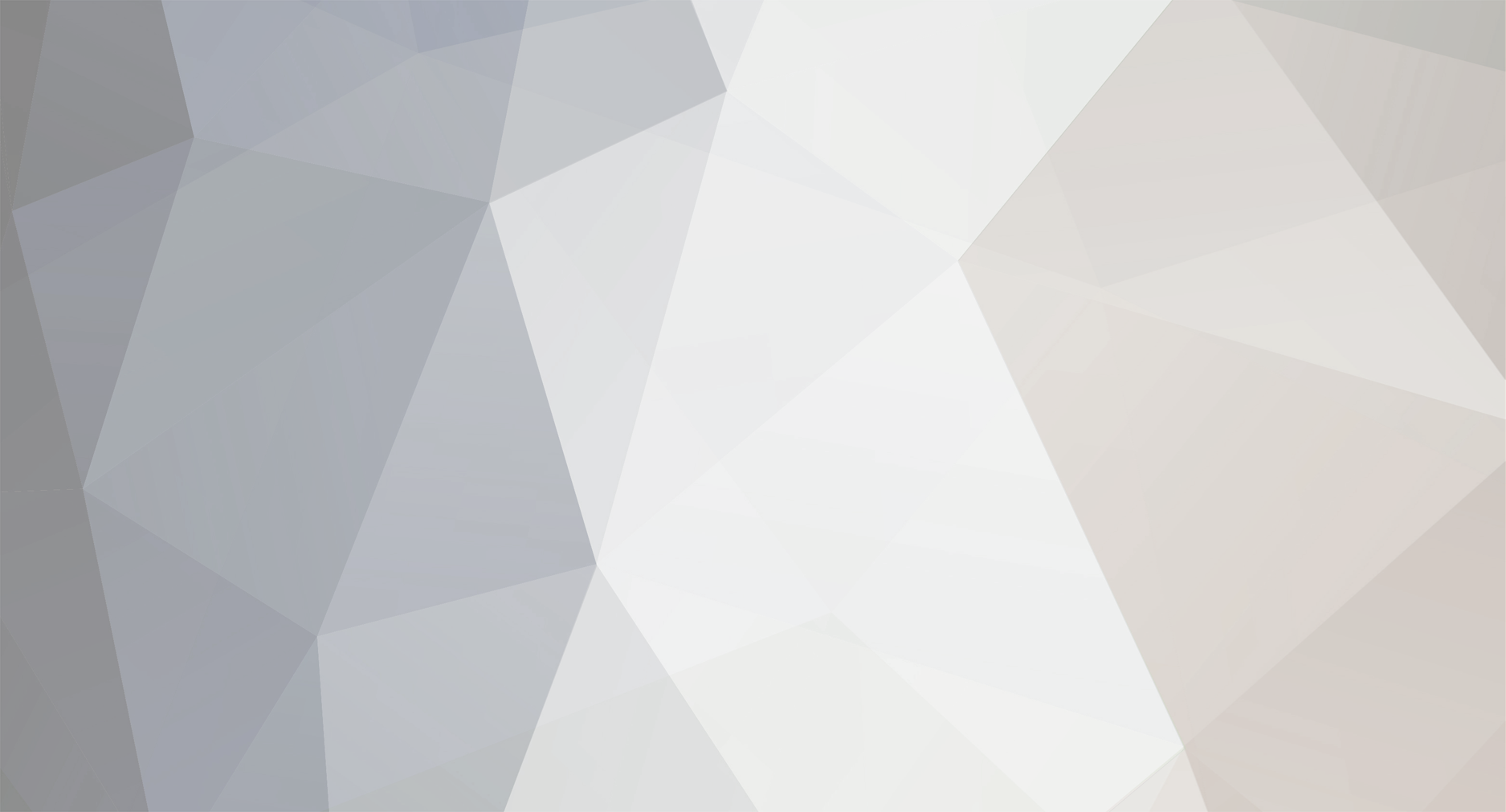
Lkuest
Members-
Posts
317 -
Joined
-
Last visited
-
Days Won
5
Content Type
Profiles
Forums
Store
Gallery
Downloads
Calendar
C-130 Hercules News
Everything posted by Lkuest
-
I'm assuming a BARV is a Bleed Air Regulator Valve, and when you say "accompanied of TIT", you mean TIT dropped with torque, and not increased. The TD Amp's job is not to maintain power, but to maintain temperature based on the throttle setting. If the TIT is low while the TD Amp is in AUTO, then there is an error with a signal being supplied to the TD Amp, or there is an error with the Amp itself, a setting or malfunction, When you lose air, you lose power for two reasons. Jet engines love more air, both to increase power through expansion, and also to keep the combustion chamber cool. If you lose air, you lose power immediately since there is less air to expand, but also the loss of cooling air causes an increase in TIT, and results in the TD Amp to pull fuel back. This all produces a loss of torque and fuel flow while maintaining TIT. I cannot emphasize this enough, before doing anything, ensure your indications are accurate! TIT to within 6 degrees of actual as measured with a test set and all thermocouples verified good and connected properly. Torque indicator recalibrated and set to within 50 in-lbs of actual. Swap the Fuel Flow gauge with a known good one for good measure, then reverify the problem. Why the engine goes to normal when the Regulator Valve gets turned off is interesting. If the TIT was to remain normal, I would say the Regulator Valve was mis-tuned and the TD Amp was doing its job. Since the TIT is also low, we know the TD Amp is not doing its job (above crossover only). Even if the Regulator was malfunctioning, the TD Amp is definitely having an issue. The fact that the valve affects the TD System operation means they may be connected electrically in some way, like the power/signal wires may be chafing together. If the fuel control was perfectly tuned and we suspected the TD Amp was just inop, we would see high TIT with bleed air open, not low TIT. To check if it is an electrical problem, check power going to the TD Amp using a TD Amp Test Set, then cycle the bleed air valve and see if the power at the Amp changes. There are two types of power going to the Amp, so check them both. If I misunderstood you, and the TIT is high during the malfunction, and not low, then you have a TD Amp malfunction AND a bleed air regulating valve balance issue causing you to lose 2500 in-lbs.
