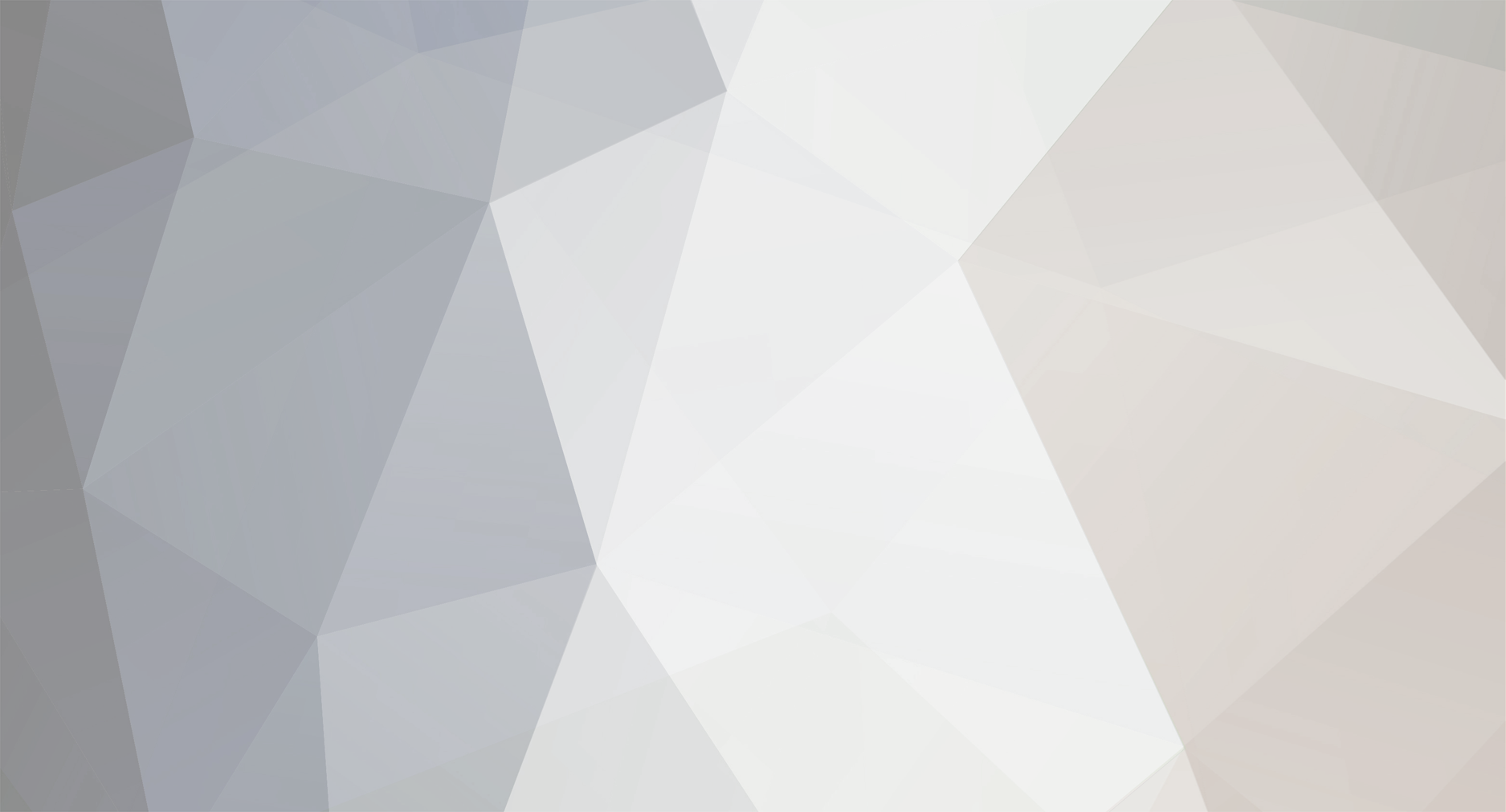
Lkuest
Members-
Posts
317 -
Joined
-
Last visited
-
Days Won
5
Content Type
Profiles
Forums
Store
Gallery
Downloads
Calendar
C-130 Hercules News
Everything posted by Lkuest
-
With RPM, TIT, FF, and Torque all low, I would think the problem is in the engine. The propeller's job is to maintain 100% rpm, no matter how much power the engine is putting out. If the propeller were to malfunction by increasing blade angle, the FF would not change noticeably, RPM would decrease, but torque would increase. If the prop were to decrease blade angle, torque would decrease, but RPM would increase until it hit the fuel control fuel governor where fuel flow would finally drop, but RPM would remain high. The problem would have to be in the engine fuel system. It sounds as if the TD System being turned on and off creates a difference, and the engine behaves normally in null, drops off power in auto. I would suspect a bad coordinator or bad wiring in the TD system. You might slowly swap TD system components between engines until the problem moves over to the other engine. I know it sounds silly, but with a strange problem like this, you'd be throwing money at it just changing parts. It may not make sense for a fuel system component to reduce RPM, since that is the propeller's job, but it may be taking so much fuel that the propeller drops down to 25 degrees blade angle and cannot maintain the RPM for the power anymore. Without running the aircraft myself, this is all that makes sense to me with the information provided. The problem cannot be caused by an air leak because the drop in torque would be accompanied by an increase in TIT.
