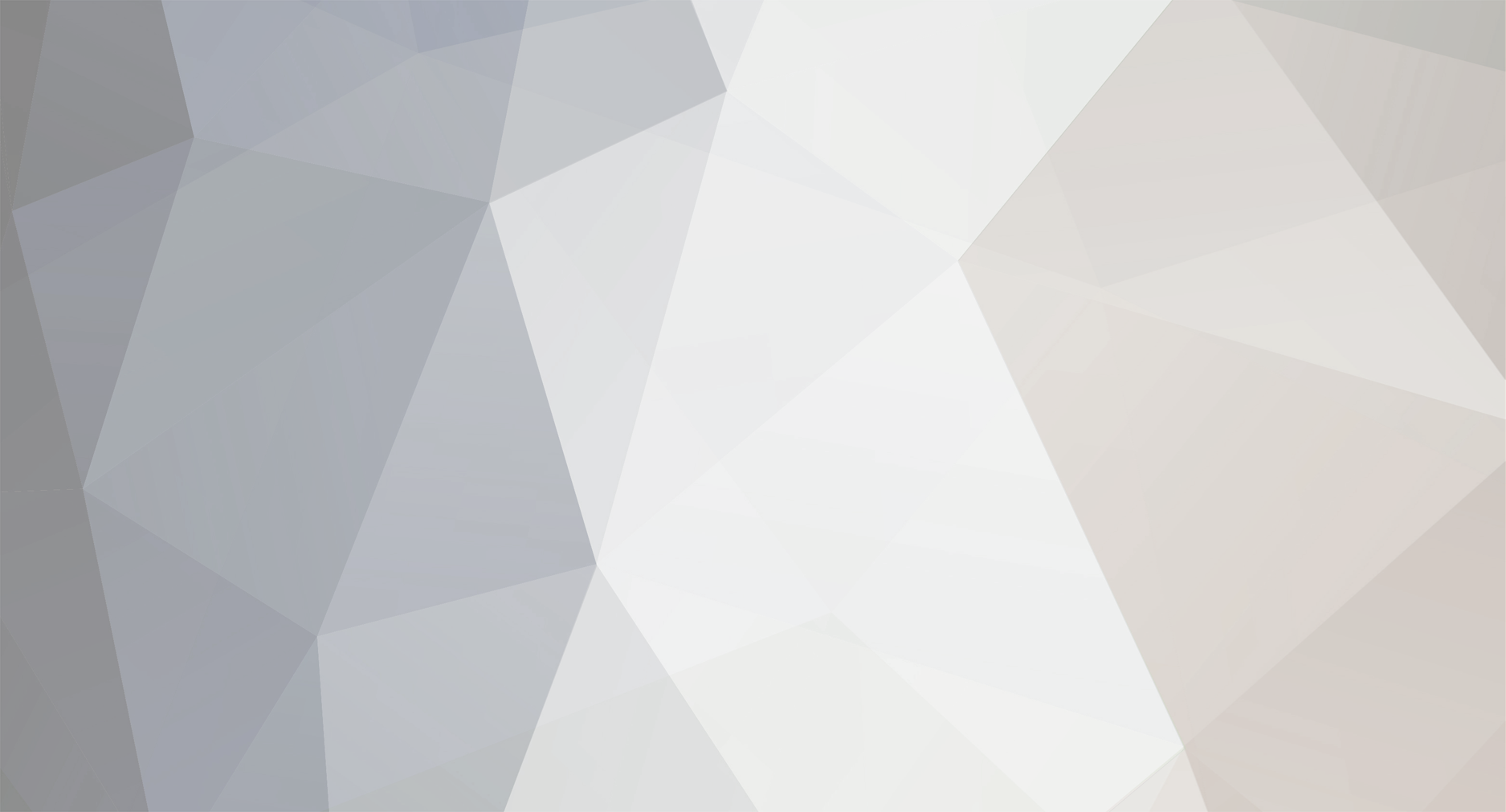
tenten
Members-
Posts
195 -
Joined
-
Last visited
-
Days Won
1
Content Type
Profiles
Forums
Store
Gallery
Downloads
Calendar
C-130 Hercules News
Everything posted by tenten
-
To my understanding this pressure reducing to 45psi will help only if one solenoid (solenoid of the Engine Bleed Air Regulator and Shutoff Valve is malfunctioning in which the valve is behaving as in “ONâ€â€ position, therefore when the main manifold is higher than 45psi the valve tends to go to the close position preventing a sufficient amount of air to enter. By reducing the pressure manifold to 45 the valve will tends to take the full open position especially during engine start thus making start possible. Note: In Override position both solenoid should be energized. (Valve fully opened) In ON position: solenoid (A) energized, solenoid ( deenergized. (Valve modulate to maintain 50 ±7 psi) In Off position: Both solenoids deenergized. (Valve closed).