-
Is the engine operating within limits? If so, disregard the differences as there is no limit for symmetrical operation in HSGI. Otherwise, you might consider checking rigging with the valve housing, or swap it with a known good valve housing, as long as the Fuel Control has already been eliminated. I know the prop causing fuel flow problems sounds weird, but I've had it cause stranger problems in HSGI.
-
I'm sure if the boss wants it to get done, it will get done one way or another. Seriously though, it depends. If you're looking for justification for an argument, the 61-series job guides are meant to be used by the specialists, so if that's the tech data being used, the engine folks are doing it. If the 12-series job guides are being used, then it's APG doing the check. By concept, APG is in charge of all routine maintenance. In practice though, if an engine troop doesn't have work, he's doing it. If engine troops are busy, it could go either way. Not sure if it really matters who does it, as long as they do it right. I've seen a few APG folks grab the wrong color can, so do what your comfort allows you to do.
-
I agree, all you can really do is a check first stage rotor blades, balance, and a good signature check. If all those are good, you might just be having bad luck. We've gotten quite a few that crack again and again, mostly due to poor weld repairs on the replacement supports. If the signature run is good, you might try installing a known brand-new case and see if it still cracks. Of note, the rear bearing support case wasn't originally designed to mount a tailpipe, so the extra length acts as a cantilever to amplify vibrations through the weak points. The support case is Allison, and the tailpipe is Lockheed. That's why vibration is the top cause, but also explains why you might have nothing wrong with the rotating assembly and still get cracks.
-
Agreed. If you are ops checking the system, the chances are you have a malfunction somewhere in the indication or fuel/TD systems, or you wouldn't be ops checking it. If the malfunction is in the fuel/TD system, the situation is at least stabilized in-flight with the appropriate procedure. When you start adding variables to a stable situation, such as enabling and disabling the system with various bleed air loads and throttle positions, you can make things much worse, such as a power surge/overtemp or an engine flameout, or any sudden power change in-between. On the ground, neither are dire events when the aircraft is safely parked.
