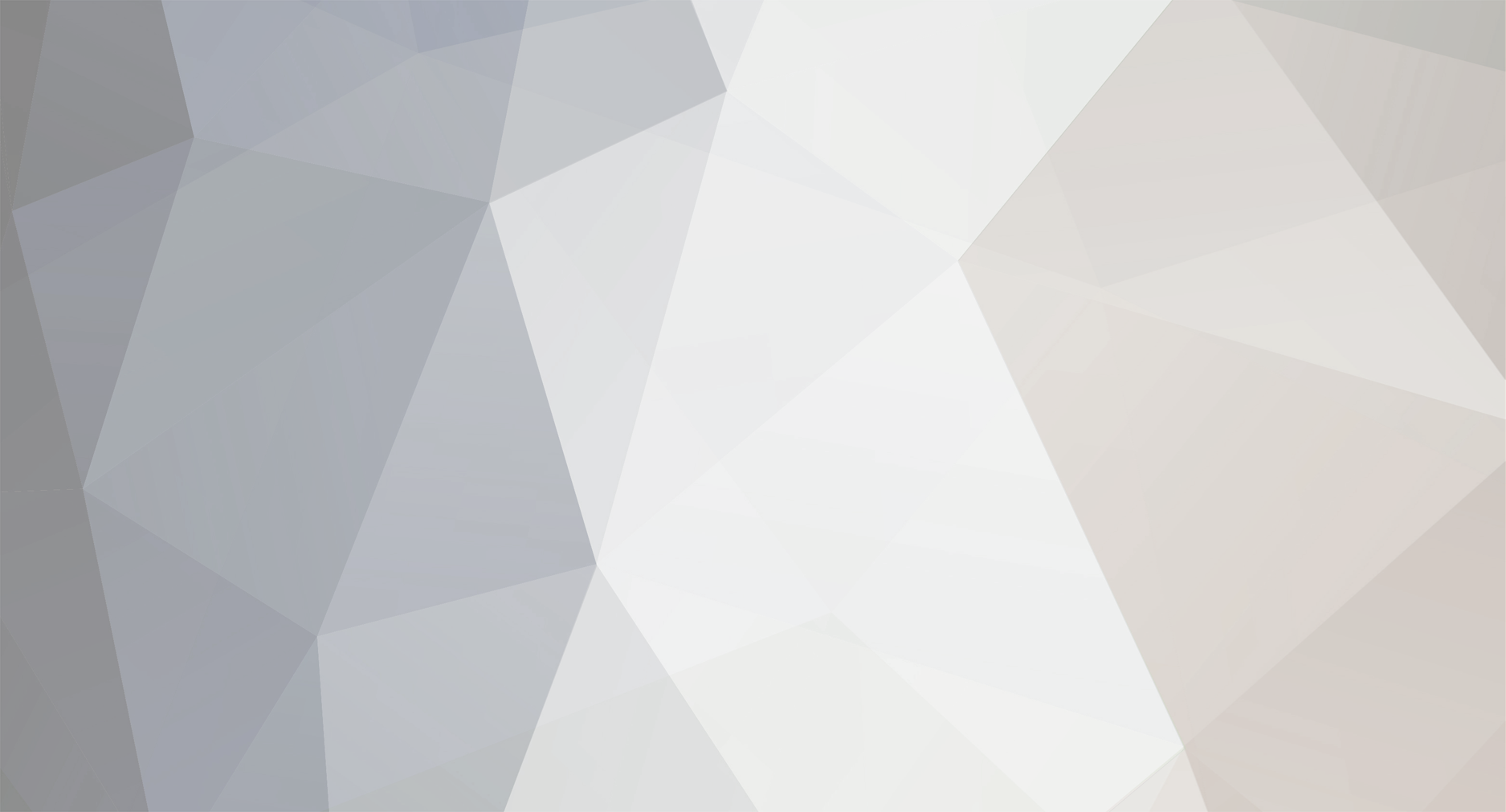
Lkuest
Members-
Posts
315 -
Joined
-
Last visited
-
Days Won
5
Content Type
Profiles
Forums
Store
Gallery
Downloads
Calendar
C-130 Hercules News
Everything posted by Lkuest
-
It's how they mount the armor, with the help of some metal brackets.