-
What is torque doing under all these conditions? Also, have you performed a TD system check using a test set?
-
If your turbines are undamaged, and TIT indication systems are functioning properly, then the problem has to be in the fuel flow indication side. I never liked the fuel flow indication system. We had an engine that constantly showed higher fuel flow then the rest of the engines, but we changed the entire TIT indication system and the fuel flow indication system, as well as inspected for turbine damage, and nothing fixed anything. We ended up just saying we had no throttle alignment limit for fuel flow and left it at that. It was like that for so long, it went to the boneyard like that with no other problems or resulting engine damage. Crane Aero has a new fuel flow indication system you might check out called MFFIS. They claim it's more reliable, so it might be worth a checkout, that is, if fuel flow indication is your problem.
-
Currently, we do them every ISO, which is a 570 day interval. The ISO cycle used to be 360 days, so they added them to the work cards for the HSC if the aircraft has flown 400 hrs or more since last ISO. Currently in the US Air Force, we fly with JP-8 or Jet-A with no additives, so they tend to need a good cleaning, sometimes even after 150 hrs. I hear the fuel nozzles that flow the +100 additive rarely flow bad at all, so it all depends on what you guys use for fuel as well.
-
The TD valve brake is de-energized engaged. When the brake breaks, it locks the fuel correction in whatever position the TD Amp wants to take it or put it to. After a null adjustment, the adjustment richens or leans the fuel mixture, which the TD Amp tries to correct for it in the controlling range. While the amp corrects, the brake slips a bit, like a clutch, which re-tunes the rich/lean back to where it was before adjustment. I've seen this problem quite a few times. It's actually a fairly common failure mode of the TD Valve due to the nature of the brake being engaged when it is de-energized (broken), but the trim motor still works to attempt corrections.
-
Does this same thing happen with #3 bleed closed, but all other conditions the same? Also, remember there is enough fuel in the engine to maintain operation for a short while, so if fuel is being cut off from outside the motor, such as the fuel shutoff valve in the wing, the engine will not shut off immediately after the valve closes. There is nothing electrically that happens in the start circuit during 55% RPM that doesn't also happen at 16%. To test this, you might actuate #4 engine anti-icing during #4 engine start and see what RPM the malfunction occurs. If the RPM is the same, the problem may be electical, but I'm not sure how. If the problem occurs at the same moment (i.e. 30 seconds into start with or without anti-icing), it may be related to the fuel fire shutoff valve.
-
Lockheed Service News Bulletin No. 2 has a picture of a nosecone removed. I'm not sure if it will help, but maybe worth looking at.
-
I have seen a few slicks with a painted titanium panel, specifically Air Guard and AETC aircraft.
-
As far as I know, All J's are capable of having externals, but it is not as economical when they are installed, so they just leave them removed.
