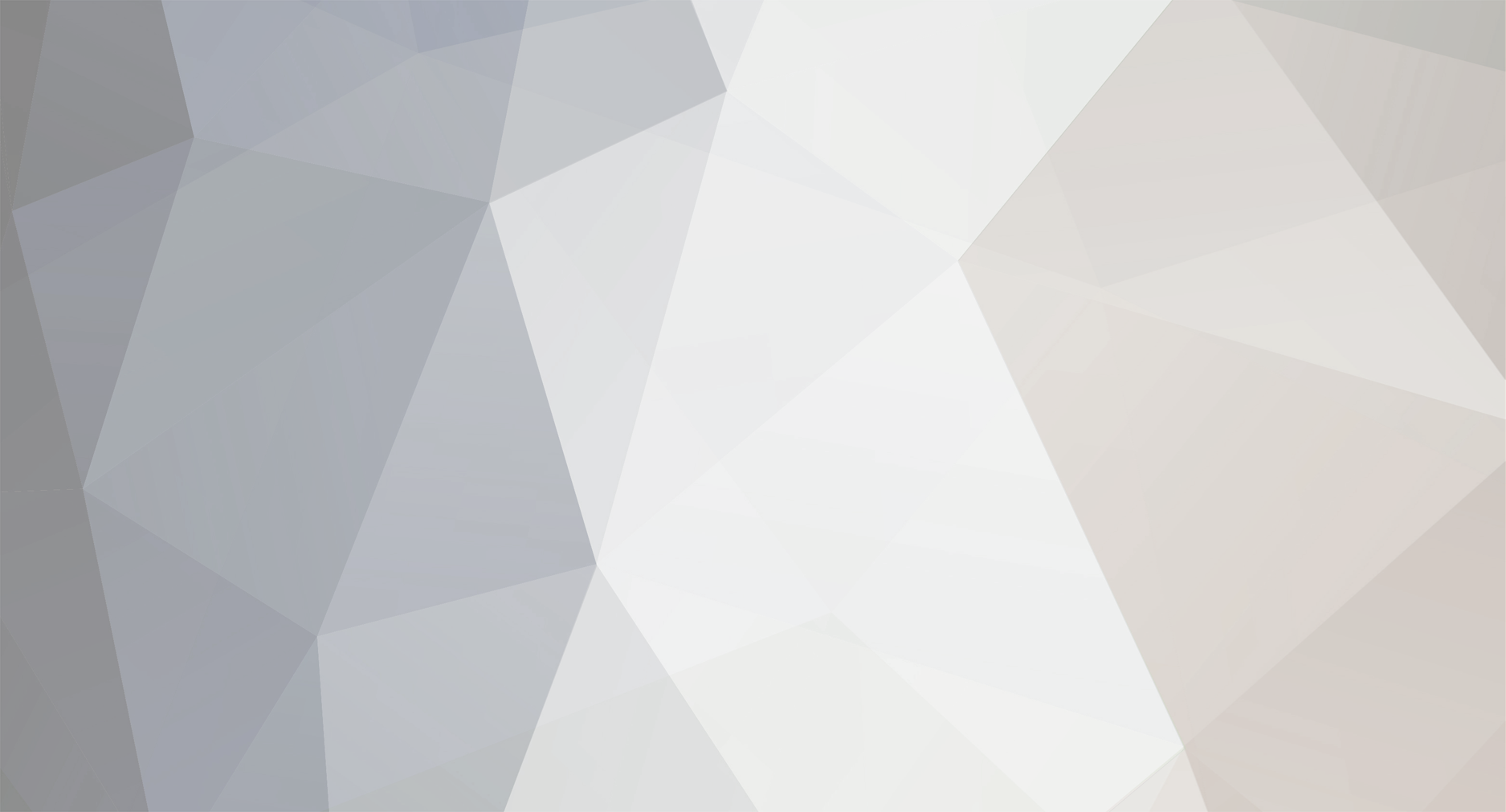
victorp1
Members-
Posts
53 -
Joined
-
Last visited
-
Days Won
1
Content Type
Profiles
Forums
Store
Gallery
Downloads
Calendar
C-130 Hercules News
Everything posted by victorp1
-
That was a term used when checking to see if the slave propellers would follow the selected master when its throttle was retarded to flight idle during a ground synchrophaser check. You would see what RPM the slaves would droop to when the master RPM was reduced. The following is an example from a procedure for a tube-type sysnchrpahser system. "Retard No. 2 throttle to the FLIGHT IDLE position. RESULT: No. 2 engine RPM should decrease to the RPM shown in figure x-x. Within 15 seconds of completion of the throttle movement, the RPM of the slave engines should decrease by 1 to 3 percent."
-
I think the following would apply: 1. If the aircraft were direct purchase from Lockheed use the SMP. 2. If they were aquired through FMS use USAF publications.