-
The current plan is to completely phase out the 62nd as the demand for "legacy" training diminishes due to new J's and AMP's, and the Little Rock Guard will be the only unit that trains the older H-models. In the near term, the 62nd is scheduled to start up a Reserve unit to stand up and phase out the Active Duty portion of the 62nd. In the long term, the 62nd will phase out the Reserves as well, leaving the Guard for H/AMP training and the 48th for the J-model training. I don't know if they plan on AMPing all of the guard's planes, but I do know they have a few assigned already, but I don't think they are doing training with them yet. So far, it's only AMC that is getting the Dyess H's.
-
When I do rigging, I always make sure the Gearbox Clevis has about 4 1/2 to 5 1/2 threads showing. If you adjust it in or out by alot, it will throw you off. Also, obviousy, since you turned to a forum for maintenance advice, I'm assuming the problem is taking you a large amount of time to resolve, so I'd advise you to go ahead and disconnect the gimbal from the doghouse at the firewall. This will enable you to go through the entire range of throttle motion without having someone in the flight deck or running up and down stands every five minutes to get below the filght idle gate. As it has already been alluded to, it is the coordinator/fuel control rigging that has the internal stops for reverse and takeoff. With the gimbal disconnected, you can check everything quickly, except ground idle, which is in the throttle quadrant. Also, while you are adjusting the rigging, tighten down all the hardware before you check to see if everything pins. Sometimes the rigging changes after you tighten stuff down. In an unrelated matter, Gimbal cables won't affect Reverse/Takeoff at the ValveHousing, but if you do adjust the throttle gimbal cables, run the throttle up and down a few times and re-check adjustment before you install gimbal clips. Sometimes it moves a little on you after adjustment.
-
I've seen windmill starts at the schoolhouse about 5 to 6 years ago, but haven't seen one since. Heard it takes Majcom approval now.
-
a. 800 in/lbs above crossover, 400 below b. treat it as an RPM flux c. probably not I'm assuming you should have a flight manual that covers this situation, but here's what I have on the top of my head: 1. Put Propeller Governing switch in mechanical 2. Put TD switch to Null Beyond those, you really need to have maintenance look at the problem, on the ground, as it could be a great deal of things. Of course, the amount of flux could tell you a lot. 5000 in/lbs would point to an acceleration bleed valve system failure. If the flux is much less, you could have a thermocouple or two with loose or missing nuts making intermittent contact. If the flux gets worse after selecting mechanical, you could have mechanical valve housing failure, with the electrical system partially covering the malfunction. You could also have internal prop leakage, which may be uncovered by putting the condition lever to air start and looking for the flux to get better. There are any number of things, electrical and mechanical, that could cause this problem, and only a maintenance team looking at total engine performance should troubleshoot a flux beyond the simple fixes in the flight manual. Any other checks beyond the flight manual shouldn't be done in the air.
-
Just got a third from Maxwell.
-
Are you talking about flight crews here? For maintenance, I didn't know there was a qualification distinction between H1,H2, and H3's. At least for engine runs, I thought they were all the same. I do understand the differences though, as I have worked on all 3 airframes. MACAWS and CAP are only minor adjustments that the H3 brings as far as engine run differences. Right now, the 62nd is in the process of recieving H2's as the E's slowly disappear. I don't know if the timetable is sensitive information or not, but needless to say, the E model's life at Little Rock is soon to come to an end. As the need for Non-AMP training starts to dwindle, the H2's will go back to where they came from, and the Guard will completely take over all the H-model training.
-
The Geneva Loc is not the proper name of the part. The proper name is Fuel Shutoff Valve Actuator. As the name implies, it is an actuator that shuts off the fuel valve inside the fuel control. I believe we call it the Geneva Loc because it is the manufacturer of the part, much like calling an engine mount a Lord mount. Someone correct me if I'm wrong.