-
Open the clamshell doors and see if the 5th and 10th bleed valves are closed. You may also want to push a borescope probe through the bleed collectors to inspect the top and bottom valves. If they are closed, think Speed Sensitive Valve failure. I have also had the Accessory Drive Housing cause the speed sensitive valve to fail. When changing the Speed Valve, I recommend draining the Accessory Drive to both lower the level of oil in the casing, as well as visually inspecting the drain plug for metal. Your defect cannot be fuel related because high TIT would cause a faster start, and low TIT would cause a slower start. They go hand-in-hand. If you suspect low-starter air pressure, disconnect the starter sensing line to force the starter control valve to stay full-open. Make sure you only use the APU/GTC air as this could shear the starter off 70psi from the engines. If it is still slow to start, it may be a sheared/jammed bleed air valve at the horsecollar. Good hunting.
-
I've seen the solid state inverter cause all 4 engine TD systems to go into full take in the A/C position only, causing a massive cold start on all 4. On a different aircraft, all for engines went into full put in the D/C position only, causing 900+ hot starts. An inverter change fixed both. I hear when we upgraded to the solid state syncrophaser, the reliability of that system went up, but so did the severety of failure. It looks to me like the same thing is happening with the solid state inverters. At least they failed during the engine start and not in flight. Yet.
-
A bit of googling turned up 7764, but I haven't seen it in person.
-
Just like the H, it's 1 on, 1 off; 1 on, 5 off, 1 on 30 off. the E's use the 1C-130H series job guides as well. There is a minimum PSI during start, but I cannot recall it off the top of my head. It's not in the engine run job guide for some reason.
-
Both the 1C-130H-1 and the 1C-130H-2-61JG-10-1 have 25 seconds listed as the limit from reverse to feather position. This is for propeller static operation testing only, not for engine operation. Typically though, the engine emergency shutdown is about 10 seconds to full feather and button popout due to having the main and standby pumps increasing the blade angle along with the aux, so there has to be a lot wrong for the engine to take 30 seconds to go static or reach full feather in flight. I am also suspecting that the propeller blades are not reaching full feather position, which would easily explain the 30 second engine static time in flight only, with a post-shutdown rotation clockwise when viewed from the rear, but it is not exactly clear what the exact defect is in the posts, so I can't recommend one thing or another. I do see that the engine was already changed, and the prop is being changed right now. Engine rigging cannot be the cause as the feathering action is both electrical and mechanical, so everything else is either already eliminated or about to be. The discrepancy is hard to understand, but from what I CAN understand, I'm guessing the feather blade angle is too low.
-
What direction is the propeller windmilling after in-flight shutdown, and what is your airspeed when you shut the engine down?
-
I've seen this caused by the hardware shearing off at the blade butt. There's a couple of screws and a couple of mounting studs that keep everything necessary for pitch change of the blade together. Thankfully it happened during a maintenance run.
-
can propeller reindexing check be carried out in flight?
Lkuest replied to edwardlcy's topic in C-130 Technical
The J is very similar in that you select a master propeller, and you may select either 2 or 3. From there, things change. The propellers on the J generate six pulses per revolution in stead of 1. FADEC A synchrophases all slaves to within 1% and 2 degrees of phase angle. On the 54H60 prop, resynching is done to establish a relationship between the electronic and mechanical parts of the valvehousing via a clutch and brake mechanism so that the electronic synchrophaser always knows what it's telling the hydromechanical pilot valve to do (calibrating the feedback pot to the pilot valve). On the J, the pitch is controlled 100% electonically via the the FADEC to maintain 100% rpm as measured at the power turbine. In synchrophasing mode, the FADEC varies RPM slightly to establish a proper phase angle, then readjusts to 100% rpm to maintain that same phase angle relationship. The FADEC tells the hydraulic Pitch Control Unit what to do, and the PCU reports back what it is doing via Transducers. There are no clutches to slip, and the dowty is so precise that no resynching is required to establish a proper relationship. The 6 pulses per revolution produced by the propeller synchrophasing system may also be used to measure RPM if needed. I'd be curious to know how the NP2000 does it. -
can propeller reindexing check be carried out in flight?