-
#3 engine unable to shutdown normally (negative fuel cut)
Lkuest replied to moe986's topic in C-130 Technical
Have you tried the switch that tells the Geneva lock to close? It can be tempermental. I've had the same problem before in ground stop. Hitting the quadrant did the trick in my case, which means switch, but it could outright fail as well. There's a lot of wiring and components in the system, so I'd recommend hunting the problem down using a wiring schematic if it isn't the switch. -
How does the starter break? Does it shear, seize, or otherwise fail to engage? There's a couple simple possibilities, but you'll have to forgive the suggestions if they seem too accusatory. Your installation method may be incorrect, such as running the starters with shipping fluid instead of engine oil, or even running the starters dry. Some people don't realize that starters without dipsticks may still need to be drained and serviced if there is a fill port on the left side. Another simple possibility may be your supplier building defective starters. either could possibly cause the starters to sieze. Certain part numbered starters use a friction seal that exerts resistive friction against a thrust assembly. If the friction seal is worn, damaged, or incorrect, it will allow the starter to freespin, and possibly shell out under high RPM. There is a procedure in USAF tech data to test the friction seal. Another simple cause may be a clogged return line from the starter back to the starter control valve. This would cause the starters to shear excessively due to too much torque being exerted through the starter shaft shear point. Of course, a damaged propeller brake can cause the starter to shear as well. The key will be to check the engine start times. If the engine starts quickly and shears, it's getting too much air. If engine starts tend to be slow, the prop break and/or gearbox may be failing internally. The worst possibility though would indeed be vibration. Since the starter is in the center of all the RGB harmonics, it tends to get quite a beating if the engine isn't quite right. If you run an engine signature and come up good, you may just have a run of defective starters, and I would recommend installing a starter you know to be reliable. I have seen an engine vibrate so much that it shook the starter nuts loose, and the starter ended up hanging on by just two nuts. The starter was still good though, so that might give you an indication of how much vibration one can take, but that of course may have more to do with the style of starter more than anything. I wouldn't suspect torquemeter shaft unless either a signature run/torquemeter runout confirms it, or your torquemeter pickup has evidence of grinding on it. You can test the power section for internal binding by releasing the prop brake using the air adapter and manually turning the engine over to listen for any abnormal noises. Rubbing blades would usually manifest as sparks shooting out of the tailpipe at night though, and internal engine failure should show up as significant oil quantity or pressure loss. I'm sure I'm missing something if someone else would like to chime in.
-
With high sustained RPM above flight idle, the cause is almost always with the propeller. The prop acts as an air brake to slow the engine down. In this case, the propeller is not slowing the engine down as much as needed. As the RPM increases roughly 5% above 100%, the fuel control realizes that the propeller is malfunctioning, then kicks in to cut fuel until the engine no longer accelerates higher. This is why you have high RPM with low torque and TIT. It all fits with a propeller failure, whether it is rigging, synchrophaser, valvehousing, pumphousing, or internal leakage. I have read some very good responses here, and I would recommend you heed all of them. You cannot replace just the dome by itself. Not only will your feather blade angle not be 100% calibrated, but your incorrect gear backlash may cause irreparable damage to the propeller blade gearing, and I wouldn't want to see that fail in-flight. I do recommend physically removing the synchrophaser prior to the run as NATOPS has suggested. This is because the synchrophaser is sending out two signals to the Speed Bias servo motor, a control input, and a reference signal. Selecting Mechanical governing only disconnects the reference, so if there is a significant malfunction with the Synchrophaser, it could change RPM, even in mechanical. Slow throttle anticipation and low pitch stop not retracting are both consistent with inadequate hydraulic system pressure, either caused by bad pumps or damaged/missing seals. I would like to note that a significant cause of maintenance issues is other maintenance. You have listed many things that you have done. It is somewhat likely that someone forgot/damaged a seal on buildup. If you kept the same pump housing through all of this, you may have damaged the small seals while pressing the pump housing onto the new prop rotating assembly. The same guy that built up the original propeller may have made the same mistakes with the new one. There's just so much that could've gone wrong with the maintenance that could easily explain the issues you are still having. My recommendation would be to install a propeller that you know works on #4 position, and work from there. There is just no way an engine can cause high RPM with low TIT, unless the rigging is very faulty.
-
When you leave on a journey and look at a map, how do you know how far you have traveled without knowing the exactly where you started? The torque shaft twists with the forces of the engine spinning one direction, and the propeller trying to slow the engine down. The more power the engine puts out, the more the shaft twists. How would you measure it though, without knowing what an un-twisted shaft looks like? This is why we have two shafts. One shaft transmits the torque, and twists while doing it, and the other shaft is a reference for the original, zero torque position. The bigger difference between the twisted shaft and the untwisted shaft, the larger the torque required to make that difference, and the higher reading we get on the indicator.
