel or the fuel is pumped out by the pump.
-
Digital fuel indication went off during normal flight
NATOPS1 replied to bruno_Tuga's topic in C-130 Technical
ANy update on this issue? -
Haven't found P&T.. any ideas?
-
Maybe you have snubbers on the Low pressure warning light pressure switches. Our snubbers are installed at the transmitters. Sometimes the light goes out before we even have ignition. This is our "normal" indication as well...
-
200 KIAS Check your FCF Note APU shall only be started below 20,000 feet and 200 KIAS.
-
You forgot #1 Windmilling on NTS, gear down, 50% flaps... I did not want to confuse the issue but I think WE have.... So to recap: There is no minimum Torque setting for takeoff... Torque will change with Alt and Temp so at a very high (High Pressure Altitude), very hot (High OAT) airport the Torque will be low... (you need a longer runway or must reduce you aircraft takeoff weight) Speed is the number we use... Takeoff speed ensures a margin above stall speed (1.1) As Stated It may sound "wrong" and ONLY after considering all other factors (terrain, climb capabilities, etc.) this is not "bad" advice. …if you have the power necessary to climb (say straight ahead out over the water) a reduced torque value will result in your VMCA KIAS to go down. Never was there a discussion about reducing power (flying around land locked states, with hills, mountains, trees, buildings) “We always taught the students that once everything gets settled after shutdown, pull back throttle on symmetrical engine to help with directional control†This is exactly what we are talking about VMCA is ALL about directional control...
-
Digital fuel indication went off during normal flight
NATOPS1 replied to bruno_Tuga's topic in C-130 Technical
Ok... #2 Gen Off same problem. So Not a gen Issue its a ESS AC suppy to AC Inst EFC Bus issue. Inverter ON no problem. Your wiring to your instruments is good, check all your connections from the Normal power fail Cb to Power relays. Changed Power relays #1 and #2? (They are denergized to allow ESS AC to power the AC Inst EFC Bus so I hope it works but not sure it will)