-
What you are asking for can be obtained by performing "Engine Performance Check-Percent Efficiency". This precise power run-up normally carried out by maintenance whenever the engine instruments appear to be indicating abnormal values while performing the Takeoff Power Check, or whenever there is reason to suspect the engine will not produce takeoff power. The procedures to perform this check in our technical manuals is located in TM 382C-2-3 section 9 (Engine Operational Checkout Procedures). And as "NATOPS1" state the minimum excepted is 95%.
-
Think of fuel nozzles; We do have a case that the work done by our repair and testing facility is not according to the standard. The finding was after getting reports that some of our turbines are suffering from burn through and the cause was found to be "improper fuel nozzles pattern" (based on testing the nozzles attached). Case approved by sending some of "ready to be useed nozzles" to other agency the result was 70% having a bad spry pattern. With a bad nozzles some times things become worse when technicians finger TD valve to increases temp a few deg to meet the limits.
-
Ess Ac Bus is the common source for both the synchrophaser and the Ac instrument Bus (Torque meter indicator) and both of them very sensitive to power source; a good idea to switch "off" no 2 generator during the malfunction to isolate the defect.
-
Yes, Ben Legere…. The possibility of intermittent malfunction of the Up Contact of the Landing Gear Lever is there in which electrical power will find its bath to close the Normal brake selector valve leaving the aircraft for some time without any braking system (since the other valve "emergency" is already closed). BUT ……..the nature of the defect as been described (hitting only with low speeds) is weakening your BET to win (no relation between speed and the valve closing through this circuit. I am supporting the possibility of electrical power gets its way to Pin "F" as mentioned by NATOPS1 either through internal malfunction within the touchdown relay (B3 / B2) or through any momentarily electrical leakage found its way to Pin "F" Relation of aircraft signaled to be as in flight(while in ground) and the speed of 15 knots is there; in which the override feature-within he anti skid system-will prevent normal brake to be inoperative till speed dropped to 15 or below.
-
Yes, SEFEGeorge that's the one. It manufactured in deferent names….. Long time been dealing with this Nav "unit", unreliable and misbehave most of the time.
-
Having the same issue three weeks ago, and since our books doesn’t have a direct approval of the case, the Aux pump had been changed, the new pump(zero hours) worked fine with us and was maintaining the 3000 where ever the elevator resting. Therefore convince ALL of them to accept the drop or…… find another good pump to make “Switch Operators†happy. TIP: Adjusting the pump pressure (caped adjustment) failed to recover the drop during ground connection to utility; it only increases the pressure to 3300 once the pump is servicing its own system.
-
Be careful!!!!! HE is telling us that oil is not coming to the pressure line. Therefore we should not advise or think to jumper oil pressure switch.