-
The first thing to do that is absolutely critical is to not fully trust the indicators. You must have a digital tachometer plugged in that can give you RPM to within 0.1% RPM. Next, tune all 4 propellers so that they are all within 0.2% of 100%. The purpose is to put minimum stress through the valve housing clutch assembly to prevent slippage and "bias". Also know that, whatever your digital tachometer reads, your aircraft RPM indicator must read accurate to within 1% rpm. Now, when the synchrophaser system is not malfunctioning, what do all four RPM indicators read? During the malfunction, what do all four RPM indicators read with #2 as a master? #3 as a master? No master selected? Hypothetically, if there was a defect in #2 pulse generator circuit, the synchrophaser would think #2 is slowing down, and would cause #1,3,4 to reduce to 98% suddenly, even though #2 is at 100%. In this same case, if you select #3 as a master, #1 and #4 would both remain at 100% while #2 would increase to 102%. While this case would possibly indicate a defective pulse generator, it is more likely bad wiring with the defective master propeller within the pulse generator electrical circuit. It is difficult to trace an intermittent problem, but we've had issues with the pulse generator electrical circuit short to ground within the 6-pin conduit itself, and the only way we could see it was to disconnect it from the propeller, check the pulse generator pins to ground while we move and yank on the conduit to allow it to hit that sweet spot where it just barely shorts out. You could also check for recessed or broken pins in the conduit. Of course, as PJVR recommends, a sync test set would help out immensely, but if one is not available, you can still make do with just a wiring schematic. It may prove difficult or impossible to guess further on a cause of the malfunction without knowing exactly what the RPMs of all 4 propellers are doing during the malfunction, with both #2 and #3 selected as a master, when no master is selected, and assurances that all 4 governors are set to 100% within 0.2% RPM. Not correctly setting mechanical RPM usually causes gradual malfunctions instead of sudden ones, but if the mechanical settings are off by a lot, you may just have a power issue to the synchrophaser, and propellers would return to the mechanical setting without the syncrophaser receiving power.
-
How can you tell it is disengaging? Are you saying that the slaves are normally a different RPM than the master? Also, is this "disengagement" sudden, or gradual?
-
The starter control valve regulates at around 39 psi, so you'd think there would be no difference between "on" and "Override" at the starter. There is, however, a difference at the starter control valve itself. It has to do with the "rise rate" of air pressure, which allows smooth and prompt engagement of the starter clutch at just the correct starter turbine RPM. Basically, the full 70+ psi opens the starter control valve more quickly. If the valve opens too slowly, and the starter turbine is allowed to spin up to an RPM too high before the force from the air forces clutch engagement. The starter control valve can be adjusted, though, to tune the rise rate to the desired manifold pressure. There are Lockheed service news bulletins that touch on it a bit, likeV13No1, V17No3, and V24No4, but I'm struggling to remember if there is one that addresses "on" vs "Override" specifically. I could swear there is one though, it just escapes me at the moment.