-
There might be several reasons why they might be promoting this as a big deal. They might not have the manning. The Air Force is constantly under pressure to do more with less. Unfortunately, that means massive personnel cutbacks. Overseas bases are also authorized to go down to 50% manning requirements, so that could be a factor. The story mentioned launching all the planes they had available. That means knocking out all the scheduled maintenance and otherwise on their entire fleet. In a small fleet such as 7 or so, that might not be too hard, but I know in a larger unit, there is always one or two down for hard maintenance or lengthy scheduled maintenance, so a massive surge like this can be a big deal. The story's importance might have been inflated. I know our local paper whips up pretty good storys, sometimes with facts that are either untrue, or they were told one thing and interpreted in a different way because they don't know how to translate the Aircraft world into a story most people can understand, probably becuase the writers themselves don't understand it. Another possibility as to why you remember flying more everyday is that you guys probably flew aircraft everyday that most aircrews nowdays wouldn't even pass the preflight on. I'm not talking trash, but there have been many changes in how the aircrews determine if an airplane is flyable. I remember at the schoolhouse we would fly 8 turn 6 everyday. We also used to have the manning to support it. Nowdays, our tempo is a little less, but now they won't even fly with a TD system malfunction. That's just the schoolhouse, but it might give you an idea about the direction we've been going. It doesn't help the case of "just fly it" that we've had many years worth of aircraft mishaps since the CCK days that make the aircrews more skeptical about taking engine malfunctions. I won't even pretend to know all the reasons why they think a 7-ship is a big deal. I just wanted to throw my 2 cents in, and maybe help you make sense if it a bit. I personally think if any unit flys 100% of their airplanes in one day, they did pretty good, just because of the way manning is nowdays.
-
I know exactly what you mean. I fixed an aircraft yaw by swapping gauges, and the problem never came back. Apparently it wasn't yawing afterall.
-
during take off and landing at 40-70 knot speed SHIMMY.....:(
Lkuest replied to thunderturk's topic in C-130 Technical
When our guys have that problem and can't find something wrong, they always change the Nose tires, even if they can't find anything wrong with them. I'm not a hydro troop or crew chief, but it seems to work for them. -
Seen the TD AMP do it many times, but the C-130 can make a liar out of you.
-
Our 1C-130A-6 page 2-A-018D gives a 15 day interval. Some places go more often than that depending on the flying tempo.
-
When you say all indicators, I'm assuming you are including RPM. Since the RPM indicators have thier own power source on the tach generator, this problem might actually be making the engines roll back, especially if the crew feels the plane slowing down or hears the engines quiet down when this happens. If the RPM indicators are rolling back, I suggest an immediate impoundment and a thorough check of the electrical system. I have seen and heard of an A/C Instrument and Engine Fuel Control Inverter causing massive problems with engine performance, which might explain the indicators rolling back and the OFF flags. The Inverter also handles part of the Temp Datum system, which would explain an RPM rollback. There was a TCTO to identify and replace faulty relays that would allow the Inverter to affect the TD amps this way, but I don't know many details about it or if we actually replaced them. Maybe the next time this problem happens, have the crew immediately switch the invertor to a different position. The USAF aircrews were flying with the invertor in the A/C position for years, making this purely a bus problem, but now are flying them in the D/C position, which would mean a TR unit could be at fault as well as possibly the bus or the D/C side of the inverter. If your RPM gauges are not rolling back, disregard.
-
I believe I remember hearing or reading a story about a Vietnamese aircrew member that single-handedly stole one of the Sout Vietnamese C-130's to rescue his family when the south was falling to the north. It's been a while since I heard it, so I'm not sure about details or whether or not my mind is just playing tricks on me.
-
Well, this one could be a tuffy. It couldn't be the pitchlock regulator because it cannot cause high RPM, only low RPM with high torque. It could be a valve housing, as I have heard of them strangely causing high fuel flow problems. The fact that RPM is better in normal makes this more probable because the synchrophaser is capable of hiding valve housing problems, and it sounds like the synchrophaser knows something RPM related is wrong with the operation and trying to fix it. I don't believe it could be a fuel control, because the fuel control makes the engine put out torque, the prop's job is to use the torque by increasing blade angle, which slows the engine back down to 100%. In the flight range, the prop controls RPM almost single-handedly. If there are RPM problems, the Prop is the most likely culprit, no matter what the fuel control is doing. You may have two different problems, but I believe the Valve Housing is at least partly at fault. The easiest way to troubleshoot a problem with multiple likely culprits is to fix one problem at a time, the most obvious cause, and see what other problems are left. The valve housing might fix everything. There is another possiblity, and that's the Coordinator. That component interprets throttle and condition lever inputs and translates them into a single throttle signal input into the valve housing. If something inside is messed up, the prop might think it's in the ground range, or maybe move it towards feather. It might explain everything, but it's a longshot. My vote goes to the Valve Housing.
-
I believe they still teach that in the schoolhouse. I've seen them do it several times when an external power unit dies and they are in a hurry. It's just our maintainers that aren't allowed to do it. The main reason having A/C power during engine start is important is to have the suction boost pumps running during initial engine rotation. After that, the engines can provide their own hydraulic flow. If this wasn't the case, I'd just leave the ATM off and just run the engine ignitors off the battery. If you try that, you may cavitate the engine pumps, so like SEFEGeorge said, running the ATM during engine start until it craps out is the best practice for doing a self-contained engine start. Me as an engine troop would rather just use an external power unit. The quicker the engine starts, the less stress is put on the starter, and the fewer starters I have to change. Starting with the ATM once in a while won't hurt much though.