-
Not specialist but trying to help on the bases of GCP if system is similar. Loosing/tripping voltage and frequency once generator is connected to the bus means that “the generator is automatically disabledâ€. Disabling the generator is a function of GCP/GCU once receiving abnormal feedback signals such as: 1- Overvoltage condition sensed by overvoltage circuit within the GCP (if the case is actual it can be seen on the indicator as a voltage overshooting at the moment of switching ON. Possible causes: a- Generator malfunction. b- Voltage regulator malfunction. c- GCP malfunction. 2- Ground Fault condition (30 amps deferential) sensed by Ground Fault Transformers, there function is to monitor Gen Contactor wires (If Gen Output is low) they will feed back to the GCP to take the generator off the line in addition to removing the excitation field. Possible causes: a- Ground Fault Transformers malfunction. b- Contactor wires malfunction.... Gen. Output circuit…. (Beyond my level to spot how and where to check) Just one Q; Was the malfunction accord once the generator takes the load of particular Bus or any Bus?
-
Oil temp during the cycling (as reported) within the normal range; once temp hits the 80 oil cooler then will take full open position, and as oil cooled and reach the 60, the cooler then will take the full closed position. Note: ignoring the cycling leads (in one case) for the actuator to fail; hence we got the message. Both types of thermostat are in used in our aircrafts with variety of parts numbers (most of them as I know solid-state types). Which part numbers or type caught on the act?.... I need to check defects history.(weekends Friday and Saturday on the HOT regions).
-
We are attacked by the cycling of oil cooler flap during cruise, the cycling is taken place every 5 to 10 minutes (fully closed X fully opened), long time when I was lucky, the most was solved by replacing the temp control thermostat in these days and age it cost me three “shoots†to keep it calm. Appreciate any idea/tips/special ground check to avoid the ugly phrase “Defect Repeated THREEE timesâ€.
-
No doubt, both the light and the engine to rotate should be within 5 seconds, starting from the moment the pilot depressing the engine ground start switch. The confusion of the two “CAUTION†stated on the FM might come from the way the FM wants to state the two cases required to discontinue the start: Case 1: From the time of “depressing†if the light doesn’t come ON within 5 sec discontinue the start (hidden: Regardless of engine rotation). Case 2: After depressing and light ON; engine rotation should be within 5 seconds. (Hidden: Even with the light “ON†if no engine rotation discontinue the start within the 5 sec). So the light “ON†in the second FM caution statement is not a starting point of timing.
-
Hint: Rudder diverter button doesn’t have mechanical detent to remain engaged; it should be depressed and held against spring load to provide the full pressure. Any idea when this feature is to be used??
-
Yes, SEFEGeorge Pulling the wing flap control C/B and setting the flap lever to the desired position to provide the proper rudder boost pressure (3000) is a procedure on the FM and was mentioned during the following emergencies and non-standard operation procedures: 1- During loss of flap electrical control system. 2- During manual flap extension. 3- During Flaps up Take-Off. As well as it is under warning on SMP 777 Quoting: WARNING Flaps up air minimum control speed charts assume effective rudder boost pressure of 3,000 PSI. To ensure rudder high boost operation, pull the wing flap control circuit breaker and position the flaps control lever to a setting greater than 21 percent.
-
“The Airplane Model” is C-130H The “382C-14E” = is the “Airplane Configuration Code” (maybe the “14E” for sup-modification code)
-
Caution Avoid abrupt or full rudder deflection with FLAPS lever positioned 15 percent or greater (high rudder boost) and air speed 210 KIAS or greater. (Ref.FM 382C-14E sec1 limitations page 5) To my understanding; the point of having this system (two range of rudder control pressure full and reduced) is: 1- To have full authority of rudder control (full pressure) during T/off and Landing (low speeds). 2- To have reduce authority/less sensitivity during climb/cruise (high speeds). Hence that high pressure (3,000) if used during high speed leads the rudder control to be very sensitive to induce a big amount of yow for any small input (hi speed/hi pressure) which may leads - if sudden or full rudder deflection is committed - to damage the rudder mechanical linkage or leading the aircraft to inter unintentionally a prohibited manoeuvring zone. For system to work engineering set up a diverter valve, reducer, transmitter and a switch actuated at 15 % and above on the flap control lever (Hence take off and landing is normally accomplish with flap lever more than 15%). That 15% switch will close the circuit through (C/B 28v Ess Dc) once flap lever15% or above leading the diverter valve to be energized thus bypassing the reducer and directly providing full system pressure (3,000psi). Once flap lever is raised up (after takeoff) to less than 15% electrical continuity will be cut-off thus diverter valve will be de-energized leading the hydraulic pressure to be routed through the reducer (1275 psi). Simply: Any time lever less than 15%, C/B out, or loss of Ess Dc power; will lead the diverter valve to be de-energized = reduce pressure 1275 psi. Tips during flight: (If failed HIGH) rudder input to be used smoothly and with caution during high speed; (if both failed LOW) charted air minimum control speed to be increased 13 knots. For only one system failed low, I haven’t got reference of how much speed to be increased.