-
Locking the TD during fuel governing and pitch lock check
Lkuest replied to tenten's topic in C-130 Technical
Tenten, I understand your frustration, but there really is no hope in logically understanding the system without looking at the schematic. Doing so allows you a much greater understanding of why the system behaves the way it does under all conditions. In this specific case, it is important to understand that the TD Valve brake does not get energized in order to engage, it actually is energized into the "released" position. If the TD Valve brake solenoid loses power, it moves the the "applied' position, locking in the fuel correction. In this case, if you were to move the TD switch to the "locked" position, this energizes the brake lock relay, which is meant to cut the power going from the brake lock relay switch to the TD Valve brake solenoid. It just so happens that, below 66 degrees, the coordinator also sends power to the TD valve brake solenoid, thus, the brake is still "energized" into the released position. Why select locked below crossover then? Because when the Brake Lock relay becomes energized, it sends power to the limit selector relay, telling the TD Amp to ignore Bias and Slope and to only start pulling fuel once the TD system reaches the max limit, which on a -15 engine is 1077. Once you advance the throttle above 66 degrees, the power no longer comes from the coordinator to release the TD Valve brake solenoid, and lock the brake. So, is the brake locked? Nope. The electronic fuel correction light is on below crossover due to being below the 66 degree switch, but remains on while advancing throttles above crossover because the brake lockout relay is already energized by the below 66 degree switch, which not only provides its own circuit once energized below crossover, but also powers the electronic fuel correction light, and also the TD Valve brake solenoid, keeping the TD Valve brake released. In short, placing the TD Control Switch to "Locked" below crossover accomplishes nothing other than providing overtemp protection, and the brake is not locked at any time, no matter the throttle position. If the brake lockout relay is energized by the coordinator below 66 degrees before going to "locked", it always powers the TD valve brake to release. You must allow the coordinator to go above the 66 degree switch in order to prevent the brake lockout relay from energizing before the brake lock relay. You do this by first putting the TD switch to "Auto", advance above crossover, then go to "Locked". This prevents the brake lockout relay from keeping itself energized, and removes all possible power sources from the TD Valve brake solenoid, allowing it to apply and lock fuel correction. Now, for your second question, if the system were to be locked above crossover, and the throttle were moved below crossover, would the brake hold below crossover? The answer is, yes. If the brake lock relay becomes energized without the brake lockout relay first becoming energized, the brake lock relay prevents the 66 degree switch from ever receiving power, thus it cannot power the TD valve brake solenoid to release it. It also does not have power to energize the electronic fuel correction light. This is why the light stays off below crossover once the TD system is locked above crossover. How can you "reset" the system? Downspeed the motor. This allows the 94% switch to energize the brake lockout relay, restoring power to the 66 degree switch and the TD Valve brake solenoid to the released position. Or, you could just put the TD switch back to Auto, which restores power to the brake lockout relay. Then, you'd have to advance the throttle above 66 degrees to deenergize the brake lockout relay in order to lock the TD valve again. -
Locking the TD during fuel governing and pitch lock check
Lkuest replied to tenten's topic in C-130 Technical
Tenten, Below crossover, the brake lock function is locked out through the brake lockout relay, so as pjvr states, going to locked below crossover would only have overtemp protection and nothing more. This same relay kicks in when you overtemp in locked, and that's why the fuel correction light stays on after overtemp. Potentially, you could have a 100 rich and 70 lean engines on opposite wings cause issues with pulling the throttles back unevenly, but you still have that problem because the props don't exactly all pitchlock at the same blade angle anyway, so the procedure may be just as effective regardless of what throttle position you flip the switch to locked. I prefer going to locked above crossover just to eliminate variables, but both procedures may give you the same information for the op check. -
why the engines be started in low speed ground idle?
Lkuest replied to MINHAS866's topic in C-130 Technical
I agree this can be an indicator of fuel control health, but please don't take it for more than it is. Even if the engine will low speed, you never know if the fuel governor is correctly set anyway without doing the correct ops check, so the LSGI operation is of low value as an indicator you have overspeed protection. Maintenance performs the ops check every HSC and ISO, so you should be covered. Sure, something could break in-between, but it's not as simple as that. The flyweights that tell the governor it is overspeeding are the same flyweights that assist the speed servo valve to increase fuel flow during engine starting, so if that mechanism were malfunctioning, you would likely see more severe issues with fuel flow. The only fuel governor components not needed by the speed servo valve are a spring and a shaft. The only true ops check for fuel cutoff is to do a fuel governor/pitchlock check. If the you are willing to tail swap for an engine that fails to low speed, you should be prepared to allow maintenance to do an official ops check of the fuel control to prevent a tail swap, especially when the LSGI solenoid is exempted on the MESL. In my experience, the entire LSGI system is infinitely less reliable than the fuel governor system. By all means, call maintenance out, but please, let us do an official ops check before refusing the aircraft. -
Ronc, Have you seen this problem with the new gaskets, or was it with the old copper ones? I haven't had any problems with the acceleration bleed pad gaskets since we went to the new material, so I'd be interested if you've had issues with the new material. I have seen many bleed pad gaskets blown out when they were copper though. Many times all we saw was either a low power engine, or copper laying around the bottom of the nacelle.
-
Could be a long shot, but you might consider an overheat detector might be lying to you. Also, if you can't pinpoint a specific clamp, you might just re-torque all of them for good measure and see if the problem goes away. Just as NATOPS1 says, I've had good luck troubleshooting air leaks by noting the difference between a bleed down with the problem motor and a bleed down with all of the other motors. In this case, that might pinpoint which side of the check valve your leak is on. Also, depending on your circumstances, an infrared camera could work wonders on a job like that. I understand you're not at home station, but if your plane isn't flying anywhere, an infrared camera might be part of your requested supplies kit. It will most definitely help you pinpoint those little leaks.