-
I have had some conversations with representives of Hamilton Sundstran about the valve housings and here is a short reply I got: "The standard governor has few parts, but it reacts slower and is less reliable. Standard Governor Pilot Valve Operation: Either the alpha shaft or the mechanical flyweights in the speed-sensing governor physically adjusts the position of the pilot valve to direct the incoming main pump pressure to the increase or decrease pitch lines. Position of the pilot valve aligns ports in the pilot valve with ports in the valve body and serves to regulate or meter the incoming pump pressure as it is directed to the increase or decrease pitch lines. Pressure in these lines will control the dome piston position and ultimately blade angle. Servo Governor Pilot Valve Operation: Either the alpha shaft or the mechanical flyweights in the speed-sensing governor physically adjusts the position of the pilot valve to direct the incoming main pump pressure to either the increase or decrease pitch side of the governor servo spool. As pressure increases or decreases on either side of the servo spool, the servo spool will shift to follow the movement of the pilot valve. As the servo spool moves, ports in the servo spool align with ports in the pilot valve body to direct a metered amount of hydraulic fluid from the main pump discharge to the increase or decrease pitch lines. Pressure in these lines will control the dome piston position and ultimately blade angle. The decrease pitch side of the governor servo spool is larger than the increase pitch side. Hydraulic fluid on the decrease pitch side of the servo spool serves to buffer the changes in the increase pitch pressure side of the servo spool and allows minor decreases in pressure in the increase pitch line to actually reduce overall propeller pitch through the external twisting forces acting on the propeller blades (twisting moment)." I hope this helps. Vic
-
About 35 years ago I had a start problem as you discribed. The speed sensitave valve had an internal failure and at approximately 40% RPM acceleration stagnated and TIT rose rapidly. We went through the procedures in the maint manual and it started with checking the acceleration bleed valves to see if they are open, which they were. Then it pointed to fuel components, but same as you, I did not have a high fuel flow for RPM. Disconnected the line to the acceleration bleed valves at the inline filter and started the engine, everything was normal for start. Replaced speed sensitive valve and engine start was back to normal. There was no wind down associated with my problem. Vic
-
I agree with NATOPS1 about the acceleration bleed valves. Disconnect the high pressure out line at the speed sensitive valve which goes to the acceleration bleed valves and see if it starts OK. I had a bad speed sensitive valve one time which would close the valves at 45% and the TIT would increase rapidly. After shutdown a visual of the acceleration bleed valves revealed they were open because when the RPM droped below 45%.
-
If this is about hydraulic pressure and engine speeds, in the Hercules Service Information Letter No. 18, dated 1 NOV 77, there is an artical which addresses "Acceptable Hydraulic Pressure". The values presented in the charts are based on a New York Air Brake but they say they are representive for the Vickers, Abex and all other engine driven hydraulic pumps for the Hercules. The utility system is the only one which drops to 2,550 PSI with only one engine at LSGI and the elevator control column against the forward stop. This would put the utility system to a possible leakage/by-pass rate of 4.3 GPM. If the question is only about the engine being on speed then "normally" we start in LSGI and when it stables there it is "on speed". But if the LSGI system is unservicable then "on speed" would be at normal speed ground idle.
-
The additional restriction is placed on by the operator/operator. USAF has their restrictions for day VFR, USNR and USMC have their restrictions but I don't know what their local 3710 dictates. When I was active duty Navy we had no restriction. The Lockheed Flight Manuals for the C-130H and the FAA Approved Flight Manual (AFM) for the commercial L-382E/G have no requirement for a APU. Along with what tenten stated, the AFM has in the limitations section "Do not operate the APU during takeoff or in flight". Also, as stated earlier you should adjust your weight and balance.
-
If it happens with gear or flaps movement you may want to check the flow regulators. To check the landing gear you will need to actuate only one at a time, so pin/ground lock the other two. The only time I had this was when one MLG flow regulator failed to full flow and utility pressure dropped to about 1500 PSI. Vic
-
The quickest and best way to identify if your emergency flap brake valve has been energized is to follow your procedures under "Overriding Flap Selector Valve (Electrical Malfunction)". If the emergency flap brake valve has been energized to the locked position there will be no hydraulic pressure available to the flaps selector valve for override operation. When the flaps stop moving and the CB is not open this does not indicate there is no electrical problem. This is why the hydraulic overriding is the first step for flap system failures.
-
The following is from the Lockheed "Slow Flight" handout. "The Flight Manual air minimum control speed data are for a 5-degree favorable bank angle. An increase in airspeed is necessary to control the airplane if the favorable bank angle is reduced to a wings-level or adverse (into the failed engine) bank angle. The accompanying figures show the influence of bank angle on VMCA. For models with T56-A-15 engines, a 9-to-12-knot increase in minimum control speed above the Flight Manual value is necessary to maintain controllability with wings level. Air minimum control speed is increased 20 knots with 5 degrees of adverse bank at minimum flying weight and increases even more as gross weight increases. Similar increases are shown for models with T-56-A-7 engines. Banking into the failed engine will cause the airplane to "slide off" to that side, increasing adverse sideslip which increases drag, reduces performance, and increases the risk of losing heading control."