Lkuest replied to edwardlcy's topic in C-130 Technical
We still safetywire it with .20 copper. The procedure to resync in flight still in our -1 though. I think if we really didn't want the crews to do it, we'd safety it with .32 or .41. We might safety it with copper so that we don't accidently hit the resync switch during ground maintenance (even though the resync switch isn't powered until a master is selected). There's even a caution in our 61JG to not hit the resync switch while the propellers are static. If we do accidently hit it, it'll be pretty easy to identify that it's been accidently hit based on broken safetywire. Without something written about why we do something, all you can do is guess, and that's my best guess. Anybody out there have a better guess, or some documentation as to why we safety the resync switch? -
What is the engine efficiency? When the speed drops, what is Torque? During flameout, check bleed air manifold pressure of that one engine. Have you checked the engine for bleed air leaks using a man-on-the-stand runs? How is the gap in the propeller torque retainer lug assembly? NTS bracket? Have you inspected the compressor 5th and 10th for damage? Have you inspected the turbine module for damage? Check Low Speed Ground Idle anti-ice check for 24 degree rise with bleed closed. Check what the blade angle is at Flight Idle and Low Pitch Stop You can also disconnect the Compressor Inlet Pressure line from the Air Inlet Housing and blow 80-120psi of air pressure into the Air Inlet Housing side of the disconnected line. You can change acceleration bleed valves, but to check them, disconnect the line coming out of the Speed Sensitive valve and apply a low amount of air pressure, then check to see if all the valves closed. It is easiest to check the 12 and 6 o'clock valves with a borescope through the bleed collectors. After you apply low air pressure, apply a vaccum and see if the valves open again. If they do this easily, the valves are all good. If one is not as free, it is probably dirty or frozen. It is possible you have a bad fuel control, but I don't see how a fuel control can cause low RPM and high fuel flow at the same time. It sounds a lot to me like a bad air system or NTS. These would cause a rich "Bog Down" you are experiencing. It seems pjvr99 has good experience that isn't in any book I've read, and everything he says makes sense. Good luck!
-
When you checked the coordinator, did you check both the 65 and 66 degree switches for breaking contact above 65/66 as well as getting contact back above 65/66? I would also slave a Relay Box in and see what happens. I'm thinking it's possible that the TD system stays in Temp Controlling mode even below the useful range of the coordinator potentiometer, causing the amp to go to full take. The popping could then be caused by the engine dropping below 94%. Don't forget the "Flag" check. Upspeed the engine, then put a rag secured to a seat rod up in the left and right bleed collectors and see if the rag whips around, indicating an open bleed air valve.
-
When you retard the throttle, does the RPM drop with the throttle? If so, this situation possibly indicates a pitchlocked propeller and requires an investigation. Someone possibly forgot to install, or damaged the pitchlock regulator seals when the propeller got swapped over to the new RGB. Also consider Foreign Object damage to the compressor. Check 5th and 10th compressor blades. Borescope turbine for damage? NTS Gap too small when pulling the pump housing towards you? What is the engine efficiency?
-
can propeller reindexing check be carried out in flight?
Lkuest replied to edwardlcy's topic in C-130 Technical
It's actually preferred to do it in flight. This allows for more stable conditions during the procedure. Refer to the 1C-130H-1, pg 1B-20. The only real consideration is during stable flight conditions. -
Snapped it as I was passing through. As far as I know, it still has a problem with the GTC w/n run w/o boost pump. Problem's been there since the 90's, and probably 10 GTC's ago.
-
Flying with a bad prop low oil light float switch...
Lkuest replied to ShadoFE's topic in C-130 Technical
Can't speak for old tech data that doesn't exist anymore, but the 3-1-6 RESTRICTION AGAINST FLIGHT OF AIRCRAFT WITH KNOWN PROPELLER DIFFICULTIES contains the current direction for what propeller malfunctions are allowed to exist and still be allowed to fly. It supersedes a version from 1996. It makes no mention of a bad float switch, and it is pretty clear that there must be no known defects with the propeller and associated systems with only three exceptions: Synchrophaser failure, Automatic De-icer system failure (with manual working), and feather override button not popping out when the prop reaches full feather. Every one of these must be troubleshot to the specific part before release. There is a note however, that an Exceptional release may be authorized by the MO or rated pilot serving as a crew member. Not sure if it's saying they must sign off if one of these three defects exist, or if either can sign off if another problem exists, but I assume the former. Of course, I believe your local MEL/MESL can trump this tech data, and if it does, it will list flight restrictions associated with the defect, such as not flying during inclement weather if the brush block is defective or blade de-ice boot wires burnt. If that's the case, what you are looking for might be a local procedure, not an Air Force-wide procedure.