-
I was agreeing with Ramrod about the interval too, 15 days. In your case though, It might be more appropriate to address it from a standpoint of leakage limitations. As long as your tec's are checking the propeller thoroughly for leaks, I wouldn't worry about "trace/evidence" unless the engine is ingesting enough hydraulic fluid to become noticeable in the Air Conditioning. The propeller control is allowed to leak 1 drop every 45 seconds, whether operating or static. Nothing else is allowed to leak, unless it's freezing outside, in which case, warm the propeller up first before doing a fluid leak inspection. Sometimes, when people "X" the props, some fluid might stream out. This is normal due to accumulation from minor seepage collecting in the rear spinner, then suddenly being released by the drain holes located half-way between the blades on the rear spinner.
-
I agree with Ramrod. The key is that, when you check using the atmospheric sump, you are checking the servicing level in a similar way to how the aircrew operate the prop, that is, with a pressure and scavenge pump running. The barrel and pressurized sump both overflow into the atmospheric (beta feedback shaft and sump relief valve), so if you have the right amount of fluid in the atmospheric, your prop should be serviced properly in the barrel and pressurized sump. This requires that #1 blade point to the top. The problem is when the pitchlock regulator orifice cups become clogged and doesn't properly fill the barrel. The pressurized sump will always be full, and the atmospheric will always be empty. The pressurized sump is inaccurate because it is not an accurate reflection of how much fluid is in the barrel. Maintainers find the pressurized sump comforting because they like to think the prop is telling them exactly how many quarts are required instead of servicing the atmospheric sump 5cc at a time.
-
I'm going to go with Flight Idle & Beta Shaft.
-
Forgive me, but it is very difficult to troubleshoot a problem this complex without being there in-person, so please feel free to disagree with me on anything. It sounds like you have so far swapped the TD Amp, TD Valve, Coordinator, Speed Sensitive Control, Relay Box, TD Null Relay, Thermocouples, Y-Lead, T-Block, thermocouple harnesses, and J3 lead from Amp to TD Valve. The only things left are the Left-Hand Wiring Harness (Spider Box), or wiring between the TD Amp, J-Box, and Firewall. The last thing I would recommend is swap engines between #2 and #3 and see if the problem stays or moves. It's a big job for just diagnosing, but it would tell you if aircraft wiring is the cause, or if the engine is defective. If the problem stays with the engine, you may have a new part that is bad. It may seem like a big job to do on just the suggestion from someone on the internet, but you've already done everything else that causes this. Do you have any engineering support from Lockheed to help you?
-
It seems the only thing you have not yet swapped to another engine is the Speed Sensitive Control. Let me see if I read your problem correctly. You advance the throttle up to flight idle, and I am guessing #2 engine is higher in TIT than the other 3. Then, you advance the throttle up to crossover, and TIT becomes 840. You move the throttle up above crossover, and the TIT becomes 790, but then TIT goes back up by itself. Do I have this correct? Does the light pop back on when temperature shoots back up, or does the light stay off all the time above crossover? Is there any other malfunction, such as the TD Valve Brake Check, Temp Control Check, Temp limiting? Does this still happen with the A/C Instrument and Engine Fuel Control Invertor in the opposite position (D/C instead of A/C, or A/C instead of D/C)? What is your Auto Start temp? What is your Null Start Temp? When TIT moves up, does torque and fuel flow also increase?
-
Well, if it's not the J3 lead, the cables between the coordinator and the Amp, or the Relay Box, then I'm thinking it is an issue with the power being supplied to the Amp. There is also a Temp Control Relay you might swap with #3 to see if that's causing it. It is located inside the cargo compartment. Just follow the wiring schematic to figure out where it is if you can't find it. Also, if the fuel control is failing, it may just be becoming too rich for the TD valve to take enough fuel. If this were the case, the fuel control would be more than 100 rich.
-
I see you mention all TD System components were swapped with #3. Did you also swap the TD Valve?
-
Most likely the 62nd name will transfer to what is currently the 48th, because of the heritage. That's the story I got anyway.