-
To my opinion you might have an issue of TD system malfunction accompanied with play on the pump housing due to warn out/looseness of anti-rotation bracket. (Sudden increase of power twists the pump housing…. activating the NTS system …….. leading the RPM to drop.) But again the value of power increase appeared to me beyond the ability of TD malfunction to produce, unless I am wrong on this understanding.
-
KJamison, We apologize for not having the direct answer to brother HercRep. Until tomorrow; no harm to discuss one of the major affect of flying without APU.
-
Thanks victorp1 for clearing up the point; so it is an individual operator restriction (MEL) and might be based on some extra equipment added in some aircrafts. NOTE: The FAA (MMEL) rev.18 dated 1994, and the Belgian air force (MEL) dated JUL 2003, along with our (MEL) allowing us to fly/dispatch the aircraft without APU/ATM generator with NO issue of VMC.
-
Seems “some good books” are not updated concerning flying without APU generator and the VMC restriction issue.
-
apexlined, We are using FM 382C-14E for military registered aircrafts and OM 282G-65C for a civil registered aircraft; And in both they do have the two cautions (word for word as you stated in your post); But also in both they did not state the technical reason behind the limits. The one that I sent as a reference which may solve 50% of your question is not in used for our aircrafts. The fact that most of the books dealing with the operators/maintainers with the words DO and DONT without giving the reason behind is unavoidable; thus sometimes making life hard to find out. NATOPS1, I agree 110% of the technical reason that you bring our attentions to, on the fact that “NTS†is mechanically deactivated during Ground Range (cammed-out) in which the safety coupling during normal ground shutdown is not backed-up by that system, but this fact will not satisfy the question of brother apexlined; he is looking for a direct authorized technical reference concerning the effect of aircraft velocity on the shutting down or the low speed selection. In another words he is looking for the velocity effect factor.
-
Quoting: CAUTION Engine shutdown should not be accomplished when taxi speed, wind velocity, or a combination of wind velocity and taxi speed is greater than 20 knots. Engine shutdown under these conditions may damage the safety coupling. When doubt exists as to the effective speed, the shutdown should be delayed. Ref. TO 1C-130H-1 (Flight Manual) (Date of Issue 1 August 2002) (Section 2 page 91). For the reason behind the low speed selection limit, I couldn't find any reference yet.
-
“May” and “Might” that I used is very weak to give you “book reference”, it is my understanding to the system, but I will try my best to find out and let you know.
-
As brothers mentioned with some details. Location: The solenoid operated brake (TD valve brake) is a part of the TD Valve Unit (the brake is located within the TD motor-generator shaft) Function: Used to lock (stop) the movement of the motor shaft which control the Bypass Control Needle Valve (Null orifice) when switch selected to LOCKED. Operation: In Null and Auto the brake is energized to release (against spring load) and to let the motor shaft free to take the proper position. The LOCKED position (which normally selected with throttles above x-over to maintain a specified corrected position) the solenoid operated brake will be de-energized thus bushed mechanically by the spring action to lock the motor shaft ; and will remain locked until signalled (energized) by TD amp if an over temperature occurred (+1077C) or switch repositioned to Auto or Null.