-
In the late 70s I had something similar but I just had low amps in flight. The glue for the blade electrical contact ring (P/N 525807) on my number two blade had failed and when the blade angle was in the flight range the ring did not contact the brushes. During normal ground operation amps checked good but if power was advanced above 8,000 in. lb. on the ground we could get the same indications.
-
In Lockheed Service Information Letter No. 18 dated 1 NOV 77 it has acceptable pressure reading for the auxiliary system as 2,700 to 3,200 PSI with the ground test valve tied and flight control boost shutoff switches open. If the elevator control column is at the forward stop the elevator boost package can bypass approximately 3.5 GPM causing the lower pressure reading on the auxiliary system gage.
-
A Garrett chart shows the 85-185L on a standard day at sea level will burn approximately 300 PPH with no load and 360 PPH at max load. Vic
-
Why not disable the fuel enrichment as per Allison CSL-1567 dated Nov 30, 1996 with Revision 1.
-
Around 1974 HS came out with a mod (service bulletin no. 39) to the pump housing which incorporate a dip stick for the atmospheric sump. The new dip stick was to aid in proper servicing. The dip stick had an OP LEVEL band and if the fluid level was in the OP LEVEL band while the aux feather pump running things should be good. After many static fluid leaks from the rear lip seal in 1981 HS came out with a mod (service bulletin no. 101) to the atmospheric sump dip stick. The bulletin had you remove existing markings from the dip stick and remark one line just about where the old OP LEVEL lower mark was and this becomes the new FULL mark. Now if there is any runback of fluid from the pressurized sump to the atmospheric sump while the prop is static the likelihood of a rear lip seal leaking due to overfilling is less. Our HS rep told us that after initial prop servicing there is no need to open the pressurized sump cap to check levels. We safety wired the caps closed to remove the temptation of opening them. This procedure worked well. Feb 1970 Service Information Release, Code SIR 54H-72 was issued which read: “54H60 Propeller Servicing Procedure Originally the various HS manuals specified that at the time of servicing 54H60 propellers, the No. 1 blade would be positioned in the 12 o'clock position. The theory that the beta feedback shaft would assist in purging entrained air has subsequently been proved invalid. There is no apparent difference in rate of air purging regardless of the location of the No. 1 blade. In view of the foregoing, the requirement for prepositioning the propeller for servicing has been deleted from all publications as they have come up for revision. Naturally there is no objection to positioning the No. 1 blade up-right prior to servicing any more than there is an objection to positioning it downward. This point is brought to the attention of all concerned in order to simplify to the maximum the already complex servicing requirements for this propeller model.†Vic
-
For P/N: 2CM85D1B try T.O. 8D6-6-6-43 for overhaul manual and T.O. 8D6-6-6-44 for IPB. Vic
-
Rolls-Royce Commercial Service Letter for T56 Approved Engine Oil (CSL-1502) has a lot of good information about lubrication. For T56 operators phone number 317-230-3774 is listed for contact. Vic
-
Engine generator frequency is determined as follows: T56 series III engine generator speed = 5,965 RPM Engine generator poles = 8 The constant 60 is used to convert RPM to revolutions per second (RPS) and each pole has two ends (60 x 2). (No. of poles x rpm) / (60 x 2) = Frequency (8 x 5,965) / 120 = 397.66 Frequency This should let you know what happened to the other 2 hertz. I have a hard time seeing 2 hertz on that meter. Vic OAE
-
Chris, The one I have has Change 8, Dated 15 DEC 97. I spoke to lockheed last fall and they said they were going to change the speeds in a new revision. I don't have that new revision yet and I checked the Lockheed Support site and the new revision was not listed in the "OFF-THE SHELF MANUAL REVISION SUMMARY" yet. You probably have the most current pub. Vic
-
Chris, I just looked at a Lockheed SMP 777 and for 15 degrees Sea Level, 2 eng Vmca is 137 KIAS and the USN/USMC performance book has 138 KIAS. (non-rosemount, stubby body) Vic
-
I have seen two photos and heard a lot of scuttle butt. No "official" information as of yet. Vic
-
The T56-A-15 with OAT 15 degrees C, sea level, no bleed, and zero knots airspeed: Prop thrust 8900 pounds TIT 1077° Torque 21,160 inch pounds Fuel flow 2460 PPH This may help you. Vic
-
NATOPS1 The attached file has information about engine and RGB oil pressures for T56 engines and the 501 engines. I hope this helps. Vic
-
Does this attachment help? Vic
-
The baseline L-382 (Lockheed L-100) powers the pilots FD system from the Essential AC bus and is always powered when the Essential AC bus is powered. The copilots FD system is normally powered from the Main AC bus but can be powered off the copilots inverter, it is controlled by the copilots AC instrument switch. The pilots FD does not get power from the inverter. Vic