-
I've never had a problem jumping chalks with 100% flaps, but than again, I don't push all 4 up at the same time, either, only for troubleshooting. It makes the plane ride like a cadillac though.
-
I won't start an engine with the ATM on. I always use external power. Especially in hot environments, you want to decrease the bleed air load on the GTC as much as you can so you can start #3 as quickly as you can. Also, our tech data states that the ATM will normally be used after the first engine is started. If the GTC gives too much air to the airplane, it looses cooling air, which makes the Load Control Valve pinch off the air supply. As soon as the cooling air comes back and the TIT drops, the valve comes back open. This explains the surging you are seeing. As far as I know, your problem is not a problem at all, and you are observing normal operation of the GTC. The proceedure you are describing is what we call a "self contained start". Where I'm from, we are not allowed to perform them unless there are absolutely no power units available, which is never. APU's are different, but as long as you are using GTC's, just start #3 with external power connected, then start the ATM after you get #3 engine to High Speed Ground Idle. You will avoid a lot of trouble following this guideline. I say HSGI, because with the engine at LSGI, the GTC acually puts out more air, and you can flame your engine out trying to start another motor, especially during hot weather operations.
-
What I heard trough the grapevine is all H-2's and above will get AMP'd and get the NP2000, and all H's will get the Electronic Valve Housing. This info comes from a pretty solid source, but with the history of these programs, it doesn't matter where the info comes from, it will probably change 30 times before anything happens.
-
You'll have to forgive me. I was fumbling through the Production list a couple of years ago and came to a realization, and a couple of years later I forgot exactly what I had found. Apparently, it's all the L-100's still flying, with a couple of exceptions, were modified to -30's from the base L-100's and L-100-20's. I totally dropped the ball on that one, and I stand corrected. I also edited my post.
-
This is kind of confusing to me because the standard sized C-130J can fly higher, faster, farther, and with heavier cargo than the -30's. I guess it's the way you typed it that made me scratch my head, but you did say "legacy", so I guess that only covers E's and H's. We do have some standard sized C-130J trash haulers though. They started going exclusively C-130J-30 after the 99 model year I believe, because we usually run out of cargo room before we run out of cargo weight capacity on shortys. It's economics that the civilians have already figured out. I also believe the C-130J can be quickly modified with external tanks though. Just ask the Italians, and the Keesler guys, and the 193rd guys, and now the MC-130J guys.
-
Where are you checking the vibrations? There are several methods of doing a vibration check. There is the single Velo on the RGB, a single accelerometer on the turbine, the torquemeter runout (finding a lot of these bad), and a multipoint harness (never done one, but the Tech Data exists). The RGB Velo doesn't always catch everything. The only other thing I can think of is check your supplier of RGB's. If it is Rolls Royce, I have no idea. If you are getting refurb units from third-party companies, you might want to check into their credentials. They may not have purchased the proper tech data for RGB overhaul, or are using unapproved materials or parts during the rebuild. Even through legit channels, we managed to recieve a large batch of engines with bad Prop Brakes causing many engine removals, even on a brand new motor. It happens.
-
Those float switches are a craps shoot. Seen some last 20 years, seen others last a month. I've never seen a correlation between part numbers and failures. I just think it is a poor design, and nobody's cried loudly enough to the right people to get a redesign. Might be something to bring up at the next T56 user's conference. I would personally like a quantity indicator to replace a dummy light. That way the engineers can write up the props when they are a quart low every time they land so we don't have to check servicing all the time.
-
How do they know it won't "sync"? Are the slaves just not following the master? As for problems with both masters, there was a TCTO to install a Constant Voltage Transformer. I don't know anything about it, but I do have a bread crumb. The TCTO is supposedly 1C-130-1309. It might be able to tell you more about it. With synchrophaser problems, you have to look at everything the synchrophaser does. Throttle anticipation? Pitchlocking? Sync and Droop? RPM correction (if mechanical isn't set at exactly 100%, is there difference between mech gov/normal gov)? If all of this is dead, there is definately a power issue or something frying new synchrophasers. If only one of these things is bad, you should have a wiring issue, but how to hunt that down, I'm sure you'd know better than I would.